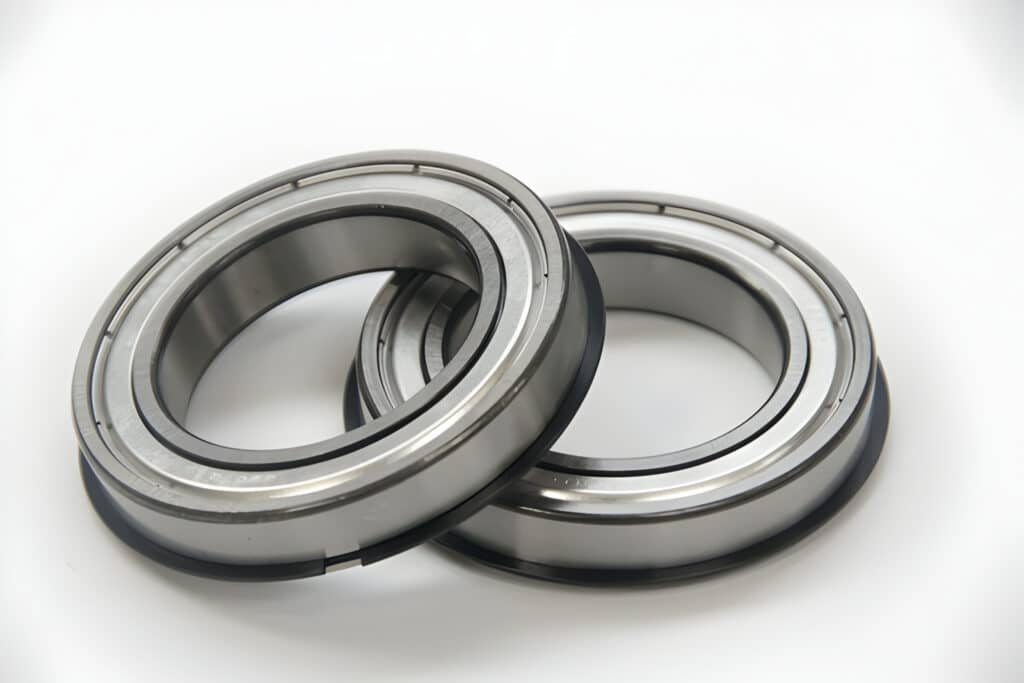
What Is Single Lip Seal
A single lip seal, also known as a single lip oil seal, is a type of seal that features a single sealing lip to prevent leakage and protect against contaminants. Single lip seals are a popular choice for many applications due to their cost-effective designs and reliable performance. These seals are commonly used in wheel bearings, pinion seals, and other rotary seal applications.
The primary function of a single lip seal is to create a barrier against fluid leakage and ingress of contaminants such as dust and water. The seal consists of a single rubber lip that contacts the sealing surface, typically a shaft or bore housing material. The lip material is chosen based on factors such as chemical resistance, temperature range, and compatibility with the fluid in question.
Single lip seals often incorporate a garter spring to maintain consistent contact between the lip and the sealing surface. The garter spring provides structural rigidity and helps compensate for wear over time. The lip seal design allows for the formation of a thin lubrication film between the lip and the sealing surface, which reduces friction and minimizes heat development.
Advantages of Single Lip Seal
- Simpler design: Single lip seals have a more straightforward design compared to double lip seals, making them easier to manufacture and install.
- Reduced friction: With only one sealing lip in contact with the shaft or bore surface, single lip seals generate less friction compared to double lip seals. This reduced friction minimizes heat development, which can be crucial in high-speed applications or when dealing with temperature-sensitive fluids.
- Lower torque requirements: Due to the reduced friction, single lip seals require less torque to operate effectively. This lower torque demand can lead to energy savings and extended seal life, particularly in applications with frequent starts and stops or variable speeds.
- Compact design: Single lip seals typically have a more compact profile than double lip seals, making them suitable for applications with limited space or tight clearances.
- Easier to maintain: The simpler design of single lip seals makes them easier to inspect, clean, and replace when necessary. This can lead to reduced maintenance costs and downtime, especially in applications where frequent seal replacements are required.
Disadvantages of Single Lip Seal
- Less protection against contaminants: Single lip seals provide less protection against the ingress of dust, dirt, and other contaminants compared to double lip seals. The additional dust lips or secondary seal in double lip designs acts as an extra barrier, offering superior protection in harsh environments.
- Reduced chemical resistance: In some cases, single lip seals may have lower chemical resistance compared to double lip seals. The choice of lip material and the presence of a barrier liquid in double lip designs can enhance the seal’s ability to withstand exposure to aggressive chemicals, making them a better choice for applications in the chemical industry.
- Lower sealing efficiency: Single lip seals may have lower sealing efficiency compared to double lip seals, particularly in applications with high pressure differences or when dealing with low-viscosity fluids. The dual sealing lips in double lip designs provide a more effective barrier against leakage, ensuring better containment of the fluid in question.
- Faster wear in abrasive environments: In applications involving abrasive particles or contaminants, single lip seals may experience faster wear compared to double lip seals. The additional protection provided by the secondary seal in double lip designs helps to extend the seal life in abrasive conditions.
When to Use Single Lip Seal
Single lip seals are a popular choice for many applications due to their cost-effective designs and ability to provide adequate sealing performance in less demanding environments. These seals are best suited for applications with moderate speeds, pressures, and temperatures. Single lip oil seals are commonly used in gear boxes, pumps, and motors where a single sealing lip is sufficient to prevent leakage of the lubricant, such as grease or oil.
Single lip seals are ideal for applications where the sealing surface is relatively smooth and free from contaminants. They work well on shafts made from hardened materials and can provide an effective barrier against the ingress of dirt, dust, and moisture. However, in environments with high levels of contamination or where the sealing surface is prone to wear, single lip seals may not provide sufficient protection, and double lip seals may be a better choice.
What Is Double Lip Seal
A double lip seal, also known as a double lip oil seal or dual lip seal, is a type of mechanical seal that provides additional protection against contaminants and leakage compared to single lip seals. Double lip seals feature two separate sealing lips, typically made of rubber or elastomer material, that create a barrier against fluid leakage and ingress of dirt, dust, and water.
The primary seal, or inner seal, is responsible for retaining the lubricant within the system, while the secondary seal, or outer seal, acts as a barrier against external contaminants. The space between the two sealing lips is often filled with a barrier fluid or grease, which enhances the sealing performance and provides lubrication to the sealing surfaces.
Advantages of Double Lip Seal
- Enhanced Protection: Double lip seals provide an additional level of protection compared to single lip seals. The secondary seal, or dust lip, acts as a barrier against water ingress, dust, and other contaminants, ensuring the primary seal remains clean and functional.
- Improved Lubrication: The double lip design allows for the retention of a lubricating film between the two seal lips. This hydrodynamic lubricating film reduces friction and heat generation, leading to extended seal life and improved performance. The presence of a barrier liquid or grease lubricant further enhances the sealing function and provides additional protection against leakage.
- Increased Structural Rigidity: Double lip seals often incorporate a garter spring design, which provides increased structural rigidity compared to single lip seals. The garter spring helps maintain consistent contact between the seal lips and the sealing surface, even under varying pressure conditions.
- Failsafe Sealing: In the event of a failure of the primary seal, the secondary seal in a double lip design acts as a failsafe, preventing immediate leakage and allowing for timely maintenance. This redundancy is particularly important in applications where seal failure can lead to significant downtime, environmental hazards, or safety risks.
Disadvantages of Double Lip Seal
- Higher cost: Double lip seals are generally more expensive than single lip seals due to their more complex design and additional components, such as the secondary seal and garter spring. This cost difference can be a significant factor when selecting the appropriate seal for an application, especially in large-scale industrial settings where numerous seals are required.
- Increased friction: The additional lip in double lip seals can lead to higher friction compared to single lip seals. This increased friction can result in greater heat generation, which may cause premature wear and reduced seal life in some applications. The friction-generated heat can also negatively impact the lubricating film, potentially compromising the seal’s performance.
- Limited high-speed compatibility: Double lip seals may not be suitable for high-speed applications due to the increased friction and heat development. The additional lip can cause more drag on the rotating shaft, leading to higher temperatures and accelerated wear. In contrast, single lip seals often have a more streamlined design that allows for better performance in high-speed environments.
- More complex installation: Double lip seals typically require more precise alignment and installation compared to single lip seals. The additional components, such as the secondary seal and garter spring, can make the installation process more challenging and time-consuming.
When to Use Double Lip Seal
Double lip seals are particularly well-suited for high-speed applications, such as those found in the marine industry, where the risk of contamination and leakage is higher.
Double lip seals are also a good choice for applications involving challenging conditions, such as high temperatures or exposure to harsh chemicals. The use of advanced materials, such as FKM-EAL (Fluoroelastomer – Environmentally Adapted Lubricant) for the seal lips, can provide excellent chemical resistance and durability in these demanding environments.