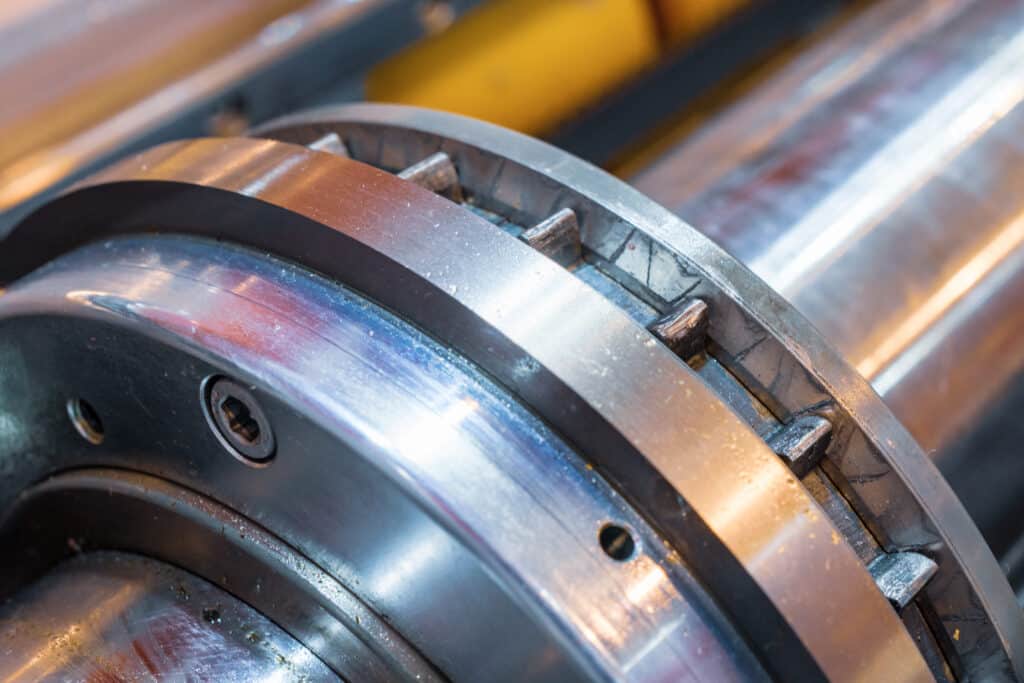
Tỷ lệ rò rỉ chấp nhận được điển hình
Trong hầu hết các ứng dụng công nghiệp, một phớt cơ khí hoạt động bình thường sẽ có tỷ lệ rò rỉ là 10 giọt mỗi giờ hoặc ít hơn cho mỗi phớt. Lượng rò rỉ nhỏ này được coi là bình thường và cần thiết để bôi trơn và làm mát phớt đúng cách. Rò rỉ quá mức vượt quá tỷ lệ này có thể chỉ ra các vấn đề về thiết kế, lắp đặt hoặc điều kiện vận hành phớt.
Rò rỉ phớt được đo bằng cách thu thập và định lượng chất lỏng rò rỉ qua mặt phớt trong một khoảng thời gian nhất định. Phương pháp được chấp nhận chung là đo giọt mỗi phút và chuyển đổi thành tốc độ theo giờ. Một giọt mỗi phút tương đương với khoảng 2,5 đến 3 ml mỗi giờ.
Rò rỉ cho phép của API 682
Tiêu chuẩn 682 của Viện Dầu khí Hoa Kỳ (API) cung cấp hướng dẫn về rò rỉ phớt chấp nhận được trong ngành dầu khí. API 682 định nghĩa ba lớp rò rỉ phớt:
- Loại I Seal: Tỷ lệ hao hụt dưới 500 ml mỗi ngày (20,8 ml/giờ)
- Con dấu loại II: Tỷ lệ rò rỉ dưới 1.000 ml mỗi ngày (41,7 ml/giờ)
- Con dấu loại III: Tỷ lệ rò rỉ dưới 2.000 ml mỗi ngày (83,3 ml/giờ)
Tỷ lệ rò rỉ cho phép này cao hơn mức chuẩn thông thường là 10 giọt mỗi giờ do điều kiện vận hành khắt khe và tính chất quan trọng của các ứng dụng dầu khí.
Các yếu tố ảnh hưởng đến tỷ lệ rò rỉ phớt
Các yếu tố thiết kế con dấu
- Vật liệu mặt: Các đặc tính tribological và khả năng tương thích của vật liệu mặt vòng chính và mặt vòng ghép ảnh hưởng đến rò rỉ. Các cặp mặt cứng như silicon carbide so với silicon carbide có xu hướng chạy với khoảng hở chặt chẽ hơn và ít rò rỉ hơn.
- Tỷ lệ cân bằng: Phớt có tỷ lệ cân bằng cao (tức là lực đóng lớn hơn) có xu hướng có tỷ lệ rò rỉ thấp hơn. Tuy nhiên, điều này phải được cân bằng với sự sinh nhiệt và hao mòn.
- Chăm sóc da mặt:Các phương pháp xử lý bề mặt như tạo vân bề mặt bằng laser (LST) hoặc tái tạo bề mặt bằng vi sóng có thể được sử dụng để tối ưu hóa địa hình của mặt phớt nhằm cải thiện khả năng bôi trơn và kiểm soát rò rỉ.
- Tải lò xo: Lực lò xo giữ các mặt lại với nhau ảnh hưởng đến tải trọng mặt và tỷ lệ rò rỉ. Lò xo mạnh hơn làm giảm rò rỉ nhưng làm tăng độ mài mòn và tỏa nhiệt.
Yếu tố thiết bị
- Tốc độ trục:Tốc độ trục cao hơn có xu hướng làm tăng rò rỉ phớt do lực ly tâm và độ nhiễu loạn lớn hơn.
- Sự không thẳng hàng: Quá mức trục lệch hoặc lệch có thể gây ra tải không đều và tăng rò rỉ ở mặt phớt.
- Rung: Rung động có thể khiến bề mặt phớt rung chuyển hoặc mở ra trong giây lát, dẫn đến tỷ lệ rò rỉ cao hơn.
Điều kiện hoạt động
- Áp lực: Áp suất kín cao hơn có xu hướng làm tăng tỷ lệ rò rỉ khi mọi thứ đều như nhau. Áp suất tăng gấp đôi sẽ làm tăng gấp đôi tỷ lệ rò rỉ.
- Nhiệt độ: Nhiệt độ tăng làm giảm độ nhớt có thể dẫn đến tỷ lệ rò rỉ cao hơn. Nhiệt độ cao cũng có thể làm hỏng chất đàn hồi và gây biến dạng bề mặt.
Tính chất chất lỏng
- Độ nhớt:Chất lỏng có độ nhớt thấp dễ bị rò rỉ hơn vì chúng chảy dễ dàng hơn qua lớp màng mỏng giữa các mặt.
- Độ bôi trơn:Các chất lỏng có khả năng bôi trơn kém có thể gây tăng ma sát và mài mòn ở bề mặt phớt, dẫn đến rò rỉ nhiều hơn.
- Độ mài mòn:Chất lỏng mài mòn làm tăng tốc độ mài mòn của bề mặt phớt, khiến bề mặt này mở ra và tăng rò rỉ theo thời gian.
- Sự biến động:Các chất lỏng dễ bay hơi hoặc dạng khí khó bịt kín hơn và dễ bị rò rỉ nhiều hơn, đặc biệt nếu hoạt động gần áp suất hơi của chất lỏng.