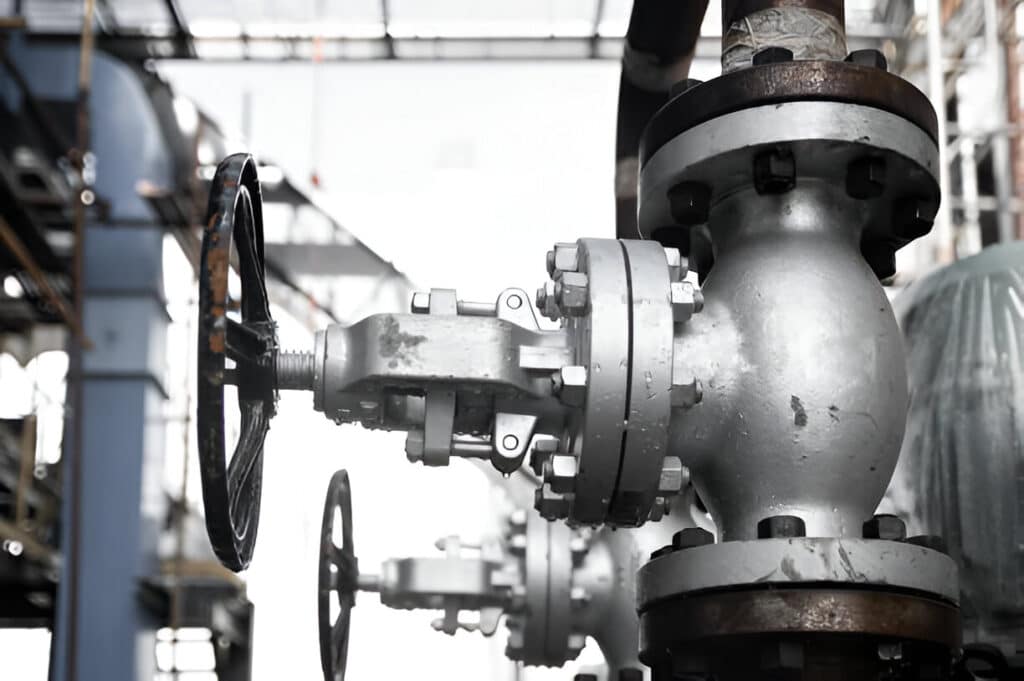
Ранние механические уплотнения (1900-1940-е гг.)
Ранние конструкции уплотнений, материалы (сталь, бронза) и области применения
Ранние механические уплотнения в основном изготавливались из таких материалов, как сталь и бронза. Эти материалы были выбраны из-за их прочности и износостойкости. Уплотнения были разработаны для установки в сальники насосов и другого вращающегося оборудования, обеспечивая более эффективное средство предотвращения утечки жидкости, чем традиционная мягкая набивка.
Изобретение первого механического уплотнения Джорджем Куком в 1905 году («Пломба Кука»).
История механических уплотнений началась в 1905 году, когда Джордж Кук изобрел первое механическая печать, известный как «Cook Seal». Эта новаторская конструкция состояла из неподвижного и вращающегося кольца, причем одно кольцо имело канавку, заполненную мягким набивочным материалом. Cook Seal был выдающимся шагом вперед в технологии герметизации, предлагая более эффективную и надежную альтернативу традиционной набивке сальника.
Разработка «печати Райана» Дж. М. Райаном из компании Crane Packing Company в 1929 году
В 1929 году Дж. М. Райан из компании Crane Packing Company представил «Пломбу Райана», которая представляла собой подпружиненный неподвижный уплотнительное лицо изготовленный из углеродного графита и вращающейся уплотнительной поверхности из бронзы. Эта конструкция улучшила Cook Seal, обеспечив лучшую герметичность и более длительный срок службы. Ryan Seal быстро завоевал популярность в различных промышленных применениях, особенно в центробежные насосы.
Достижения середины XX века (1950-1970-е годы)
Внедрение новых материалов для уплотнительных поверхностей, таких как углеродный графит, карбид вольфрама, керамика
В 1950-х и 1960-х годах производители механических уплотнений начали экспериментировать с новыми материалами для уплотнительных поверхностей, чтобы улучшить производительность и долговечность. Углеродный графит стал популярным выбором для стационарных уплотнительных поверхностей благодаря своей превосходной износостойкости и самосмазывающимся свойствам. Карбид вольфрама и керамика, такая как карбид кремния, также были представлены в качестве материалов для уплотнительных поверхностей, предлагая превосходную твердость и химическую стойкость по сравнению с традиционной бронзой и сталью.
Разработка коэффициента давления-скорости (PV) Гербертом Хаммером из Durametallic
В 1960-х годах Герберт Хаммер из Durametallic Corporation разработал фактор давления-скорости (PV), критический параметр проектирования, который связывает давление уплотнения и скорость скольжения поверхностей уплотнения. Фактор PV позволил производителям уплотнений оптимизировать конструкции уплотнений для конкретных применений, учитывая такие факторы, как свойства жидкости, температура и давление. Эта разработка привела к созданию более эффективных и надежных механических уплотнений.
Появление стандартных картриджных уплотнений и схем уплотнений (одинарных, двойных, тандемных)
Внедрение стандартных картриджных уплотнений в 1960-х годах произвело революцию в отрасли механических уплотнений. Картриджные уплотнения представляли собой предварительно собранные блоки, включавшие все необходимые компоненты, такие как уплотнительные поверхности, вторичные уплотнительные элементы и пружины, в едином, готовом к установке пакете. Такая конструкция упрощала установку и обслуживание уплотнений, сокращая время простоя и расходы, связанные с заменой уплотнений.
В этот период также были разработаны различные конструкции уплотнений для удовлетворения различных требований к применению. Одинарные уплотнения, состоящие из одной пары уплотнительных поверхностей, стали наиболее распространенной конструкцией для общего применения. Двойные уплотнения, состоящие из двух пар уплотнительных поверхностей с барьерная жидкость между ними, были введены для более требовательных приложений, требующих более высокого уровня безопасности и надежности. Тандемные уплотнения с двумя парами уплотнительных поверхностей, расположенных последовательно, были разработаны для приложений, где резервное уплотнение было необходимо в случае отказа основного уплотнения.
Основание крупных компаний по производству уплотнений, таких как John Crane, Flowserve, Burgmann
В середине 20 века появилось несколько крупных производителей механических уплотнений, которые в дальнейшем сформировали отрасль. Компания John Crane, основанная в 1917 году, стала ведущим мировым поставщиком механических уплотнений и уплотнительных систем. Корни Flowserve Corporation, образованной в результате слияния BW/IP и Durco International в 1997 году, восходят к Byron Jackson Company, известному производителю насосов и уплотнений, основанному в 1872 году. Компания Burgmann Industries, основанная в 1884 году, выросла и стала крупным игроком на европейском рынке механических уплотнений.
Эти компании сыграли значительную роль в развитии технологии механических уплотнений за счет постоянных инвестиций в исследования и разработки, внедрения инновационных конструкций, материалов и производственных процессов, которые устанавливают новые стандарты производительности и надежности уплотнений.
Современная эра механических уплотнений (1980-е годы — настоящее время)
Улучшения в конструкции уплотнений и материалах, обусловленные более строгими нормами и требованиями отрасли
В 1980-х и 1990-х годах растущая обеспокоенность состоянием окружающей среды и более строгие правила относительно выбросов и утечек из промышленного оборудования привели к значительному прогрессу в разработке и материалах механических уплотнений. Например, поправки к Закону США о чистом воздухе 1990 года предписывали сокращение выбросов летучих органических соединений (ЛОС) от насосов и другого оборудования, подталкивая производителей уплотнений к разработке более эффективных и экологически безопасных уплотнительных решений.
Требования отрасли к более высокой надежности, более длительному сроку службы и улучшенной производительности в сложных условиях также стимулировали инновации в конструкции и материалах уплотнений. Производители уплотнений сосредоточились на разработке современных материалов для поверхностей уплотнений, оптимизации геометрии уплотнений и внедрении таких функций, как спиральные канавки и лазерная обработка поверхности, для улучшения производительности уплотнения и снижения износа.
Использование современных материалов, таких как карбид кремния, алмазные покрытия, высокопроизводительные полимеры
Использование современных материалов стало отличительной чертой современных разработок механических уплотнений. Карбид кремния, керамический материал с превосходной твердостью, износостойкостью и химической инертностью, стал предпочтительным выбором для уплотнительных поверхностей в сложных условиях, связанных с абразивными или едкими жидкостями. Алмазные покрытия, нанесенные с использованием методов химического осаждения из паровой фазы (CVD) или физического осаждения из паровой фазы (PVD), также использовались для повышения износостойкости и долговечности уплотнительных поверхностей.
Высокоэффективные полимеры, такие как политетрафторэтилен (ПТФЭ), полиэфирэфиркетон (ПЭЭК) и ароматические полиамиды (например, кевлар), все чаще используются во вторичных уплотнительных элементах и других компонентах уплотнений. Эти материалы обеспечивают превосходную химическую стойкость, низкое трение и высокую температурную стабильность, что позволяет механическим уплотнениям надежно работать в широком диапазоне сложных условий.
Интеграция таких функций, как лазерная топография лица, для повышения производительности
Достижения в области производственных технологий позволили производителям уплотнений внедрять сложные функции в конструкции механических уплотнений. Например, лазерная обработка позволила создать точную микротопографию на поверхностях уплотнений, например спиральные канавки или углубления, которые могут улучшить смазку, уменьшить трение и повысить эффективность уплотнения.
Другие конструктивные особенности, которые стали более распространенными в современных механических уплотнениях, включают в себя:
- Двунаправленные уплотнительные возможности, позволяющие уплотнениям эффективно работать в обоих направлениях вращения.
- Самоустанавливающиеся уплотнительные поверхности, обеспечивающие оптимальный контакт и герметичность даже в условиях несоосности
- Уплотнительные поверхности с балансировкой давления, снижающие чистое усилие закрытия на уплотнительных поверхностях и продлевающие срок службы уплотнения
- Гибкие графитовые вторичные уплотнительные элементы, обеспечивающие улучшенную химическую совместимость и высокотемпературные характеристики
Применение модульных картриджных уплотнений и разъемных уплотнений для облегчения установки и обслуживания
Модульные картриджные уплотнения стали пользоваться все большей популярностью в последние десятилетия из-за простоты установки и обслуживания. Эти уплотнения разработаны с взаимозаменяемыми компонентами, что позволяет пользователям быстро заменять изношенные или поврежденные детали без необходимости замены всего узла уплотнения. Такой модульный подход сокращает время простоя и расходы на обслуживание, обеспечивая большую гибкость в конфигурации уплотнения для конкретных применений.
Разъемные уплотнения, состоящие из двух половин, которые можно установить вокруг вала без необходимости полной разборки оборудования, также получили распространение в уплотнительной промышленности. Разъемные уплотнения особенно выгодны для применений, где требуется частое обслуживание уплотнения или где разборка оборудования затруднена или занимает много времени.