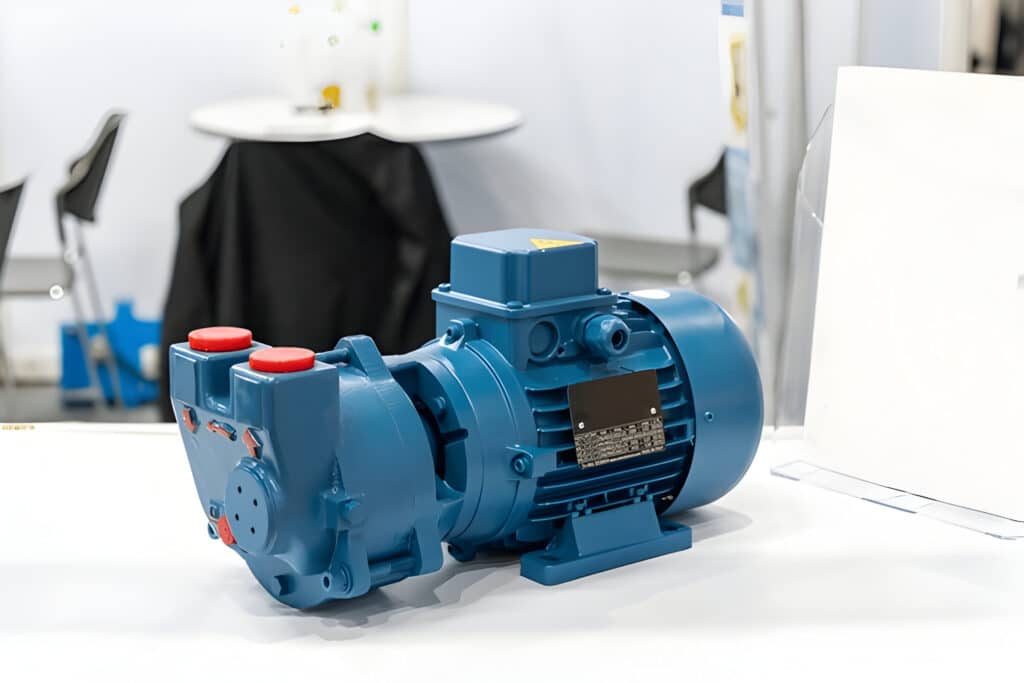
What is Pumping Ring
Pumping rings are components in mechanical seals that help circulate fluid between the seal faces. A mechanical seal prevents leakage by creating a seal between a rotating shaft and a stationary housing. The pumping ring creates a pumping action that circulates fluid across the seal faces, providing lubrication and cooling.
How do Pumping Rings Work
The pumping ring has angled grooves on its surface that act as small pumps. As the shaft rotates, these grooves pump fluid from the outside towards the seal faces. The fluid then flows across the seal faces, lubricating and cooling them.
What is the Purpose of the Pumping Ring
The primary purpose of a pumping ring is to create a closed-loop swirling flow of barrier fluid between the inboard and outboard seals in a dual seal cartridge. This circulation helps to:
- Cool the mechanical seals by transferring heat away from the seal faces.
- Lubricate the seal faces to reduce wear and friction.
- Maintain a higher pressure in the seal chamber than the process fluid, preventing contamination and extending seal life.
- Provide a means of circulating barrier fluid without the need for an external reservoir or pumping system.
Pumping Ring Types
There are three main types of pumping rings used in mechanical seals:
Radial flow impellers using drilled vanes
Radial flow impellers with drilled vanes are one of the most common types of pumping rings. They consist of a series of radial vanes or holes drilled into the impeller, which create a pressure differential as the impeller rotates. This pressure differential drives the barrier fluid from the high-pressure region near the outer diameter of the impeller to the low-pressure region near the inner diameter, creating a closed-loop circulation.
Radial flow impellers with drilled vanes are relatively simple to manufacture and can provide good flow rates and pressure head characteristics, making them suitable for a wide range of applications.
Radial flow using slots
Radial flow pumping rings using slots operate on a similar principle to those with drilled vanes but feature a series of radial slots or grooves machined into the impeller instead of holes. As the impeller rotates, the slots create a pressure differential that drives the barrier fluid from the outer diameter to the inner diameter, creating a closed-loop circulation.
Slotted radial flow pumping rings can offer improved flow characteristics compared to drilled vane designs, as the slots provide a more continuous flow path and reduce flow separation and turbulence. However, they may be more complex to manufacture and may not be suitable for all applications.
Axial flow using spiral grooves
Axial flow pumping rings using spiral grooves are designed to create a helical flow path for the barrier fluid as the impeller rotates. The spiral grooves are machined into the face of the impeller, and as the impeller rotates, the barrier fluid is pushed along the grooves from the outer diameter to the inner diameter, creating a closed-loop circulation.
Axial flow pumping rings with spiral grooves can provide excellent flow rates and pressure head characteristics, particularly at high rotational speeds. They are often used in applications where high flow rates and low pressure drops are required, such as in high-speed turbomachinery and compressors.
However, axial flow pumping rings may be more complex to design and manufacture than radial flow designs, and their performance can be more sensitive to changes in operating conditions and fluid properties.
Applications of Pumping Rings
API PLAN 23
API PLAN 23 covers the requirements for pumping rings used in mechanical seals for centrifugal pumps. It specifies the materials, dimensions, and manufacturing tolerances for pumping rings. The plan is applicable to pumping rings used in various industries, including oil and gas, chemical, and power generation.
API PLAN 52
API PLAN 52 provides guidelines for the design and testing of mechanical seals used in centrifugal and rotary pumps. It covers the requirements for pumping rings, including materials, dimensions, and testing procedures. The plan is widely used in the oil and gas industry.
API PLAN 53
API PLAN 53 is a standard for the design and testing of mechanical seals used in reciprocating pumps. It specifies the requirements for pumping rings, including materials, dimensions, and testing methods. This plan is commonly used in the oil and gas industry for reciprocating pumps.
Pumping Ring Performance
Flow Rate Requirements
One of the primary considerations in pumping ring performance is the required flow rate of the barrier fluid. The flow rate must be sufficient to maintain a stable fluid film between the seal faces, remove heat generated by friction, and prevent the ingress of process fluids.
Pumping Ring Performance Curves
Pumping ring performance is typically characterized by performance curves that plot the flow rate against the pressure head generated by the pumping ring at various rotational speeds.
Piping System Curves
The piping system curve represents the pressure drop across the piping, fittings, and other components in the circulation loop. The intersection of the pumping ring performance curve and the piping system curve determines the actual circulation rate of the barrier fluid in the system.
Factors Affecting Pumping Ring Performance
Several factors can influence the performance of pumping rings in mechanical seal applications.
Diameter and Speed
Larger diameters and higher rotational speeds generally result in increased flow rate capacity and pressure head.
Clearances and Porting
The clearances between the pumping ring and the stationary components, as well as the size and location of the inlet and outlet ports, significantly impact the pumping ring’s performance. Smaller clearances can increase the pressure head generated by the pumping ring but may also result in higher frictional losses and heat generation.
Fluid Properties
The properties of the barrier fluid, such as viscosity, density, and compressibility, play a crucial role in pumping ring performance. Higher viscosity fluids may require larger clearances and ports to maintain adequate flow rates, while lower viscosity fluids may enable smaller clearances and improved pressure-generating capabilities. The compatibility of the barrier fluid with the seal materials and the process fluid must also be considered to ensure reliable long-term operation.