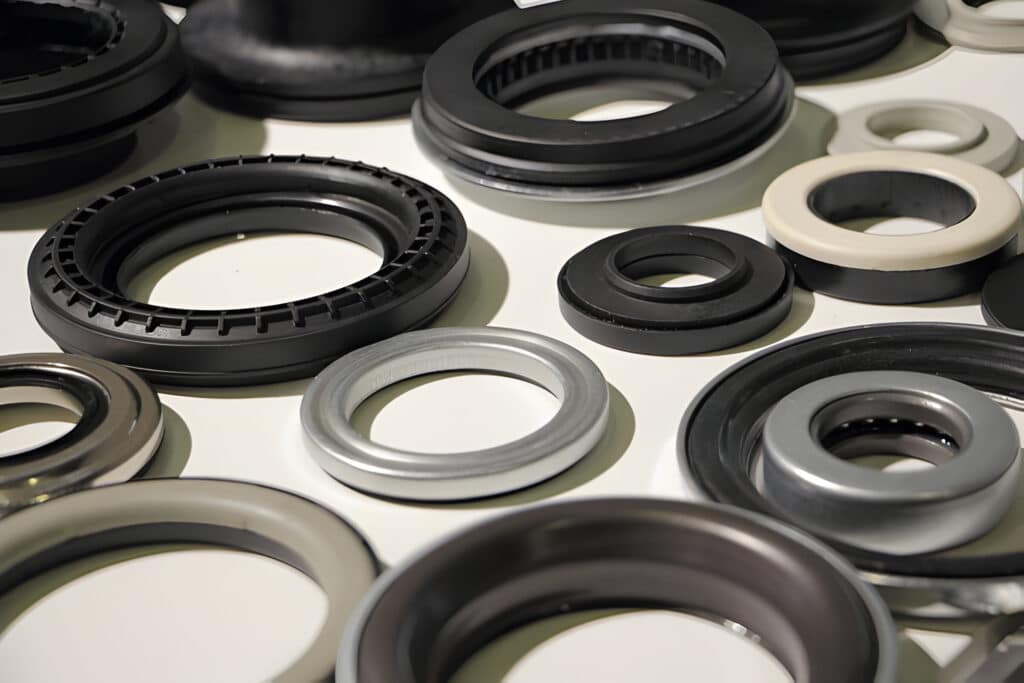
What Is a Bearing Seal
A bearing seal is a critical component in mechanical systems that helps protect bearings from contamination and retain lubricants. Bearing seals come in various types, each designed to suit specific operating conditions and requirements. The most common types of bearing seals include contact seals, non-contact seals, labyrinth seals, and bearing shields.
Contact Bearing Seals
Contact bearing seals, also known as lip seals, are the most common type of bearing seal. They feature a flexible sealing lip that maintains direct contact with the shaft or housing, creating a positive seal against contaminants and lubricant leakage.
Advantages of Contact Bearing Seals
- Provide a positive seal against contaminants and lubricant leakage
- Offer excellent chemical resistance and durability
- Suitable for a wide range of applications and operating conditions
- Low cost compared to other seal types
Disadvantages of Contact Bearing Seals
- Generate friction and heat due to constant contact with the shaft or housing
- Limited speed capability compared to non-contact seals
- May experience wear over time, requiring replacement
Types of Contact Bearing Seals
- Molded rubber seals (e.g., 2RS, 2RU)
- Low-friction contact rubber seals
- Double lip seals
- Nitrile (BUNA-N) and fluoroelastomer (FKM) materials
Non-contact Bearing Seals
Non-contact bearing seals, also known as gap seals, maintain a small clearance between the seal and the shaft or housing. This design minimizes friction and heat generation while still providing effective sealing against contaminants. Non-contact seals are commonly used in high-speed applications or where low torque is required.
Advantages of Non-contact Bearing Seals
- Minimal friction and heat generation due to lack of direct contact
- Suitable for high-speed applications
- Longer service life compared to contact seals
- Lower torque requirements
Disadvantages of Non-contact Bearing Seals
- May allow small amounts of contaminants to enter the bearing
- Require precise installation and alignment to maintain proper clearance
- Higher cost compared to contact seals
Types of Non-contact Bearing Seals
- Labyrinth seals
- Splash rings
- Non-contact rubber seals
- Plastic and rubber materials
Labyrinth Seals
Labyrinth seals are a type of non-contact seal that features a series of intricate passages and chambers designed to create a tortuous path for contaminants. This design effectively prevents the ingress of contaminants while allowing for minimal friction and heat generation. Labyrinth seals are commonly used in high-speed applications or where a high level of contamination protection is required.
Advantages of Labyrinth Seals
- Excellent protection against contaminants
- Suitable for high-speed applications
- Minimal friction and heat generation
- Long service life
Disadvantages of Labyrinth Seals
- Require precise installation and alignment
- May allow small amounts of lubricant leakage
- Higher cost compared to other seal types
Types of Labyrinth Seals
- Straight labyrinth seals
- Stepped labyrinth seals
- Stainless steel and brass materials
Bearing Shields
Bearing shields are thin metal or plastic discs that cover the side of the bearing, providing protection against larger contaminant particles. They are typically used in conjunction with other seal types to enhance overall sealing performance. Bearing shields are commonly used in applications where the primary concern is protection against solid contaminants rather than liquid or moisture ingress.
Advantages of Bearing Shields
- Provide additional protection against larger contaminant particles
- Low cost compared to other seal types
- Simple design and easy installation
Disadvantages of Bearing Shields
- Limited protection against liquid or moisture ingress
- May not provide a complete seal against smaller contaminant particles
Types and Materials of Bearing Shields
- Metal shields (e.g., stainless steel, steel)
- Plastic shields
- Single and double shielded bearings
Selecting the Right Seal Type
Operating Speed and Temperature Range
Contact seals, such as lip seals, are generally recommended for applications with lower speeds and temperatures, as they can maintain direct contact with the shaft without excessive wear or heat generation.
Non-contact seals are better suited for high-speed applications or environments with elevated temperatures, as they do not rely on direct contact and can operate with minimal friction and heat generation.
Contamination Level and Types of Contaminants
In highly contaminated environments, contact seals with additional dust lips or multi-lip designs can provide enhanced protection against the ingress of dirt, dust, and other particulates.
Non-contact seals are effective in preventing the entry of larger contaminants but may not be as efficient in sealing out finer particles. In such cases, a combination of seal types or the use of bearing shields can offer improved contamination resistance.
Lubricant Retention Requirements
The selected seal type should be capable of retaining the lubricant within the bearing while preventing leakage.
Contact seals, particularly those with multiple lips or specially designed geometries, can provide excellent lubricant retention by maintaining a tight seal against the shaft.
Non-contact seals may not be as effective in retaining lubricants, especially in applications with high rotational speeds or frequent changes in direction.
Friction and Heat Generation Concerns
Friction and heat generation are important considerations when selecting a bearing seal, as excessive friction can lead to increased wear, reduced efficiency, and premature failure.
Contact seals, while providing excellent sealing performance, can generate higher levels of friction due to their direct contact with the shaft. This friction can result in elevated operating temperatures, which may adversely affect the lubricant and bearing components.
Non-contact seals generate minimal friction and heat, making them suitable for applications where low friction and cool running are essential.