Le giranti degli agitatori sono componenti essenziali in vari processi industriali, tra cui miscelazione, reazioni chimiche e applicazioni di trasferimento di calore. Sono disponibili in diversi tipi, ciascuno progettato per soddisfare esigenze specifiche in base a fattori quali la viscosità, i modelli di flusso del fluido e l'efficienza di miscelazione desiderata. Questo articolo discuterà i cinque tipi principali di giranti per agitatori: agitatori a elica, a turbina, a pale, ad ancora e a nastro elicoidale.
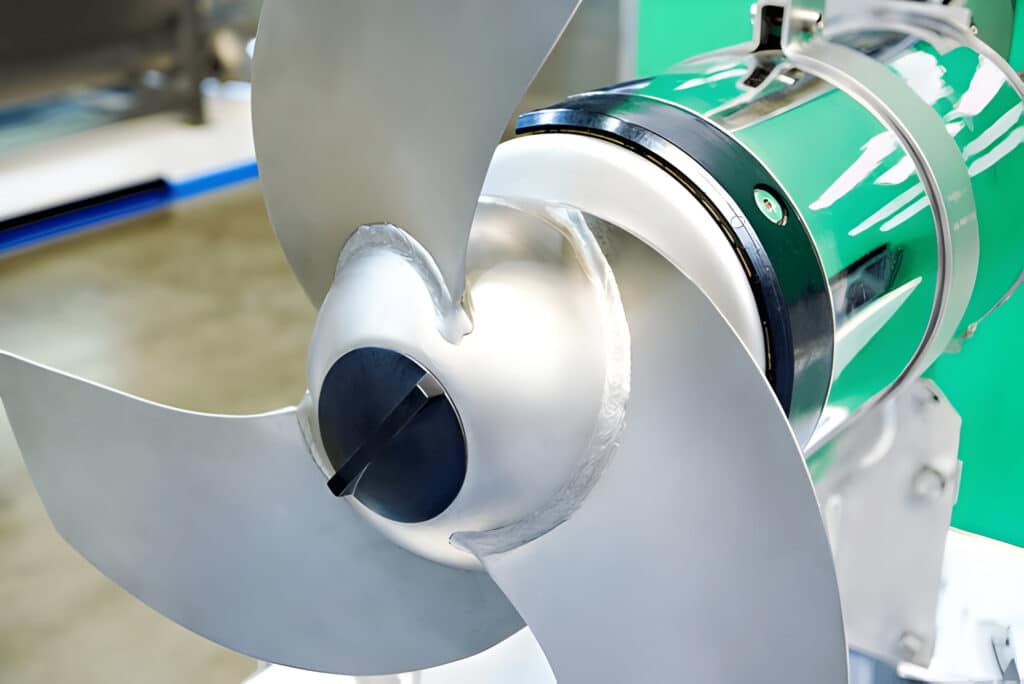
Giranti dell'agitatore dell'elica
Le giranti dell'agitatore, note anche come eliche marine o giranti a flusso assiale, sono un tipo versatile di girante utilizzato in vari processi industriali. Queste giranti generano uno schema di flusso assiale, ideale per la miscelazione di fluidi a viscosità da bassa a media.
Gli agitatori ad elica sono caratterizzati da un flusso elevato e da un basso taglio, che li rendono adatti per applicazioni che richiedono una miscelazione delicata o una sospensione solida.
Il design degli agitatori ad elica consiste tipicamente in un mozzo centrale con tre o più pale fissate ad un angolo di inclinazione specifico. L'angolo di inclinazione delle pale può variare a seconda dell'applicazione, essendo comune un angolo standard di 45°. Il diametro della girante viene solitamente selezionato in base al diametro del serbatoio, con un rapporto tipico compreso tra 1:3 e 1:2.
Giranti per agitatori a turbina
Le giranti degli agitatori a turbina offrono una gamma di modelli di flusso e capacità di miscelazione. Queste giranti sono progettate per gestire fluidi con viscosità da bassa a media e possono essere utilizzate per applicazioni di miscelazione di liquidi, sospensione solida, dispersione di gas e trasferimento di calore.
Esistono due tipi principali di giranti per turbine: flusso radiale e flusso assiale.
Giranti a flusso radiale: come la turbina Rushton, generano un flusso perpendicolare all'albero dell'agitatore, creando uno schema di flusso radiale ideale per la miscelazione gas-liquido e la sospensione solida.
Ventole a flusso assiale: come le turbine a pale inclinate o le giranti a profilo idrodinamico, producono un flusso parallelo all'albero dell'agitatore, determinando un modello di flusso assiale adatto alla miscelazione e alla sospensione solida in fluidi a viscosità da bassa a media.
Giranti per agitatori a pale
Le giranti dell'agitatore a pale sono costituite da pale piatte montate su un albero agitatore centrale, che creano uno schema di flusso radiale che favorisce una miscelazione efficace. Gli agitatori a pale sono adatti per un'ampia gamma di processi industriali, tra cui miscelazione, sospensione di solidi e applicazioni di trasferimento di calore.
Il design a pale piatte delle giranti a pale genera un elevato grado di taglio, rendendole ideali per disperdere particelle solide e frantumare agglomerati. I modelli di flusso radiale creati dagli agitatori a pale contribuiscono anche a un efficiente trasferimento di calore e di massa, poiché il fluido circola continuamente all'interno del recipiente di miscelazione. Le giranti a pale funzionano generalmente a velocità inferiori rispetto ad altri tipi di giranti, con conseguente minore consumo energetico e riduzione del taglio del fluido.
Giranti dell'agitatore di ancoraggio
Le giranti dell'agitatore ad ancora sono un tipo di agitatore progettato per la miscelazione di fluidi e materiali viscosi in recipienti di miscelazione cilindrici. Queste giranti sono caratterizzate dal loro design unico, che presenta pale curve per seguire i contorni della parete del serbatoio, fornendo una soluzione di miscelazione efficace per applicazioni ad alta viscosità. Le giranti ad ancoraggio generano schemi di flusso tangenziali, ideali per favorire il trasferimento di calore e prevenire l'accumulo di materiale viscoso sulla parete del serbatoio.
Il design degli agitatori ad ancora include tipicamente due o più pale angolate fissate all'albero centrale dell'agitatore. L'angolazione delle pale varia a seconda delle specifiche esigenze di processo, con un angolo standard che varia da 45° a 90°. Questa configurazione delle pale consente la massima dissipazione di energia e una miscelazione efficiente, anche in fluidi impegnativi ad alta viscosità.
Giranti per agitatori a nastro elicoidale
Le giranti degli agitatori a nastro elicoidali sono un tipo di agitatore progettate per miscelare fluidi e materiali viscosi. Queste giranti sono dotate di pale angolate che creano una combinazione di modelli di flusso radiale e assiale, rendendole adatte a un'ampia gamma di applicazioni, tra cui reazioni chimiche, trasferimento di calore e dispersione di gas.
Le pale di una girante a nastro elicoidale sono tipicamente disposte in una configurazione a spirale o elicoidale attorno all'albero dell'agitatore. L'angolo delle pale varia a seconda dell'applicazione specifica e delle caratteristiche di miscelazione desiderate. Questo design esclusivo favorisce un modello di flusso tangenziale, particolarmente efficace per la miscelazione vicino alla parete del vaso e per prevenire zone morte.
Le pale angolate degli agitatori elicoidali creano una combinazione di flussi radiali e assiali, che migliora l'efficienza della miscelazione e favorisce la distribuzione uniforme degli ingredienti. Ciò li rende adatti a processi che richiedono un'agitazione delicata, come la miscelazione di prodotti sensibili al taglio o la sospensione di particelle solide in liquidi viscosi.