Mechanical seals are essential components in various industrial applications, particularly in equipment involving rotating shafts, such as pumps, mixers, and compressors. These seals prevent leakage of liquids and gases, ensuring optimal performance and safety. In this article, we will discuss the main components of a mechanical seal and their functions.
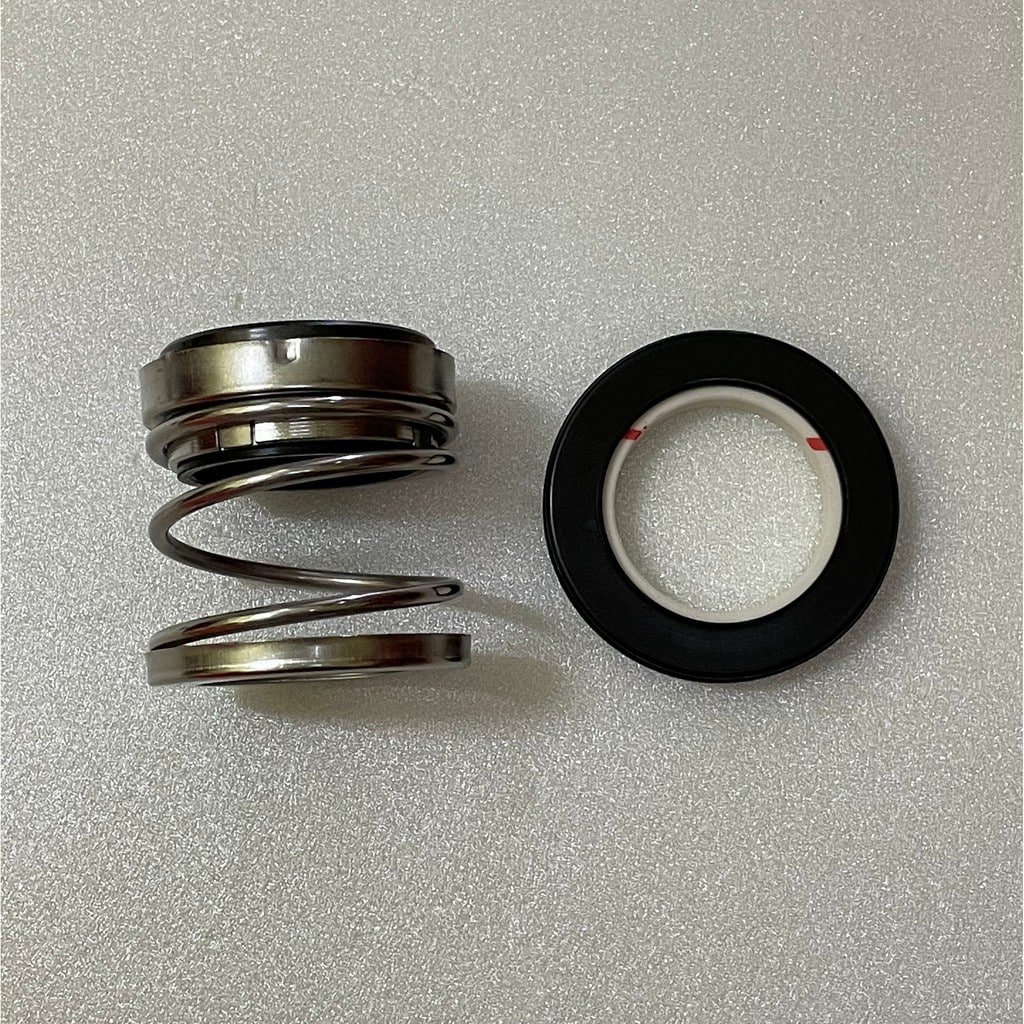
Rotating Primary Face
The rotating primary face, also known as the mating ring, is a critical component of a mechanical seal. It is typically made of hard, wear-resistant materials such as silicon carbide, tungsten carbide, or ceramic.
The rotating primary face is attached to the shaft and rotates with it, creating a seal against the stationary primary face.
Stationary Primary Face
The stationary primary face, also referred to as the primary ring or seal ring, is the counterpart to the rotating primary face. It is usually made of the same material as the rotating face to ensure optimal sealing performance.
The stationary primary face is mounted in the seal gland or housing and remains fixed during operation. The contact between the stationary and rotating primary faces creates the primary sealing surface, preventing fluid leakage.
Mechanical Loading Devices
Mechanical loading devices, such as springs, bellows, or diaphragms, play a vital role in maintaining constant contact between the primary sealing surfaces.
These devices apply a controlled force to the stationary primary face, ensuring that it remains in close contact with the rotating primary face. The loading device compensates for any wear, thermal expansion, or shaft misalignment, maintaining a consistent seal throughout the equipment’s operation.
Static and/or Dynamic Secondary Seals
Secondary seals, which can be static or dynamic, are responsible for preventing leakage between the stationary components of the mechanical seal and the equipment housing.
Static secondary seals, such as O-rings or gaskets, create a seal between non-moving parts. Dynamic secondary seals, like V-rings or U-cups, seal between the rotating and stationary components of the seal assembly.
Secondary seals are typically made of elastomeric materials, such as nitrile, fluorocarbon, or perfluoroelastomer, depending on the application requirements.
Drive Mechanisms
Drive mechanisms, such as pins, lugs, or set screws, transmit rotational motion from the shaft to the rotating components of the mechanical seal. These mechanisms ensure that the rotating primary face remains in sync with the shaft’s rotation. The drive mechanism must be designed to accommodate any shaft deflection or axial movement while maintaining proper alignment between the rotating and stationary seal components.