Have you ever wondered how water is pumped to high elevations or pressures? The answer lies in multistage pumps.
A multistage pump is a type of pump that uses multiple impellers to increase the pressure of a fluid. By arranging these impellers in series, the pump can achieve higher discharge pressures than single-stage pumps.
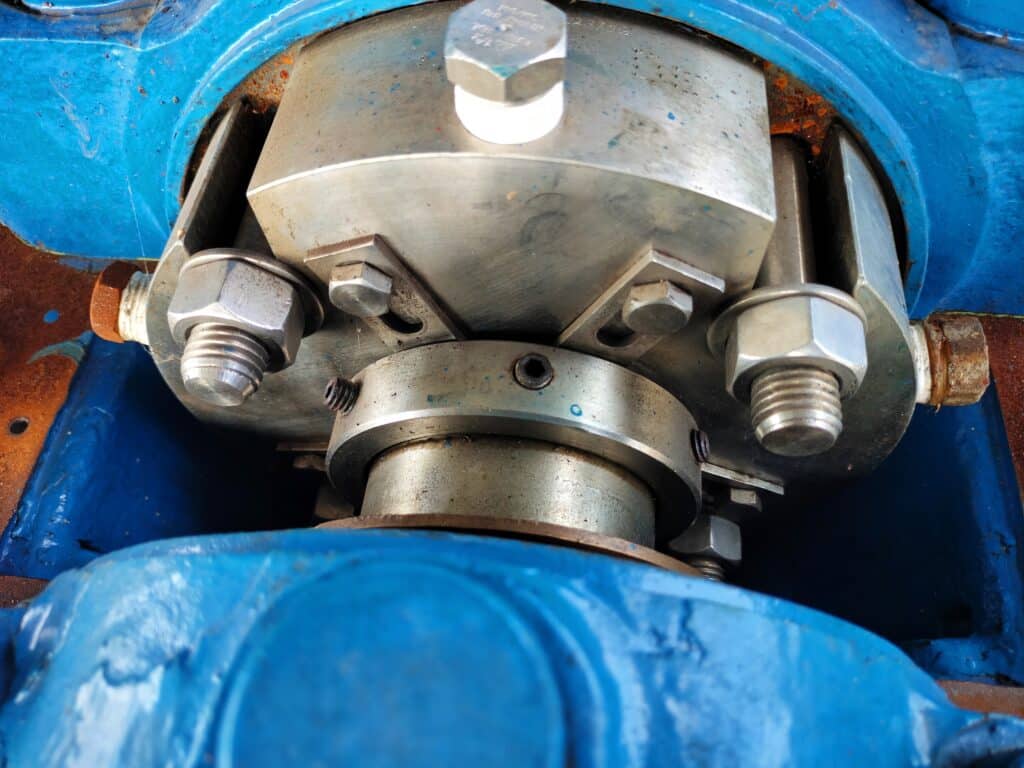
What is a Multistage Pump
A multistage pump is a type of pump that consists of multiple impellers arranged in series on a single shaft, allowing for higher discharge pressures and a wider range of flow rates compared to single-stage pumps. The fluid flows through each impeller stage, increasing in pressure with each pass, making multistage pumps ideal for applications requiring elevated pressures, such as in high-rise buildings, boiler feed water, and municipal water supply systems.
The modular design of multistage pumps allows for flexibility in meeting specific discharge pressure requirements by adding or removing stages, while maintaining a compact footprint. With their ability to handle a wide range of flow rates and pressures, multistage pumps are a versatile and efficient choice for numerous applications, including domestic water supply, industrial processes, and pressure cleaning.
How Multistage Pumps Work
Multistage pumps consist of multiple impellers arranged in series on a single shaft, allowing them to generate higher discharge pressures compared to single-stage pumps. As the fluid flows through each stage, the pressure and head increase incrementally.
The impellers are housed within individual stage casings, which guide the fluid from one stage to the next. This design enables multistage pumps to achieve a wide range of flow rates and discharge pressures while maintaining a compact footprint.
This process repeats through each subsequent stage, with each impeller adding more energy to the fluid. The number of stages determines the final discharge pressure.
Components of Multistage Pumps
- Pump Casing: Houses multiple impellers mounted on a single shaft, with each impeller representing a separate stage.
- Diffuser Casings: Guide the fluid from one impeller to the next, gradually increasing the pressure between stages.
- Shaft: Supported by bearings, sized to handle the thrust generated by the multiple stages.
- Suction Inlet: Located at the first stage of the pump.
- Discharge Outlet: Connects to the final stage.
- Intermediate Bearings: Used in some designs for additional support.
- Special Impeller Designs: Enhance performance for specific applications.
- Cooling Arrangements: For the motor, included in some designs.
Advantages of Multistage Pumps
- Ability to generate very high pressures in a compact size: Multistage pumps achieve elevated discharge pressures by adding stages, suitable for applications like pressure cleaning and high-rise buildings.
- Improved efficiency compared to single-stage pumps: Their design allows for higher energy efficiency, resulting in energy savings and lower operating costs.
- Lower speed and noise operation: Multistage pumps operate at lower speeds while maintaining required flow rate and pressure, reducing noise levels and vibrations.
- Smaller motor size for the same pressure: They require smaller motor horsepower compared to single-stage pumps for the same head and flow conditions, making them more compact and cost-effective.
- Space savings with vertical designs: Vertical multistage pumps, like the Vertical Turbine type, have a smaller footprint, ideal for applications with limited floor space, such as multi-story buildings.
Disadvantages of Multistage Pumps
- Higher Initial Cost: More complex design and additional components increase the cost compared to single-stage pumps.
- Increased Maintenance: More parts, such as multiple impellers, bearings, and seals, can wear out or fail.
- Reduced Efficiency at Lower Flow Rates: The pump may not operate optimally when demand is low.
- Increased Noise and vibration: Multiple stages and higher operating speeds can cause more noise and vibration.
- Limited Flexibility: Designed for a specific range of operating conditions, limiting flow rate and pressure adjustments.
- Larger Footprint: Requires more space compared to single-stage pumps, a concern for applications with limited floor space.
- Higher Risk of Cavitation: Improper sizing or operation can lead to cavitation and pump damage.
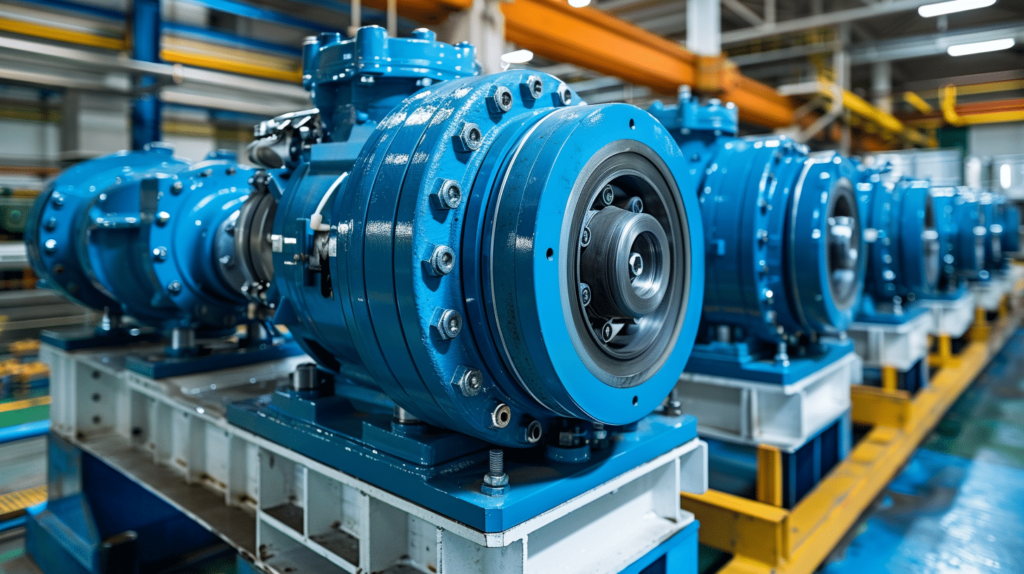
Types of Multistage Pumps
Horizontal Multistage Centrifugal Pumps
Horizontal multistage centrifugal pumps are designed to deliver high discharge pressures by utilizing multiple impellers mounted on a single shaft. These pumps are ideal for applications requiring elevated pressure, such as booster systems, pressure cleaning, and high-rise buildings.
Vertical Multistage Centrifugal Pumps
Vertical multistage centrifugal pumps are designed to deliver high discharge pressures while occupying minimal floor space. They consist of multiple impellers mounted on a single shaft, with each impeller housed in a separate stage casing.
The vertical orientation of these pumps enables them to generate high head pressures while maintaining a relatively small footprint. By stacking multiple stages, the pump can achieve the desired discharge pressure without the need for a larger impeller or motor.
Submersible Multistage Pumps
Submersible multistage pumps are designed to operate while fully submerged in the pumped fluid. These pumps are ideal for applications where the fluid level is below the surface, such as in wells, boreholes, or tanks.
The submersible design eliminates the need for priming and allows for a more compact installation. They are equipped with a submersible electric motor that is directly coupled to the pump, ensuring efficient power transmission.
Applications and Industries
- Water Supply Systems: Used in municipal water supply to maintain steady pressure and flow throughout distribution networks.
- High-Rise Buildings: Essential for delivering water to upper floors, ensuring adequate pressure and flow at all levels.
- Industrial Processes: Used in boiler feed systems for high-pressure water in steam generation. Applied in the chemical, pharmaceutical, and food industries for fluid transfer and pressure boosting.
- Irrigation Systems: Provide necessary pressure for efficient water distribution.
- Fire Suppression: Critical in fire suppression systems for reliable pressure and flow.
- Water Treatment Plants: Used for various processes in water treatment to ensure efficient operation.
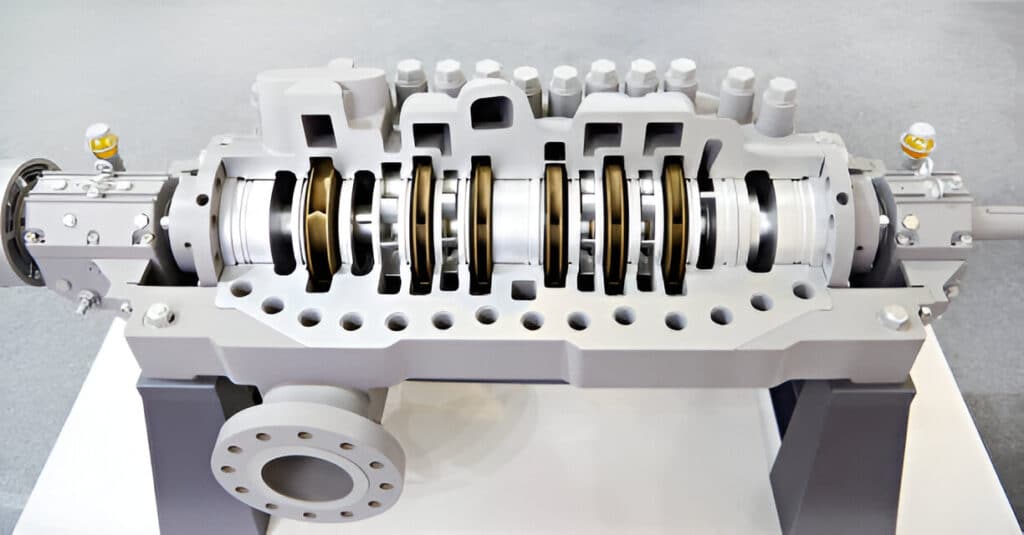
How to Select a Multistage Pump
Determining Pressure and Flow Requirements
Accurately assess the system’s pressure and flow needs. Match the pump’s capabilities to these requirements for optimal performance.
Evaluating NPSH and Suction Conditions
Calculate the Net Positive Suction Head (NPSH) available in the system. Ensure the chosen pump’s NPSH required is lower than the available NPSH.
Material Selection for the Application
Choose pump materials based on the fluid being pumped. Consider factors such as corrosiveness, temperature, and abrasiveness.
Choosing Between Horizontal and Vertical
Horizontal pumps often offer easier maintenance access. Vertical pumps may be preferable in limited floor space situations.
FAQs
What Is the Difference between Single Stage Pump and Multi Stage Pump
Single stage pumps have one impeller. Multi stage pumps have multiple impellers. Single stage pumps generate lower pressure. Multi stage pumps produce higher pressure. Single stage pumps are simpler. Multi stage pumps are more complex but more efficient.
What Is the Difference between a Jet Pump and a Multistage Pump
Jet pumps use fluid to create suction. Multistage pumps use multiple impellers. Jet pumps are better for shallow wells. Multistage pumps work well for deep wells. Jet pumps are simpler. Multistage pumps offer higher pressure and efficiency.
In Conclusion
In conclusion, multistage pumps are powerful and efficient pumping solutions for high-pressure applications. They offer numerous advantages over single-stage pumps, making them ideal for various industries and settings.
To learn more about multistage pumps and how they can benefit your specific application, contact a trusted pump supplier today.