A mechanical seal is a critical component in rotating equipment that prevents fluid leakage and contains pressure. These seals are widely employed across various industries, including oil and gas, chemical processing, and water treatment, where they ensure the reliable and efficient operation of pumps, compressors, and other machinery.
The design and function of mechanical seals have evolved significantly over the years, with advancements in materials science and engineering leading to improved performance and longevity. In this blog post, we will delve into the intricacies of mechanical seals, exploring their fundamental principles, key components, and functions.
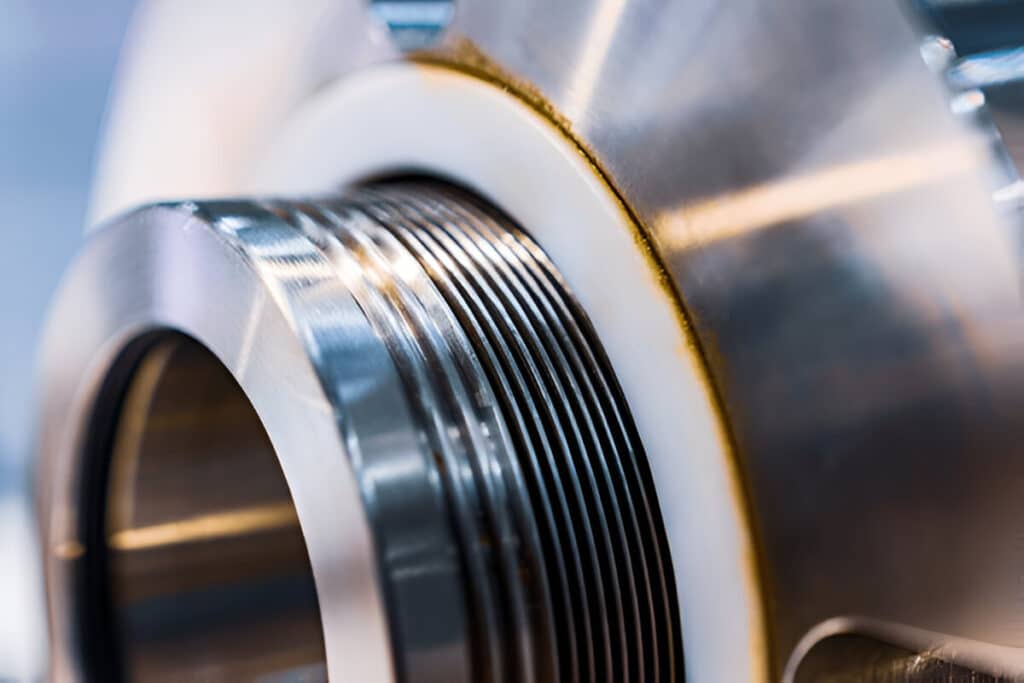
What Is a Mechanical Seal
A mechanical seal is a type of sealing device used to prevent leakage of fluids along rotating shafts, particularly in centrifugal pumps and other rotating equipment. It consists of two main components: a stationary seal ring mounted in the pump housing and a rotating seal ring attached to the shaft. These two rings form a sealing interface, creating a barrier between the process fluid and the atmosphere.
Mechanical seals serve as a superior alternative to traditional gland packing, offering better sealing performance and reduced maintenance requirements. They are designed to contain fluids within the pump while allowing the shaft to rotate freely, minimizing friction and wear. By effectively sealing the pump shaft, mechanical seals help prevent fluid leakage, which can lead to product loss, environmental contamination, and safety hazards.
The sealing action of a mechanical seal relies on the precise flatness and smoothness of the seal faces. The rotating and stationary seal faces are pressed together by a combination of hydraulic and spring forces, creating a thin fluid film between them. This fluid film acts as a barrier, preventing leakage while lubricating the seal faces to minimize wear and friction.
How Mechanical Seals Work
Mechanical seals are designed to contain fluid within a pump housing or vessel by creating a seal between the stationary and rotating parts of the equipment. The primary seal faces, consisting of a stationary seal ring and a rotating seal ring, are perpendicular to the shaft and form a sealing interface. These seal faces are pushed together by a combination of hydraulic forces from the sealed fluid and spring pressure from the seal’s spring mechanism.
The primary seal faces are typically made from hard, wear-resistant materials such as silicon carbide, tungsten carbide, or carbon graphite. These materials are precision-machined to create a flat, smooth sealing surface. As the shaft rotates, a thin film of fluid is drawn between the seal faces, lubricating them and preventing direct contact. This fluid film, along with the hydraulic and spring forces, helps maintain the seal’s integrity and prevents leakage.
Secondary seals, such as O-rings, wedge seals, or elastomeric bellows, are used to seal between the stationary and rotating components of the mechanical seal assembly. These secondary seals prevent leakage between the seal faces and the pump housing or shaft sleeve. They also accommodate minor shaft movements and misalignments, ensuring that the primary seal faces remain in proper contact.
In some mechanical seal designs, such as double seals or tandem seals, additional seals are used to provide enhanced leakage protection or to seal a barrier fluid. The barrier fluid, which is typically clean and compatible with the process fluid, is maintained at a higher pressure than the process fluid to prevent contamination and provide lubrication to the sealing faces.
Components of Mechanical Seals
Mechanical seals consist of several key components that work together to provide effective sealing and prevent leakage. These components include:
- Primary Seal Faces: The primary seal faces are the heart of a mechanical seal. Made from materials such as silicon carbide, tungsten carbide, or carbon graphite, these precision-lapped surfaces create a dynamic sealing interface that prevents fluid from escaping along the rotating shaft. The stationary face is typically mounted in the gland or seal housing, while the rotating face is attached to the shaft or shaft sleeve.
- Secondary Seals: Secondary seals, also known as static seals, are responsible for sealing between stationary components and preventing leakage to the atmosphere. These seals can be made from elastomeric materials such as O-rings, V-rings, or PTFE wedges. In some designs, metal bellows or elastomeric bellows are used as secondary seals to accommodate shaft movements and provide additional sealing.
- Spring Mechanism: The spring mechanism applies a constant force to the primary seal faces, ensuring proper contact and sealing. This force is essential for maintaining the seal face gap and accommodating any shaft misalignment or axial shaft adjustments. Common spring types include coil springs, wave springs, and metal bellows.
- Support Hardware: Mechanical seals rely on various support components to function effectively. These include seal glands, retaining rings, drive collars, and anti-rotation pins. The seal gland provides a mounting surface for the stationary seal face and helps to align the seal components. Retaining rings and drive collars secure the rotating components to the shaft, while anti-rotation pins prevent unwanted seal face rotation.
Functions of Mechanical Seals
Primary Sealing Function
The primary function of a mechanical seal is to contain process fluid within the pump or equipment and prevent leakage along the rotating shaft. The primary seal faces create a dynamic sealing interface that maintains a thin fluid film between the stationary and rotating faces. This fluid film, generated by the pumping action and seal face geometry, prevents direct contact between the faces and minimizes wear while allowing for efficient sealing.
Shaft Sealing and Alignment
Mechanical seals provide effective sealing around rotating shafts, accommodating shaft speeds, and permitting limited shaft movement. The seal components, such as the secondary seals and spring mechanism, allow for some degree of shaft misalignment and axial shaft adjustment while maintaining a proper sealing environment.
Fluid Compatibility and Containment
Mechanical seals are designed to handle a wide range of fluids, including water, hydrocarbons, chemicals, and abrasive liquids. The seal face materials and secondary seals are selected based on their compatibility with the process fluid, ensuring optimal sealing performance and longevity.
Pressure and Temperature Management
Mechanical seals are capable of operating across a wide range of pressures and temperatures. The seal components, such as the primary seal faces, secondary seals, and support hardware, are designed to withstand the specific pressure and temperature requirements of the application. In high-pressure applications, balanced seal designs are often used to minimize the closing force on the seal faces, reducing wear and extending seal life.
Benefits of Using Mechanical Seals
Reduced Leakage Rates
One of the primary benefits of using mechanical seals is their ability to significantly reduce leakage rates compared to traditional packing methods. The dynamic sealing interface created by the primary seal faces minimizes fluid escape, ensuring efficient containment of the process fluid. This reduction in leakage not only improves the overall efficiency of the pumping system but also minimizes environmental impact and enhances safety in the workplace.
Lower Maintenance Costs
Mechanical seals offer lower maintenance costs compared to other sealing methods, such as gland packing. The precision-engineered components and advanced seal face materials used in mechanical seals result in longer service life and reduced wear, minimizing the need for frequent seal replacements. Additionally, the reduced leakage rates associated with mechanical seals help to prevent damage to bearings and other pump components, further reducing maintenance requirements and costs.
Increased Operational Efficiency
The use of mechanical seals contributes to increased operational efficiency in pumping systems. By maintaining a proper sealing environment and minimizing leakage, mechanical seals reduce power consumption and improve overall pump performance. The efficient sealing provided by mechanical seals also helps to prevent contamination of the process fluid, maintaining product quality and reducing the risk of process disruptions.
Longevity and Durability
Mechanical seals are designed for longevity and durability, offering extended service life in demanding applications. The high-quality materials used in seal construction, such as silicon carbide, tungsten carbide, and engineered plastics, provide excellent wear resistance and chemical compatibility. The robust design of mechanical seals, combined with proper installation and maintenance, ensures reliable sealing performance over an extended period, reducing downtime and replacement costs.
Types of Mechanical Seals
Single Seals
Single mechanical seals, also known as component seals, consist of a single set of seal faces that provide a dynamic sealing interface between the rotating shaft and the stationary housing. These seals are typically used in applications with clean, non-abrasive fluids and moderate temperature and pressure conditions.
Single seals can be either balanced or unbalanced, depending on the pressure distribution across the seal faces. Balanced seals have equal pressure on both sides of the seal faces, reducing wear and extending seal life. Unbalanced seals have higher pressure on one side, which can lead to increased wear and shorter seal life.
Double Seals
Double mechanical seals feature two sets of seal faces, providing an additional layer of protection against leakage. The space between the two sets of seal faces is filled with a barrier fluid, which can be either a liquid or a gas. The barrier fluid serves to lubricate and cool the seal faces, as well as to prevent process fluid from entering the atmosphere.
Double seals are commonly used in applications with hazardous, toxic, or expensive fluids, where leakage must be minimized. They can also be used in high-pressure or high-temperature applications, where a single seal may not provide adequate sealing performance.
Pusher Vs. Non-pusher Seals
Pusher seals, also known as conventional seals, use a spring mechanism to maintain contact between the seal faces. The spring pushes the rotating seal face against the stationary seal face, ensuring a tight seal. Pusher seals are widely used due to their simplicity and cost-effectiveness.
Non-pusher seals, such as bellows seals and metal bellows seals, use a flexible element to maintain contact between the seal faces. The flexible element, typically made of elastomeric or metallic materials, acts as both a spring and a secondary seal. Non-pusher seals offer better performance in applications with high shaft runout or misalignment, as the flexible element can accommodate these irregularities.
Cartridge Seals
Cartridge seals are pre-assembled units that combine all the components of a mechanical seal into a single, easy-to-install package. They consist of the seal faces, secondary seals, spring mechanism, and support hardware, all housed within a single assembly.
Cartridge seals offer several advantages over component seals, including easier installation, improved reliability, and reduced maintenance costs. They are particularly useful in applications where frequent seal replacement is required, as they can be quickly and easily installed without the need for specialized tools or expertise.
Split Seals
Split seals are designed to be installed around a shaft without the need for complete disassembly of the equipment. They consist of two or more parts that can be assembled around the shaft, making them ideal for applications where seal replacement must be performed quickly and with minimal downtime.
Split seals are commonly used in large, expensive equipment such as pumps, compressors, and agitators, where complete disassembly would be time-consuming and costly. They are also useful in applications where the equipment cannot be easily moved or accessed, such as in underground or offshore installations.
Applications of Mechanical Seals
Oil and Gas
In the oil and gas industry, mechanical seals are used in pumps and compressors handling hydrocarbons, drilling fluids, and other process media. These seals are designed to withstand high pressures, temperatures, and abrasive conditions commonly encountered in this sector. Specialized mechanical seals, such as API 682 seals, are engineered to meet the stringent requirements of the petroleum industry.
Chemical Processing
Chemical processing plants rely on mechanical seals to contain and prevent leakage of various chemicals, solvents, and reagents. These seals must be compatible with the process fluids and resist corrosion, erosion, and chemical attack. Dual mechanical seals with barrier fluids are often employed to provide an extra layer of protection against leakage and ensure compliance with environmental regulations.
Water Treatment
In water treatment applications, mechanical seals play a crucial role in sealing pumps and other equipment handling water, wastewater, and various treatment chemicals. These seals must be able to withstand exposure to chlorine, acids, and other corrosive substances while preventing contamination of the water supply. Cartridge seals are commonly used in this industry for their ease of installation and maintenance.
Food and Beverage
The food and beverage industry requires mechanical seals that meet strict hygiene and sanitation standards. These seals must be designed to prevent bacterial growth, withstand frequent cleaning and sterilization cycles, and maintain the purity of the product. Single and double mechanical seals made from FDA-approved materials, such as stainless steel and special elastomers, are widely used in this sector to ensure product safety and compliance with regulations.