Fluid leakage is one of the most common failure modes in hydraulic and pneumatic systems. Selecting the right seal can prevent leaks, ensure efficiency, and extend equipment life.
Axial and radial seals are two primary types used in these systems, but they have distinct differences in their design, function, and application. In this article, we’ll explore the key differences between axial and radial seals and provide guidance on how to choose the most suitable option for your specific requirements.
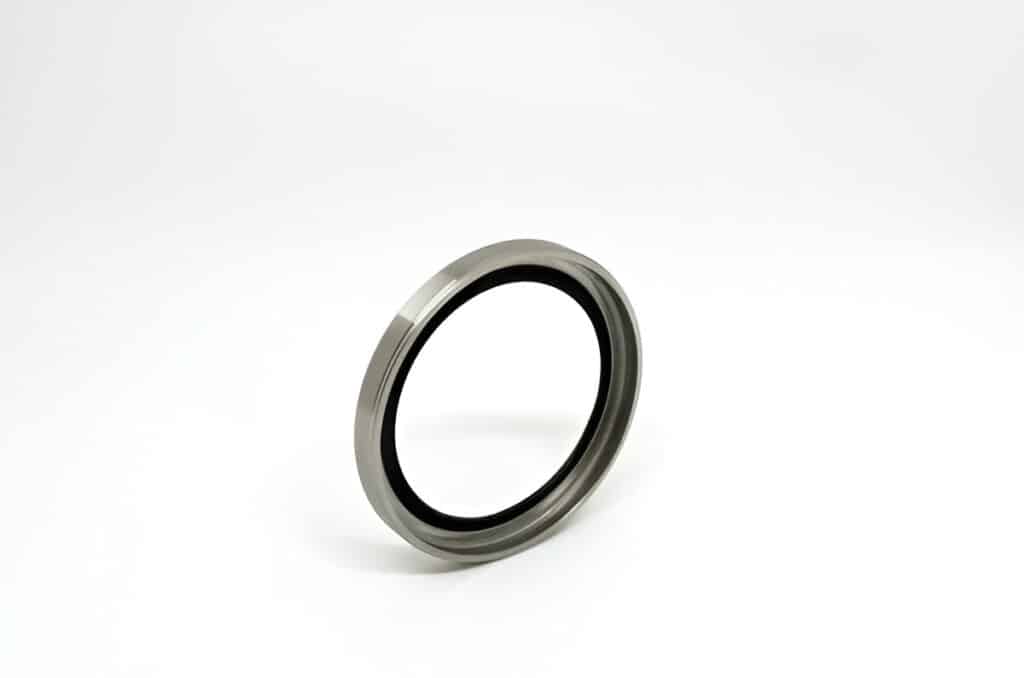
What is a radial seal
A radial seal, also known as a radial shaft seal, is a type of seal that is designed to prevent leakage along a shaft or housing bore in a radial direction (perpendicular to the shaft axis). The primary sealing lip of a radial seal is positioned at a right angle to the shaft, maintaining tight contact with the shaft surface.
What is an axial seal
An axial seal, in contrast to a radial seal, is oriented with its primary sealing interface parallel to the shaft axis or along the face of a housing bore. Axial seals are used to prevent leakage across two machine components that are assembled perpendicular to the shaft, such as between a bearing housing and end cover.
Difference Between Radial Seals and Axial Seals
Mechanism
Radial seals, also known as shaft seals, provide a sealing effect along the radius of a shaft or housing bore. They are installed in a gland perpendicular to the shaft axis, with the sealing lip in direct contact with the shaft surface. The sealing lip is energized by a combination of its own elasticity and the system pressure, maintaining a tight seal.
Axial seals seal along the shaft axis. They are positioned parallel to the shaft thrust face, with the sealing occurring between the flat surfaces of the seal and the shaft or housing. Axial seals prevent leakage by maintaining a tight face-to-face contact between the mating parts.
Motion Direction
Radial seals are primarily used to seal rotating shafts, accommodating circular motion. As the shaft rotates, the seal maintains continuous contact to prevent fluid from escaping the system or contaminants from entering.
Axial seals are suited for sealing along the shaft axis in applications involving lateral motion. Axial seals prevent leakage as the shaft moves back and forth, maintaining a tight seal between the flat mating surfaces.
Materials
Radial seals are typically made from elastomeric materials such as nitrile rubber (NBR), fluoroelastomers (FKM), or polyurethane (PU).
Axial seals can be made from a wider range of materials, including elastomers like NBR and FKM, as well as thermoplastics such as PTFE, polyamide, or polyethylene.
Shape
Radial seals are typically designed as circular rings with a cross-section that includes a sealing lip, a metal insert for reinforcement, and a spring for additional energizing force. The circular shape allows the seal to fit snugly around the shaft and maintain a 360-degree sealing contact.
Axial seals often have a flat disc or washer-like shape. They can be simple flat gaskets or more complex designs with multiple sealing lips or grooves.
Applications
Due to their different mechanisms and motion handling capabilities, radial and axial seals find applications in various industrial sectors. Radial seals are extensively used in rotating equipment such as:
- Pumps: To seal the rotating shaft and prevent fluid leakage
- Gearboxes: To contain lubricating oil and protect against contamination
- Electric motors: To seal the shaft and prevent ingress of dust or moisture
- Automotive engines: To seal crankshafts, camshafts, and other rotating components
Axial seals are commonly employed in applications involving linear motion, such as:
- Hydraulic cylinders: To seal the piston rod and prevent fluid leakage
- Pneumatic actuators: To seal the piston and maintain air pressure
- Valve stems: To prevent leakage along the valve shaft
- Compressors: To seal the reciprocating piston and prevent gas leakage
Choosing Between Axial and Radial Seals
Gland Design and Dimensions
Axial seals are typically used in applications with axially constrained spaces, such as those found in hydraulic cylinders, pumps, and valves. The gland for an axial seal is usually a simple counterbore or groove that allows the seal to be compressed axially.
Radial seals are suited for radially constrained spaces, such as those in rotating shafts or reciprocating piston rods. The gland for a radial seal is typically a bore or groove that allows the seal to be compressed radially against the shaft or rod surface.
Type of Motion
Axial seals are generally better suited for static or slow reciprocating motions, as they can maintain a tight seal with minimal friction. The axial compression of the seal against the mating surface creates a robust sealing interface.
Radial seals are ideal for rotary and high-speed reciprocating motions, as they can provide effective sealing while accommodating the dynamic motion of the shaft or rod. The radial compression of the seal against the moving surface allows it to maintain contact and prevent leakage, even under high rotational speeds or frequent direction changes.
Operating Pressures
Axial seals are generally better suited for high-pressure applications, as the axial compression of the seal creates a strong sealing force that can withstand significant pressure differentials. The higher the pressure, the greater the axial force on the seal, which enhances its sealing capability.
Radial seals, while still effective at moderate pressures, may have limitations in extremely high-pressure environments. The radial compression of the seal against the shaft or rod may not provide sufficient sealing force to overcome very high pressures. In such cases, additional sealing elements or backup rings may be necessary to support the radial seal and prevent extrusion or blowout.
Gaps and Tolerances
Axial seals are more forgiving of larger gaps and looser tolerances, as the axial compression of the seal can accommodate some variation in the mating surfaces. This makes axial seals a good choice for applications where precise alignment or tight tolerances are difficult to maintain.
Radial seals, however, require tighter control of gaps and tolerances to ensure proper sealing. The radial compression of the seal against the shaft or rod relies on a consistent and uniform contact between the seal and the mating surface. Any excessive gaps or variations in the surface can lead to leakage or premature seal wear.
Surface Finishes
Axial seals are generally more tolerant of rougher surface finishes, as the axial compression of the seal can help to fill in surface irregularities and create a good sealing interface. This makes axial seals a viable option for applications where achieving a very smooth surface finish is impractical or cost-prohibitive.
Radial seals require smoother surface finishes to ensure proper sealing and minimize wear. The radial contact between the seal and the shaft or rod can be adversely affected by surface irregularities, leading to leakage paths or accelerated seal degradation.
Presence of Contaminants
Axial seals are generally less sensitive to contaminants, as the axial compression of the seal can help to exclude or expel particles from the sealing interface. The higher sealing force of axial seals can also help to resist the ingress of contaminants.
Radial seals, while still effective in many contaminated environments, may be more vulnerable to damage or wear from abrasive particles. The radial contact between the seal and the rotating or reciprocating surface can create a path for contaminants to enter and accumulate, leading to accelerated seal wear or leakage. In highly contaminated applications, additional measures such as shaft scraper seals or exclusion devices may be necessary to protect the radial seal.