What’s the difference between pumps in series and parallel flow configurations?
Pumps in series increase the pressure, while pumps in parallel increase the flow rate. The choice between series and parallel depends on the specific system requirements.
In this blog post, we’ll dive deeper into the characteristics and applications of pumps in series versus parallel.
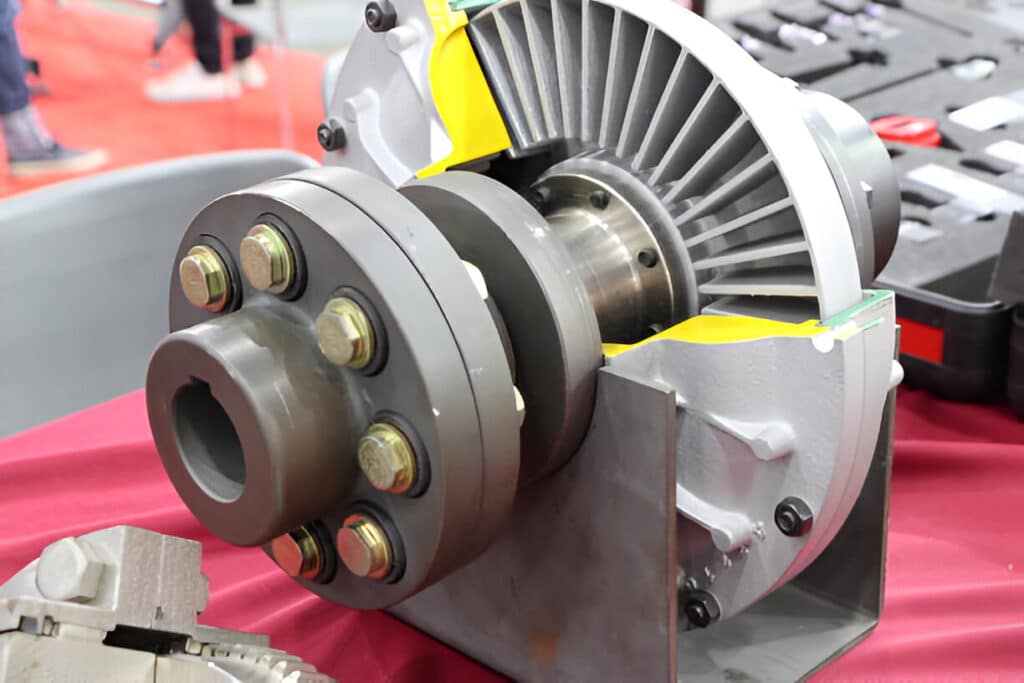
What is Pumps in Series
Pumps in series refers to a configuration where multiple pumps are connected sequentially, with the discharge of one pump feeding directly into the suction of the next.
This arrangement is used to achieve higher head pressures than a single pump can provide.
Centrifugal pumps are commonly used in series configurations to overcome large static heads or transport fluids over long distances.
Formula of Pumps in Series
The formula for pumps in series is straightforward:
H_{total} = H1 + H2 + … + Hn
Where H_total is the total head produced by the pumps in series, and H1, H2, etc. are the individual heads produced by each pump. The flow rate remains constant through all pumps in the series.
Advantages of Pumps in Series
- Increased total head pressure
- Ability to overcome large static heights
- Improved efficiency for high-head, low-flow applications
- Flexibility to adjust system performance by adding or removing pumps
- Reduced energy consumption compared to a single large pump
- Enhanced reliability through redundancy
Disadvantages of Pumps in Series
- Increased complexity of system design and control
- Higher initial costs due to multiple pump units
- Potential for cavitation in downstream pumps if not properly designed
- Increased maintenance requirements
- Greater space requirements compared to a single pump
- Potential for pressure buildup and equipment damage if not properly managed
Examples of Pumps in Series
- Multistage centrifugal pumps in water supply systems
- Boiler feed water pumps in power plants
- Pipeline booster stations for long-distance fluid transport
- High-rise building water distribution systems
- Reverse osmosis desalination plants
- Mining operations for transporting slurries over long distances
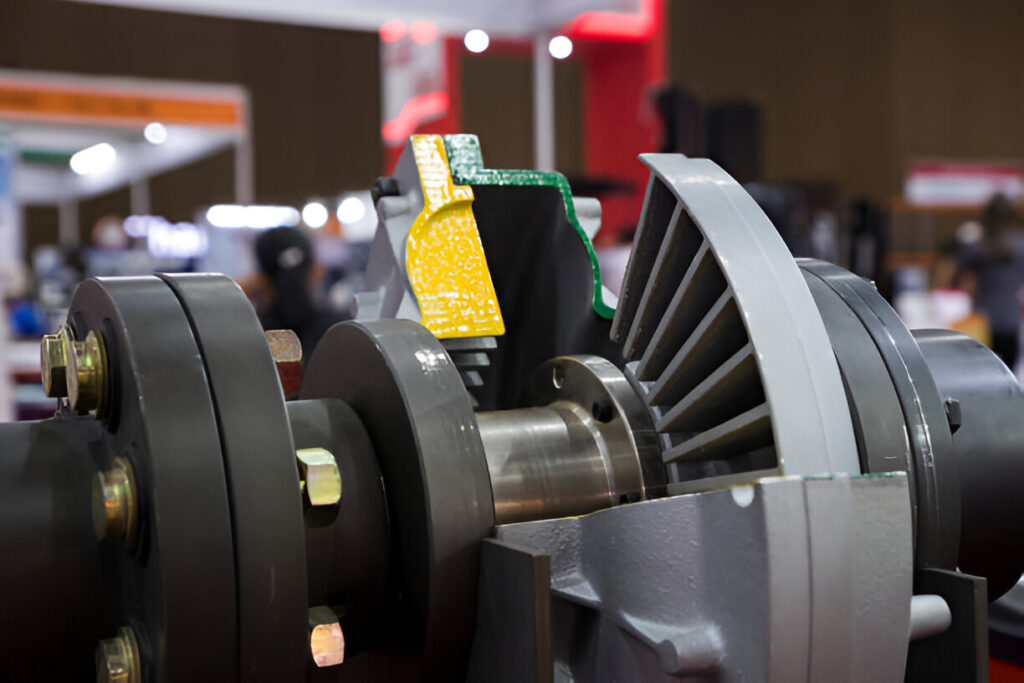
What is Pumps in Parallel
Pumps in parallel refers to an arrangement where two or more pumps are connected to a common discharge line and share the same suction conditions.
This configuration is used to increase the flow rate of a system while maintaining the same head. In a parallel setup, the pumps operate simultaneously, each contributing to the total flow output.
Parallel pumping is commonly employed in systems that require variable flow rates or have fluctuating demand.
Formula of Pumps in Parallel
The formula for pumps in parallel focuses on the addition of flow rates. For identical pumps in parallel, the total flow rate (Q_total) is the sum of individual pump flow rates:
Q_{total} = Q_1 + Q_2 + … + Q_n
Where Q_1, Q_2, etc., represent the flow rates of individual pumps.
For the head (H), all pumps in parallel operate at the same head:
H_{total} = H_1 = H_2 = … = H_n
The composite pump curve for parallel pumps is created by adding the flow rates horizontally at constant head values.
Advantages of Pumps in Parallel
- Increased system flexibility to handle varying flow demands
- Improved energy efficiency during periods of low flow
- Enhanced reliability through redundancy
- Ability to maintain partial capacity if one pump fails
- Easier maintenance as individual pumps can be serviced without shutting down the entire system
- Better matching of pump output to system requirements
- Reduced wear on individual pumps due to load sharing
Disadvantages of Pumps in Parallel
- Potential for hydraulic imbalance if pumps are not properly matched
- Increased complexity in system design and control
- Higher initial installation costs compared to single large pump systems
- Possible reduction in efficiency if operating far from the best efficiency point
- Risk of deadheading (no flow) in weaker pumps if not properly controlled
- Increased space requirements for multiple pump installations
Examples of Pumps in Parallel
- Water supply systems in high-rise buildings
- Municipal water distribution networks
- Cooling water systems in power plants
- Irrigation systems for large agricultural operations
- Industrial process water supply in manufacturing facilities
- Wastewater treatment plant influent pumping stations
- Chilled water systems in large commercial HVAC applications
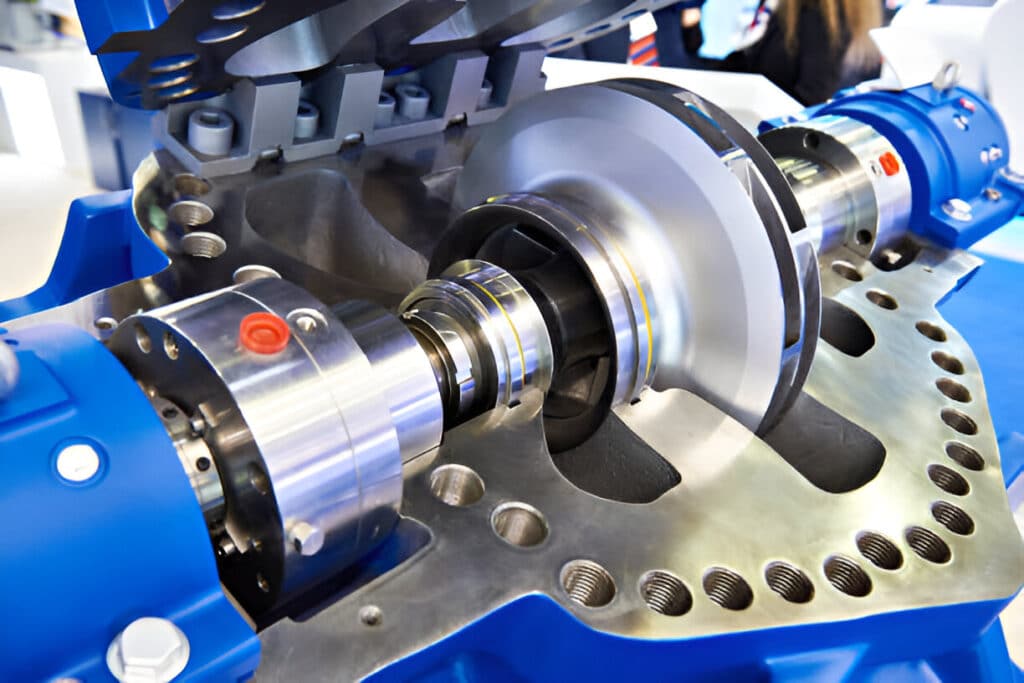
Difference between Pumps in Series vs Parallel
Configuration and Flow Characteristics
Pumps in series: Pumps are connected sequentially, with the discharge of one pump feeding into the suction of the next. This arrangement increases the total head while maintaining the same flow rate.
Pumps in parallel: Pumps are connected side-by-side, with their discharges combining into a common outlet. This configuration increases the total flow rate while maintaining the same head.
Head and Flow Rate Effects
Pumps in series: Total head is the sum of individual pump heads, allowing for higher pressure or elevation gains. Flow rate remains constant through each pump.
Pumps in parallel: Individual flow rates are added, increasing the overall system capacity. Head remains the same across all pumps.
Applications and Advantages
Series configurations: Series configurations are ideal for overcoming high static heads or long distances. They are commonly used in multi-stage pumps and high-rise building water supply systems.
Parallel arrangements: Parallel arrangements are suitable for variable flow conditions and provide operational flexibility. They allow for energy-efficient operation by activating additional pumps only when higher flow rates are required.
System Curves and Performance
Pumps in series: The composite pump curve for series pumps shows increased head at the same flow rate.
Pumps in parallel: For parallel pumps, the curve displays increased flow at the same head.
Combining Series and Parallel
Series-parallel
Series-parallel pump configurations combine the advantages of both arrangements. This setup increases the total head by connecting pumps in series, while also boosting flow rate through parallel connections. The compact arrangement allows for efficient use of space in pump stations.
Series-parallel configurations are particularly useful in applications requiring both high pressure and high flow rates, such as in large-scale water distribution systems or industrial processes with varying demands.
Parallel-series
Parallel-series pump arrangements offer exceptional flexibility to meet a wide range of operating conditions. This configuration allows for efficient operation across varying flow and pressure requirements. By adjusting the number of pumps operating in parallel and series, the system can adapt to changing demands while maintaining optimal energy efficiency.
Parallel-series setups are commonly used in applications with fluctuating needs, such as HVAC systems in large buildings or water supply networks with variable consumption patterns.
In Conclusion
Pumps in series and parallel offer distinct advantages for different applications. Series configurations increase head, while parallel setups boost flow rate. The choice depends on specific system requirements and operational needs.
Proper selection and configuration of pumps can significantly enhance efficiency and performance. Consult with a pump specialist to determine the optimal arrangement for your system.