Ever wondered how some hydraulic systems achieve efficient fluid transfer in compact spaces?
An internal gear pump is a positive displacement pump that uses two gears to move fluid within a compact casing.
This pump type is known for its smooth operation and ability to handle high-viscosity fluids. Its design allows for high efficiency and reduced noise, making it ideal for various industrial applications.
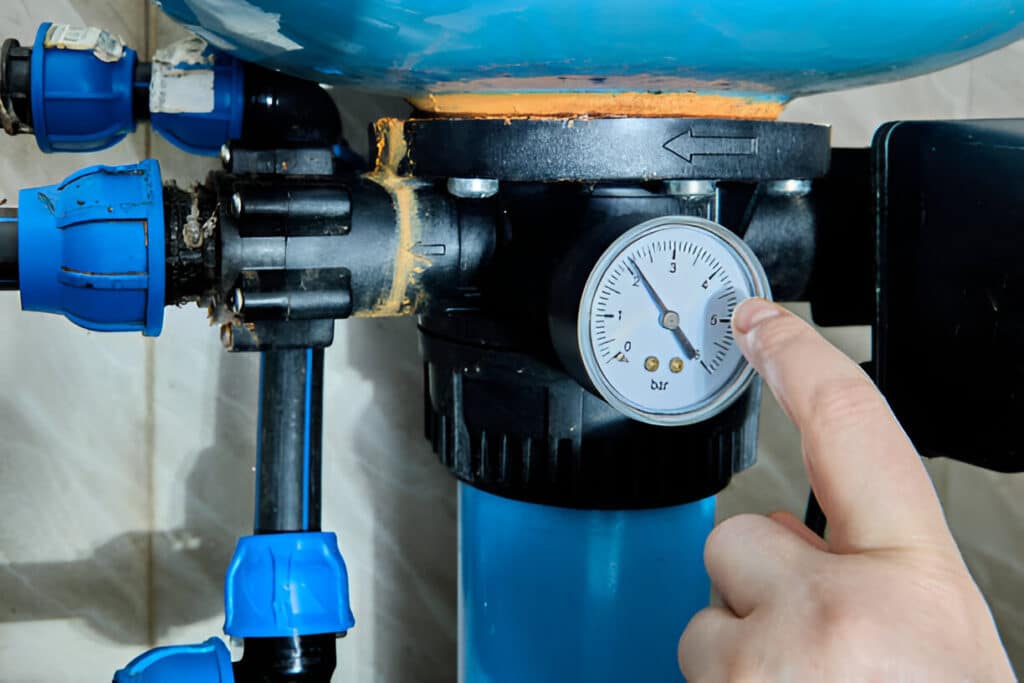
What Is an Internal Gear Pump
An internal gear pump is a type of positive displacement pump designed to handle fluids with a wide range of viscosities. It consists of two main components: a larger external rotor gear with internal teeth and a smaller idler gear that meshes with it. The idler gear is positioned off-center within the rotor gear, creating a crescent-shaped space between them.
Types of Internal Gear Pump
External Gear Pumps
External gear pumps utilize two identical gears mounted on separate shafts. These pumps excel in high-pressure applications and handle a wide range of viscosity fluids. The meshing gears create a liquid seal with the pump casing, drawing fluid into the suction port and expelling it through the discharge port.
External gear pumps are commonly used for hydraulic power applications, fuel oils, and lube oil transfer. They offer accurate flow control and are suitable for metering operations.
Internal Gear Pumps
Internal gear pumps consist of a larger outer rotor gear and a smaller inner idler gear. This design allows for handling highly viscous fluids and shear-sensitive materials. The crescent-shaped partition between the gears aids in fluid transfer from the inlet to the outlet.
Internal gear pumps are versatile, capable of pumping fluids ranging from 1 cP to over 1,000,000 cP. They are often employed in food processing, chemical blending, and bulk transfer applications. These pumps provide a smooth, constant flow and have excellent self-priming capabilities.
How Does an Internal Gear Pump Work
The operation of an internal gear pump begins as fluid enters the suction port between the rotor and idler gears.
As the gears rotate, they create an expanding volume that draws fluid into the spaces between the gear teeth. The fluid is then trapped and carried around the pump casing in the cavities formed by the meshing gears.
As the gears continue to rotate, they come back into mesh near the discharge port, reducing the volume and forcing the fluid out under pressure. This process creates a smooth, continuous flow with minimal pulsation.
The crescent-shaped partition in the pump casing plays a crucial role by sealing the fluid between the inlet and outlet ports, preventing backflow and ensuring efficient operation.
Components of Internal Gear Pump
- Rotor gear: Larger gear with internal teeth, externally driven
- Idler gear: Smaller gear nested inside the rotor gear
- Pump casing: Houses gears and creates liquid seal
- Crescent-shaped partition: Fills void between gears, separates inlet/outlet ports
- Suction port: Fluid entry point
- Discharge port: Pressurized fluid exit point
- Drive shaft: Connects rotor gear to power source
- Bearings: Support rotating components
- Seals: Prevent fluid leakage
- Relief valve: Protects against over-pressurization
- End plates: Enclose pumping chamber on both sides
- Mounting brackets: Secure pump in place
Advantages of Internal Gear Pump
- Smooth, Pulseless Flow Well-Suited for Metering and Dosing
- Wide Viscosity Range from Thin Solvents to Thick Syrups and Polymers
- Ability to Handle High Temperatures
- Bi-Directional Pumping for Loading/Unloading with Same Pump
- Self-Priming and Can Run Dry for Short Periods without Damage
- Simple Design with Only Two Moving Parts for High Reliability
- Compact and Relatively Inexpensive Compared to Other Pump Types
- Suitability for Shear-Sensitive Fluids and Hygienic Applications
Disadvantages of Internal Gear Pump
- Not Suitable for Abrasive Fluids or Fluids with Large Solids
- Potential for Accelerated Wear with Continuous Use on Abrasive Fluids
- Requires Clean Fluid and Filtration to Avoid Clogging and Damage
- Flow Slip Increases at Very Low Viscosity and High Pressure
- Maximum Pressure and Speed Limitations Compared to Some Other Pumps
Applications of Internal Gear Pump
- Food Processing – Chocolate, Dairy, Juices, Sauces
- Petroleum – Fuel Oils, Lubricants, Asphalt
- Chemical – Polymers, Adhesives, Solvents, Detergents
- Plastics – Resins, Polymers, Silicones
- Pharmaceutical – Lotions, Ointments, Cosmetics
- Pulp & Paper – Coatings, Dyes, Adhesives
FAQs
Are Internal Gear Pumps Self-Priming?
Internal gear pumps are generally not self-priming. They require a flooded suction or external priming mechanism. These pumps can handle some air but need liquid in the pump chamber to create suction and maintain efficient operation.
How Do I Know If My Gear Pump Is Bad?
- Unusual noises (grinding, whining)
- Decreased performance or flow rate
- Leaks from seals or joints
- Excessive heat generation
- Pressure fluctuations
- Contaminated hydraulic fluid
- Increased power consumption
How to Prime a Gear Pump?
To prime a gear pump:
- Fill the pump casing with fluid
- Ensure inlet line is filled
- Open discharge valve slightly
- Start the pump briefly
- Repeat if necessary
- Close air bleed valves when fluid flows steadily
In Conclusion
Internal gear pumps are versatile positive displacement pumps suitable for a wide range of viscosities and applications. They offer smooth, precise flow control and are ideal for handling challenging fluids like asphalt, chemicals, and food products.
For optimal performance, consider an internal gear pump for high-viscosity or temperature-sensitive applications. Consult a pump specialist to determine the best solution for specific needs.