PTFE (polytetrafluoroethylene) and EPDM (ethylene propylene diene monomer) are two widely used synthetic materials in various industrial applications. While both offer unique properties and benefits, they differ significantly in their chemical composition, temperature resistance, and suitability for specific environments.
This article will delve into the key distinctions between PTFE and EPDM, examining their characteristics, advantages, and typical use cases in the machinery industry.
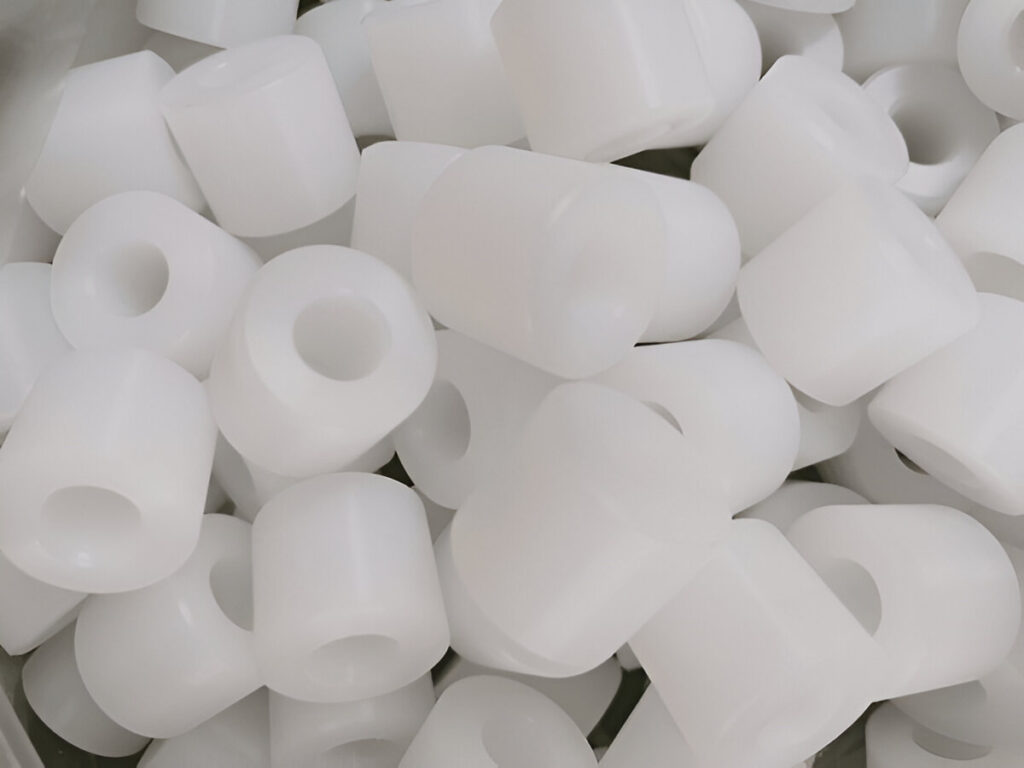
What Is PTFE
PTFE (polytetrafluoroethylene) is a synthetic fluoropolymer known for its excellent chemical resistance, low friction coefficient, and high temperature stability. This thermoplastic polymer consists of carbon and fluorine atoms arranged in a linear chain, with strong carbon-fluorine bonds contributing to its unique properties.
PTFE is hydrophobic and oleophobic, repelling both water and oil. It has a very low dielectric constant, making it an excellent insulator for electrical applications. PTFE’s low surface energy results in a non-stick surface, preventing adhesion of other materials.
One of PTFE’s most notable characteristics is its wide operating temperature range, maintaining its properties from -200°C to +260°C. It does not melt but undergoes a phase transition at 327°C. PTFE has a high density of around 2.2 g/cm³, contributing to its mechanical strength and durability.
PTFE finds applications in various industries due to its unique combination of properties. It is used in non-stick cookware coatings, bearings, seals, gaskets, and electrical insulation. PTFE is also utilized in chemical processing equipment, medical devices, and aerospace components.
What Is EPDM
EPDM (ethylene propylene diene monomer) is a synthetic rubber known for its excellent resistance to heat, ozone, and weather. This elastomer is composed of ethylene, propylene, and a diene monomer, forming a saturated polymer backbone with unsaturated side chains.
EPDM has a lower density compared to PTFE, typically ranging from 0.86 to 0.88 g/cm³. This lower density contributes to its flexibility and elasticity, allowing it to return to its original shape after deformation.
One of EPDM’s key properties is its outstanding resistance to ozone, UV radiation, and weathering. It maintains its flexibility and mechanical properties even after long-term exposure to outdoor conditions. EPDM also exhibits good resistance to heat, with a continuous operating temperature range of -40°C to +150°C.
EPDM has good chemical resistance to dilute acids, alkalis, and polar solvents. However, it is not as chemically inert as PTFE and may degrade when exposed to concentrated acids, oils, or non-polar solvents.
The combination of weather resistance, flexibility, and durability makes EPDM suitable for various applications. It is commonly used in automotive seals and hoses, roofing membranes, electrical insulation, and waterproofing systems. EPDM is also found in seals for windows and doors, conveyor belts, and mechanical rubber goods.
Key Difference Between PTFE and EPDM
Density
PTFE has a higher density, typically ranging from 2.13 to 2.19 g/cm³, while EPDM has a lower density of about 0.86 g/cm³. The higher density of PTFE contributes to its superior mechanical properties and resistance to wear and tear.
Elasticity
EPDM is an elastomer, meaning it has excellent elasticity and can be stretched and compressed without permanent deformation.
PTFE, on the other hand, is a thermoplastic with limited elasticity.
Chemical Resistance
Both PTFE and EPDM offer excellent chemical resistance, but PTFE surpasses EPDM in this regard. PTFE is virtually chemically inert and resistant to a wide range of chemicals, including strong acids, bases, and solvents.
EPDM also has good chemical resistance but may swell or degrade when exposed to certain chemicals, such as oils and fuels.
Temperature Resistance
PTFE has a higher temperature resistance compared to EPDM. PTFE can withstand temperatures ranging from -200°C to +260°C, making it suitable for high-temperature applications.
EPDM has a lower temperature range, typically from -50°C to +150°C, which limits its use in extreme temperature environments.
Mechanical Strength
PTFE exhibits superior mechanical strength compared to EPDM. PTFE has a higher tensile strength, ranging from 20 to 35 MPa, while EPDM has a tensile strength of about 10 MPa.
PTFE’s higher mechanical strength makes it more resistant to wear, abrasion, and deformation, making it suitable for applications requiring durability and long service life.
Applications
PTFE is commonly used in applications requiring low friction, high temperature resistance, and excellent chemical resistance, such as seals, gaskets, and bearings in chemical processing, automotive, and aerospace industries.
EPDM, with its elasticity and good chemical resistance, is often used in applications requiring sealing and weathering resistance, such as roofing membranes, automotive seals, and electrical insulation.