Tungsten and tungsten carbide are often mistaken as one and the same, but beneath their similar names lie distinct properties that set them apart. While both derive from the rare metal element tungsten, the addition of carbon atoms in tungsten carbide results in a unique compound with its own set of characteristics.
In this blog post, we’ll delve into the key distinctions between tungsten and tungsten carbide, exploring factors such as hardness, brittleness, density, corrosion resistance, and cost.
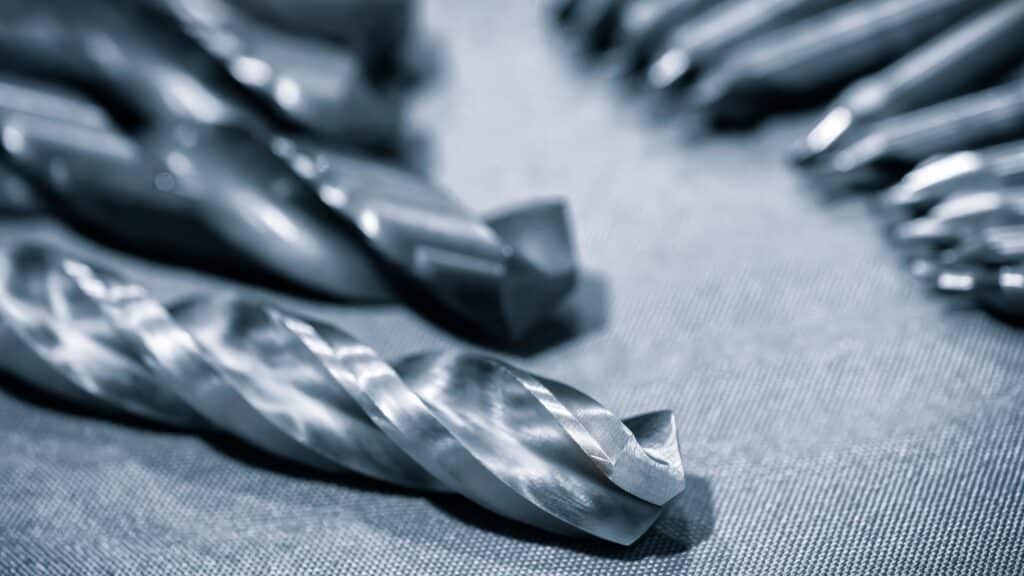
What is Tungsten
Tungsten, also known by the chemical symbol W, is a naturally occurring metallic element. It is considered a rare metal, comprising only about 1.5 ppm of the Earth’s crust. Tungsten has the atomic number 74 and is located in period 6, group 6 of the periodic table, placing it among the transition metals.
In its pure elemental form, tungsten is a steel-gray to tin-white metal. It possesses several notable properties, including the highest melting point (3422°C, 6192°F) and highest tensile strength of all metals. Tungsten also has the second highest atomic weight (183.84 u) of all naturally occurring elements, behind only uranium. Its density of 19.3 g/cm³ is comparable to gold (19.32 g/cm³) and is much higher than that of lead (11.34 g/cm³).
What is Tungsten Carbide
Tungsten carbide (WC) is an inorganic chemical compound containing equal parts of tungsten and carbon atoms. Also known as tungsten monocarbide, it is the most important and widely used carbide of tungsten.
The tungsten and carbon atoms in WC are bonded together in a hexagonal crystal structure, resulting in ceramic-like material properties. With a Mohs hardness rating between 9 and 9.5, tungsten carbide approaches the hardness of diamond (10). It has a high melting point of 2,870°C (5,200°F), although this is lower than pure tungsten due to the presence of carbon.
Types of Binders for Tungsten Carbide
While pure tungsten carbide has excellent hardness, it is brittle and prone to shattering, especially under impact. To improve its toughness and durability, tungsten carbide powders are mixed with metallic binders before being sintered into solid parts.
Cobalt (Co)
Cobalt is the most widely used binder for tungsten carbide. Cobalt-bonded tungsten carbide, often referred to simply as carbide, is the industry standard for cutting tools and wear parts. The cobalt content typically ranges from 3% to 30% by weight, with higher cobalt proportions providing increased toughness at the expense of some hardness and wear resistance. Cobalt has excellent wetting and adhesion properties with tungsten carbide, allowing for the production of highly dense, void-free sintered parts.
Nickel (Ni)
Nickel can serve as an alternative binder to cobalt in tungsten carbide composites. Compared to cobalt, nickel binders result in better corrosion resistance and improved chemical stability, particularly against acidic environments. However, nickel-bonded carbides have lower hardness and wear resistance ratings. Nickel is sometimes used in conjunction with cobalt to fine-tune the properties of the tungsten carbide composite.
Other Binders
Other metals, such as chromium and iron, are less commonly used as sole binders but can be combined with cobalt or nickel to impart specific properties:
- Chromium enhances the corrosion and oxidation resistance of the tungsten carbide composite. It is often used in combination with nickel binders.
- Iron can serve as an economical alternative or addition to cobalt binders. Ferro-tungsten carbide has lower hardness but higher toughness compared to cobalt-bonded grades.
The Difference Between Tungsten vs. Tungsten Carbide
Hardness and Durability
Tungsten carbide is significantly harder than pure tungsten metal. On the Mohs hardness scale, tungsten carbide rates at about 9-9.5, nearly as hard as diamond (10). In contrast, tungsten has a hardness of approximately 7.5, similar to other hard metals like hardened steel.
The extreme hardness of tungsten carbide translates to exceptional wear resistance and durability. Tungsten carbide tools and components maintain a sharp edge and resist abrasion better than tungsten under demanding conditions. However, the hardness of tungsten carbide also makes it more brittle.
Brittleness and Impact Resistance
The trade-off for tungsten carbide’s superior hardness is increased brittleness compared to pure tungsten. Tungsten metal is relatively ductile and has better impact resistance. It can withstand heavier blows without chipping or fracturing.
In applications with high impacts or vibration, tungsten is often the better choice. Tungsten carbide is more suitable where extreme wear resistance is required but impact forces are lower, such as in cutting tools, dies, and abrasives.
Density and Weight
Tungsten is one of the densest metals, with a density of 19.3 g/cm³, about 1.7 times that of lead.
Tungsten carbide is slightly less dense at around 15.6 g/cm³, but still much heavier than steel (7.8 g/cm³).
Corrosion Resistance
Both tungsten and tungsten carbide have good corrosion resistance thanks to the formation of a thin oxide layer on their surface. However, tungsten carbide typically has cobalt or nickel binders that can be more susceptible to corrosion in certain environments, especially acidic conditions.
Pure tungsten generally offers better corrosion resistance across a broader range of environments. For the most demanding applications, pure tungsten or tungsten alloys are usually preferred over carbide.
Heat Resistance
Tungsten has the highest melting point of all metals at 3422°C (6192°F). This makes it ideal for extremely high-temperature applications such as lighting filaments, rocket engine nozzles, and welding electrodes.
Tungsten carbide has a lower melting point around 2870°C (5198°F), but this is still exceptionally high compared to most other materials. Tungsten carbide maintains most of its hardness and strength at elevated temperatures.
Electrical Conductivity
Pure tungsten is a good conductor of electricity and is often used for electrical contacts and electrodes. It has a resistivity of 5.6 μΩ·cm, lower than nickel and carbon steel.
In contrast, tungsten carbide is more of an electrical insulator, with much higher resistivity around 20 μΩ·cm or more depending on the binder material. The cobalt binder in cemented carbide gives it some conductivity, but far less than pure tungsten.
Appearance
Pure tungsten has a grayish-white metallic luster similar to other metals.
Tungsten carbide is usually a matte gray, charcoal color due to its carbon content and binder materials. The exact shade can vary depending on the ratio of tungsten to carbide and the specific binder composition.
Cost
Tungsten carbide powder is cheaper than pure tungsten because it uses less tungsten per unit volume.
However, the processing and sintering of tungsten carbide components tends to be more expensive and energy intensive. The brittle nature of carbide also leads to more waste in machining operations. So in general, finished tungsten carbide parts are more costly than pure tungsten.