What is the purpose of a pump coupling, and why is it crucial in mechanical systems?
A pump coupling is a mechanical device that connects the shaft of a pump to the shaft of a motor, enabling power transmission.
Selecting the appropriate coupling is crucial for ensuring optimal pump performance and reliability. Factors such as torque transmission, shaft alignment, and operating conditions must be considered when choosing a coupling type.
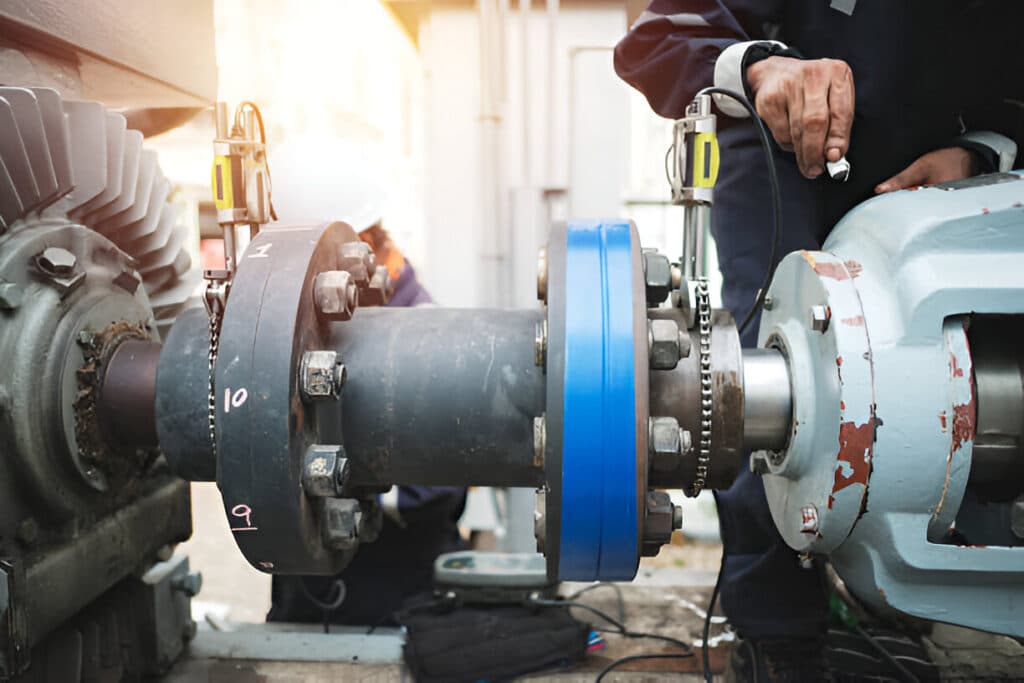
Rigid couplings
Rigid couplings are a type of pump coupling that provides a permanent or semi-permanent connection between two shafts. They are designed to transmit torque and power while maintaining precise alignment between the connected shafts. Rigid couplings offer high torsional rigidity and are suitable for applications with minimal misalignment.
Common types of rigid couplings include muff couplings, flange couplings, and clamp couplings. These couplings typically consist of metal components that create a mechanical connection between the shaft ends. Rigid couplings do not allow for significant angular, radial, or axial misalignment.
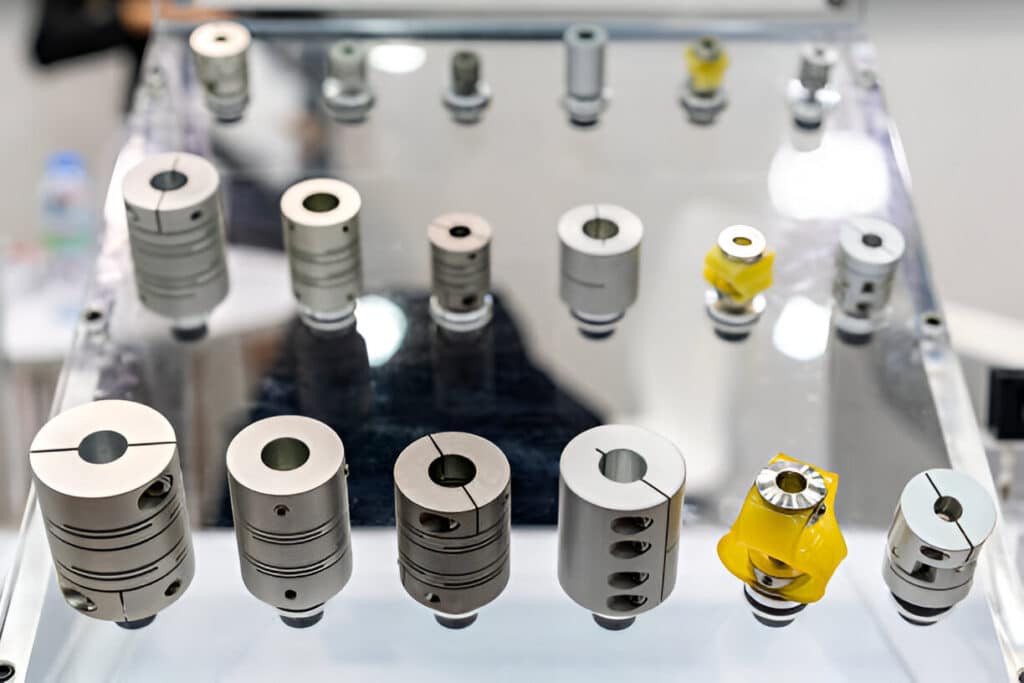
Flexible couplings
Elastomeric Coupling
Elastomeric couplings feature flexible rubber or elastomer elements that connect two hubs or flanges. These elements accommodate misalignment and dampen vibrations, making them suitable for applications with shock loads or slight misalignments between shafts. The elastomer material allows for some angular and parallel misalignment while transmitting torque between the pump and motor shafts.
Grid Coupling
Grid couplings consist of two grooved hubs connected by a serpentine grid made of flexible metal alloy. The grid element fits into the grooves of the hubs, allowing for angular and parallel misalignment compensation. Grid couplings offer high torsional rigidity and can handle shock loads, making them suitable for power transmission applications in pumps and other industrial machinery.
Disc Coupling
Disc couplings use a series of thin, flexible metal discs to connect two shaft hubs. The discs, made from stainless steel or other durable materials, provide misalignment capabilities and allow for axial movement due to thermal expansion. Disc couplings offer high torsional stiffness, low restoring forces, and require no lubrication, making them a low-maintenance option for connecting pump shafts.
Gear Coupling
Gear couplings feature external gear teeth on the hubs that mesh with internal teeth on a connecting sleeve. The gear teeth allow for angular and parallel misalignment while transmitting torque between the pump and motor shafts. Gear couplings provide high torque capacity and torsional stiffness, making them suitable for heavy-duty power transmission applications. However, they require regular lubrication and may generate noise during operation.
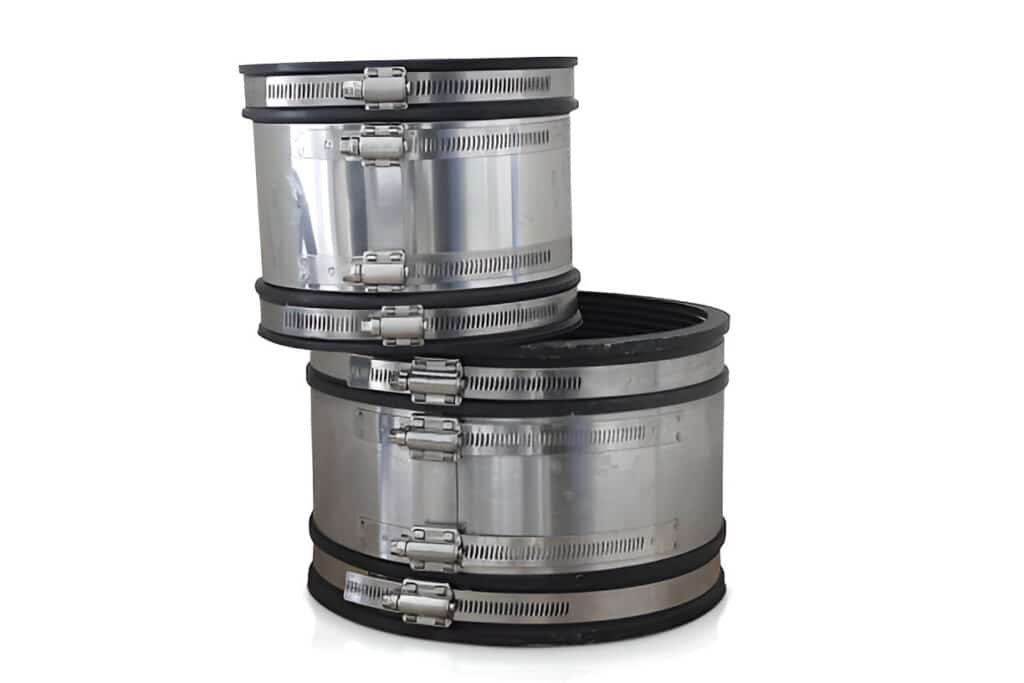
Magnetic Couplings
Magnetic couplings offer a unique solution for connecting pump shafts without physical contact. They consist of two main components: the drive magnet assembly and the driven magnet assembly. The drive magnet is connected to the motor shaft, while the driven magnet is attached to the pump shaft.
Magnetic forces transfer torque between the two assemblies, allowing for power transmission without mechanical connection. This eliminates the need for seals, lubrication, and regular maintenance associated with traditional couplings. Magnetic couplings can accommodate a certain degree of misalignment, reducing the risk of premature wear and failure.
Coupling Selection Factors
Torque Transmission and Service Factors
Couplings must be able to transmit the required torque and accommodate service factors such as shock loads and vibrations. The coupling’s torque capacity should exceed the maximum torque demand of the application, considering any potential overload conditions.
Shaft Misalignment Tolerance
Misalignment between the pump and motor shafts is inevitable due to factors like manufacturing tolerances, installation errors, and thermal expansion. Couplings should be selected based on their ability to accommodate axial, radial, and angular misalignments without causing excessive stress on the connected components or reducing the coupling’s life expectancy.
Ease of Installation and Maintenance
The coupling design should facilitate easy installation and alignment, minimizing downtime during initial setup and subsequent maintenance. Couplings that require minimal lubrication and offer extended service intervals are preferred for reduced maintenance costs and improved reliability.
Environmental Factors
The operating environment plays a crucial role in coupling selection. Factors such as temperature extremes, corrosive conditions, and contamination should be considered. Couplings made from materials resistant to the specific environmental challenges ensure optimal performance and longevity.
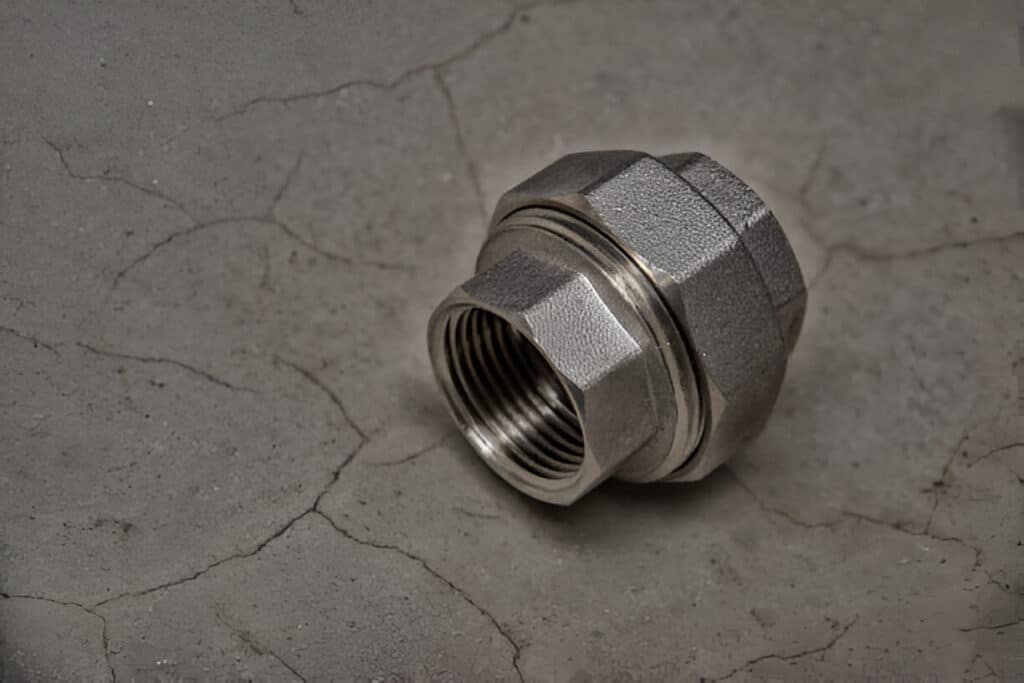
FAQs
What are spacer pump couplings?
Spacer pump couplings are used to connect two shafts with a gap between them. They allow for easy installation and removal of the pump without disturbing the motor or other components.
What are the advantages of using flexible pump couplings?
Flexible pump couplings can accommodate misalignment, reduce vibration and shock transmission, and compensate for thermal expansion or contraction of the shafts.
When should rigid pump couplings be used?
Rigid pump couplings should be used when precise alignment is required, and there is no need for misalignment compensation or vibration damping.
What materials are pump couplings typically made from?
Pump couplings can be made from various materials, including stainless steel, cast iron, aluminum, and elastomers, depending on the application and environmental factors.
What is the difference between a jaw coupling and a spider coupling?
Jaw couplings use interlocking jaws to connect the shafts, while spider couplings use a flexible elastomeric element called a spider to transmit torque and accommodate misalignment.
How often should pump couplings be inspected and maintained?
Pump couplings should be inspected regularly for wear, damage, or misalignment. The frequency of maintenance depends on the application and operating conditions, but it is generally recommended to check couplings at least every six months.
In Conclusion
Pump couplings are essential components in various industrial applications. Selecting the appropriate type of coupling based on specific requirements ensures optimal performance, reliability, and efficiency.
To learn more about pump couplings and how to choose the right one for your application, consult with a trusted supplier or engineer.