Agitators play a crucial role in various industrial processes, including chemical reactions, heat transfer, and mixing of liquids and solids. There is a wide range of agitator types available, each designed to cater to specific process requirements. This article will discuss the most common types of agitators and their applications.
Types of Agitators
Paddle Agitators
Paddle agitators consist of a central shaft with flat blades or paddles attached to it, which rotate to create a radial flow pattern in the mixing tank. The paddles are typically mounted at a 90-degree angle to the agitator shaft and can be either straight or curved.
Paddle agitators are well-suited for mixing medium to high viscosity fluids and are effective in promoting heat transfer and gas dispersion. They operate at relatively low speeds, ranging from 20 to 150 rpm, and are capable of handling liquids with viscosities up to 50,000 cP. The power requirement for paddle agitators is generally lower compared to other types of agitators.
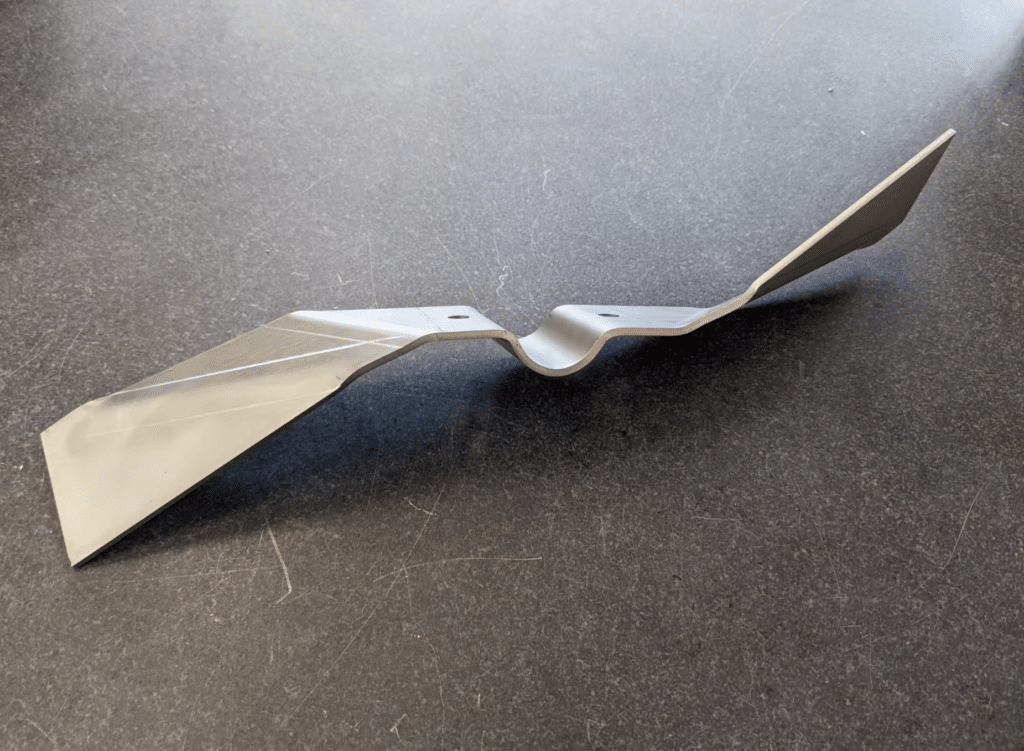
Anchor Agitators
Anchor agitators consist of a central shaft with two or more large, flat blades attached, resembling an anchor shape. The blades of anchor agitators sweep close to the vessel walls and bottom, ensuring efficient mixing and heat transfer, particularly in applications involving high-viscosity fluids or solid particles.
Anchor agitators operate at low speeds and generate a mainly tangential flow pattern, making them well-suited for laminar flow conditions. They are commonly used in the chemical, food, and pharmaceutical industries for processes such as blending, homogenization, and suspension of solids in liquids. The close proximity of the blades to the vessel walls helps prevent the formation of stagnant zones and promotes uniform mixing.
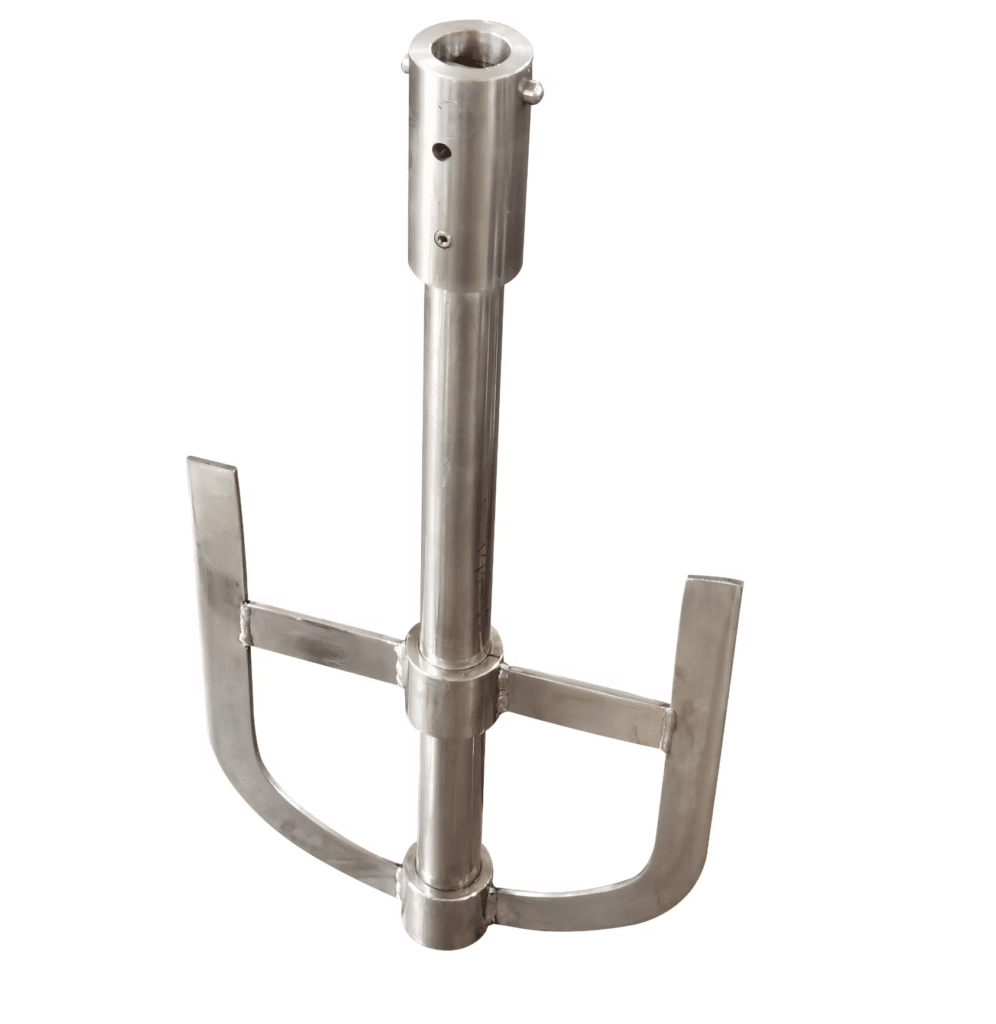
Helical Ribbon Agitators
Helical ribbon agitators are a type of agitator designed for mixing highly viscous liquids and pastes. These agitators feature a central shaft with one or more helical ribbons or spirals attached, which create a combination of radial and axial flow patterns as the agitator rotates. The unique design of helical ribbon agitators makes them ideal for applications involving high-viscosity materials, such as in the chemical, pharmaceutical, and food processing industries.
The primary advantage of helical ribbon agitators is their ability to generate a well-defined flow pattern that promotes efficient mixing and heat transfer. As the agitator rotates, the helical ribbons move the material both radially and axially, ensuring thorough mixing throughout the vessel. This motion also helps to prevent the formation of dead zones and minimize the accumulation of material on the vessel walls.
Helical ribbon agitators are particularly effective for laminar flow conditions, where the fluid viscosity is high and turbulent mixing is difficult to achieve. The close clearance between the ribbons and the vessel wall creates a shearing action that helps to break down the viscous material and promote mixing. Additionally, the increased surface area of the helical ribbons enhances heat transfer rates, making these agitators well-suited for applications involving heating or cooling of viscous materials.
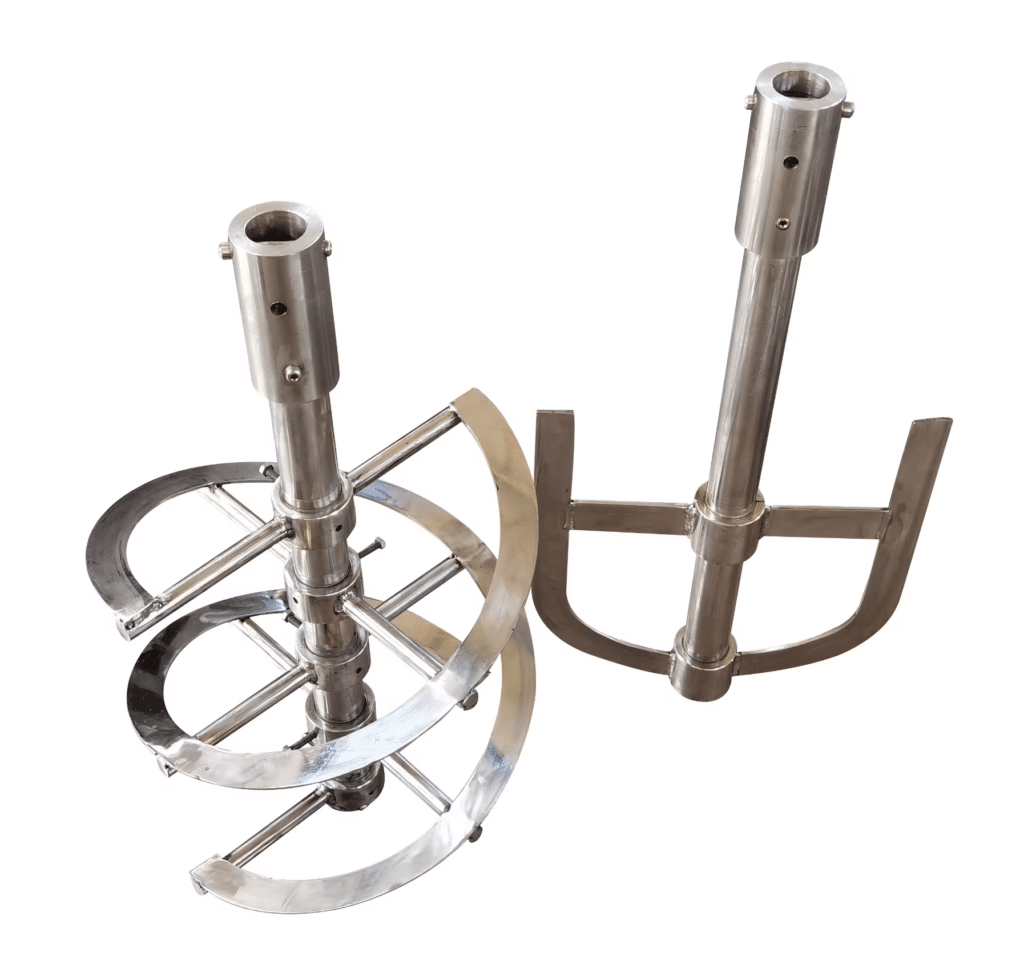
Double Helical Ribbon Agitators
Double helical ribbon agitators feature two helical ribbons wound around a central shaft, creating a unique flow pattern that ensures efficient mixing and heat transfer. The helical design of the ribbons promotes both radial and axial flow, allowing for thorough mixing of the entire contents of the tank.
Agitators with Screw Impellers
Agitators with screw impellers are a type of agitator designed for mixing viscous liquids and materials with high solids content. These agitators feature a helical screw-shaped impeller that creates an axial flow pattern, effectively moving the fluid in a vertical direction. The geometry of the screw impeller allows for efficient mixing and heat transfer, making them ideal for various industrial processes, including chemical reactions, dispersion operations, and the production of pharmaceuticals.
One of the primary advantages of screw impeller agitators is their ability to handle high-viscosity fluids and slurries. The screw design generates a powerful pumping action that can move thick, viscous materials with ease.
Propeller Agitators
Propeller agitators consist of a shaft with a propeller blade attached, which generates an axial flow pattern when rotated. The angle of the blade varies, typically ranging from 45° to 60°, and the pitch angle can be adjusted to optimize the flow characteristics for specific applications.
Propeller agitators are well-suited for mixing low to medium viscosity fluids and can effectively blend miscible liquids or disperse gases and solid particles in a liquid medium. They are commonly used in tanks with a diameter of up to 3 meters and can operate at speeds ranging from 400 to 1,750 rpm.
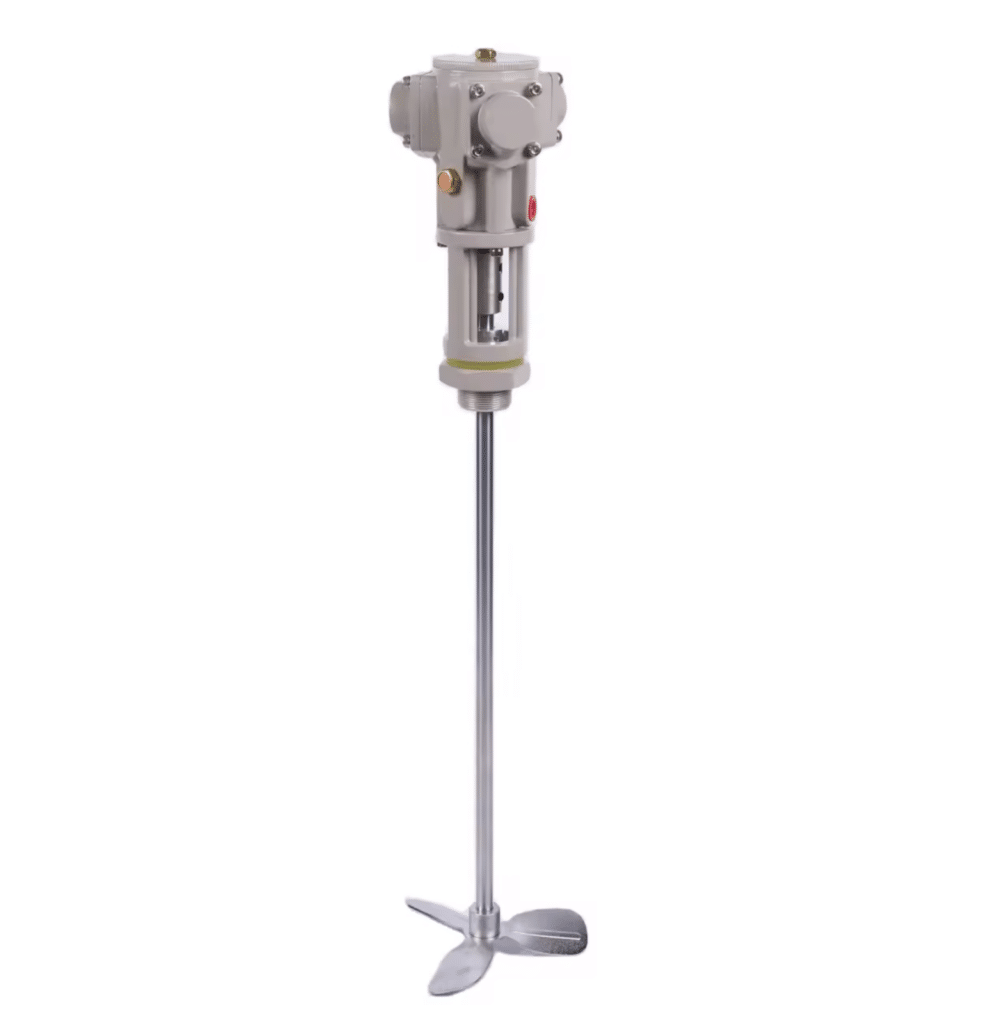
Radial Propeller Agitators
Radial propeller agitators generate a radial flow pattern, which is perpendicular to the agitator shaft, creating turbulent movement and promoting effective mixing.
The design of radial propeller agitators typically consists of flat blades mounted on a central hub, with the blade angle varying between 30° and 45°. The diameter of the agitator is usually 30-50% of the tank diameter, and the agitator speed ranges from 20 to 150 rpm.
Radial propeller agitators are suitable for low to medium viscosity fluids and can handle solid particles in suspension. They are efficient in gas-liquid dispersion operations and can improve heat transfer rates when used in combination with heat exchangers.
Turbine Agitators
Turbine agitators known for their ability to generate high shear rates and turbulent movement in the fluid, making them suitable for a wide range of viscosities.
Turbine agitators typically consist of a central shaft with multiple flat blades or impellers attached at right angles. The impellers can be either radial or axial, depending on the desired flow pattern.
Radial flow impellers, such as Rushton turbines, create a flow pattern perpendicular to the agitator shaft, promoting good mixing and gas dispersion.
Axial flow impellers, like pitched blade turbines, generate a flow parallel to the shaft, which is ideal for blending and solid suspension.
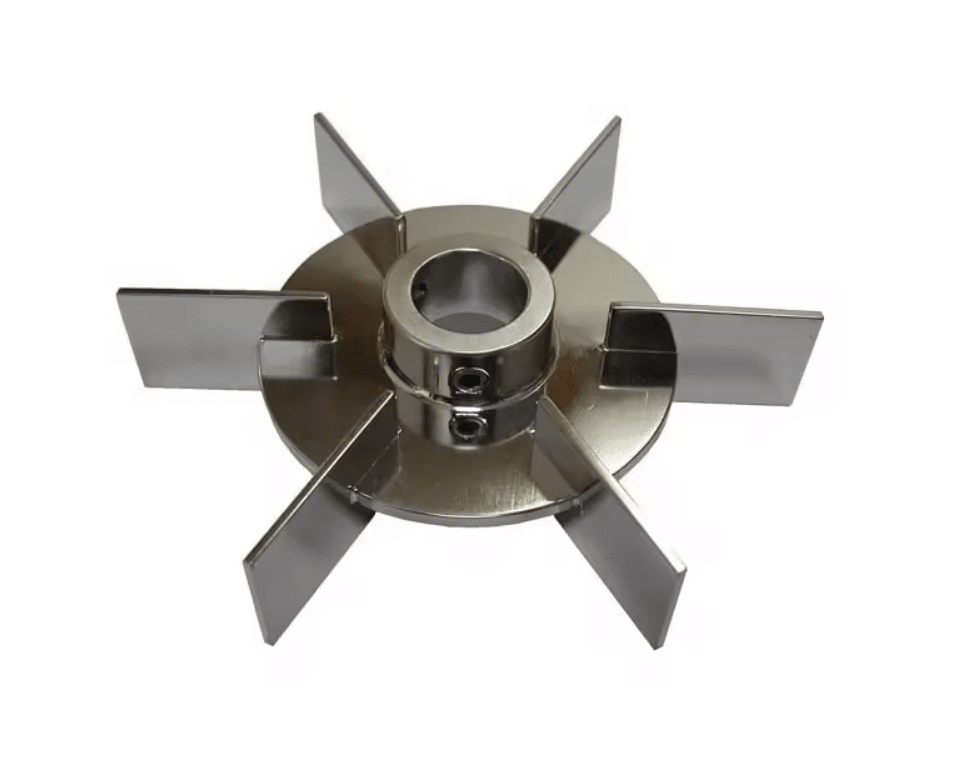
Straight Blade Turbine Impellers: Straight blade turbine impellers feature flat blades attached to a central hub. They provide radial flow and are effective for gas dispersion and solid suspension. Straight blade turbine impellers are commonly used in the chemical and petrochemical industries.
Pitched Blade Turbine Impellers: Pitched blade turbine impellers feature angled blades that provide a combination of axial and radial flow. They are suitable for a wide range of applications, including blending, solid suspension, and heat transfer. Pitched blade turbine impellers are commonly used in the chemical, food, and pharmaceutical industries.
Rushton Turbine Impellers: Rushton turbine impellers consist of six flat blades attached to a central disc. They provide high shear and are effective for gas-liquid dispersion and emulsification. Rushton turbine impellers are commonly used in the chemical and biotechnology industries.
Smith Turbine Impeller: Smith turbine impellers feature curved blades that provide a combination of axial and radial flow. They are designed to reduce power consumption while maintaining mixing efficiency. Smith turbine impellers are commonly used in the chemical and wastewater treatment industries.
Curved Blade Turbine Impellers: Curved blade turbine impellers feature blades with a curved profile, providing a combination of axial and radial flow. They are suitable for a wide range of applications, including blending, solid suspension, and heat transfer. Curved blade turbine impellers are commonly used in the chemical, food, and pharmaceutical industries.
Agitators with Retreat Curve Impellers
Agitators with retreat curve impellers are a type of agitator designed for efficient mixing processes and effective power usage. These impellers feature curved blades that are angled away from the direction of rotation, creating a unique flow pattern that combines both axial and radial flow components. The specific angle of the blades varies depending on the application, with standard angles ranging from 45° to 90°.
Retreat curve impellers are well-suited for medium to high viscosity fluids and can handle a wide range of mixing tasks, including blending, dispersion, and gas incorporation. The curved blade design promotes a more uniform mixture by creating a flow pattern that draws material from the bottom of the tank and disperses it throughout the vessel.
Agitators with Hydrofoil Impellers
Agitators with hydrofoil impellers feature a unique blade design that resembles a marine propeller, providing excellent fluid mixing solutions with minimal power consumption. The hydrofoil shape of the blades allows for a more efficient power usage compared to traditional flat blades, reducing production costs.
Hydrofoil impellers generate an axial flow pattern, making them suitable for mixing low to medium viscosity fluids. The axial flow creates a vertical motion in the mixing tank, ensuring effective mixing throughout the vessel. This flow pattern is particularly useful in applications requiring gas dispersion or solid suspension.
Agitators with Dispersion Blade Impellers
Agitators with dispersion blade impellers are designed for efficient mixing and dispersion operations, particularly in gas dispersion and immiscible mixtures. These impellers feature a unique blade design that promotes effective mixing and reduces power consumption. The blades are typically curved or angled, with variations in pitch angle and diameter to suit specific applications.
Dispersion blade impellers are commonly used in the chemical and pharmaceutical industries for processes involving gas-liquid reactions, such as fermentation, hydrogenation, and oxidation. They excel at creating a uniform mixture and improving mass transfer rates between the gas and liquid phases. The blade design generates a combination of radial and axial flow patterns, which enhances the dispersion of gas bubbles throughout the mixing tank.
Agitators with Coil Impellers
The coil impeller consists of a helical ribbon or spiral-shaped blade wrapped around the agitator shaft. This design creates a combination of radial and axial flow patterns, enhancing the mixing performance. As the impeller rotates, it generates a turbulent movement in the fluid, ensuring a consistent mixture and preventing the formation of dead zones.
Coil impellers are well-suited for handling medium to high viscosity fluids, as they provide a gentle mixing action while minimizing shear forces. This makes them ideal for applications involving shear-sensitive materials, such as polymer solutions, pastes, and gels. The coil design also promotes effective heat transfer, making these agitators suitable for use in heat exchangers and reactors.
How to Select an Agitator
- Viscosity: For low to medium viscosity fluids, propeller agitators or turbine agitators may be suitable. For more viscous liquids, anchor agitators or helical ribbon agitators are often used to ensure effective mixing and prevent dead zones.
- Flow Pattern: The desired flow pattern within the mixing tank is another essential consideration. Axial flow impellers, such as propeller agitators, create a flow pattern parallel to the agitator shaft, making them ideal for blending and solid suspension. Radial flow impellers, like Rushton turbine impellers, generate a flow pattern perpendicular to the agitator shaft, making them suitable for gas dispersion and heat transfer applications.
- Tank Geometry: The diameter of the agitator should be proportional to the tank diameter, typically ranging from 1/3 to 1/2 of the tank diameter. The placement of baffles and the overall tank design will also impact the choice of agitator to ensure efficient mixing and minimize dead zones.
- Power Requirement: The power requirement depends on the fluid properties, agitator speed, and desired mixing intensity. It is crucial to choose an agitator that can deliver the necessary power input while optimizing energy efficiency to minimize operating costs.
- Process Requirements: The specific process requirements, such as the need for heat transfer, gas dispersion, or chemical reactions, will dictate the type of agitator needed. For example, in applications requiring high heat transfer rates, agitators with high surface area impellers, like anchor agitators or helical ribbon agitators, may be preferred. For gas-liquid dispersion, Rushton turbine impellers or other radial flow impellers are often used.
- Material Compatibility: The materials of construction for the agitator must be compatible with the fluids or chemicals being mixed. In corrosive environments or when handling sensitive materials, such as in the pharmaceutical industry, agitators made from stainless steel or other corrosion-resistant alloys may be necessary to ensure long-term durability and product purity.