Carbon seals are specialized mechanical components designed to prevent leakage and maintain pressure in rotating equipment. These seals are constructed from carbon materials, which exhibit excellent wear resistance, thermal stability, and chemical inertness.
The unique properties of carbon make it an ideal choice for sealing applications in various industries, including oil and gas, petrochemical, and power generation. In this blog post, we will delve into the intricacies of carbon seals, exploring their design, functionality, and applications in the machinery industry.
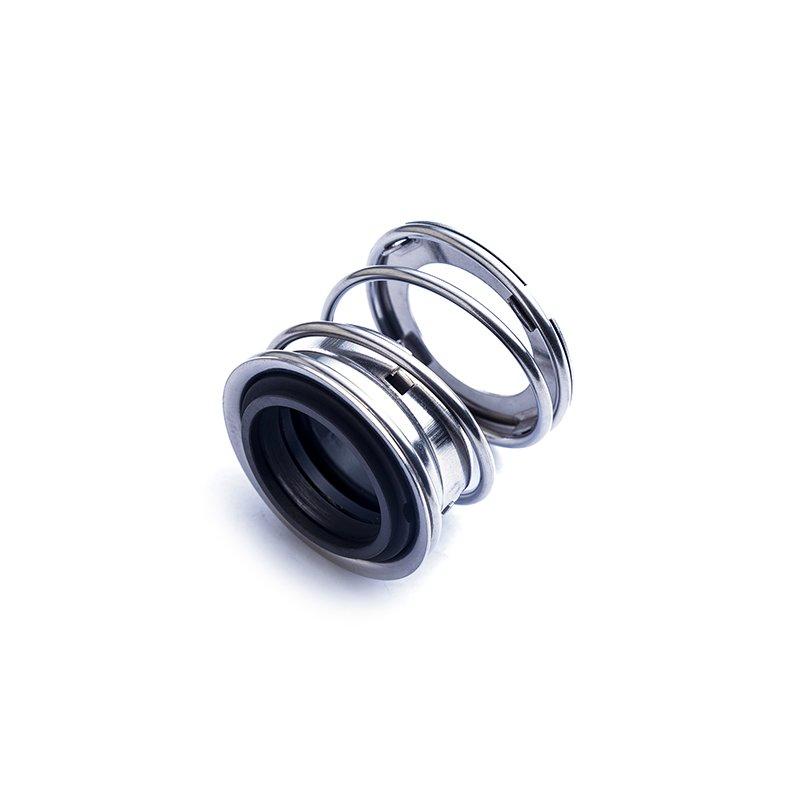
What Is a Carbon Seal
A carbon seal is a specialized sealing device designed to prevent fluid leakage and maintain system integrity in various industrial applications. These seals are constructed from high-quality carbon materials, such as graphite or carbon-graphite composites, which possess unique properties that make them suitable for demanding sealing environments.
Carbon seals are known for their excellent chemical resistance, allowing them to withstand exposure to a wide range of aggressive fluids and chemicals. They also exhibit exceptional temperature stability, enabling them to operate effectively in both high and low-temperature conditions. These properties make carbon seals a reliable choice for industries such as chemical processing, oil and gas, pharmaceuticals, and food and beverage production.
How Carbon Seals Work
The working principle of carbon seals relies on the creation of a tight, low-friction seal between two surfaces. When installed, the carbon seal is positioned between a stationary and a rotating component, such as a pump shaft and housing. As the rotating component moves, the carbon seal maintains contact with the stationary surface, preventing fluid from escaping the system.
The sealing action of carbon seals is achieved through a combination of factors. First, the carbon material’s inherent self-lubricating properties allow for smooth, low-friction operation, reducing wear and tear on the sealing surfaces. Second, the carbon seal’s precise manufacturing process ensures a close fit between the seal and the mating surfaces, minimizing leakage paths.
Additionally, carbon seals often incorporate a spring-loaded mechanism that maintains a constant sealing force against the mating surface. This feature compensates for any wear or dimensional changes that may occur over time, ensuring a consistent and reliable seal throughout the seal’s service life.
Benefits of Carbon Seals
- Chemical Resistance and Compatibility: Carbon seals exhibit exceptional chemical resistance, making them suitable for use with a wide range of fluids, including aggressive chemicals, solvents, and hydrocarbons. This compatibility ensures reliable sealing performance and minimizes the risk of seal degradation or failure due to chemical exposure.
- Temperature Stability and Performance in Extreme Conditions: Carbon seals maintain their sealing properties across a broad temperature range, from cryogenic temperatures to high-heat environments. This temperature stability enables their use in demanding applications where seals are subjected to extreme cold or heat, ensuring consistent performance and reliability.
- Low Friction Characteristics Leading to Energy Efficiency: The inherent low friction properties of carbon materials result in reduced frictional losses during operation. This translates to improved energy efficiency, as less power is required to overcome seal friction. Lower friction also contributes to reduced heat generation, which can extend the life of the seal and surrounding components.
- Durability and Reduced Maintenance Needs: Carbon seals are known for their durability and long service life. The high strength and wear resistance of carbon materials enable these seals to withstand harsh operating conditions and maintain their sealing integrity over extended periods. This durability reduces the frequency of seal replacements and associated maintenance costs, resulting in improved equipment uptime and overall operational efficiency.
Comparison with Traditional Sealing Solutions
Carbon Seals vs. Mechanical Seals
Carbon seals offer several advantages over traditional mechanical seals. Mechanical seals rely on the contact between two flat surfaces, typically made of materials like ceramics or tungsten carbide, to create a seal. While effective in many applications, mechanical seals are prone to wear and tear due to friction, reducing their lifespan and increasing maintenance requirements. In contrast, carbon seals utilize the unique properties of carbon materials to provide a more robust and reliable sealing solution.
Carbon Seals vs. Elastomeric Seals
Elastomeric seals, such as O-rings and gaskets made from rubber or synthetic polymers, are another common type of sealing solution. These seals are known for their flexibility and ability to conform to irregular surfaces. However, elastomeric seals have limitations in terms of chemical compatibility and temperature resistance. Exposure to aggressive chemicals or extreme temperatures can cause elastomeric seals to degrade, leading to leakage and failure. Carbon seals, on the other hand, exhibit exceptional chemical resistance and can withstand a wide range of temperatures, making them suitable for demanding industrial applications.
Carbon Seals vs. Packing Seals
Packing seals, made from materials like graphite or PTFE, are often used in rotating equipment to prevent leakage around shafts. While packing seals can be effective in certain applications, they have several drawbacks compared to carbon seals. Packing seals require frequent adjustment and replacement to maintain proper sealing, leading to increased maintenance costs and downtime. Additionally, packing seals are prone to leakage, especially under high pressure or temperature conditions. Carbon seals provide a more reliable and long-lasting solution, reducing the need for frequent maintenance and minimizing the risk of leakage.
Applications of Carbon Seals
- Chemical Processing: In the chemical industry, carbon seals are extensively used to handle aggressive fluids, solvents, and reagents. Their chemical resistance and compatibility ensure reliable sealing performance, preventing leakage and contamination of process fluids.
- Oil and Gas: Carbon seals find application in various oil and gas industry equipment, such as pumps, compressors, and valves. They provide effective sealing solutions for handling hydrocarbons, drilling fluids, and other media encountered in upstream and downstream operations.
- Water Treatment: In water treatment plants, carbon seals are employed in pumps, mixers, and other equipment to prevent leakage and ensure the integrity of the treatment process. Their chemical resistance and low friction characteristics contribute to efficient and reliable operation.
- Pharmaceuticals: The pharmaceutical industry relies on carbon seals for critical applications where contamination prevention and product purity are paramount. Carbon seals’ chemical compatibility and ability to withstand sterilization processes make them suitable for use in pharmaceutical manufacturing equipment.
- Food and Beverage: Carbon seals are utilized in food and beverage processing equipment, such as pumps, mixers, and filling machines. Their chemical resistance, temperature stability, and low friction properties ensure hygienic and efficient operation, meeting stringent food safety standards.