In the world of machinery, understanding the differences between various types of equipment is paramount for optimal performance and efficiency. Plan 11 and Plan 13 are two distinct classifications that encompass a wide range of machinery, each with its own unique characteristics and applications.
This blog post will delve into the specifics of Plan 11 and Plan 13, exploring their functions, operations, and key differences. We will examine how these classifications impact factors such as pressure management, flow control, and monitoring and maintenance requirements, providing valuable insights for professionals in the field.
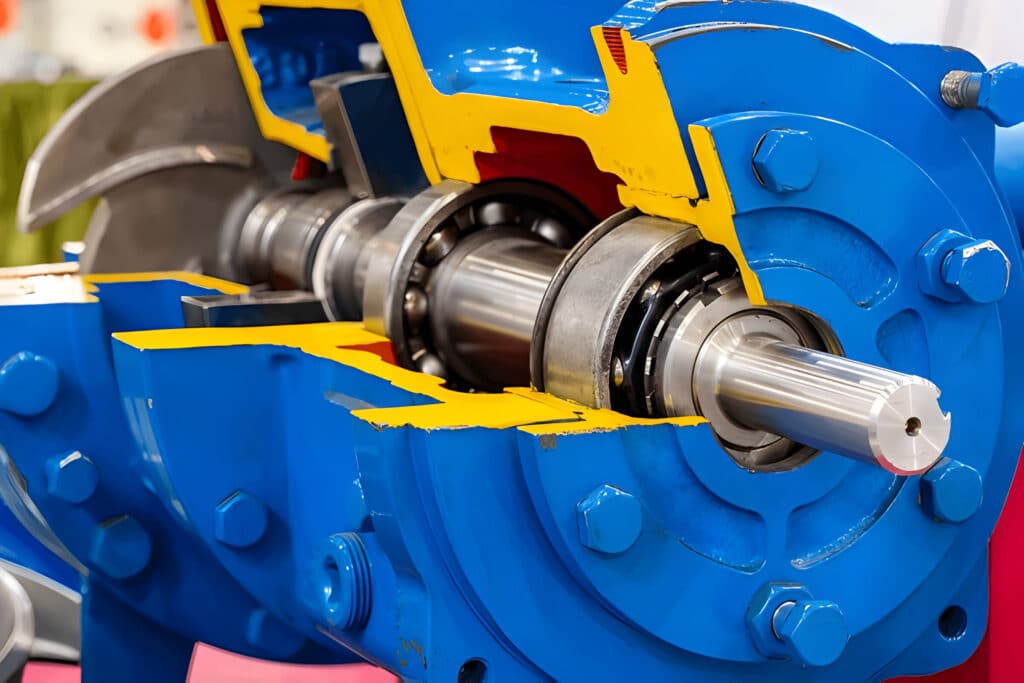
What Is Plan 11
Plan 11 is a control system used in fluid power applications to regulate the operation of a hydraulic pump. It consists of a variable displacement pump, a pressure compensator, and a control piston. The pressure compensator maintains a constant pressure in the system by adjusting the displacement of the pump.
The control piston is connected to the pressure compensator and the pump’s swashplate. As the load pressure increases, the pressure compensator moves the control piston, which in turn reduces the pump’s displacement to maintain the set pressure. Conversely, when the load pressure decreases, the control piston increases the pump’s displacement to maintain the set pressure.
Plan 11 is commonly used in applications where a constant pressure is required, such as in hydraulic presses, injection molding machines, and other industrial equipment. It provides a simple and reliable method of pressure control without the need for complex electronic controls.
What Is Plan 13
Plan 13 is an advanced control system for hydraulic pumps that combines the features of Plan 11 with additional flow control capabilities. Like Plan 11, it consists of a variable displacement pump, a pressure compensator, and a control piston. However, Plan 13 also includes a flow compensator and a load sensing valve.
The flow compensator maintains a constant flow rate regardless of changes in load pressure. It achieves this by adjusting the pump’s displacement in response to signals from the load sensing valve. The load sensing valve monitors the pressure at the load and sends a signal to the flow compensator to adjust the pump’s displacement accordingly.
Plan 13 is used in applications where both constant pressure and precise flow control are required, such as in mobile hydraulic systems, construction machinery, and agricultural equipment. It offers improved efficiency and performance compared to Plan 11, as it allows the pump to deliver only the required flow, reducing power consumption and heat generation.
The combination of pressure and flow control in Plan 13 enables more advanced hydraulic system designs and provides greater flexibility in meeting the specific requirements of different applications.
Difference Between Plan 11 and Plan 13
Function and Operation
Plan 11 systems are designed to maintain a constant downstream pressure, regardless of changes in flow rate or upstream pressure. They achieve this by modulating the valve opening in response to pressure variations, ensuring a stable pressure at the outlet.
In contrast, Plan 13 systems are designed to maintain a constant flow rate, irrespective of changes in upstream or downstream pressure. These systems adjust the valve opening to compensate for pressure fluctuations, thereby maintaining a steady flow rate through the system.
Application
Plan 11 systems are commonly used in applications where precise pressure control is critical, such as in gas distribution networks, industrial processes, and irrigation systems. These systems help prevent damage to downstream equipment and ensure consistent performance.
Plan 13 systems, on the other hand, are employed in applications where maintaining a constant flow rate is essential. Examples include chemical dosing, fuel injection systems, and cooling water circuits. By ensuring a steady flow rate, Plan 13 systems help optimize process efficiency and product quality.
Pressure Management
Plan 11 systems prioritize maintaining a constant downstream pressure. They continuously monitor the outlet pressure and adjust the valve position to compensate for any deviations. This active pressure management ensures that downstream equipment and processes receive a stable pressure supply, preventing damage and ensuring optimal performance.
Plan 13 systems, however, do not actively manage downstream pressure. Instead, they focus on maintaining a constant flow rate, allowing the downstream pressure to fluctuate as necessary. This approach is suitable for applications where downstream pressure variations do not significantly impact the process or equipment.
Flow Control
Plan 11 systems do not directly control the flow rate; instead, they indirectly influence it by managing the downstream pressure. As a result, the flow rate may vary depending on the system’s demand and the valve’s capacity to maintain the set pressure.
Conversely, Plan 13 systems are designed specifically for flow control. They continuously monitor the flow rate and adjust the valve opening to maintain the desired flow, even in the face of pressure changes.
Monitoring and Maintenance
Plan 11 systems require regular monitoring of downstream pressure to ensure the system is operating within the desired range. Pressure sensors and monitoring equipment are crucial components in Plan 11 systems, allowing for real-time tracking and adjustment of pressure control.
Plan 13 systems, on the other hand, prioritize flow rate monitoring. Flow meters are essential components in these systems, providing accurate measurements of the fluid or gas flow. Regular calibration and maintenance of flow meters are necessary to ensure the system continues to maintain the desired flow rate accurately.