Proper lubrication is essential for the longevity and performance of bearings. Both overgreasing and undergreasing can lead to premature bearing failure, increased downtime, and costly repairs. This article explores the consequences of improper lubrication and provides guidance on establishing a precision lubrication program.
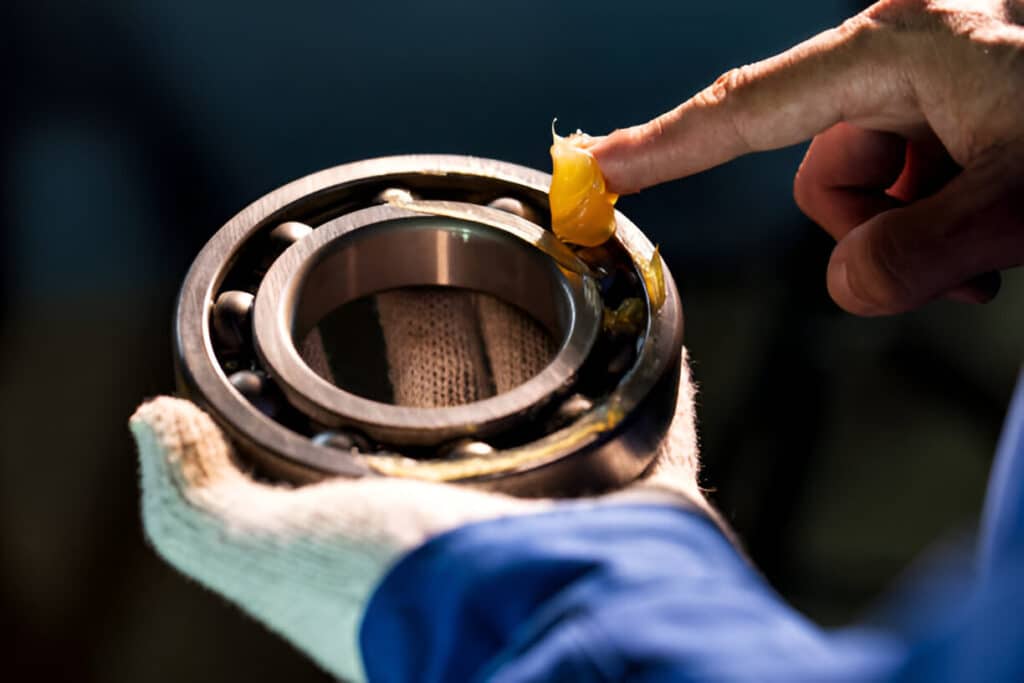
Consequences of Overgreasing
Overgreasing is a common problem that can cause significant issues for bearings, including:
Grease Churning and Overheating
- Excess grease causes rolling elements to churn and slide, leading to energy loss and increased operating temperatures
- Fluid friction from churning grease accelerates grease oxidation and oil bleed, degrading lubricant properties
- Excessive heat generation can cause premature bearing failure and damage to surrounding components
Seal Damage and Contamination
- High pressure from grease guns can rupture seals, allowing contamination ingress and grease leakage
- Damaged seals lead to housekeeping issues and further contamination of the bearing cavity
- Contamination from moisture and solid particles accelerates wear and reduces bearing life
Degraded Lubrication
- Overgreasing can cause the grease thickener to harden into a crusty build-up, blocking grease flow to bearing surfaces
- Starvation of critical bearing areas occurs when excess grease prevents fresh lubricant from reaching the contact zones
- Hardened grease can cause increased friction, wear, and eventual bearing failure
Increased Downtime
- Overgreased bearings require more frequent maintenance and replacement, leading to increased downtime and lost production
- Cleaning and replacing damaged seals and housings adds to maintenance costs and downtime
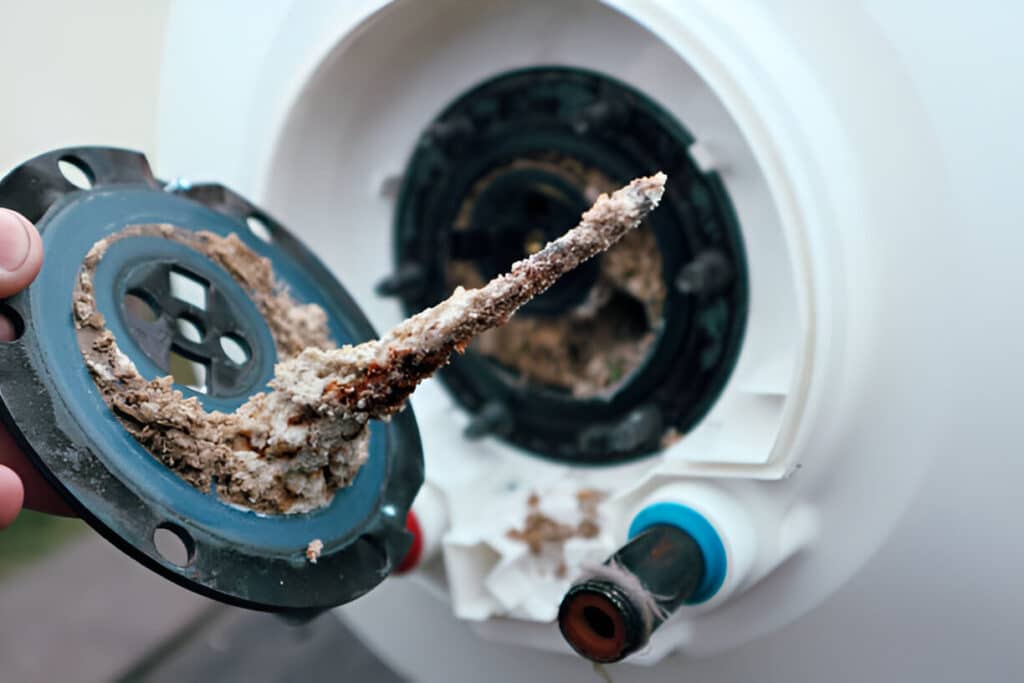
Problems Caused by Undergreasing
Undergreasing, or insufficient lubrication, can be just as detrimental to bearing performance as overgreasing.
Inadequate Lubricant Film
- Lack of grease leads to metal-to-metal contact of bearing surfaces, causing accelerated wear and friction
- Inadequate lubrication can result in bearing seizure, particularly in high-load or high-speed applications
- Increased wear reduces bearing life and leads to premature failure
Overheating
- Insufficient lubrication causes excess heat generation from friction, leading to accelerated grease breakdown
- High operating temperatures can cause the remaining grease to oxidize and lose its lubricating properties
- Excessive heat can damage bearing components and surrounding structures
Contamination
- Undergreased bearings are more susceptible to moisture and dirt ingress due to insufficient grease barrier
- Solid contaminants cause abrasive wear on bearing surfaces, reducing bearing life and performance
- Contamination can lead to corrosion and further degradation of the bearing and lubricant
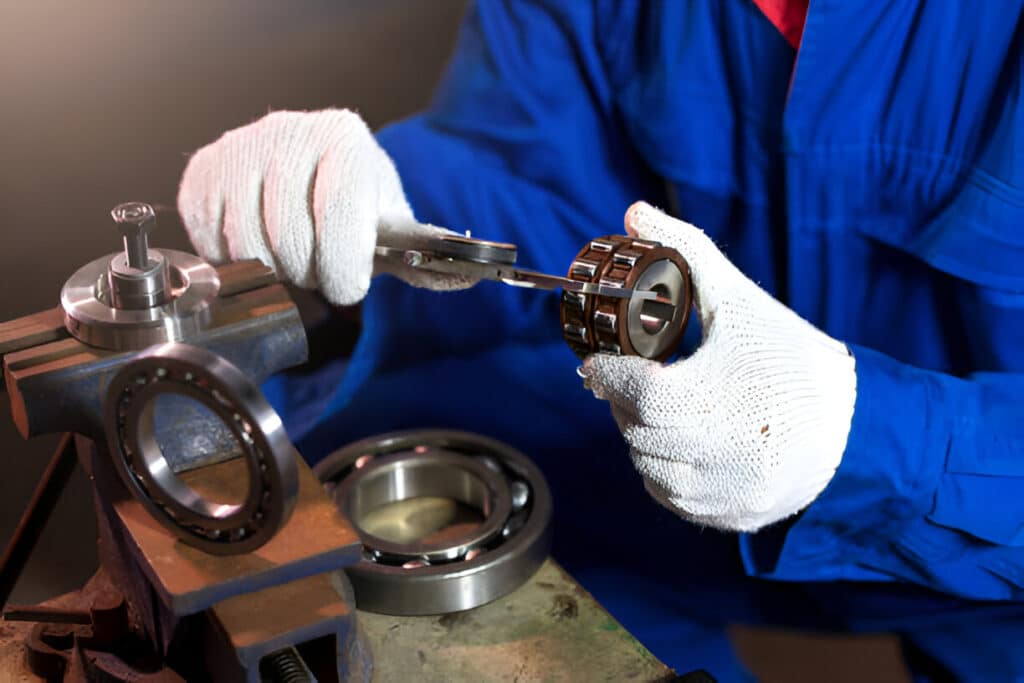
Calculating Optimal Grease Quantity
To avoid the problems associated with over and under greasing, it is essential to calculate the correct volume of grease for each bearing. The following formula can be used as a starting point:
G = 0.005 x D x B
Where:
G = Grease quantity in ounces
D = Bearing outer diameter in inches
B = Bearing width in inches
This formula provides a general guideline, but factors such as bearing type, speed, load, and operating conditions must also be considered when determining the optimal grease quantity.
Establishing a Precision Lubrication Program
A comprehensive precision lubrication program is crucial for maintaining bearing health and preventing failures caused by improper lubrication.
Grease Selection
- Choose a grease with the appropriate base oil viscosity, thickener type, and additive package for the application
- Ensure compatibility when switching greases to avoid adverse reactions and degraded performance
Relubrication Intervals and Quantities
- Set relubrication intervals based on operating conditions, bearing type, and grease life
- Calculate grease replenishment quantities to maintain optimal fill levels without overgreasing
Lubrication Procedures
- Train technicians on proper lubrication techniques, including the use of calibrated grease guns for precise dispensing
- Clean grease fittings and purge old grease before applying fresh lubricant
- Allow the bearing to run during and after relubrication to distribute the grease evenly
Condition Monitoring
- Regularly track bearing operating temperatures and vibration levels to detect early signs of lubrication issues
- Analyze used grease samples for contamination, oxidation, and consistency changes
- Adjust lubrication practices based on condition monitoring feedback to optimize bearing performance
Conclusion
Over and under greasing are common causes of premature bearing failure, increased maintenance costs, and lost productivity. By understanding the consequences of improper lubrication and implementing a precision lubrication program, organizations can extend bearing life, reduce downtime, and improve overall equipment reliability.