EPT (Ethylene Propylene Terpolymer) and EPDM (Ethylene Propylene Diene Monomer) are two synthetic rubber compounds widely utilized in various industrial applications. While both materials share similarities in their chemical composition, they exhibit distinct properties that make them suitable for different purposes.
This article will delve into the key differences between EPT and EPDM, focusing on their chemical structures, physical characteristics, and typical applications in the machinery industry.
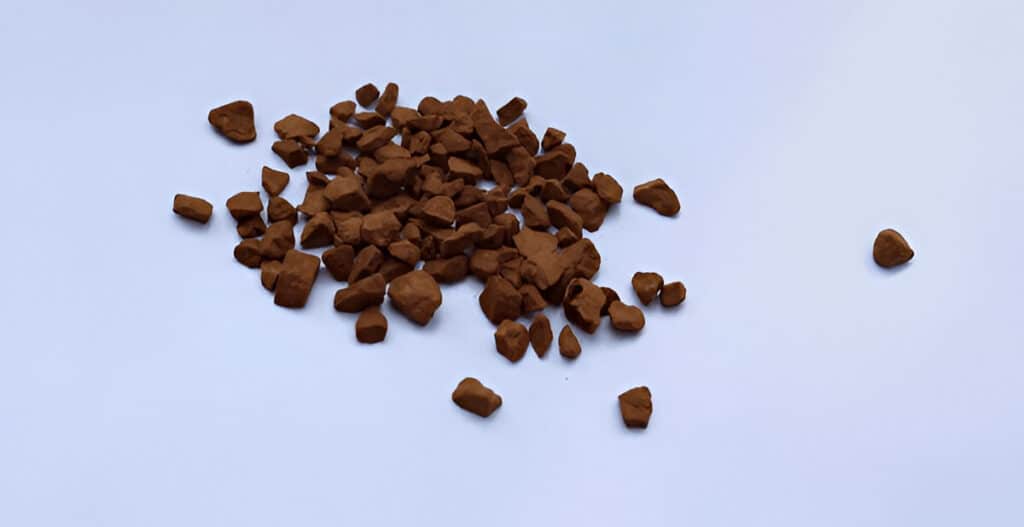
What Is EPT
EPT, short for Ethylene Propylene Terpolymer, is a synthetic rubber material that belongs to the family of Ethylene Propylene Diene Monomer (EPDM) elastomers. EPT is produced by polymerizing ethylene, propylene, and a third non-conjugated diene monomer. The specific diene used in EPT is 1,4-hexadiene (HD), which distinguishes it from other EPDM rubbers that use different diene monomers.
The inclusion of HD in EPT provides the rubber with enhanced properties compared to conventional Ethylene Propylene Rubber (EPR). EPT exhibits improved heat resistance, oxidation stability, and resistance to weathering and ozone. These properties make EPT suitable for applications that require durability in harsh environments, such as automotive seals, hoses, and weatherstripping.
What Is EPDM
EPDM, or Ethylene Propylene Diene Monomer, is a synthetic rubber that is widely used in numerous applications due to its excellent physical and chemical properties. EPDM is a terpolymer, meaning it is composed of three monomers: ethylene, propylene, and a non-conjugated diene. The most commonly used dienes in EPDM production are ethylidene norbornene (ENB), dicyclopentadiene (DCPD), and 1,4-hexadiene (HD).
EPDM exhibits outstanding resistance to ozone, UV radiation, and weathering, making it ideal for outdoor applications. It also has good resistance to water, steam, and various polar substances. EPDM’s electrical insulation properties are excellent, and it can withstand temperatures ranging from -50°C to +150°C, depending on the specific formulation.
The versatility and durability of EPDM make it a popular choice for automotive parts, roofing membranes, seals, gaskets, hoses, and electrical insulation. Its ability to maintain its properties in demanding environments has led to its widespread adoption across industries.
Key Difference Between EPT and EPDM
Composition
EPT, or ethylene propylene terpolymer, consists of ethylene, propylene, and a small amount of a non-conjugated diene monomer. The specific diene used can vary, but common examples include ethylidene norbornene (ENB) and dicyclopentadiene (DCPD). The incorporation of the diene monomer allows for vulcanization using sulfur or peroxides.
In contrast, EPDM, or ethylene propylene diene monomer, is composed of ethylene, propylene, and a larger amount of a non-conjugated diene monomer compared to EPT. The most commonly used diene monomers in EPDM are ENB, DCPD, and 1,4-hexadiene. The higher diene content in EPDM enables better vulcanization and cross-linking.
Performance Characteristics
EPT exhibits good resistance to heat, ozone, and weathering. It has excellent electrical insulation properties and maintains flexibility at low temperatures. EPT also demonstrates good resistance to acids, alkalis, and polar solvents. However, it has limited resistance to oils and non-polar solvents.
EPDM, on the other hand, offers superior resistance to heat, ozone, weathering, and aging compared to EPT. It has excellent resistance to acids, alkalis, polar solvents, and steam. EPDM also provides good electrical insulation properties and low-temperature flexibility. Additionally, EPDM shows better resistance to oils and non-polar solvents than EPT.
Applications
EPT finds applications in various industries due to its specific properties. It is commonly used in the automotive industry for hoses, seals, and weather stripping. In the electrical and electronics sector, EPT is employed for wire and cable insulation. It is also utilized in the construction industry for roofing membranes and window seals.
EPDM, with its superior performance characteristics, has a wide range of applications. In the automotive industry, it is used for hoses, seals, O-rings, and weather stripping. EPDM is also extensively employed in the construction sector for roofing membranes, pond liners, and window and door seals. In the electrical and electronics industry, EPDM is used for wire and cable insulation, as well as for gaskets and seals in appliances.