The design and performance of bellows rely heavily on the selection of appropriate materials. From stainless steels to advanced polymers, the choice of bellows material impacts critical factors such as durability, flexibility, and corrosion resistance.
This article provides an in-depth look at the various metallic and non-metallic materials commonly used in bellows applications. We will explore the properties, advantages, and considerations for each material category, enabling engineers and purchasing managers to make informed decisions when specifying bellows for their projects.
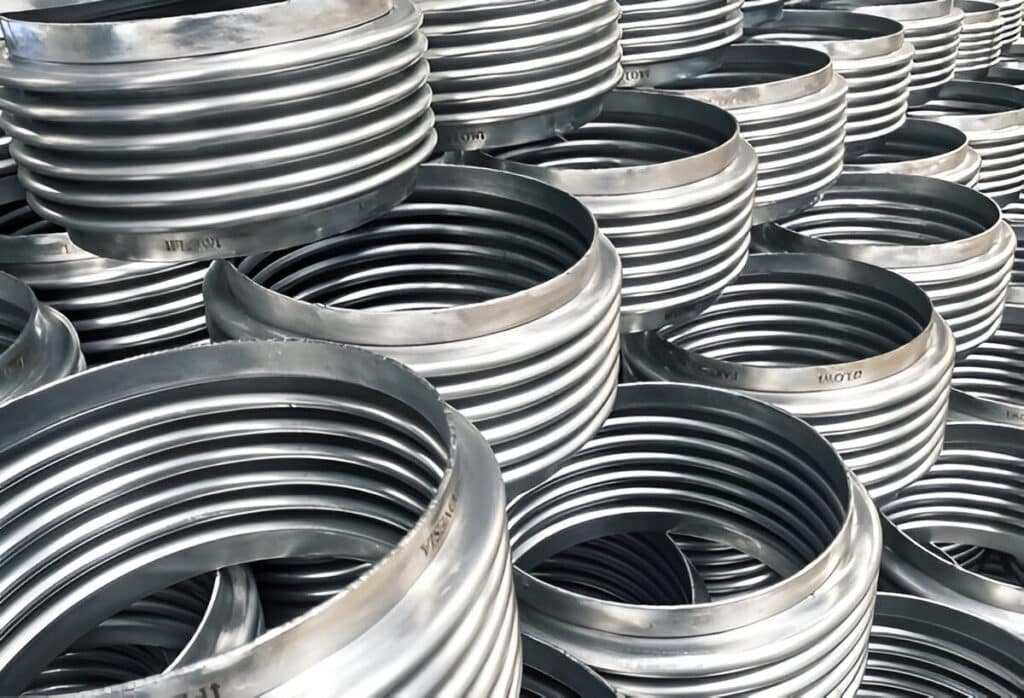
Metallic Bellows Materials
Stainless Steels
Stainless steels are among the most commonly used materials for metallic bellows due to their excellent corrosion resistance, strength, and formability. The chromium content in stainless steels forms a passive layer on the surface, protecting the material from oxidation and corrosion. Several grades of stainless steel are commonly employed in bellows manufacturing:
- 304 (UNS: S30400): This austenitic stainless steel contains 18% chromium and 8% nickel, offering good corrosion resistance, formability, and weldability. It is widely used in applications with moderate corrosion requirements.
- 304L (UNS: S30403): A low-carbon variant of 304 stainless steel, 304L has improved weldability and resistance to intergranular corrosion. It is often specified for applications involving welding or exposure to mildly corrosive environments.
- 316 (UNS: S31600): With the addition of molybdenum, 316 stainless steel provides enhanced corrosion resistance, particularly against pitting and crevice corrosion in chloride-containing environments. It is suitable for more demanding applications, such as those involving seawater or chemicals.
- 316L (UNS: S31603): Similar to 304L, this low-carbon version of 316 stainless steel offers improved weldability and resistance to intergranular corrosion. It is frequently used in welded constructions exposed to corrosive environments.
- 321 (UNS: S32100): This titanium-stabilized austenitic stainless steel is designed to prevent chromium carbide precipitation during welding or high-temperature exposure. It maintains its corrosion resistance and mechanical properties in elevated-temperature applications.
Nickel Alloys
Nickel alloys offer exceptional corrosion resistance, high-temperature strength, and oxidation resistance. They are often specified for bellows operating in extreme environments, such as those found in aerospace, chemical processing, and oil and gas industries. Some common nickel alloys used in bellows include:
- Inconel: A family of austenitic nickel-chromium-based superalloys, Inconel materials (e.g., Inconel 625, Inconel 718) provide excellent strength and corrosion resistance at elevated temperatures. They are used in high-temperature, corrosive environments, such as jet engines and chemical processing equipment.
- Hastelloy: These nickel-molybdenum alloys (e.g., Hastelloy C-22, Hastelloy C-276) offer outstanding resistance to oxidizing and reducing acids, as well as stress corrosion cracking. They are employed in severe corrosive environments, including chemical processing and pollution control systems.
- Monel: A nickel-copper alloy, Monel exhibits good resistance to seawater, hydrofluoric acid, and sulfuric acid. It is used in marine applications, acid processing, and food and pharmaceutical industries.
Brass and Bronze
Brass and bronze are copper alloys that provide moderate strength, good formability, and resistance to certain corrosive environments. Brass, an alloy of copper and zinc, is known for its machinability and resistance to atmospheric corrosion. Bronze, typically composed of copper and tin, offers higher strength and wear resistance compared to brass. These materials are often used in less demanding applications or for decorative purposes.
Beryllium Copper
Beryllium copper is a copper alloy containing a small amount of beryllium, which significantly enhances its strength, wear resistance, and electrical conductivity. This material is used in bellows that require high fatigue strength, good thermal conductivity, and resistance to corrosion in mild environments. Beryllium copper bellows are often found in electrical and electronic applications, as well as in precision instruments.
Titanium
Titanium and its alloys are known for their exceptional strength-to-weight ratio, corrosion resistance, and biocompatibility. They are used in bellows for aerospace, medical, and marine applications.
Aluminum
Aluminum alloys, such as 5052 and 6061, offer a combination of light weight, good formability, and moderate strength. Aluminum bellows are often used in automotive exhaust systems, HVAC equipment, and lightweight mechanical assemblies.
Non-Metallic Bellows Materials
Polyurethane
Polyurethane is a versatile polymer known for its outstanding abrasion resistance, tear strength, and flexibility. It can withstand exposure to a wide range of chemicals, oils, and solvents. Polyurethane bellows are well-suited for applications requiring high flexibility and durability, such as dust covers, protective boots, and machinery seals.
PVC
Polyvinyl chloride (PVC) is a thermoplastic polymer known for its good chemical resistance, flame retardancy, and insulating properties. PVC bellows are commonly used in pipe and duct systems, as well as protective covers for machinery. They offer a cost-effective solution for applications requiring moderate flexibility and durability.
Neoprene Coated Nylon
Neoprene coated nylon bellows offer a combination of flexibility, strength, and chemical resistance. The nylon fabric provides high tensile strength, while the neoprene coating enhances chemical resistance and weatherability. These bellows are commonly used in outdoor applications, such as protective covers for construction equipment and marine bellows.
Hypalon Coated Nylon
Hypalon coated nylon bellows provide superior resistance to chemicals, ozone, and UV radiation compared to neoprene coated nylon. The Hypalon coating offers excellent weatherability and durability, making these bellows ideal for harsh outdoor environments. Common applications include protective covers for industrial machinery and equipment exposed to sunlight and ozone.
Fiberglass with Coatings
Fiberglass bellows with various coatings offer high strength, temperature resistance, and insulating properties. The fiberglass fabric provides excellent tensile strength and dimensional stability, while the coatings enhance chemical resistance and weatherability. Common coatings include silicone, PTFE, and neoprene. Fiberglass bellows are well-suited for high-temperature applications, such as exhaust systems and thermal expansion joints.