What’s the difference between an axial compressor and a centrifugal compressor? Both types of compressors are used to increase the pressure of a gas, but they achieve this in different ways.
An axial compressor uses a series of rotating blades to gradually increase the pressure of the gas as it moves through the compressor. In contrast, a centrifugal compressor uses a rotating impeller to accelerate the gas, which then slows down and increases in pressure.
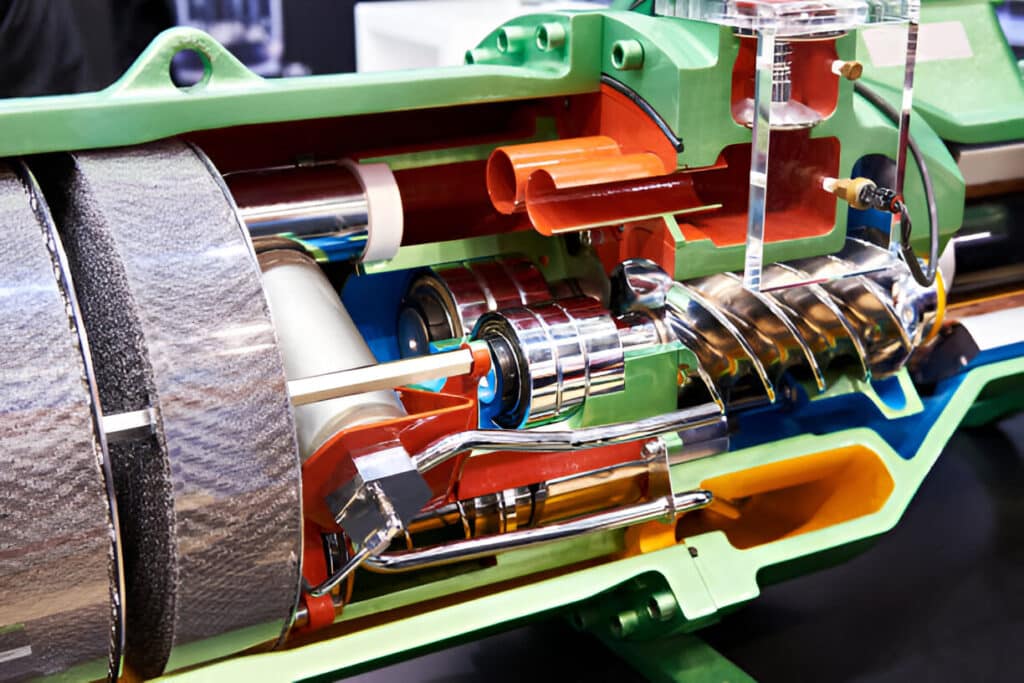
What is Axial Compressor
An axial compressor is a type of dynamic compressor that increases the pressure of a gas by applying kinetic energy. It consists of a series of airfoil-shaped blades arranged in a circular array around a central shaft or drum.
Axial compressors are commonly used in gas turbines for power generation, as well as in aircraft engines such as turbojets and turbofans. They are capable of handling large volumes of gas and achieving high compression ratios, making them suitable for applications requiring high flow rates and moderate pressure ratios.
How Does Axial Compressor Work
In an axial compressor, air flows parallel to the axis of rotation through a series of rotating and stationary blades. The rotating blades, known as rotors or impellers, accelerate the air, while the stationary blades, called stators, convert the increased kinetic energy into pressure.
This process is repeated across multiple stages, with each stage consisting of a rotor followed by a stator, gradually increasing the pressure of the air.
Advantages of Axial Compressors
- Higher efficiency: Axial compressors achieve higher peak efficiency.
- Larger flow rate: They handle a larger volume of gas flow.
- Higher compression ratios: Using multiple stages, they achieve higher overall compression ratios, allowing for greater pressure increases in a compact design.
- Wider operating range: Axial compressors offer a wider range in flow rate and pressure ratio, providing more flexibility.
- Lightweight design: They are more compact and lightweight.
Disadvantages of Axial Compressors
- Aerodynamic sensitivity: More susceptible to stall and flow disruptions due to blade angle changes.
- Multiple stages: Requires 10-15 stages for pressure ratios comparable to centrifugal compressors, increasing complexity and weight.
- Limited operating range: Narrower range compared to centrifugal compressors, reducing application flexibility.
- Efficiency variability: More sensitive to changes in gas composition and inlet conditions.
- Cost: Generally more expensive to manufacture and maintain due to complex design and precision requirements.
- Vulnerability: More prone to damage from foreign objects or debris.
- Pressure ratio limitations: Less suitable for high pressure ratios in a single stage.
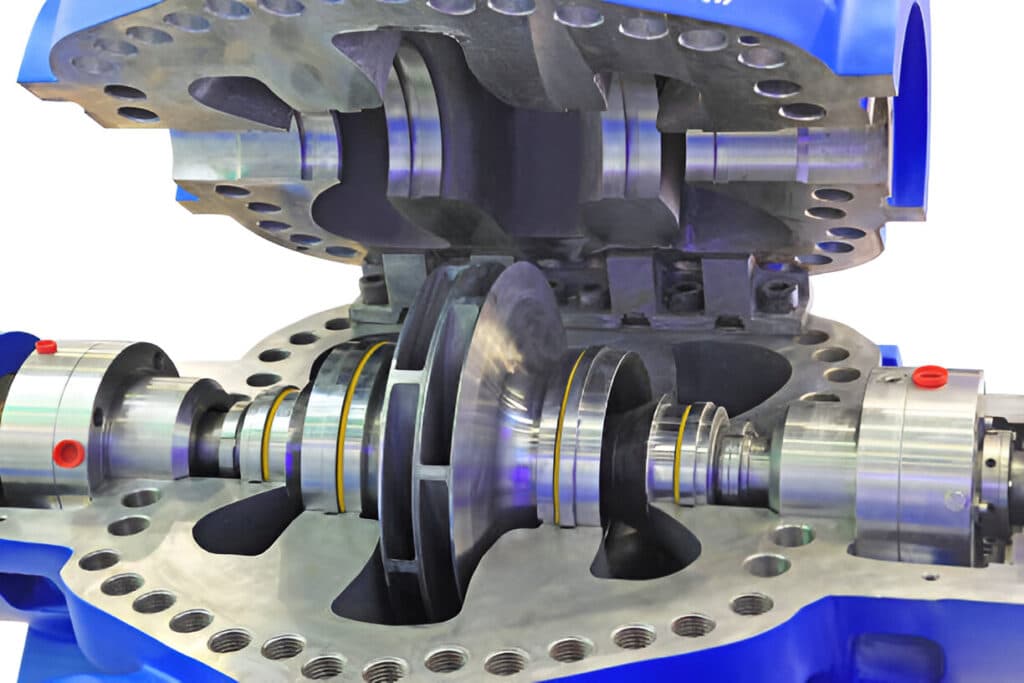
What is Centrifugal Compressor
A centrifugal compressor is a dynamic compressor that uses an impeller to increase the velocity and pressure of a gas. The impeller is a rotating disk with curved blades that draw in the gas and accelerate it radially outward.
These compressors are commonly used in various industries, including oil and gas, petrochemical, and automotive, for tasks such as gas compression, air separation, and turbocharging. Centrifugal compressors offer several advantages, including a wide operating range, compact design, and the ability to handle a variety of gas compositions.
How Does Centrifugal Compressor Work
A centrifugal compressor uses an impeller to draw in gas and accelerate it radially outward. As the gas flows through the impeller, its velocity increases, converting kinetic energy into pressure.
The compressed gas is then discharged into a diffuser, which slows down the flow and further increases the pressure.
Advantages of Centrifugal Compressor
- Wide operating range: Handles varying gas compositions and flow rates more effectively than axial compressors.
- Compact design: Requires fewer stages for the same pressure ratio, suitable for limited space applications.
- Stable operation: Less susceptible to flow disruptions and aerodynamic stall across a broad range of conditions.
- Simple design: Single impeller allows for easier maintenance and lower manufacturing costs compared to multi-stage axial compressors.
- Contaminant tolerance: More tolerant of small particles in the gas stream, reducing risk of component damage.
Disadvantages of Centrifugal Compressor
- Limited pressure ratios: Lower pressure ratios per stage compared to axial compressors.
- Lower efficiency at high flow rates: Less efficient than axial compressors when handling high flow rates.
- Larger size and weight: Generally bulkier and heavier than axial compressors for equivalent performance.
- Limited range of operation: Narrower operating range compared to axial compressors.
- Susceptibility to surge: More prone to flow instability, requiring careful design and control measures.
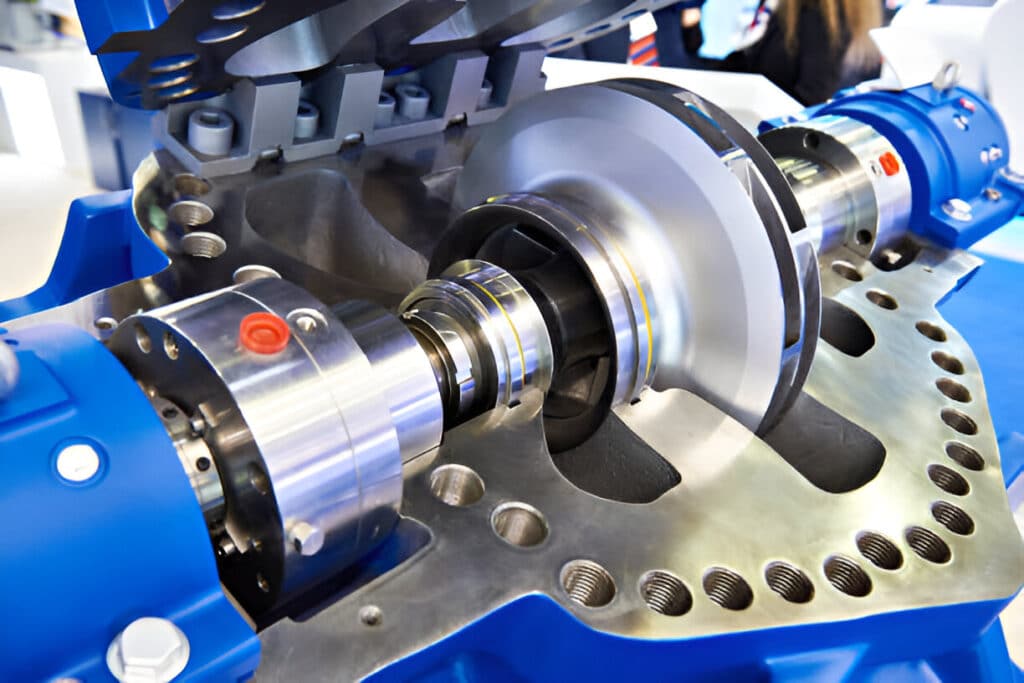
Factors to Consider When Choosing Axial Compressor or Centrifugal Compressor
Pressure Ratio and Flow Rate
Axial compressors: Axial compressors are suitable for high flow rate applications with moderate pressure ratios.
Centrifugal compressors: Centrifugal compressors are ideal for high pressure ratio and low flow rate applications.
Efficiency
Axial compressors: Axial compressors generally have higher peak efficiency compared to centrifugal compressors.
Centrifugal compressors: Centrifugal compressors maintain efficiency over a wider range of operating conditions.
Size and Weight
Axial compressors: Axial compressors are typically longer and lighter than centrifugal compressors for the same pressure ratio.
Centrifugal compressors: Centrifugal compressors are more compact and have a smaller footprint.
Maintenance and Reliability
Axial compressors: Axial compressors are more susceptible to blade damage and flow disruptions.
Centrifugal compressors: Centrifugal compressors have fewer moving parts and are generally more reliable and easier to maintain compared to axial compressors.
Cost
Axial compressors are typically more expensive than centrifugal compressors for the same pressure ratio and flow rate.
FAQs
Are axial compressors more efficient
Axial compressors are generally more efficient than centrifugal compressors. They handle larger volumes of air. Axial compressors achieve higher pressure ratios per stage. They are preferred in gas turbines and jet engines for their efficiency.
Does Axial flow compressors have better power to weight ratio than centrifugal flow compressors
Axial flow compressors typically have a better power-to-weight ratio than centrifugal flow compressors. They are more compact and lighter for similar power output.
Which compressor type handles dirty air better
Centrifugal compressors are generally more tolerant of dirty air and particulates due to their simpler blade design and larger flow passages. Axial compressors are more sensitive to contamination.
Which type is easier to maintain
Centrifugal compressors are usually easier to maintain due to fewer moving parts and simpler construction. Axial compressors have more complex blade arrangements, requiring more intricate maintenance procedures.
In Conclusion
Both axial and centrifugal compressors have their unique advantages and applications. The choice between the two depends on specific requirements such as flow rate, pressure ratio, and space constraints.
For expert guidance on selecting the right compressor for your needs, consult with our experienced team today.