Pulsating flow plagues many industrial processes, causing equipment damage, reduced efficiency, and suboptimal performance. Left unchecked, these destructive pulsations wreak havoc on piping systems, pumps, and other critical components. Pulsation dampeners offer a robust solution to mitigate these harmful effects, smoothing out flow fluctuations to protect equipment and optimize processes.
In this comprehensive guide, we’ll dive deep into pulsation dampeners, exploring their functions, working principles, key components, and various types. We’ll also clarify when to deploy pulsation dampeners and how they differ from accumulators. Finally, we’ll address common questions about the gas used in these devices, their pulsation elimination capabilities, and the importance of proper pre-charge pressure.
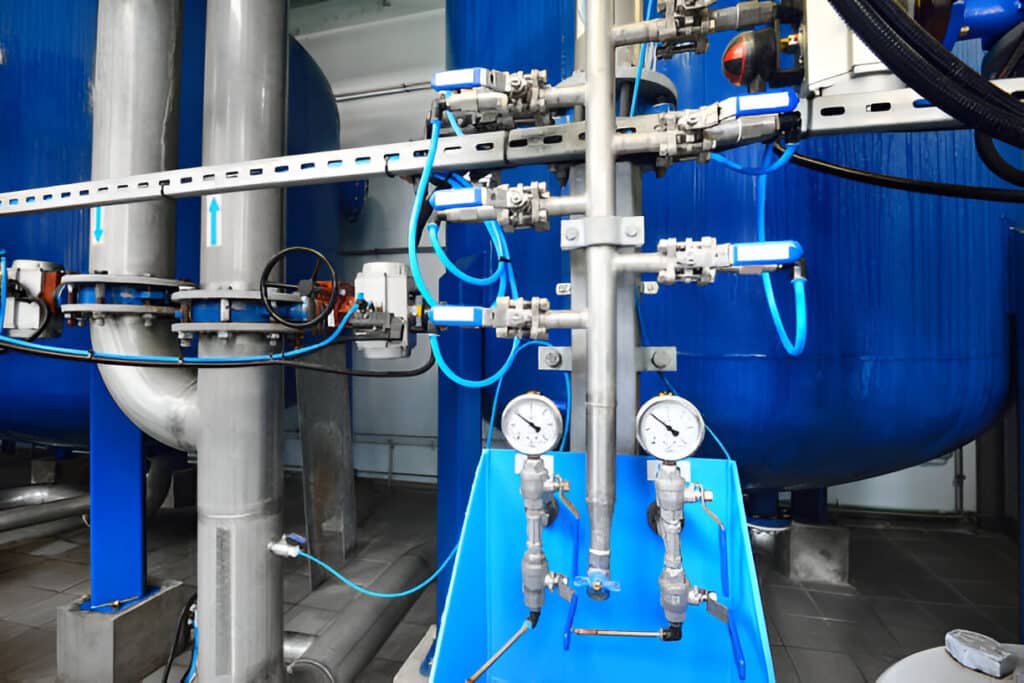
What is a Pulsation Dampener
A pulsation dampener, also known as a pulsation damper or pulsation attenuator, is a mechanical device designed to reduce pressure fluctuations and vibrations in fluid systems. These devices are commonly used in hydraulic and pneumatic applications to smooth out pressure spikes and minimize the transmission of pulsations through piping networks.
Pulsation dampeners work by absorbing and dissipating the energy of pressure waves, thereby reducing their amplitude and frequency. They typically consist of a gas-charged chamber separated from the fluid system by a flexible barrier, such as a bladder, diaphragm, or piston. As pressure fluctuations enter the dampener, the gas chamber compresses and expands, acting as a spring to absorb and dampen the pulsations.
Functions of Pulsation Dampeners
- Reducing pressure pulsations: Pulsation dampeners absorb sudden pressure spikes and fluctuations, minimizing their impact on the system and connected equipment.
- Stabilizing flow rate: By evening out flow irregularities, pulsation dampeners help maintain a consistent and steady flow of fluid or gas through the system.
- Protecting system components: Pulsation dampeners help protect pipes, valves, fittings, and other system components from the damaging effects of pressure surges and vibrations.
- Improving system efficiency: By reducing pressure fluctuations and stabilizing flow, pulsation dampeners can improve overall system efficiency and performance.
- Enhancing process control: Pulsation dampeners contribute to better process control by maintaining more consistent pressure and flow conditions.
- Reducing noise and vibration: By absorbing pressure spikes and flow oscillations, pulsation dampeners can significantly reduce noise and vibration in the system.
How Pulsation Dampeners Work
Pulsation dampeners are designed to reduce pressure spikes and flow fluctuations in fluid systems. They work by absorbing the kinetic energy of the pulsating fluid and releasing it back into the system at a steady rate. This process helps to smooth out the flow and pressure, reducing vibration, noise, and potential damage to system components.
The basic operating principle of a pulsation dampener involves a pressure vessel divided into two chambers by a flexible bladder, diaphragm, or piston. One chamber is connected to the fluid system and is filled with the process liquid. The other chamber contains a compressed gas, typically nitrogen or air.
When a pressure pulse occurs in the fluid system, the process liquid is forced into the dampener’s fluid chamber, causing the gas in the other chamber to compress. This compression absorbs the energy of the pressure pulse, reducing its amplitude. As the pressure pulse subsides, the compressed gas expands, pushing the process liquid back into the system at a controlled rate. This action evens out the pressure fluctuations, resulting in a steadier flow downstream of the dampener.
Components of Pulsation Dampeners
- Pressure Vessel: The main body of the pulsation dampener, designed to withstand the system pressure and contain the dampening media.requirements.
- Dampening Media: The compressible material inside the pressure vessel that absorbs and dissipates pressure pulsations. Common dampening media include compressed gas (such as nitrogen or air), elastomeric bladders, or flexible diaphragms.
- Inlet and Outlet Ports: The connections that allow the pulsation dampener to be integrated into the fluid system.
- Charging Valve (for gas-charged models): A valve used to introduce and maintain the desired pre-charge pressure in the dampening media.
- Bladder or Diaphragm (for bladder and diaphragm types): A flexible barrier that separates the system fluid from the dampening media.
- Anti-Extrusion Plate (for bladder types): A perforated metal plate that supports the bladder and prevents it from extruding into the inlet and outlet ports under high-pressure conditions.
- Mounting Hardware: Components such as brackets, flanges, or feet that enable the pulsation dampener to be securely installed in the fluid system.
Types of Pulsation Dampeners
Bladder Type
Bladder-type pulsation dampeners feature an elastomeric bladder that serves as a flexible barrier between the system fluid and the gas charge. The bladder is typically made from materials such as Buna-N, Neoprene, or EPDM, chosen for their compatibility with the system fluid and their ability to withstand repeated flexing.
As pressure pulsations enter the dampener, the bladder expands and contracts, absorbing the energy and smoothing out the flow. The gas charge, which is maintained at a pre-determined pressure, provides the necessary resistance to the bladder’s movement, enabling effective dampening.
Diaphragm Type
Diaphragm-type pulsation dampeners use a flexible diaphragm, typically made from materials such as PTFE or Viton, to separate the system fluid from the gas charge. The diaphragm is supported by a perforated metal plate or screen, which prevents excessive deformation under pressure.
Similar to bladder-type dampeners, the diaphragm flexes in response to pressure pulsations, absorbing the energy and attenuating the fluctuations. The gas charge provides the necessary resistance to the diaphragm’s movement, ensuring effective dampening performance.
However, diaphragm-type dampeners may have lower dampening efficiency compared to bladder types, and the diaphragm may be more susceptible to fatigue and wear over time.
Hydropneumatic (Flow-Through) Type
Hydropneumatic, or flow-through, pulsation dampeners do not utilize a physical barrier between the system fluid and the gas charge. Instead, they rely on the direct interaction between the fluid and the gas to achieve dampening.
In this design, the system fluid enters the dampener and comes into direct contact with the gas charge. As pressure pulsations propagate through the fluid, the gas compresses and expands, absorbing the energy and smoothing out the flow. The dampened fluid then exits the device and continues through the system.
However, hydropneumatic dampeners may have limitations in terms of dampening efficiency, particularly in low-pressure applications. Additionally, the direct contact between the fluid and gas may lead to gas absorption or the formation of foam in some cases.
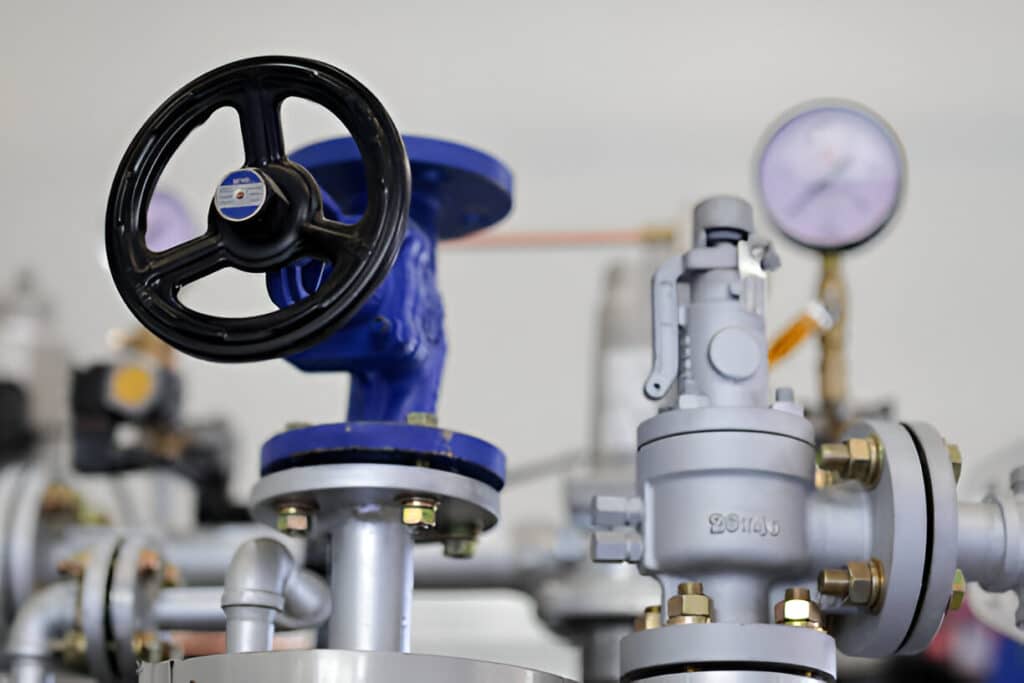
When to Use Pulsation Dampeners
- Positive displacement pumps: Piston, plunger, and diaphragm pumps create significant pressure pulsations due to their reciprocating action. Installing a pulsation dampener near the pump discharge helps smooth out these pulsations.
- Protecting sensitive equipment: Pressure spikes and vibrations can damage delicate instruments, meters, and control valves. Placing a pulsation dampener upstream of such components helps shield them from harmful pulsations.
- Improving flow meter accuracy: Pulsating flow can cause errors in flow measurement devices like turbine or paddle wheel meters. A pulsation dampener installed upstream of the meter will even out the flow, enhancing measurement precision.
- Extending equipment life: The cyclic stresses from pressure pulsations can lead to premature failure of pipes, fittings, and other system components. Pulsation dampeners help mitigate these stresses, prolonging the service life of the system.
- Ensuring consistent process conditions: In applications like chemical dosing or mixing, pulsations can cause uneven distribution or incomplete reactions. Dampeners provide steadier flow for improved process consistency and quality.
- Reducing noise and vibration: Pressure pulsations often lead to undesirable noise and vibration in the piping system. Pulsation dampeners are effective at attenuating these issues, creating a quieter and more stable operating environment.
Difference Between Accumulators and Pulsation Dampeners
While accumulators and pulsation dampeners are sometimes used interchangeably, they serve distinct primary functions in hydraulic systems:
Accumulators:
- The main purpose is energy storage. They store hydraulic energy in the form of pressurized gas, which can be used to supplement pump flow during peak demand periods or to support the system if the pump fails.
- Helps maintain a set system pressure, making up for leakage or thermal expansion/contraction of the oil.
- Absorbs pressure surges and sudden fluid demands, reducing shocks in the system.
- Accumulators have significantly larger gas and fluid volumes compared to pulsation dampeners.
Pulsation Dampeners:
- Designed specifically to reduce pressure pulsations and vibrations in the system. They do not provide significant energy storage capacity.
- Contains a relatively small volume of gas and fluid, just enough to dampen pulsations effectively.
- Responds rapidly to pressure spikes, making them better suited for high-frequency pulsations like those from reciprocating pumps.
- Multiple pulsation dampeners may be used at various points in a system, whereas accumulators are typically installed near the power unit.
FAQs
What gas is in pulsation dampeners?
Nitrogen is the most common gas used in pulsation dampeners. It is an inert gas that provides a compressible cushion to absorb pressure pulsations. The nitrogen is separated from the pumped fluid by a bladder or diaphragm inside the dampener.
Can a pulsation dampener eliminate all pulsations?
While pulsation dampeners can significantly reduce pulsations, they cannot completely eliminate them. Dampeners are designed to attenuate pulsations to an acceptable level, typically reducing peak-to-peak amplitudes by 80-90%.
What happens if the pre-charge pressure is too high or too low?
- If pre-charge is too high, the gas volume is too small to effectively absorb pulsations. This leads to higher residual pulsations downstream.
- If pre-charge is too low, the bladder or diaphragm can bottom out during operation, causing dampener failure and even higher pulsations.
Pre-charge should be set at 80-90% of minimum system pressure for best results.