Pumps are the workhorses of countless industrial operations, yet selecting the correct type can be challenging. The choice between centrifugal and positive displacement pumps significantly impacts performance. These two pump types differ vastly in their operation, capabilities, and applications.
This article will explore the intricacies of each, analyzing their mechanisms, performance characteristics, and typical uses, providing guidance for optimal pump selection. It will cover important aspects such as operating principles, flow rates, viscosity handling, and maintenance considerations to help professionals in the field make informed decisions.
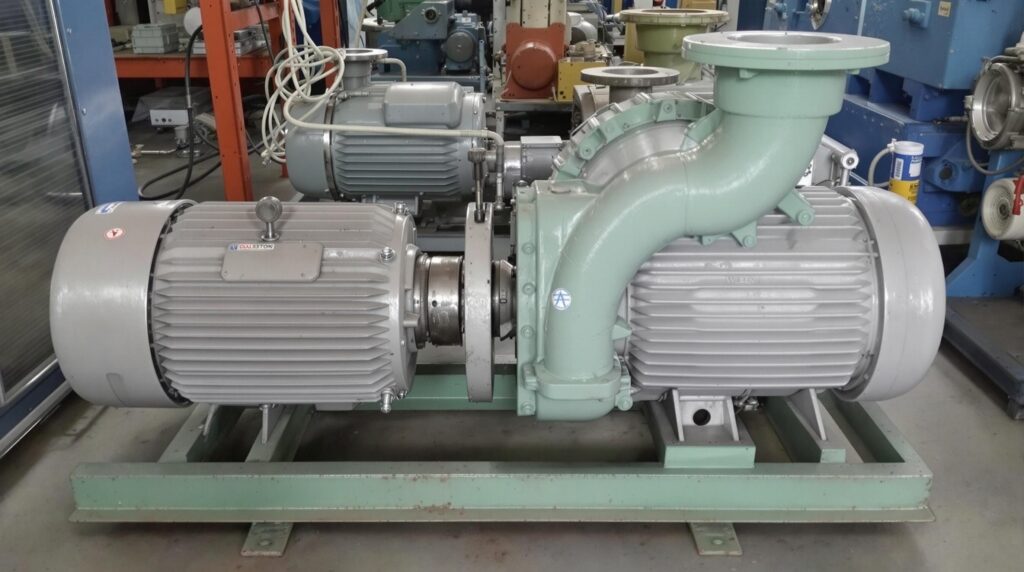
What Is a Centrifugal Pump
A centrifugal pump is a type of rotodynamic pump that uses a rotating impeller to impart kinetic energy to the fluid, increasing its velocity and pressure. This kinetic energy is then converted into pressure energy as the fluid exits the pump.
Centrifugal pumps are characterized by their ability to move large volumes of fluid at relatively low pressures, making them suitable for a wide range of applications involving low-viscosity fluids. They are widely used in various industries, domestic settings, and agriculture due to their simple design, ease of operation, and cost-effectiveness.
Operating Principles of Centrifugal Pumps
Centrifugal pumps operate on the principle of converting mechanical energy from a motor into kinetic energy within the fluid. The process begins when the electric motor turns the pump shaft, which is connected to the impeller. The impeller, equipped with a series of blades or vanes, rotates at high speed, typically ranging from 500 to 5000 rpm. This rotation creates a centrifugal force that draws fluid into the pump’s center, near the impeller’s eye. As the fluid moves through the impeller, it gains velocity and is pushed outward towards the casing’s outer edges.
The pump casing is designed to collect the fluid discharged by the impeller and direct it to the pump outlet. The shape of the casing converts the fluid’s kinetic energy into pressure energy, enabling the fluid to be pushed through the discharge pipe. The key here is that the pump produces flow by creating pressure.
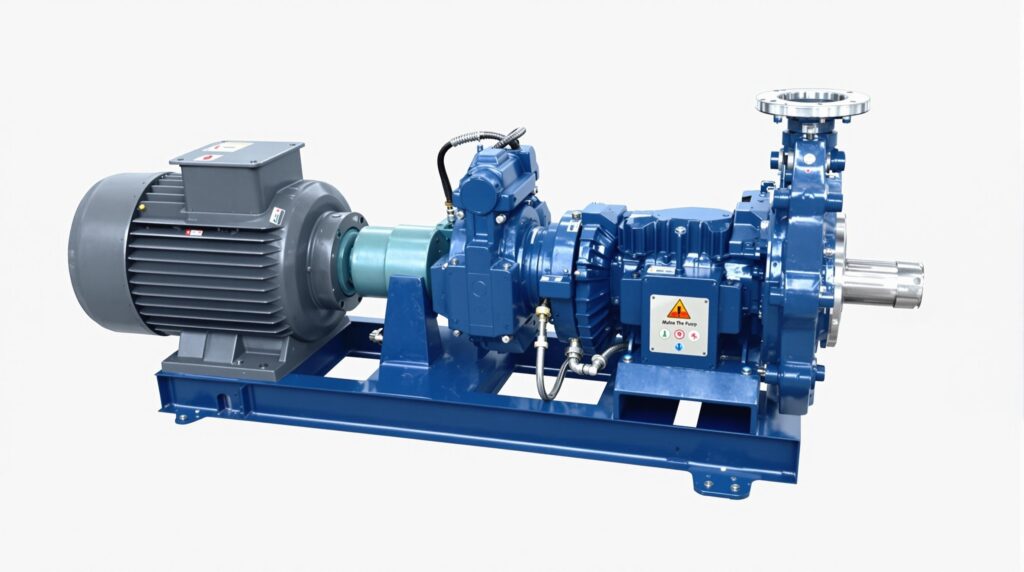
What Is a Positive Displacement Pump
A positive displacement pump is a type of pump that moves fluid by trapping a fixed amount of fluid in a cavity and then forcing or displacing that volume into the discharge pipe. Unlike centrifugal pumps, which impart kinetic energy to the fluid, positive displacement pumps create a consistent flow by repeatedly enclosing and transferring fixed volumes of fluid.
This mechanism allows positive displacement pumps to handle viscous fluids and generate high pressures, making them ideal for applications requiring accurate dosing, high pressure, and the handling of challenging fluids.
Operating Principles of Positive Displacement Pumps
Positive displacement pumps operate by mechanically trapping a fixed volume of fluid and moving it from the suction side to the discharge side of the pump. These pumps use an expanding cavity on the suction side and a decreasing cavity on the discharge side. As the cavity on the suction side expands, fluid is drawn into the pump. As the cavity collapses, the fluid is forced out through the discharge line. This process creates a consistent flow, proportional to the speed of operation, regardless of the pressure. Positive displacement pumps are categorized into two main types: reciprocating and rotary.
- Reciprocating pumps, like piston, plunger, and diaphragm pumps, use a back-and-forth movement to create the pumping action.
- Rotary pumps, such as gear, lobe, screw, and vane pumps, use rotating elements to move fluid.
The pressure generated by these pumps is determined by the resistance of the system, and they can achieve high pressures without a significant drop in flow rate. It is important to note that a positive displacement pump will continue to produce flow even against a closed discharge, leading to a rapid increase in pressure, which makes pressure relief or safety valves necessary.
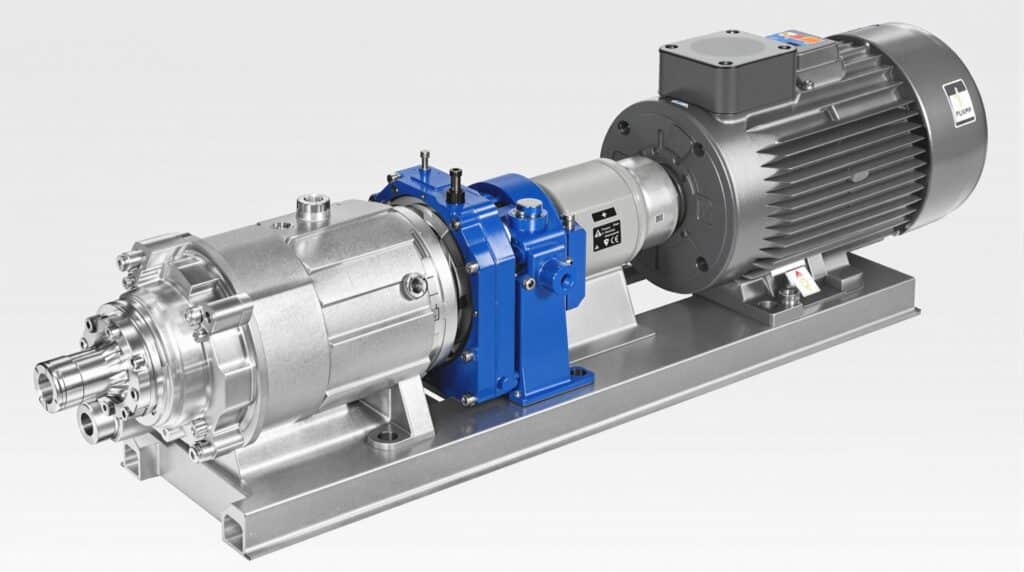
Comparing Centrifugal and Positive Displacement Pumps
Mechanism of Operation
Centrifugal pumps operate by using an impeller to impart kinetic energy to the fluid, which increases velocity and subsequently the pressure, moving it through the pump. They do not trap fixed volumes of fluid, instead, they create pressure to move the fluid.
Positive displacement pumps, on the other hand, operate by trapping a fixed volume of fluid within a chamber and forcing it out into the discharge line using a mechanical action. This direct displacement mechanism allows them to maintain a consistent flow rate regardless of pressure changes.
Flow Rate Characteristics
Centrifugal pumps exhibit a variable flow rate that changes with system pressure. As the pressure increases, the flow rate decreases, and vice-versa.
Positive displacement pumps deliver a nearly constant flow rate, irrespective of changes in pressure. The flow rate is proportional to the pump’s operating speed, making them ideal for applications needing a predictable and consistent output.
Viscosity Handling
Centrifugal pumps are best suited for low-viscosity fluids such as water, solvents, and light oils. Their performance significantly decreases with higher viscosity fluids due to increased frictional losses inside the pump. The flow rate rapidly decreases as the viscosity increases.
Positive displacement pumps excel at handling high-viscosity fluids, such as thick oils, syrups, and slurries. The flow rate can actually increase with increasing viscosity. They are designed with internal clearances that accommodate thick fluids, ensuring a consistent flow regardless of viscosity.
Suction Lift Abilities
Standard centrifugal pumps are not self-priming and cannot create a suction lift, meaning they cannot draw fluid upwards into the pump.
Positive displacement pumps, due to their design, can create a vacuum on the inlet side, allowing them to draw fluids from below the pump’s level, providing suction lift capabilities.
Shearing Considerations
Centrifugal pumps, with their high-speed impellers, can cause shearing of fluids, which can be a problem for shear-sensitive materials. The high-speed motor can degrade the fluid as it passes through the pump.
Positive displacement pumps produce less shearing, making them a better choice for fluids that are sensitive to mechanical stress or those containing fragile solids. They are often used to gently handle shear-sensitive fluids and those containing fragile solids.
Maintenance Demands
Centrifugal pumps generally have lower maintenance needs due to their simple design and fewer moving parts. This makes them suitable for continuous operation. However, issues such as cavitation, impeller wear, and seal leaks can require attention.
Positive displacement pumps typically have more complex mechanisms with multiple moving parts, leading to higher maintenance requirements.
Typical Cost Differences
Centrifugal pumps are usually more cost-effective to purchase due to their simpler design and widespread availability. They also often have lower maintenance costs.
Positive displacement pumps have higher initial costs, especially for specialized types, because of their more complex designs. They also have higher maintenance costs due to the more complex internal components and more wear-prone parts. However, they can be more energy efficient when dealing with high viscosity fluids.
Typical Applications
Centrifugal pumps are commonly used for applications involving low-viscosity fluids and high flow rates. These include water supply and circulation, irrigation, wastewater treatment, chemical processing, oil and gas production, HVAC systems, and power generation. They are also used to transfer and process large quantities of liquid during cooking, packaging, or cleaning processes in food processing.
Positive displacement pumps are preferred for applications that require accurate dosing, high pressure, and the handling of viscous or shear-sensitive fluids. Typical uses include pumping thick oils, metering chemicals, transferring ingredients, syrups, and finished products in food processing, handling corrosive, abrasive, and high-viscosity fluids in chemical processing, and precise dosing in pharmaceuticals.
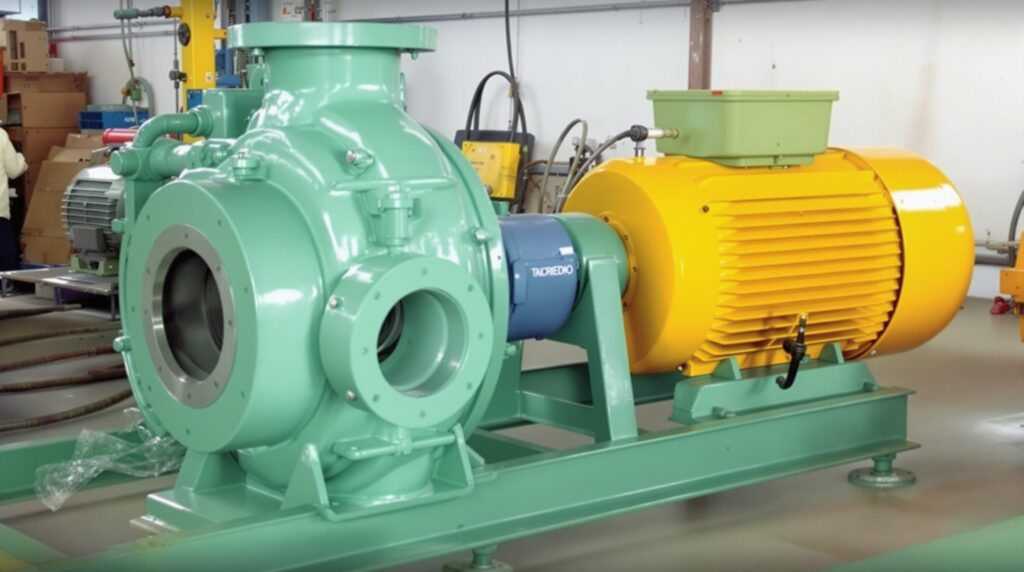
How to Select the Right Pump for Your Application
Defining Your System Requirements
The first step is to clearly define your system requirements. This includes understanding the fluid to be pumped, the required flow rate, the pressure needed, and any specific operational conditions. Determine the volume of fluid that needs to be moved within a given time frame. The flow rate is typically measured in gallons per minute (GPM) or liters per minute (LPM).
Assess the total pressure or head that the pump must overcome. This includes static head (the vertical distance the fluid must be lifted) and friction losses within the piping system.
Fluid Properties
The properties of the fluid being pumped are a key factor in selecting the right pump. Viscosity, which refers to the fluid’s thickness or resistance to flow, affects the performance of both pump types. Centrifugal pumps are suitable for low-viscosity fluids, while positive displacement pumps are better for high-viscosity fluids. Other fluid properties such as density, corrosiveness, and the presence of solids should also be considered.
Flow Rate Requirements
The required flow rate is a critical parameter. If the application requires a high and consistent flow rate at lower pressures, a centrifugal pump may be adequate for low viscosity applications. However, if the application requires a constant flow rate even under varying pressures, a positive displacement pump is a better option, especially if the viscosity is high. If there are fluctuations in demand, a centrifugal pump can adapt better.
Pressure (Head) Needs
The pressure or head requirements of the system are also important. If the application requires high pressure, a positive displacement pump is generally more suitable, as they can deliver a consistent flow rate without a significant drop in pressure. Centrifugal pumps are more effective for lower pressure applications and can have flow rates drop considerably when pressure increases.
Power requirements
The power requirement of the pump will influence operational costs. Centrifugal pumps are energy efficient under optimal conditions. Positive displacement pumps are more efficient at handling highly viscous fluids and can maintain efficiency across a range of pressures.
Also, consider the operating speed of each type of pump, as centrifugal pumps tend to run at higher speeds while positive displacement pumps run at lower speeds. These differences in operating speeds can impact seal life, and may influence the selection process.