What makes carbide superior to steel in certain applications?
Carbide’s unique properties, such as high hardness and wear resistance, make it the preferred choice over steel for specific uses.
In this blog post, we’ll explore the key characteristics of carbide and steel, helping you make an informed decision.
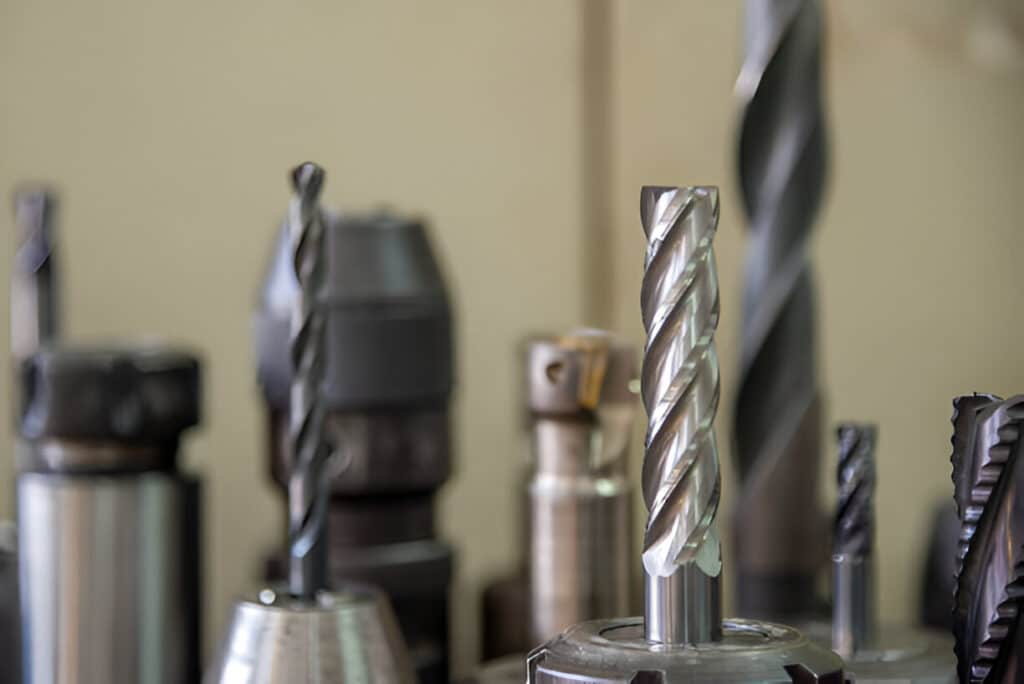
What is Carbide
Carbide is a compound of carbon and a less electronegative element, typically a metal. Tungsten carbide, a popular type, combines tungsten and carbon. Carbides are known for their extreme hardness, high melting points, and excellent wear resistance. These properties make carbide materials ideal for cutting tools and abrasives.
What is Steel
Steel is an alloy primarily composed of iron and carbon, with carbon content typically ranging from 0.2% to 2.1%. High-speed steel (HSS), a type of tool steel, often contains additional alloying elements like tungsten, molybdenum, and vanadium. Steel exhibits a balance of strength, toughness, and ductility, making it versatile for various applications.
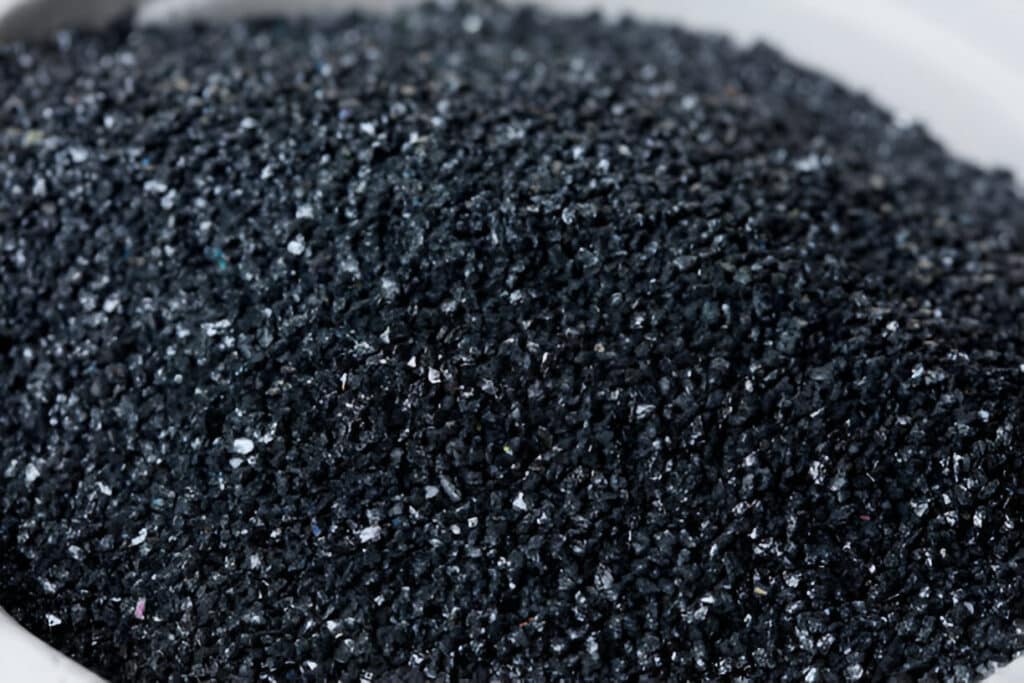
Properties Comparison
Hardness
Tungsten carbide: Tungsten carbide significantly outperforms steel in terms of hardness. Carbide tools typically have a hardness of 85-95 HRA.
Steel: High-speed steel (HSS) tools range from 62-65 HRC. This superior hardness allows carbide to maintain a sharper cutting edge for longer periods and machine harder materials more effectively.
Toughness
Steel: Steel generally exhibits greater toughness compared to carbide. High-speed steel has an impact toughness of 0.18-0.32 MJ/m2, making it more resistant to chipping and breakage.
Carbide: Carbide, being a ceramic material, is more brittle and prone to fracturing under impact, despite its higher hardness.
Wear Resistance
Carbide: Carbide demonstrates superior wear resistance compared to steel. The high hardness and presence of hard carbide particles in its microstructure contribute to this property. Carbide tools maintain their cutting edge and dimensional stability for longer periods, especially when machining abrasive materials.
Heat Resistance
Tungsten carbide: Tungsten carbide outperforms steel in heat resistance. Carbide tools can maintain their hardness and cutting efficiency at temperatures up to 800-1000°C. This superior heat resistance allows carbide tools to operate at higher cutting speeds.
Steel: The hardness of high-speed steel tools begins to decrease significantly at temperatures above 500°C.
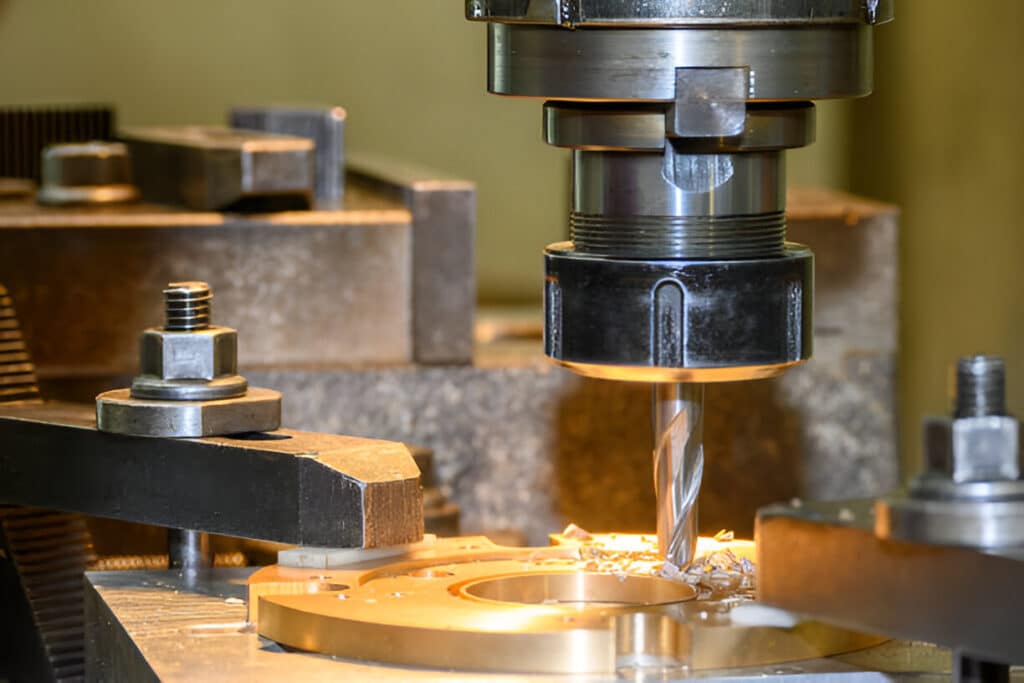
Differences Between Carbide vs. Steel
Property | Carbide | Steel |
---|---|---|
Hardness | 85-95 HRA (69-81 HRC) | 62-65 HRC for high-speed steel |
Toughness | Lower toughness, more brittle | Higher toughness, less brittle |
Wear Resistance | Excellent wear resistance | Good wear resistance, but lower than carbide |
Heat Resistance | Maintains hardness up to 800-1000°C | Loses hardness above 500-600°C |
Cutting Speed | 4-7 times faster than steel | Lower cutting speeds than carbide |
Tool Life | 5-80 times longer than steel tools | Shorter life than carbide tools |
Cost | More expensive | Less expensive than carbide |
Typical Applications | Cutting tools, mining tools, wear parts | Cutting tools, drill bits, general tooling |
FAQs
How can you tell carbide from steel?
Carbide is darker gray than steel. It’s heavier and harder. A magnet test can help – carbide is less magnetic. Carbide produces shorter, orange sparks when ground, while steel sparks are longer and brighter. Carbide is more brittle and can chip or crack.
Is carbide a type of steel?
No, carbide is not a type of steel. Carbide is a compound of carbon and metal, usually tungsten. Steel is an alloy of iron and carbon. Carbide is harder and more brittle than steel.
In Conclusion
Carbide and steel are both valuable materials with distinct properties and applications. Carbide excels in wear resistance and hardness, while steel offers strength, toughness, and versatility.
The choice between carbide and steel depends on the specific requirements of the application. Consider factors such as wear resistance, impact resistance, and cost when making a decision.
For personalized recommendations on material selection, consult with a qualified engineer or supplier.