Le tenute meccaniche sono componenti essenziali in diverse applicazioni industriali, poiché prevengono le perdite di fluido e garantiscono il funzionamento efficiente delle apparecchiature. Per migliorare le prestazioni e la longevità delle tenute meccaniche, vengono spesso impiegati sistemi di raffreddamento. Un raffreddamento in un tenuta meccanica si riferisce ad un fluido secondario che viene introdotto nel facce di foca per fornire raffreddamento, lubrificazione e protezione dalle condizioni avverse.
Questo articolo del blog approfondirà le complessità dei sistemi di quench nelle tenute meccaniche. Esploreremo i componenti che compongono un sistema di quench, i tipi di fluidi comunemente utilizzati e le funzioni chiave che questi sistemi svolgono, come il raffreddamento, la prevenzione delle perdite e la protezione dalla cristallizzazione. Inoltre, discuteremo le diverse applicazioni dei sistemi di quench in diversi settori, le considerazioni progettuali e le pratiche di monitoraggio, nonché i vantaggi e i potenziali svantaggi associati all'implementazione di sistemi di quench nelle tenute meccaniche.
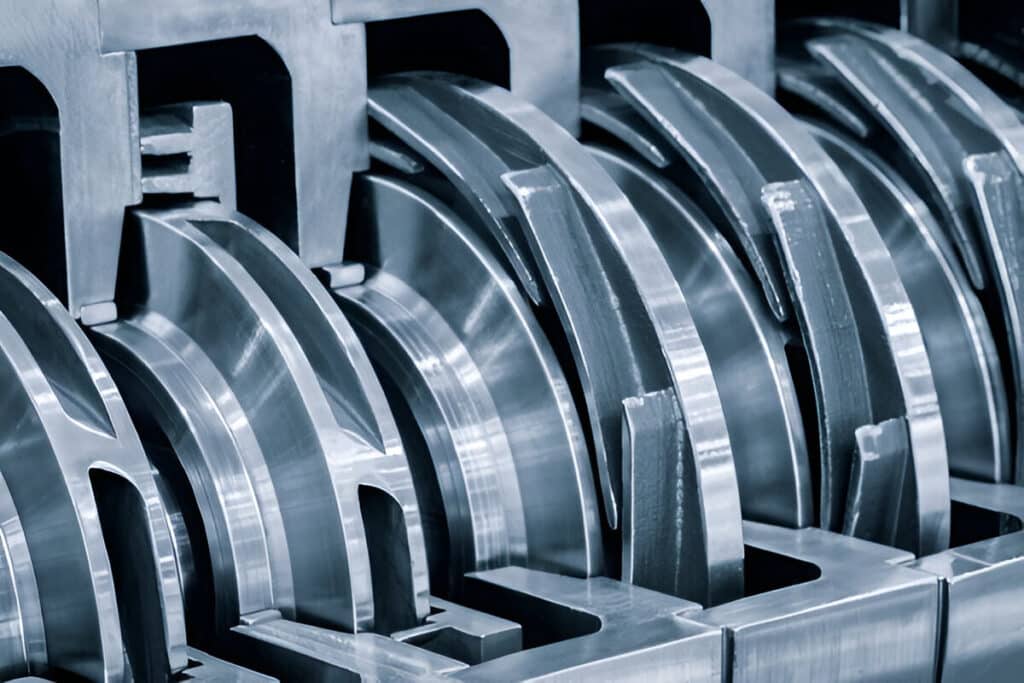
Che cosa è un quench in una tenuta meccanica
Nel contesto delle tenute meccaniche, un quench si riferisce a un metodo di raffreddamento e lubrificazione delle facce della tenuta per prevenire perdite ed estendere vita di focaLa tempra prevede l'introduzione di un fluido, in genere un liquido o un gas, nel camera di tenuta o sul lato atmosferico delle facce della guarnizione. Questo fluido serve ad assorbire il calore generato dall'attrito e a dissiparlo lontano dalla componenti di tenuta.
Il fluido di tempra aiuta anche a lubrificare le facce di tenuta, riducendo l'usura causata dal contatto costante e dal movimento relativo tra le facce rotanti e fisse. Mantenendo una sottile pellicola di fluido tra le facce, il quench riduce il contatto diretto e minimizza i danni correlati all'attrito.
Componenti di un sistema di spegnimento
Un tipico sistema di spegnimento è composto da diversi componenti chiave che lavorano insieme per raggiungere gli obiettivi desiderati:
- Serbatoio del fluido di tempra: si tratta di un contenitore che contiene il fluido di tempra, che può essere un liquido o un gas, a seconda dei requisiti dell'applicazione. Il serbatoio deve avere una capacità sufficiente per garantire un'adeguata fornitura del fluido di tempra.
- Pompa di circolazione o compressore: a seconda che il fluido di tempra sia un liquido o un gas, viene utilizzata una pompa o un compressore per far circolare il fluido attraverso il sistema. Ciò garantisce un flusso continuo del fluido di tempra alle superfici di tenuta.
- Tubazioni e valvole: una rete di tubazioni e valvole viene utilizzata per trasportare il fluido di tempra dal serbatoio alla guarnizione e ritorno. Le tubazioni devono essere progettate per ridurre al minimo le cadute di pressione e garantire una distribuzione uniforme del flusso.
- Dispositivi di controllo del flusso: includono componenti quali misuratori di portata, regolatori di pressione e valvole di strozzatura, che aiutano a mantenere la portata e la pressione desiderate del fluido di tempra sulle superfici di tenuta.
- Scambiatore di calore (facoltativo): in alcuni casi, uno scambiatore di calore può essere incorporato nel sistema di tempra per rimuovere il calore in eccesso dal fluido di tempra, soprattutto se il fluido di processo genera calore significativo o se il fluido di tempra deve essere mantenuto a una temperatura specifica.
Tipi di fluidi utilizzati
La selezione del fluido di tempra dipende da vari fattori, come le proprietà del fluido di processo, le condizioni operative e le considerazioni ambientali. Alcuni tipi comuni di fluidi di tempra includono:
- Acqua: l'acqua è un fluido di tempra ampiamente utilizzato per le sue eccellenti proprietà di raffreddamento e lubrificazione, nonché per la sua abbondanza e il basso costo. Tuttavia, potrebbe non essere adatto per applicazioni che coinvolgono fluidi di processo idroreattivi o idrosolubili.
- Soluzioni a base di glicole: i fluidi a base di glicole, come glicole etilenico o glicole propilenico, sono spesso utilizzati come fluidi di tempra per le loro buone caratteristiche di trasferimento di calore e bassi punti di congelamento. Sono particolarmente utili in applicazioni in cui il fluido di processo può cristallizzare o solidificare a temperature più basse.
- Oli: vari tipi di oli, tra cui oli minerali, oli sintetici e oli vegetali, possono essere utilizzati come fluidi di tempra. Forniscono una buona lubrificazione e sono adatti per applicazioni che coinvolgono alte temperature o fluidi di processo chimicamente aggressivi.
- Gas: in alcuni casi, gas come azoto, aria o vapore possono essere utilizzati come fluidi di tempra. I sistemi di tempra gassosi sono in genere utilizzati quando il fluido di processo è sensibile alla contaminazione o quando è richiesto un ambiente non reattivo.
Funzioni dei sistemi di spegnimento
Raffreddamento e lubrificazione della guarnizione
Una delle funzioni principali di un sistema di tempra in una tenuta meccanica è quella di fornire raffreddamento e lubrificazione alle facce della tenuta. Il flusso costante del fluido di tempra aiuta a dissipare il calore generato dall'attrito tra le facce rotanti e fisse della tenuta.
Inoltre, il fluido di tempra agisce come lubrificante tra le facce della guarnizione, riducendo l'attrito e l'usura. Mantenendo una sottile pellicola di fluido tra le facce, il sistema di tempra riduce al minimo il contatto diretto e aiuta a prolungare la durata di servizio della guarnizione.
Prevenzione delle perdite nell'atmosfera e della contaminazione
Un'altra funzione fondamentale dei sistemi di raffreddamento è quella di impedire la fuoriuscita del fluido sigillato nell'atmosfera e di proteggerlo dalla contaminazione esterna.
Mantenendo una pressione più elevata nella camera di tempra rispetto alla pressione atmosferica, il sistema di tempra assicura che qualsiasi perdita che potrebbe verificarsi venga indirizzata nuovamente nel fluido di tempra anziché fuoriuscire nell'atmosfera. Questa differenza di pressione positiva impedisce anche l'ingresso di contaminanti atmosferici, come umidità o polvere, nel fluido sigillato, mantenendone la purezza e l'integrità.
Protezione contro la cristallizzazione e la reazione con le condizioni atmosferiche
In alcune applicazioni, il fluido sigillato può essere soggetto a cristallizzazione o reazioni avverse se esposto alle condizioni atmosferiche. Ad esempio, alcuni fluidi possono solidificare, precipitare o formare depositi a contatto con aria o umidità. Questi fenomeni possono portare all'accumulo di solidi sulle superfici di tenuta, causando un aumento dell'attrito, dell'usura e, infine, cedimento della tenuta.
Il sistema di tempra attenua questi problemi isolando il fluido sigillato dall'atmosfera e mantenendo un ambiente controllato all'interno della camera di tempra. Il fluido di tempra viene attentamente selezionato per essere compatibile con il fluido sigillato e per prevenire qualsiasi reazione indesiderata. Mantenendo il fluido sigillato immerso nel fluido di tempra, il sistema impedisce l'esposizione diretta alle condizioni atmosferiche, riducendo al minimo il rischio di cristallizzazione o altre reazioni dannose.
Applicazioni dei sistemi di spegnimento
Applicazioni ad alta temperatura
I sistemi di tempra sono comunemente impiegati in applicazioni ad alta temperatura in cui il fluido sigillato è a una temperatura elevata. In questi casi, il fluido di tempra funge da mezzo di raffreddamento, assorbendo e dissipando il calore generato dal processo di sigillatura. Mantenendo una temperatura più bassa sulle facce di tenuta, il sistema di tempra impedisce danni termici ai componenti di tenuta e garantisce un funzionamento affidabile in ambienti ad alta temperatura esigenti.
Sigillatura di fluidi pericolosi e tossici
In settori quali l'elaborazione chimica, la raffinazione del petrolio e la farmaceutica, le tenute meccaniche sono spesso utilizzate per contenere fluidi pericolosi o tossici. I sistemi di tempra svolgono un ruolo fondamentale in queste applicazioni, fornendo un ulteriore strato di protezione contro le perdite. Il fluido di tempra agisce come una barriera, impedendo la fuoriuscita di sostanze pericolose nell'atmosfera e riducendo al minimo il rischio di contaminazione ambientale o esposizione del personale.
Fluidi cristallizzanti e solidificanti
Alcuni fluidi di processo tendono a cristallizzare o solidificare quando esposti a determinate condizioni, come variazioni di temperatura o pressione. Questi fluidi possono rappresentare delle sfide per le tenute meccaniche, poiché la formazione di solidi sulle superfici di tenuta può portare a un aumento dell'attrito, dell'usura e a guasti prematuri. I sistemi di tempra sono impiegati in queste applicazioni per mantenere un ambiente stabile attorno alla tenuta, impedendo la cristallizzazione e garantendo un funzionamento regolare.
Vantaggi dei sistemi di spegnimento
Durata prolungata della guarnizione
Uno dei principali vantaggi dei sistemi di tempra è la loro capacità di estendere la durata di vita delle guarnizioni meccaniche. Fornendo raffreddamento, lubrificazione e protezione efficaci contro condizioni avverse, i sistemi di tempra riducono l'usura delle superfici di tenuta. Il flusso costante del fluido di tempra aiuta a mantenere un ambiente di tenuta stabile, riducendo al minimo le sollecitazioni termiche e meccaniche sui componenti della tenuta.
Maggiore sicurezza del processo
I sistemi di quench contribuiscono in modo significativo a migliorare la sicurezza dei processi mitigando i rischi associati a perdite e contaminazione. Impedendo la fuoriuscita di fluidi pericolosi o tossici nell'atmosfera, i sistemi di quench aiutano a proteggere il personale, le attrezzature e l'ambiente da potenziali danni.
Affidabilità del processo migliorata
L'uso di sistemi di quench può migliorare notevolmente l'affidabilità delle tenute meccaniche e dei processi che servono. Mantenendo condizioni di tenuta ottimali e prevenendo guasti prematuri delle tenute, i sistemi di quench riducono al minimo i tempi di fermo non pianificati e le interruzioni della produzione.
Svantaggi dei sistemi di spegnimento
Aumento della complessità e dei costi
L'implementazione di un sistema di quench aggiunge complessità alla disposizione di tenuta, richiedendo componenti, tubazioni e strumentazione aggiuntivi. Questa maggiore complessità può tradursi in costi iniziali più elevati per l'attrezzatura, l'installazione e la messa in servizio. La necessità di monitoraggio regolare, manutenzione e potenziali riparazioni del sistema di quench contribuisce anche ad aumentare le spese operative per tutta la durata dell'attrezzatura.
Potenziale di contaminazione del fluido di tempra
Sebbene i sistemi di tempra siano progettati per prevenire la contaminazione del fluido sigillato, esiste un potenziale rischio che il fluido di tempra stesso venga contaminato. L'ingresso di fluido di processo, contaminanti atmosferici o la degradazione del fluido di tempra nel tempo possono comprometterne l'efficacia e portare a effetti negativi sulle prestazioni di tenuta.
Requisiti di manutenzione aggiuntivi
La presenza di un sistema di tempra introduce requisiti di manutenzione aggiuntivi rispetto a sistemi di tenuta più semplici. Il fluido di tempra deve essere periodicamente controllato per contaminazione, degradazione e compatibilità con il fluido sigillato e materiali di tenutaAnche le tubazioni, le pompe e la strumentazione associate al sistema di raffreddamento richiedono regolari ispezioni, pulizie e calibrazioni per garantire prestazioni ottimali.