Agitator impellers are essential components in various industrial processes, including mixing, chemical reactions, and heat transfer applications. They come in different types, each designed to suit specific needs based on factors such as viscosity, fluid flow patterns, and the desired mixing efficiency. This article will discuss the five main types of agitator impellers: propeller, turbine, paddle, anchor, and helical ribbon agitators.
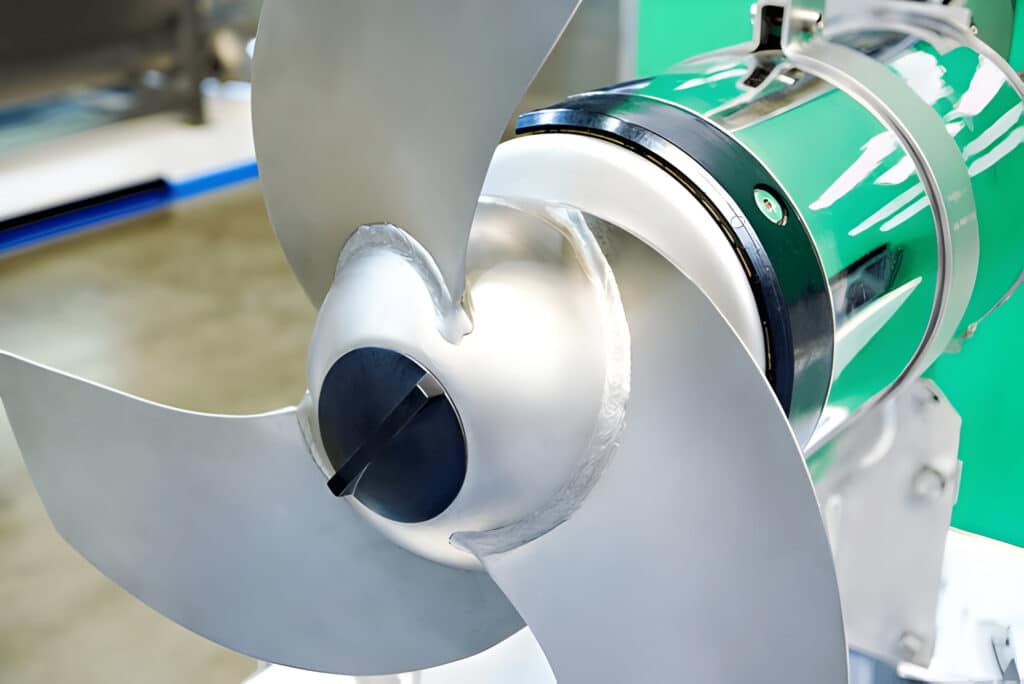
Propeller Agitator Impellers
Propeller agitator impellers, also known as marine propellers or axial flow impellers, are a versatile type of impeller used in various industrial processes. These impellers generate an axial flow pattern, which is ideal for mixing low to medium viscosity fluids.
Propeller agitators are characterized by their high flow and low shear characteristics, making them suitable for applications requiring gentle mixing or solid suspension.
The design of propeller agitators typically consists of a central hub with three or more blades attached at a specific pitch angle. The pitch angle of the blades can vary depending on the application, with a standard angle of 45° being common. The diameter of the impeller is usually selected based on the tank diameter, with a ratio of 1:3 to 1:2 being typical.
Turbine Agitator Impellers
Turbine agitator impellers offer a range of flow patterns and mixing capabilities. These impellers are designed to handle fluids with low to medium viscosity and can be used for liquid blending, solid suspension, gas dispersion, and heat transfer applications.
There are two main types of turbine impellers: radial flow and axial flow.
Radial flow impellers: such as the Rushton turbine, generate flow perpendicular to the agitator shaft, creating a radial flow pattern that is ideal for gas-liquid mixing and solid suspension.
Axial flow impellers: like pitched blade turbines or hydrofoil impellers, produce flow parallel to the agitator shaft, resulting in an axial flow pattern that is suitable for blending and solid suspension in low to medium viscosity fluids.
Paddle Agitator Impellers
Paddle agitator impellers consist of flat blades mounted on a central agitator shaft, creating a radial flow pattern that promotes effective mixing. Paddle agitators are well-suited for a wide range of industrial processes, including blending, solids suspension, and heat transfer applications.
The flat blade design of paddle impellers generates a high degree of shear, making them ideal for dispersing solid particles and breaking up agglomerates. The radial flow patterns created by paddle agitators also contribute to efficient heat transfer and mass transfer, as the fluid is continuously circulated throughout the mixing vessel. Paddle impellers typically operate at lower speeds compared to other impeller types, resulting in lower power consumption and reduced shear on the fluid.
Anchor Agitator Impellers
Anchor agitator impellers are a type of agitator designed for mixing viscous fluids and materials in cylindrical mixing vessels. These impellers are characterized by their unique design, which features blades that are curved to follow the contours of the vessel wall, providing a effective mixing solution for high-viscosity applications. Anchor impellers generate tangential flow patterns, which are ideal for promoting heat transfer and preventing the build-up of viscous material on the tank wall.
The design of anchor agitators typically includes two or more angled blades attached to a central agitator shaft. The angle of the blades varies depending on the specific process requirements, with a standard angle ranging from 45° to 90°. This blade configuration allows for maximum energy dissipation and efficient mixing, even in challenging high-viscosity fluids.
Helical Ribbon Agitator Impellers
Helical ribbon agitator impellers are a type of agitator designed for mixing viscous fluids and materials. These impellers feature angled blades that create a combination of radial and axial flow patterns, making them suitable for a wide range of applications, including chemical reactions, heat transfer, and gas dispersion.
The blades of a helical ribbon impeller are typically arranged in a spiral or helical configuration around the agitator shaft. The angle of the blades varies depending on the specific application and desired mixing characteristics. This unique design promotes a tangential flow pattern, which is particularly effective for mixing near the vessel wall and preventing dead zones.
The angled blades of helical agitators create a combination of radial and axial flow patterns, which enhances mixing efficiency and promotes uniform distribution of ingredients. This makes them suitable for processes requiring gentle agitation, such as blending shear-sensitive products or suspending solid particles in viscous liquids.