Magnetic drive pumps are a type of pump that uses magnetic coupling to transmit power from the motor to the impeller, eliminating the need for a mechanical seal.
This article will explore the working principles, advantages, and applications of magnetic drive pumps in various industries.
By understanding the unique features of these pumps, readers can make informed decisions when selecting pumping solutions for their specific needs.
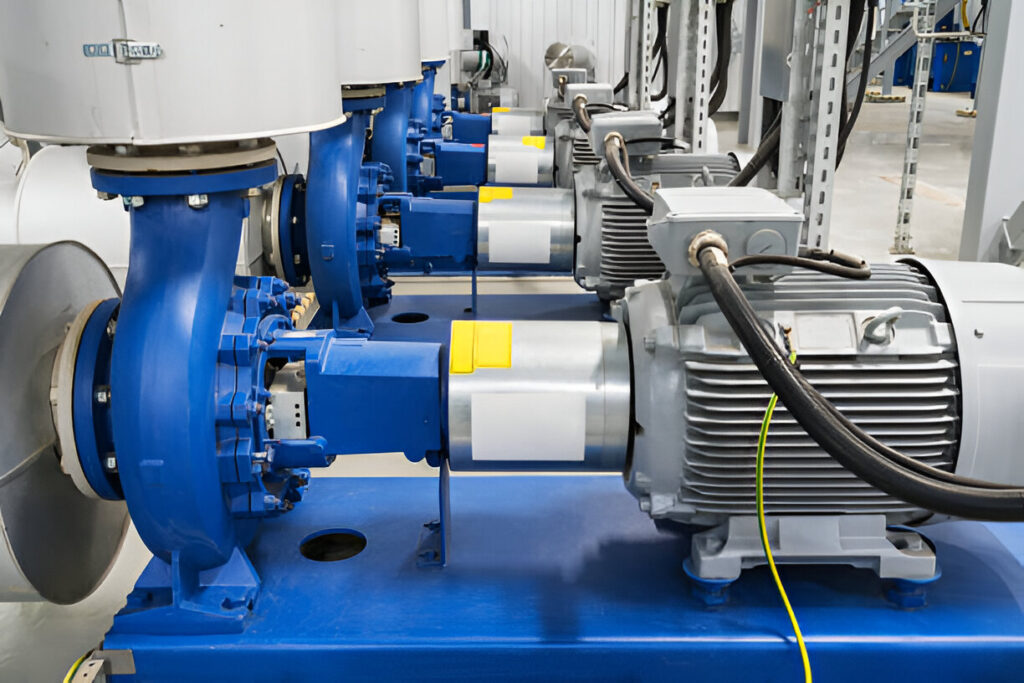
What Are Magnetic Drive Pumps
Magnetic drive pumps, also known as mag-drive pumps or seal-less pumps, are a type of pump that utilizes a magnetic coupling to transfer torque from the motor to the impeller without direct mechanical contact. This innovative design eliminates the need for traditional shaft seals, offering a leak-free solution for handling various liquids, including aggressive acids, toxic chemicals, and ultra-pure fluids.
How Magnetic Drive Pumps Work
The working principle of magnetic drive pumps relies on the power of magnetic fields to transmit torque from the motor to the impeller. The pump consists of two main assemblies: the outer drive magnet assembly, which is connected to the motor shaft, and the inner magnet assembly, which is coupled to the impeller.
When the motor rotates, the outer drive magnet creates a rotating magnetic field that interacts with the inner magnet assembly, causing the impeller to rotate. The containment shell, typically made of stainless steel or other corrosion-resistant materials, forms a sealed barrier between the fluid being pumped and the external environment.
As the impeller rotates, it generates centrifugal force, which propels the fluid from the inlet to the outlet of the pump. The absence of a mechanical seal eliminates the risk of leakage, making magnetic drive pumps suitable for handling a wide range of fluids, including those that are difficult to seal, such as low-viscosity liquids, liquids with suspended solids, and fluids that tend to crystallize or polymerize.
Components of Magnetic Drive Pumps
Magnetic drive pumps consist of several key components that enable their seal-less, leak-free operation. The main components include:
- Outer magnet assembly (drive magnet): This is the magnetic assembly that is connected to the motor shaft and rotates with it. It creates the magnetic field that drives the inner magnet assembly and impeller.
- Inner magnet assembly: Also known as the driven magnet, this assembly is located inside the containment shell and is coupled to the impeller. It is driven by the magnetic field created by the outer magnet assembly.
- Containment shell/rear casing: The containment shell is a stationary component that separates the pumped fluid from the atmosphere and the outer magnet assembly. It is typically made of corrosion-resistant materials like stainless steel or high-performance polymers like polyvinylidene fluoride (PVDF).
- Impeller: The impeller is the rotating component responsible for moving the fluid through the pump. In magnetic drive pumps, the impeller is directly coupled to the inner magnet assembly and is driven by the magnetic field created by the outer magnet assembly.
Other important components in magnetic drive pumps include:
- Bearings: These support the inner magnet assembly and impeller, allowing them to rotate smoothly. Common bearing materials include carbon, ceramic, and silicon carbide.
- Motor adapter: This component connects the motor to the outer magnet assembly and ensures proper alignment between the motor shaft and the drive magnet.
Advantages of Magnetic Drive Pumps
- Leak-free, seal-less design: Eliminates the risk of leakage, enhancing safety for hazardous or expensive liquids.
- Handling difficult liquids: Excels with aggressive acids, corrosive chemicals, and ultra-pure fluids.
- Longer MTBF: Reduced wear and tear leads to increased reliability and lower operating costs.
- Handling difficult-to-seal liquids: Effective with liquids prone to crystallization or polymerization.
- Productivity enhancement: Robust construction and reliable performance minimize downtime.
- Dry run protection: Safeguards prevent damage during dry run conditions.
- Corrosion resistance: Constructed with materials suitable for handling corrosive liquids.
- Compact design: Simplifies installation and reduces overall system footprint.
Disadvantages of Magnetic Drive Pumps
- Higher initial costs: More expensive upfront than traditional mechanically sealed pumps.
- Limited flow and pressure capabilities: Restricted at larger sizes due to magnetic coupling torque limitations.
- Dry running and overheating risks: Can damage components if run without sufficient liquid for cooling.
- Potential for decoupling: Magnetic coupling may separate under sudden load increases or operation outside the preferred range.
- Limited solids handling ability: Best suited for clean liquids; may struggle with high solids content or abrasive particles.
- Vibration concerns: This can be an issue, especially at higher speeds or with entrained gases.
- Bearing wear: Accelerated wear is possible if the pumped fluid has poor lubricating properties or contains abrasives.
- Reduced efficiency: Due to eddy current losses in the containment shell.
- Demagnetization risk: High temperatures or chemical corrosion can weaken magnets over time.
Applications of Magnetic Drive Pumps
- Chemical processing and transfer
- Pharmaceutical production
- Food and beverage processing
- Pulp and paper industry
- Petrochemical and refining
- Semiconductor manufacturing
- Water treatment and purification
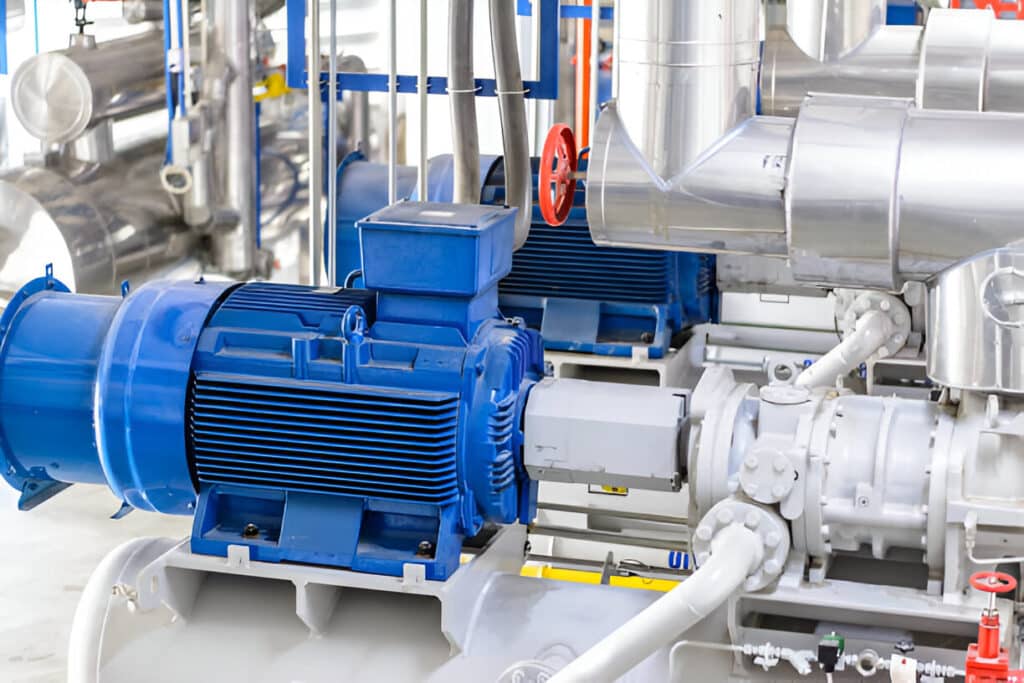
Common Liquids Handled by Magnetic Drive Pumps
- Acids, caustics, solvents
- Heat transfer fluids
- Ultra-pure liquids
- Polymers and resins
Types of Magnetic Drive Pumps
Centrifugal
Centrifugal magnetic drive pumps are the most common type of mag-drive pump, offering a wide range of flow rates and pressure capabilities. They use a rotating impeller to create centrifugal force, which moves the fluid through the pump. Centrifugal mag-drive pumps are ideal for handling clean, non-abrasive liquids in various industrial applications, such as chemical transfer, beverage processing, and ultra-pure liquid handling.
Positive Displacement
Positive displacement magnetic drive pumps are designed to handle high-viscosity fluids and provide consistent flow rates regardless of pressure changes. These pumps use a rotating mechanism, such as gears or vanes, to trap and move a fixed volume of fluid with each rotation. Positive displacement mag-drive pumps are commonly used in applications involving high-viscosity liquids, such as polymers, resins, and some food processing applications.
Regenerative Turbine Pumps
Regenerative turbine magnetic drive pumps, also known as peripheral or side-channel pumps, are a type of centrifugal pump that combines the features of both centrifugal and positive displacement pumps. They use an impeller with a series of small cells that rotate at high speeds, creating a regenerative turbine action. This design allows for high pressure and low flow rates, making them suitable for applications such as boiler feed, reverse osmosis, and high-pressure cleaning.
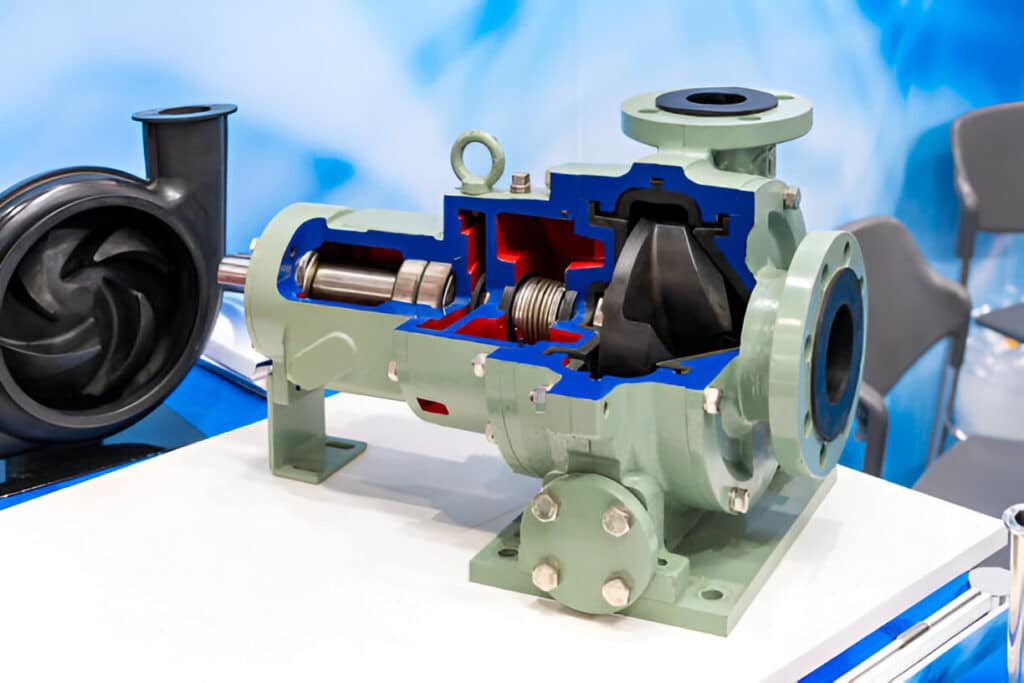
Selecting Magnetic Drive Pumps
Flow rate and pressure requirements
Magnetic drive pumps are available in a wide range of sizes and configurations, each designed to handle specific flow rates and pressure ranges. Determine the maximum flow rate and pressure needed for your process, and choose a pump that can comfortably meet those requirements.
Fluid properties (viscosity, specific gravity, temperature)
Consider the fluid’s viscosity, specific gravity, and temperature, as these characteristics can significantly impact pump performance. Magnetic drive pumps are well-suited for handling a wide range of viscosities, from thin liquids like water to more viscous fluids like oils and polymers. However, extremely high viscosities may require a positive displacement pump instead of a centrifugal pump. Similarly, high fluid temperatures can affect the materials used in the pump construction, so be sure to select a pump with components rated for your specific temperature range.
Solids handling and erosive/abrasive wear
If your application involves pumping liquids with suspended solids or abrasive particles, it’s essential to consider the pump’s ability to handle these materials. Magnetic drive pumps generally have limited solids handling capabilities compared to other pump types, such as direct drive pumps or external gear pumps. Abrasive particles can cause accelerated wear on pump components, particularly the impeller and bushings. In these cases, consider selecting a pump with wear-resistant materials, such as ceramic bearings or hardened stainless steel, to extend the pump’s service life and minimize maintenance requirements.
Chemical compatibility and corrosion resistance
Chemical compatibility is a critical factor when selecting a magnetic drive pump for handling aggressive acids, caustics, or solvents. Ensure that the pump materials, including the housing, impeller, and bushings, are compatible with the fluid being pumped. Many magnetic drive pumps are available with a variety of material options, such as stainless steel, Hastelloy, or PVDF (polyvinylidene fluoride), to provide excellent corrosion resistance.
NPSH and suction conditions
Net Positive Suction Head (NPSH) and suction conditions are crucial considerations when selecting a magnetic drive pump. NPSH refers to the minimum pressure required at the pump inlet to prevent cavitation, which can cause damage to the pump and reduce performance. Ensure that your system can provide sufficient NPSH to the pump, taking into account factors such as fluid temperature, viscosity, and suction line losses.
Power/torque limitations and magnet decoupling risk
Magnetic drive pumps rely on the magnetic coupling between the drive magnet and the impeller magnet to transfer power. This magnetic coupling has inherent power and torque limitations, which can lead to decoupling under overload conditions. When selecting a magnetic drive pump, consider the maximum torque requirements of your application and choose a pump with a sufficient safety margin to prevent decoupling. Some pumps feature advanced magnetic coupling designs, such as those with rare earth alloy magnets, which can provide increased torque transmission capabilities and reduce the risk of decoupling.
FAQs
Magnetic Drive vs. Canned Motor
Magnetic drive pumps use magnetic forces to rotate the impeller. Canned motor pumps have the motor and pump in a single sealed chamber.
Magnetic drive pumps are leak-free and require no seals. Canned motor pumps are compact and efficient.
Magnetic Drive vs. Mechanical Seal
Magnetic drive pumps use magnetic forces to rotate the impeller without direct contact. Mechanical seal pumps use a mechanical seal to prevent leaks around the rotating shaft.
Magnetic drive pumps are leak-free and require no seals. Mechanical seal pumps are more common and less expensive.
Magnetic Drive vs. Direct Drive
Magnetic drive pumps use magnetic forces to rotate the impeller without direct contact. Direct drive pumps have the impeller directly attached to the motor shaft.
Magnetic drive pumps are leak-free and require no seals. Direct drive pumps are compact and efficient. Magnetic drive pumps are suitable for high-temperature and high-pressure applications. Direct drive pumps are less expensive.
In Conclusion
Magnetic drive pumps offer numerous advantages over traditional mechanically sealed pumps. Their sealless design eliminates leaks, reduces maintenance, and improves safety. These pumps are ideal for handling hazardous, corrosive, or high-purity fluids.
To learn more about magnetic drive pumps and their applications, contact a reputable pump manufacturer today.