Mechanical seals rely on dedicated fluids (often oils or oil-based fluids) to lubricate and cool the seal faces, which prevents excessive friction and wear. These fluids serve different roles in seal support systems, from barrier and buffer fluids used in dual-seal arrangements to general lubricating/circulating oils in various flush or support plans.
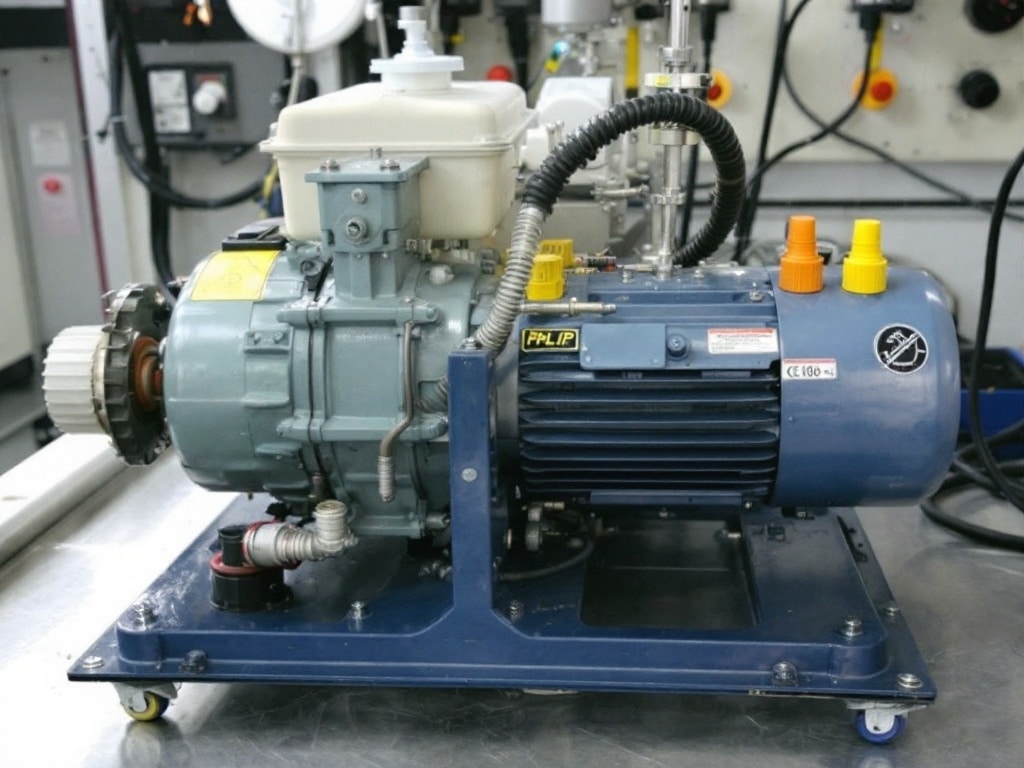
Types of Mechanical Seal Fluids
Mechanical seal support fluids can be categorized by their function in the seal system:
Barrier Fluids (Seal Oils)
In a pressurized dual-seal arrangement (often called a double seal), an external fluid is kept at higher pressure than the process fluid. This barrier fluid completely isolates the pumped process liquid from the environment. It lubricates the inner and outer seal faces and carries away heat. Barrier fluids are used in API Plan 53/54 systems (e.g., Plan 53A with a pressurized reservoir, Plan 54 with an external circulation system).
A barrier fluid is typically a clean, stable oil (or oil-based mixture) selected to withstand operating conditions. It must be compatible with the process and seal materials, provide good lubrication and cooling, and pose no safety or environmental hazards. Because it is pressurized above process pressure, no process fluid leaks past the inboard seal; any leakage tends to be outward of the outboard seal.
Buffer Fluids
In an unpressurized dual-seal (tandem) arrangement, the external fluid is maintained at or below process pressure. This buffer fluid provides lubrication and cooling between the two seals but is not intended to fully contain the process fluid. Buffer fluid systems (e.g., API Plan 52 with an unpressurized reservoir) allow a small amount of process leakage into the buffer fluid or vice versa. Thus, the buffer fluid must be compatible with the process liquid because some mixing will occur.
Like barrier fluids, buffer fluids should be safe, stable, and a good lubricant/heat-transfer medium. However, because buffer fluid pressure is lower, they do not isolate the process; they primarily serve to reduce leakage to atmosphere and to lubricate the seal faces. Buffer fluids often require more frequent maintenance since they can become contaminated by the process.
Lubrication Oils
Not all mechanical seals use a dedicated external reservoir; many single seals are lubricated by the process fluid or by a flush. In cases where the process fluid is a poor lubricant or contains abrasives, an external lubricating oil or flush fluid may be introduced (e.g., API Plan 32 injects a clean fluid, which could be an oil, into the seal chamber).
These lubricating oils serve to flush and lubricate the seal faces of single seals or quench the atmospheric side of a seal (Plan 62), improving reliability. They are generally supplied from a separate system and may or may not be recirculated.
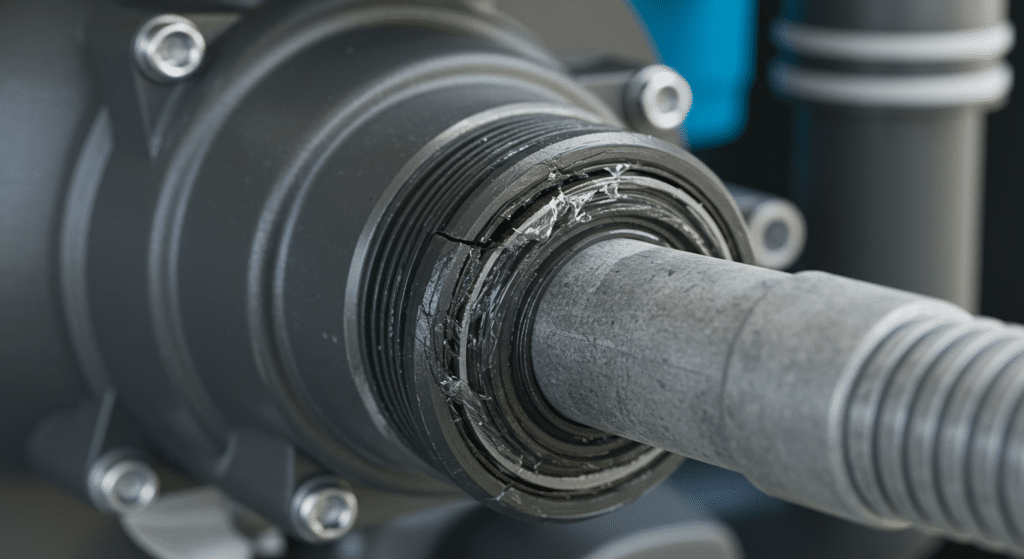
Types of Oils Used in Mechanical Seals
There is a wide range of oil types used in seal systems, from traditional mineral oils to advanced synthetics. Each type offers different performance characteristics:
Mineral Oils
These are petroleum-derived oils that have been traditionally used in many seal systems. Mineral oils are readily available and cost-effective, providing decent lubrication in moderate conditions. However, they have limited temperature resilience – at high temperatures they oxidize and break down, potentially leaving deposits and losing lubricity.
Their viscosity index is moderate (meaning viscosity changes significantly with temperature). Mineral oils can be suitable for general-purpose seal lubrication when operating temperatures are not extreme and maintenance intervals are relatively short.
Synthetic Oils
A broad category encompassing oils engineered from chemical base stocks rather than directly refined from crude. Synthetics are formulated to offer superior properties such as wider temperature range, higher oxidative stability, and improved lubricity compared to mineral oils. Several subtypes relevant to mechanical seals include:
- PAO (Polyalphaolefin) Oils: PAOs are synthetic hydrocarbons that mimic the structure of highly refined mineral oil but with uniform molecules and no unwanted compounds. They have excellent thermal stability, low volatility, high viscosity index, and good material compatibility.
- PAG (Polyalkylene Glycol) Oils: PAGs are polymers of ethylene or propylene oxide (or both). They have very high viscosity indices, meaning they maintain viscosity with temperature changes exceptionally well, and can be formulated to be water-soluble or insoluble.
- Silicone Oils: Silicone-based fluids (typically polydimethylsiloxane or similar) are highly inert and stable across very wide temperature ranges. They remain liquid at extremely low temperatures and can tolerate high temperatures (some up to ~250–300 °C) without oxidizing in the same way hydrocarbons do.
- Ester-Based Synthetics: This category includes diesters and polyol esters, which are synthetic oils formed by reacting alcohols with carboxylic acids. Ester oils have been used for decades in high-temperature lubrication (e.g., jet engine oils, compressor oils) due to their excellent lubricating film strength and thermal stability. They also biodegrade more readily than PAOs, making them attractive for environmentally sensitive uses.
- Fluorinated Oils (PFPE): For the most demanding chemical and temperature extremes, perfluoropolyether (PFPE) oils or similar fluorinated fluids are used. These oils are fully fluorinated, making them chemically inert to virtually all chemicals and oxidizing environments.
- Other Niche Fluids: In some cases, light hydrocarbons like kerosene or diesel have been used as seal oils. These fluids have low viscosity (~2 cSt) and good lubricity, which can work well for seal faces. However, they are obviously flammable and have relatively low flash points, so their use is limited to systems where these fluids are already handled and safety measures are in place.
Oil / Fluid Type | Composition/Base | Key Characteristics | Typical Uses / Notes |
---|---|---|---|
Mineral Oil | Petroleum-derived (highly refined) | Good lubricity; moderate viscosity index; economical. Limited high-temp stability (oxidizes, forms varnish); may contain additives (avoid EP additives). | General-purpose seal oil in moderate conditions. Used when temperatures are not extreme and a cost-effective lubricant is acceptable. Tends to require more frequent changes at high temperatures. |
PAO Synthetic | Polyalphaolefin (synthetic hydrocarbon) | Excellent thermal stability and oxidation resistance; high viscosity index (flat viscosity vs. T); very low pour point. No polar constituents – needs no additives (often used neat); compatible with common seal materials. | Widely used barrier/buffer fluid in modern systems. Available in light grades (ISO VG 5–20) ideal for seals. Also formulated in food-grade*versions (NSF H1). Suitable for Oil & Gas, chemical, general industry – the go-to choice for reliability and extended service life. |
PAG Synthetic | Polyalkylene glycol (ether polymer) | Very high viscosity index (superb for wide temp range); excellent lubricity (low friction); can be formulated water-soluble or insoluble. Hygroscopic (absorbs water) in many cases; not compatible with mineral oil; can soften certain paints or polymers. | Used in specialized applications requiring extreme temp range or very high film strength. Some food-grade and fire-resistant fluids are PAG-based. Less common as seal pot fluids due to mixing issues, but can outperform others in high-temp or low-temp extremes if chosen carefully. |
Silicone Oil | Polydimethylsiloxane or similar | Ultra-wide temperature capability (stable from deep cold to ~250 °C); chemically inert to most materials; high flash point; low volatility. Lower boundary lubricity under load; can form hard silica particles that abrade seals; high gas solubility. | Rarely used for seal lubrication due to the risk of fouling and abrasion. May be employed in some high-temp heat transfer roles or where chemical inertness is critical (e.g., oxygen service), but generally avoided as a direct seal oil unless no alternative. |
Ester-Based Synthetic | Diesters or polyol esters (organic) | Strong lubricating film; high thermal stability (resists coking); biodegradability higher than PAO; good solvency for additives if needed. Can hydrolyze with water (forming acids); may cause swelling of certain elastomers if not compatible; moderately high pour points for some. | Used in some high-temperature or high-speed machinery where mineral/PAO oils fail (e.g., some compressor or vacuum pump seal systems). Sometimes blended with PAOs in commercial fluids to improve overall properties. Also considered in eco-sensitive areas if formulated to be biodegradable. |
Fluorinated Oil (PFPE) | Perfluoropolyether (fully fluorinated) | Chemically inert to virtually all substances; non-flammable; extremely wide operating temperature (–40 °C to 250 °C or more); no oxidation or gum formation. Very high density (~1.8 g/mL); expensive; lower lubricity than hydrocarbon oils (but sufficient for most seals); not mixable with other oils. | The choice for aggressive chemicals and oxygen-rich environments. Used in chemical processing, pharmaceutical, or aerospace seals where any organic oil would react or pose fire risk. E.g. Halocarbon’s MSHV fluids for reactive chemical pumps. Due to cost, used only when absolutely needed. |
Water/Glycol (50/50) | Water + Ethylene or Propylene Glycol | Not an oil, but common seal fluid: Excellent cooling capacity (water’s high specific heat); low viscosity for easy circulation; glycol prevents freezing and corrosion (with inhibitors). Non-toxic (especially propylene glycol mixes); not flammable. Boiling/evaporation can be an issue at high temperatures; poor lubricity compared to oils (but sufficient for many dual seals). | Common in dual seals (Plans 52, 53) for moderate temperature pumps. Chosen in food/pharma when oil contamination is a concern (use propylene glycol grade). Avoid automotive antifreeze (silicate inhibitors cause seal wear). Ensure use of industrial uninhibited or properly inhibited glycol to protect seal metals. Not used above ~80 °C process temperature due to risk of vaporization. |
Kerosene/Diesel | Light petroleum fractions | Very low viscosity (~1–3 cSt) – flows and cools easily; good natural lubricity on carbon faces; readily available. Flammable (low flash point); moderate toxicity; will evaporate or fume at higher temperatures (creating hazard). | Historically used as an easy barrier fluid in refinery or remote settings (if those fuels were on hand). Lubricates seal faces effectively, but due to fire risk it is generally not preferred if other safer fluids are available. |
Vegetable Oils | Natural oils (e.g., canola, soy) | Biodegradable, renewable; decent lubricity (especially some modified triglycerides); mild EP properties. Oxidation-prone at high temps (polymerize into gum); limited temperature range (can cloud or solidify when cold unless winterized); can support microbial growth in presence of water. | Occasionally used in environmentally sensitive applications (e.g., near waterways) where any leakage must be non-polluting. Typically only suitable for low-to-medium temperature seals. Performance is inferior to synthetic oils; thus, bio-derived synthetic esters are often favored over raw vegetable oils for seal service. |