Flax
Flax packing, made from natural flax fibers, is a traditional choice for pump applications involving clean water and mild acids. Its soft and pliable nature allows for easy installation and conformity to the pump shaft, creating an effective seal. Flax packing is best suited for low-pressure and low-temperature applications, such as in centrifugal pumps handling cold water or lubricating fluids.
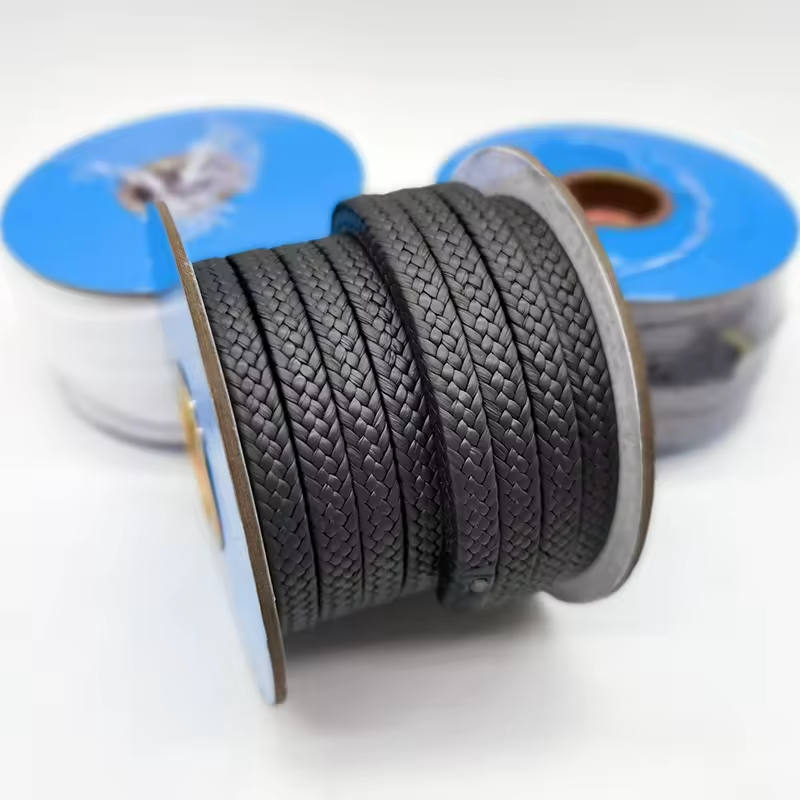
Acrylic
Acrylic packing, composed of synthetic acrylic fibers, offers excellent resistance to abrasion and a wide range of chemicals. Its low coefficient of friction minimizes wear on the pump shaft and stuffing box, extending the service life of the equipment. Acrylic packing is suitable for applications involving moderate temperatures and pressures, making it a popular choice for process pumps in various industries.
Novoloid
Novoloid packing, made from synthetic phenolic fibers, exhibits exceptional thermal stability and chemical resistance. It is well-suited for high-temperature applications, such as in pumps handling steam or hot fluids. Novoloid packing’s low thermal expansion coefficient ensures a stable and reliable seal, even under extreme conditions.
Aramid
Aramid packing, constructed from aramid fibers, boasts high tensile strength and excellent resistance to abrasion and chemicals. Its superior mechanical properties make it ideal for demanding pump applications, such as those involving abrasive slurries or corrosive fluids. Aramid packing can withstand high pressures and temperatures, making it a reliable choice for critical processes in industries like mining and chemical processing.

Filament polytetrafluoroethylene (PTFE)
Filament PTFE packing combines the chemical inertness and low friction properties of PTFE with the strength of filament fibers. This combination results in a packing material that offers exceptional resistance to a wide range of chemicals, including strong acids and bases. Filament PTFE packing is self-lubricating, minimizing wear on the pump shaft and ensuring smooth operation. It is suitable for applications involving corrosive fluids, high temperatures, and moderate pressures.
EXPANDED PTFE FIBERS
Expanded PTFE fiber packing is made from highly compressed PTFE fibers, resulting in a dense and flexible material. This packing type offers excellent chemical resistance, low friction, and superior sealing properties. Expanded PTFE packing is ideal for applications involving aggressive chemicals, high temperatures, and pressures, such as in the chemical processing and pharmaceutical industries.
CARBON AND GRAPHITE PACKING FIBERS
Carbon and graphite packing fibers are known for their high thermal conductivity, excellent chemical resistance, and self-lubricating properties. These materials are well-suited for high-temperature and high-pressure applications, such as in pumps handling steam, hot gases, or abrasive fluids.
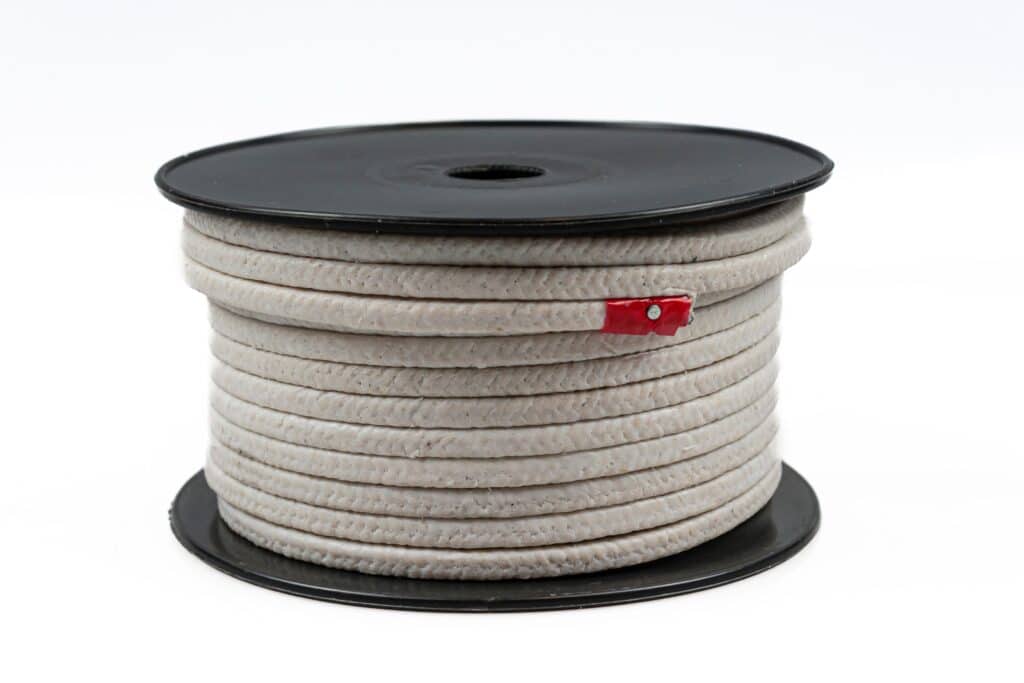
FLEXIBLE GRAPHITE TAPE
Flexible graphite tape is a versatile packing material that combines the benefits of graphite with the flexibility of a tape form. It offers excellent thermal stability, chemical resistance, and conformability to the pump shaft. Flexible graphite tape is suitable for a wide range of applications, including high-temperature and high-pressure environments, as well as in pumps handling corrosive or abrasive fluids.
PURE GRAPHITE PACKING FIBERS
Pure graphite packing fibers are made from high-purity graphite, offering exceptional thermal conductivity and chemical resistance. This material is ideal for extreme temperature applications, such as in pumps handling molten salts or hot gases. Pure graphite packing fibers provide efficient heat dissipation, minimizing the risk of thermal damage to the pump components. They also exhibit excellent sealing properties, preventing leakage and ensuring reliable operation.
Packing Material | Temperature Limits | Pressure Limits | Chemical Compatibility | Abrasion Resistance | Shaft Speed Ratings | Typical Applications |
---|---|---|---|---|---|---|
Flax | -50°C to 120°C | Up to 100 psi | Limited, suitable for water and mild acids | Low | Low to moderate | Clean water, cold water, and mild acids |
Acrylic | -50°C to 150°C | Up to 300 psi | Good, resistant to most chemicals | Moderate | Moderate to high | Process pumps, moderate temperature and pressure applications |
Novoloid | -50°C to 250°C | Up to 500 psi | Excellent, resistant to most chemicals | High | Moderate to high | High-temperature applications, steam, and hot fluids |
Aramid | -50°C to 250°C | Up to 500 psi | Excellent, resistant to most chemicals and abrasive media | Very high | High | Abrasive slurries, corrosive fluids, and demanding applications |
Filament PTFE | -200°C to 260°C | Up to 500 psi | Excellent, resistant to almost all chemicals | Moderate to high | Moderate to high | Corrosive fluids, high temperatures, and moderate pressures |
Expanded PTFE | -200°C to 260°C | Up to 1000 psi | Excellent, resistant to almost all chemicals | High | High | Aggressive chemicals, high temperatures, and pressures |
Carbon and Graphite | -200°C to 650°C | Up to 1000 psi | Excellent, resistant to most chemicals and abrasive media | Very high | High | High-temperature and high-pressure applications, abrasive fluids |
Flexible Graphite Tape | -200°C to 650°C | Up to 1000 psi | Excellent, resistant to most chemicals and abrasive media | Very high | High | High-temperature and high-pressure environments, corrosive or abrasive fluids |
Pure Graphite | -200°C to 650°C | Up to 1000 psi | Excellent, resistant to most chemicals and abrasive media | Very high | High | Extreme temperature applications, molten salts, and hot gases |
FAQs
What is the best packing for a water pump?
For cold water applications, flax packing is a suitable choice due to its soft and conformable nature. In applications involving higher temperatures or mildly acidic water, acrylic or aramid packing may be more appropriate.