Springs are essential mechanical components that store and release energy, providing resistance to force or torque. They play a crucial role in various applications, from automotive suspension systems to consumer products. This article explores the different types of springs based on their load application, force-displacement characteristics, and manufacturing methods.
Classification Based on How the Load Is Applied
Compression Springs
Compression springs are one of the most common types of springs. They are designed to resist compressive forces applied axially, storing mechanical energy when compressed and releasing it when the load is removed. These springs have a wide range of applications, including automotive suspension systems, industrial machinery, and consumer products like pens and mouse traps.
Compression springs are typically made from round wire coiled into a helical shape, with a constant diameter throughout their length. The choice of material depends on the specific application requirements, such as load capacity, corrosion resistance, and temperature resistance. Common materials include spring steel, stainless steel, and phosphor bronze.
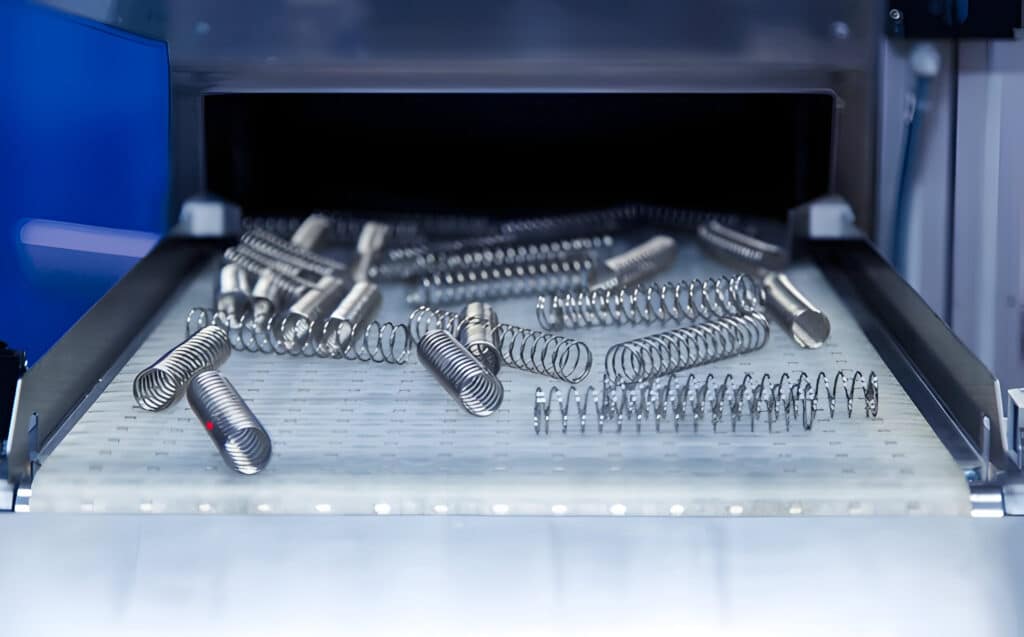
Extension Springs
Extension springs, also known as tension springs, are designed to resist tensile forces applied axially. They store mechanical energy when stretched and release it when the load is removed. Extension springs are commonly used in garage door systems, agricultural equipment, and exercise equipment.
Extension springs are made by coiling a wire into a helical shape, with hooks or loops formed at each end for attachment. The initial tension in the spring is determined by the manufacturing process, which involves stretching the spring to a specific length before heat treatment.
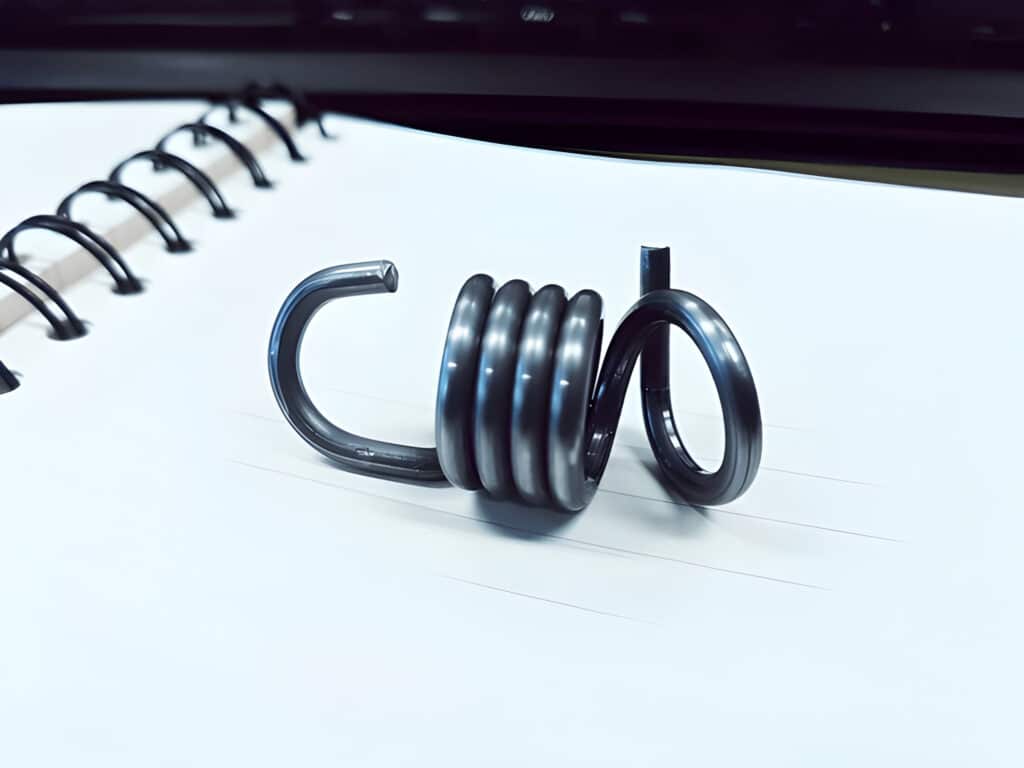
Torsion Springs
Torsion springs are designed to resist rotational forces or torque applied about their axis. They store mechanical energy when twisted and release it when the torque is removed. Torsion springs are used in various applications, including door hinges, automotive seat recliners, and window shade rollers.
Torsion springs are typically made by coiling a rectangular or square wire into a helical shape, with the ends formed into specific shapes for attachment. The choice of material depends on the required spring rate, fatigue life, and environmental conditions. Common materials include spring steel and stainless steel.
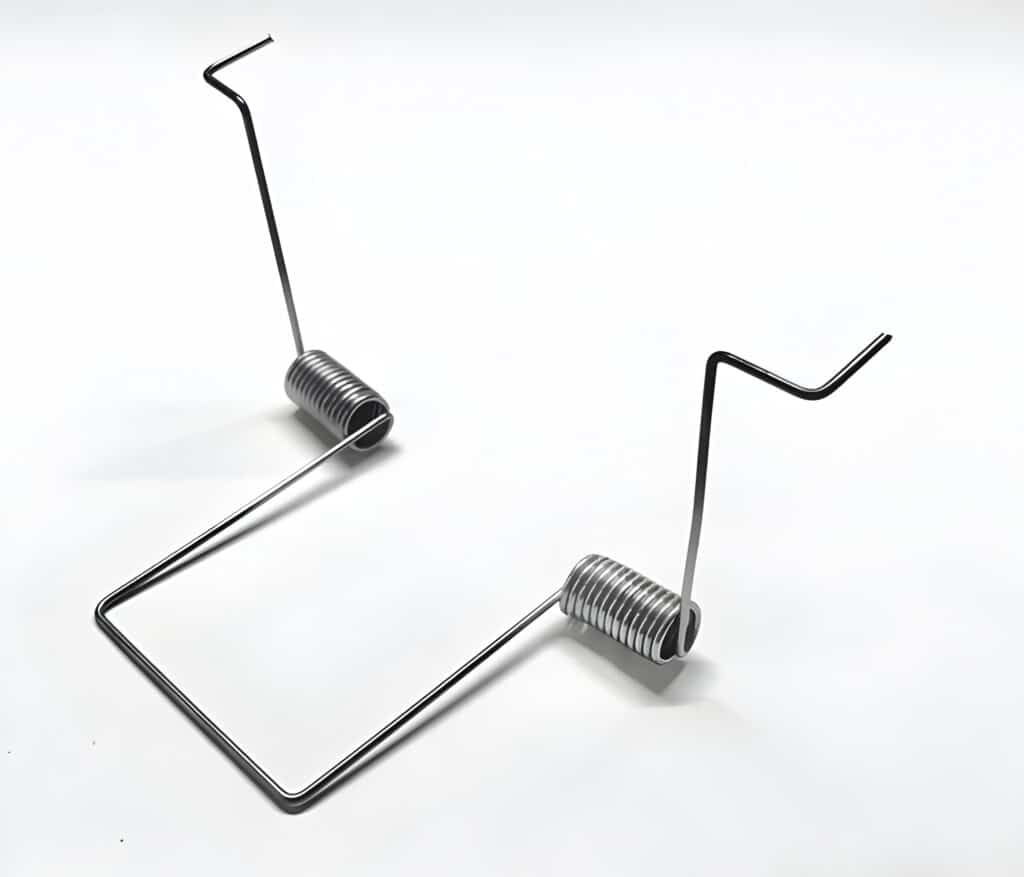
Classification Based on Force and Displacement
Linear Springs
Linear springs exhibit a constant spring rate, meaning that the force required to compress or extend the spring is directly proportional to the displacement.
This linear relationship is described by Hooke’s law: F = kx,
where:
F is the force,
k is the spring constant,
x is the displacement.
Linear springs are used in applications where a consistent force-displacement relationship is required, such as in automotive suspension systems and industrial machinery. They are typically made from round wire coiled into a helical shape, with a constant diameter throughout their length.
Variable Rate Springs
Variable rate springs, also known as non-linear springs, exhibit a changing spring rate as they are compressed or extended. This means that the force required to compress or extend the spring changes non-linearly with displacement. Variable rate springs are used in applications where a specific force-displacement profile is required, such as in automotive valve springs and off-road vehicle suspension systems.
Variable rate springs can be designed by varying the coil diameter, pitch, or wire diameter along the length of the spring. Conical springs and barrel-shaped springs are examples of variable rate springs, where the coil diameter changes along the length of the spring.
Constant Force Springs
Constant force springs are designed to provide a constant force output over a specific range of motion. They are made from a pre-stressed strip of material, typically stainless steel, which is coiled into a spiral shape. As the spring is extended, the material unwinds from the coil, maintaining a constant force throughout its range of motion.
Constant force springs are used in applications where a consistent force is required, such as in counterbalance mechanisms, door closers, and tensioning devices. They offer advantages such as compact size, long service life, and consistent performance over their range of motion.
Classification by Manufacturing Method
Coil Springs
Coil springs are the most common type of spring, made by winding a wire into a helical shape. They can be designed as compression, extension, or torsion springs, depending on the application requirements. Coil springs are manufactured using various methods, including hot coiling, cold coiling, and CNC coiling.
The choice of manufacturing method depends on factors such as the spring material, wire diameter, and production volume. Hot coiling is typically used for larger wire diameters and high-strength materials, while cold coiling is used for smaller wire diameters and lower-strength materials. CNC coiling offers high precision and flexibility, enabling the production of complex spring geometries.
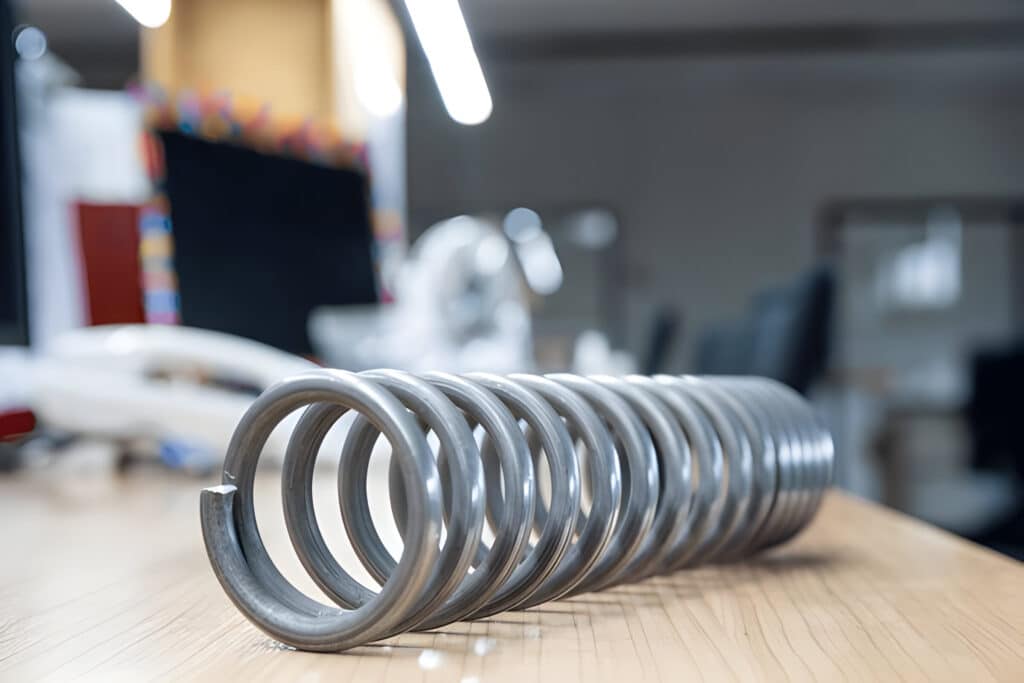
Flat Springs
Flat springs are made from flat strips of material, typically spring steel or stainless steel, formed into various shapes such as leaf springs, Belleville washers, and wave springs. They are designed to provide resistance to bending or compression forces, depending on the specific configuration.
Leaf springs are commonly used in automotive suspension systems, particularly in heavy-duty vehicles, to support the vehicle’s weight and provide shock absorption. They consist of several layers of curved spring steel, known as leaves, stacked together and connected at the ends using spring shackles.
Belleville washers, also known as disc springs, are conical-shaped washers that provide resistance to axial loads. They can be stacked in series or parallel to achieve desired load-deflection characteristics, making them suitable for applications with limited space and high load requirements.
Wave springs are made by forming a flat wire into a wavy shape, providing resistance to axial loads while occupying minimal space. They are used in applications where high loads and small deflections are required, such as in aerospace and industrial equipment.
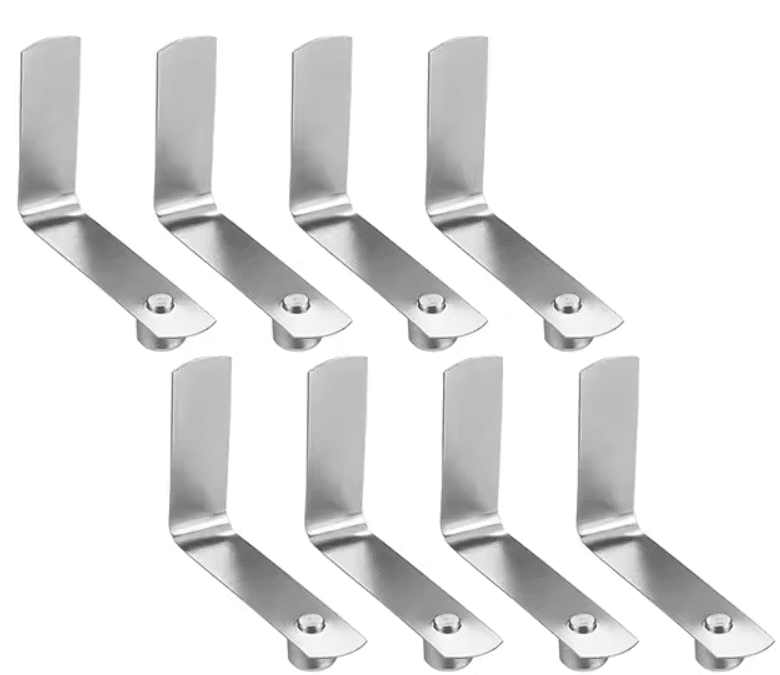
Disk Springs
Disk springs, also known as Belleville springs, are conical-shaped washers that provide resistance to axial loads. They are made by stamping or forging a flat circular disk with a specific cone angle and inner and outer diameters. Disk springs can be stacked in series or parallel to achieve desired load-deflection characteristics.
Disk springs offer several advantages over traditional coil springs, including high load capacity, small deflection, and compact size. They are used in various applications, such as in heavy machinery, automotive clutches, and valves, where high loads and limited space are critical factors.
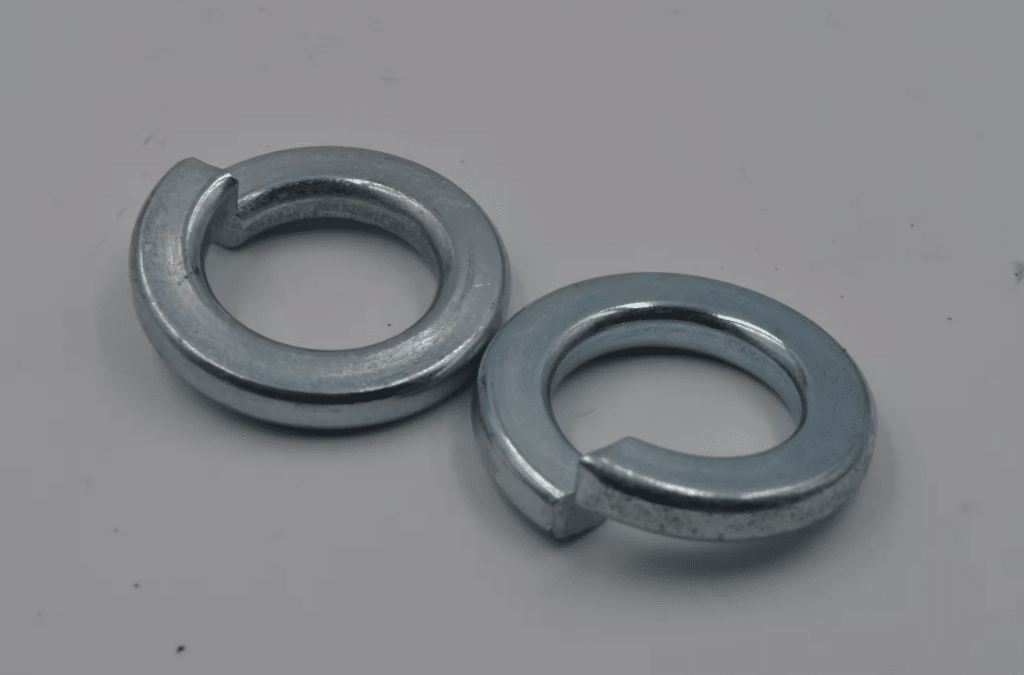
Machined Springs
Machined springs are custom-designed springs manufactured using CNC machining processes, such as milling, turning, and grinding. They are typically made from solid bars or tubes of material, such as spring steel, stainless steel, or titanium, and can be designed to meet specific load-deflection requirements.
Machined springs offer several advantages over traditional spring manufacturing methods, including high precision, complex geometries, and the ability to incorporate features such as mounting holes and threads. They are used in specialized applications, such as in aerospace, medical devices, and high-performance industrial equipment.
Molded Springs
Molded springs are made by injecting a polymer material, such as polyurethane or nylon, into a mold cavity shaped like the desired spring geometry. They offer unique properties compared to metal springs, such as high corrosion resistance, low weight, and the ability to dampen vibrations.
Molded springs are used in various applications, such as in automotive suspension bushings, industrial vibration isolators, and medical devices. The choice of polymer material depends on factors such as load capacity, temperature resistance, and chemical compatibility with the operating environment.
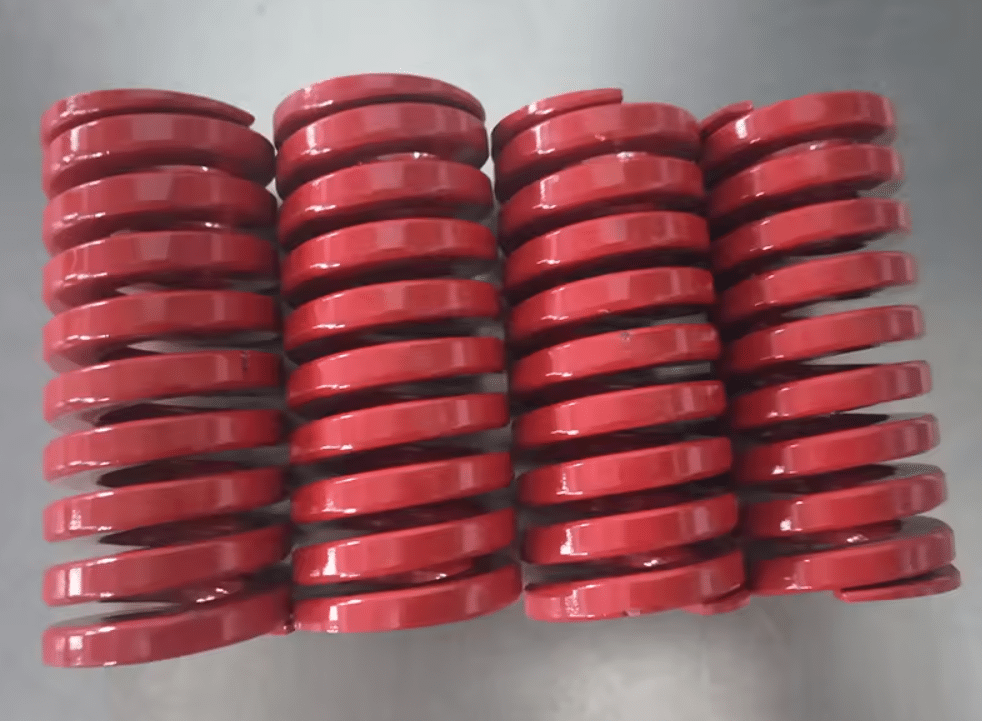
Gas Springs
Gas springs are a type of spring that uses compressed gas, typically nitrogen, to provide resistance to compressive forces. They consist of a sealed cylinder containing a piston and compressed gas, which exerts a force on the piston when the spring is compressed.
Gas springs offer several advantages over mechanical springs, including adjustable force output, compact size, and the ability to provide damping. They are used in various applications, such as in automotive hood and trunk lift supports, office chair height adjustment mechanisms, and industrial machinery.
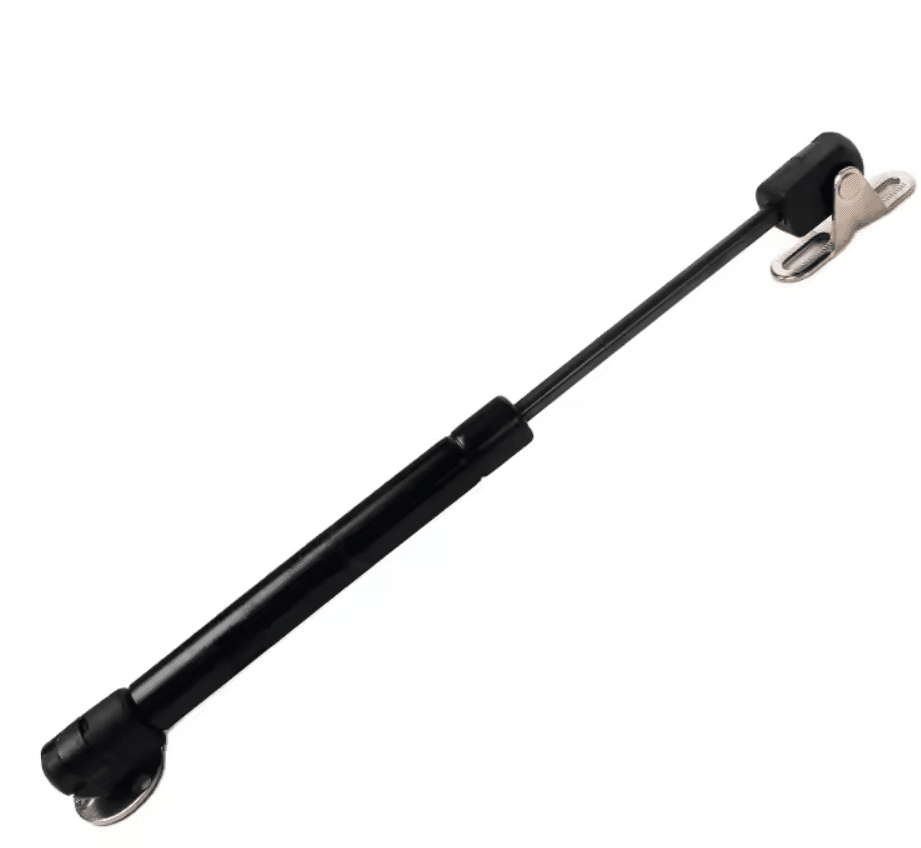
Air Springs
Air springs, also known as pneumatic springs, use compressed air to provide resistance to compressive forces. They consist of a flexible bellows or diaphragm filled with compressed air, which expands and contracts as the spring is loaded and unloaded.
Air springs offer several advantages over mechanical springs, including adjustable stiffness, load leveling capabilities, and vibration isolation. They are used in various applications, such as in automotive air suspension systems, industrial vibration isolation mounts, and agricultural equipment.
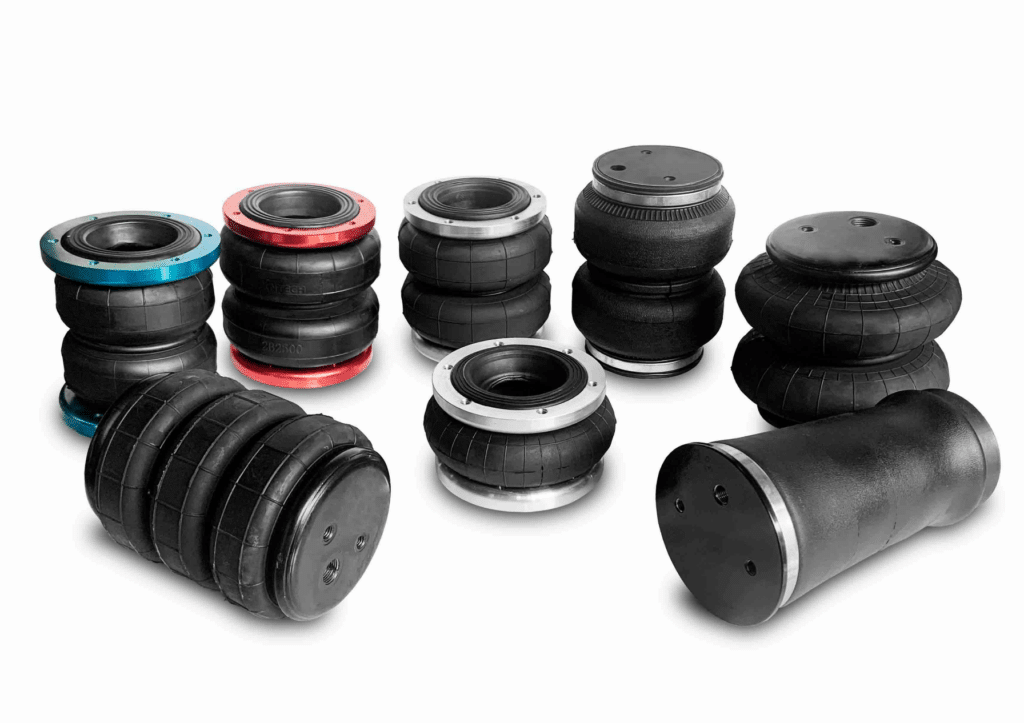
Leaf Springs
Leaf springs are a type of flat spring commonly used in automotive suspension systems, particularly in heavy-duty vehicles. They consist of several layers of curved spring steel, known as leaves, stacked together and connected at the ends using spring shackles.
Leaf springs are designed to support the vehicle’s weight and provide shock absorption, helping to improve ride comfort and handling. They can be configured in various ways, such as semi-elliptical, quarter-elliptical, or cantilever, depending on the specific application requirements.
The choice of leaf spring design depends on factors such as load capacity, vehicle weight distribution, and available space. Leaf springs are known for their durability, load-carrying capacity, and ability to provide lateral stability, making them suitable for heavy-duty applications such as commercial trucks and off-road vehicles.
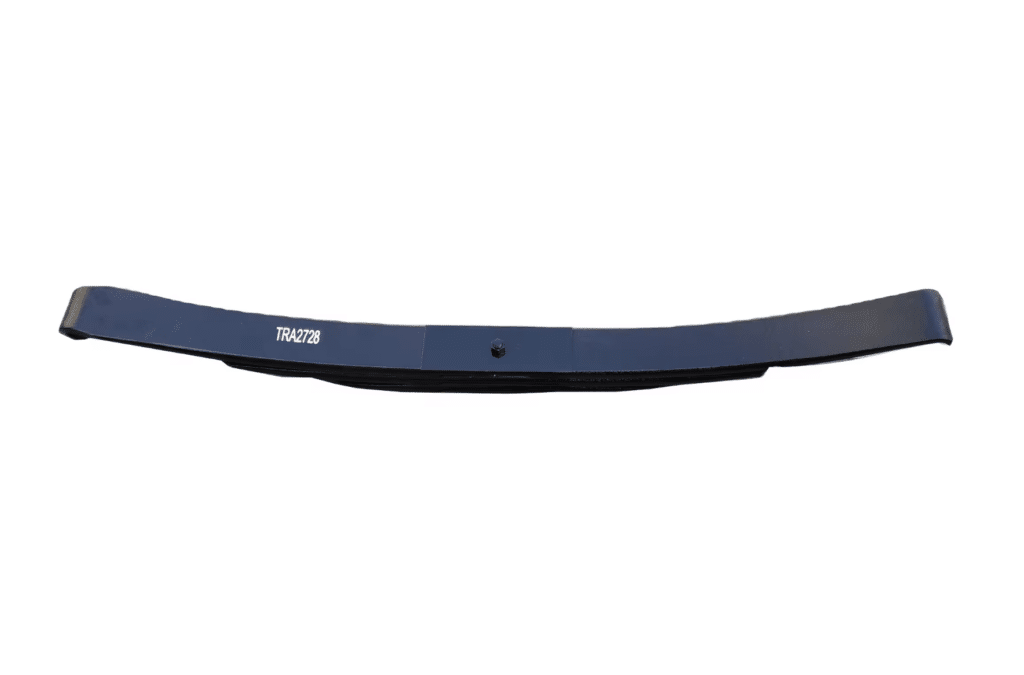
Helical Springs
Helical springs are a type of coil spring made by winding a wire into a helical shape, with a constant or variable diameter. They can be designed as compression, extension, or torsion springs, depending on the application requirements.
Basic Spring Principles
Springs are mechanical devices that store and release energy based on the principles of elasticity and Hooke’s law. When a force is applied to a spring, it deforms, storing potential energy in the form of strain energy. When the force is removed, the spring returns to its original shape, releasing the stored energy.
The relationship between the applied force and the resulting deformation is described by Hooke’s law, F = kx, where F is the force, k is the spring constant, and x is the deformation. The spring constant, also known as the spring rate, determines the stiffness of the spring and is dependent on factors such as the material properties, cross-sectional area, and length of the spring.
Springs are designed to operate within their elastic limit, where the deformation is directly proportional to the applied force. If the force exceeds the elastic limit, the spring may undergo permanent deformation or failure, compromising its performance and safety.
The energy storage capacity of a spring is determined by its geometry, material properties, and the applied load. The maximum energy storage occurs when the spring is compressed or extended to its solid height or maximum extension, respectively.