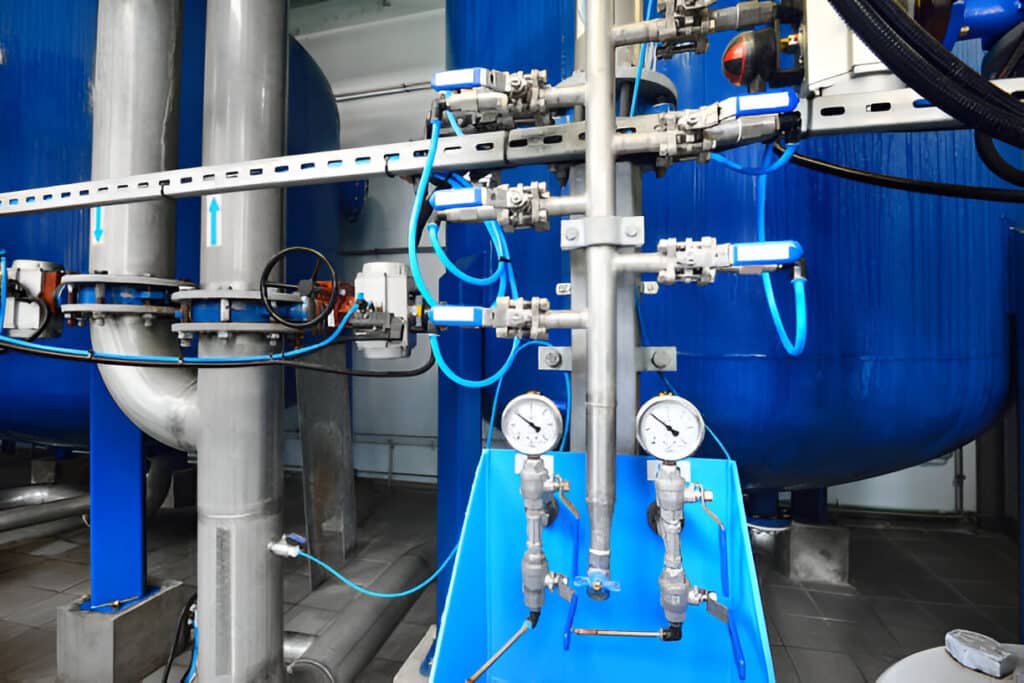
What Is Static Leak Testing
Static leak testing, also known as hydrostatic testing, is a method used to detect leaks in closed systems, such as pipelines, pressure vessels, and tanks. This type of leak detection involves filling the system with a liquid, usually water, and pressurizing it to a predetermined level. The pressure is then monitored over a period of time to identify any pressure drops, which would indicate the presence of a leak. Static leak detection systems are commonly used in industries such as oil and gas, chemical processing, and water distribution networks.
Advantages of Static Leak Testing
- High sensitivity: Static leak testing can detect very small leaks, making it suitable for systems requiring a high degree of leak tightness.
- Simplicity: The test setup is relatively simple, requiring only a pressure source and a means of monitoring pressure.
- Cost-effective: Static leak testing is generally less expensive than other leak detection methods, as it does not require sophisticated equipment or specialized personnel.
- Comprehensive coverage: Static leak testing can detect leaks throughout the entire system, including those in hard-to-reach areas.
Disadvantages of Static Leak Testing
- Time-consuming: Static leak testing requires the system to be pressurized and monitored for an extended period, which can be time-consuming and may result in extended downtime.
- Limited to closed systems: Static leak testing is only applicable to closed systems and cannot be used for open systems or those with continuous flow.
- Potential for false positives: Temperature changes and trapped air can cause pressure fluctuations, leading to false alarms or inaccurate results.
- Inability to locate leaks: While static leak testing can detect the presence of a leak, it does not provide information on the exact location of the leak within the system.
What Is Dynamic Leak Testing
Dynamic leak testing, also referred to as pressure decay testing, is a method used to detect leaks in systems with continuous flow or those that cannot be isolated for static testing. This type of leak detection involves pressurizing the system with a gas, typically air or nitrogen, and monitoring the pressure decay over time. A rapid pressure drop indicates the presence of a leak. Dynamic leak detection systems are widely used in industries such as automotive, aerospace, and medical device manufacturing.
Advantages of Dynamic Leak Testing
- Fast testing: Dynamic leak testing can detect leaks quickly, making it suitable for high-volume production environments.
- Applicability to open systems: Dynamic leak testing can be used for systems with continuous flow or those that cannot be isolated for static testing.
- Precise leak location: Advanced dynamic leak detection methods, such as those using acoustic technologies or multiple-sensor approaches, can pinpoint the exact location of leaks within a system.
- Automation potential: Dynamic leak testing can be easily automated, reducing the risk of human error and increasing efficiency.
Disadvantages of Dynamic Leak Testing
- Higher cost: Dynamic leak testing often requires specialized equipment and trained personnel, making it more expensive than static testing.
- Sensitivity limitations: Dynamic leak testing may not be as sensitive as static testing, especially for very small leaks.
- Complexity: Setting up and interpreting results from dynamic leak tests can be more complex than static tests, requiring a higher level of expertise.
- Potential for false positives: Dynamic leak testing can be affected by factors such as temperature changes and vibrations, leading to false alarms or inaccurate results.
The Difference between Static and Dynamic Leak Testing
Test Conditions
- Static leak testing is performed on closed systems filled with a liquid and pressurized to a predetermined level.
- Dynamic leak testing is performed on systems with continuous flow or those pressurized with a gas.
Leak Detection Method
- Static leak testing detects leaks by monitoring pressure drops over an extended period.
- Dynamic leak testing detects leaks by monitoring pressure decay over a short period.
Sensitivity
- Static leak testing is generally more sensitive and can detect smaller leaks.
- Dynamic leak testing may have limitations in detecting very small leaks.
Applicability
- Static leak testing is limited to closed systems that can be isolated and filled with a liquid.
- Dynamic leak testing can be used for open systems or those with continuous flow.
Test Duration
- Static leak testing requires an extended monitoring period, which can be time-consuming.
- Dynamic leak testing can detect leaks quickly, often within seconds or minutes.