What is API Plan 23
API Plan 23 is specifically designed for single seals with a fluid reservoir and a circulation device, such as a pumping ring or a throat bushing. The main purpose of this plan is to provide a cool and clean environment for the mechanical seal by continuously circulating the barrier fluid from the reservoir through the seal chamber and back to the reservoir.
How Does API Plan 23 Work
In an API Plan 23 system, cool, clean fluid is circulated from a seal pot or reservoir to the seal chamber. The seal pot is usually mounted above the pump so that the cooling fluid can flow to the seal chamber using gravity. This fluid is the same as the pumped process fluid.
The cooling fluid enters the seal chamber and flows around the mechanical seal. As it does this, it absorbs heat from the seal faces, keeping them at a safe operating temperature.
In addition to cooling the seal, the circulating fluid also helps to flush away any particles or contaminants that might be present in the seal chamber. This keeps the seal faces clean and prevents abrasive wear or clogging.
The heated fluid then flows back to the seal pot. In the seal pot, the hot fluid can cool down before it’s circulated back to the seal chamber again. This cooling often happens naturally as the fluid sits in the pot, but in some cases, cooling coils or other heat exchange devices might be used to speed up the process.
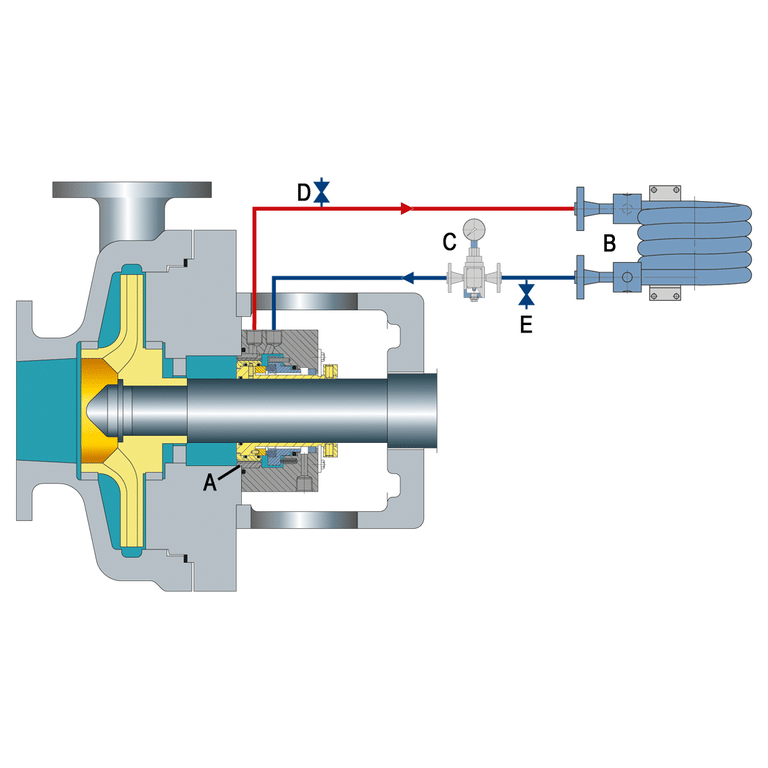
Design of API Plan 23
- Seal Chamber: This is where the mechanical seal is installed, designed to accommodate the seal and provide a suitable environment for its operation.
- Circulation Pump: Used to circulate the fluid through the system, the pump should be sized appropriately to maintain the required flow rate and pressure.
- Heat Exchanger: Employed to remove heat from the circulating fluid, it can be a shell and tube, plate, or fin-type heat exchanger, depending on the application and heat load.
- Piping and Instrumentation: Connects the seal chamber, circulation pump, and heat exchanger, designed to minimize pressure drops and ensure proper flow distribution. Instrumentation like pressure gauges, temperature sensors, and flow meters monitor the system’s performance.
- Fluid Reservoir: Required to store the circulating fluid and accommodate thermal expansion, it should be sized to hold enough fluid for the system’s operation and be equipped with a level indicator.
Advantages of API Plan 23
- Clean and Cool Environment: API Plan 23 provides a clean, cool environment for seal faces by continuously flushing the seal chamber with fluid from an external source, which prevents the buildup of heat and contaminants.
- Improved Reliability: By maintaining a clean and stable environment around the seal, Plan 23 significantly reduces the risk of failure due to contamination or overheating, leading to longer seal life and lower maintenance costs.
- Enhanced Monitoring: The flush fluid in Plan 23 can be easily sampled and analyzed for signs of seal wear or contamination, allowing for early detection of issues and proactive maintenance, thus preventing unexpected downtime.
Disadvantages of API Plan 23
- Increased Complexity: API Plan 23 involves additional piping, valves, and instrumentation, leading to higher initial installation costs and ongoing maintenance needs.
- Reliance on External Fluid Source: The dependency on an uninterrupted and uncontaminated flush fluid supply is crucial. Interruptions or contamination can adversely affect seal performance and durability.
- Compatibility Requirements: The introduction of an external flush fluid into the seal chamber necessitates careful consideration of compatibility between the flush fluid and the process fluid to prevent chemical reactions or contamination.
Applications
- Pumps
- Compressors
- Mixers and Agitators
- Turbines
- Reactors and Vessels
- Paper and Pulp Industry
- Marine Applications