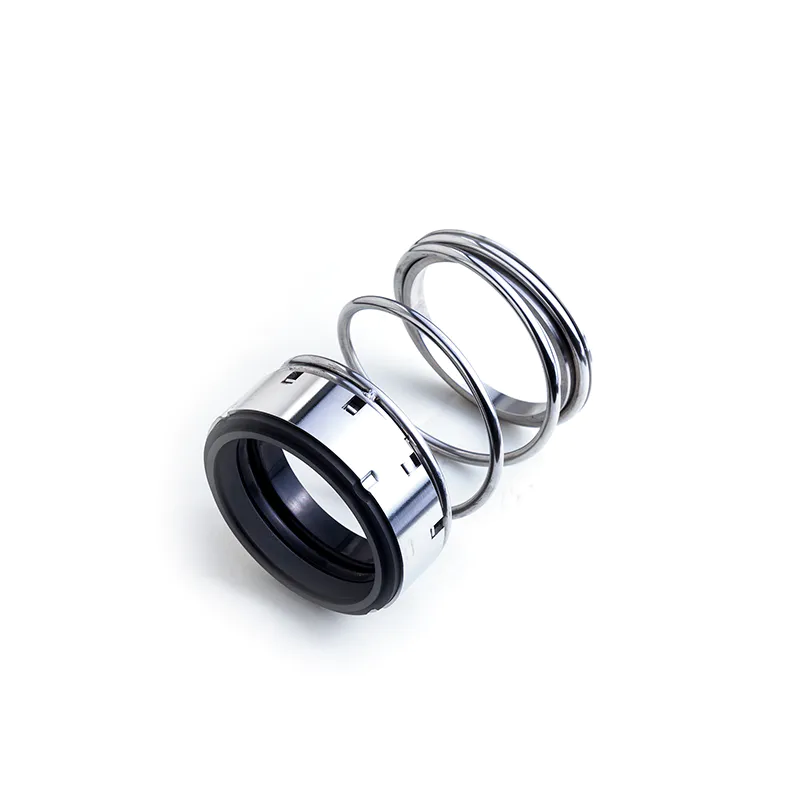
What Are Type 1 Mechanical Seals
Type 1 mechanical seals, also known as full convolution bellows seals, are a reliable sealing solution used in various industrial applications. These seals consist of a rotating primary ring and a stationary mating ring, with a bellows assembly that provides flexibility and allows for axial movement. The bellows is typically made of a corrosion-resistant material such as stainless steel or Hastelloy, ensuring durability and compatibility with a wide range of fluids.
One of the key features of Type 1 mechanical seals is their ability to handle misalignment and shaft movement. The full convolution bellows design allows for greater axial travel compared to other seal types, compensating for any irregularities in the shaft or equipment. This adaptability makes Type 1 seals suitable for applications with moderate shaft runout or end play.
Type 1 mechanical seals are commonly used in pumps, mixers, and other rotating equipment across various industries, including chemical processing, oil and gas, pharmaceuticals, and food and beverage. They are capable of sealing a wide range of fluids, from low-viscosity liquids to high-viscosity slurries, and can operate in temperatures ranging from cryogenic to over 400°C (752°F).
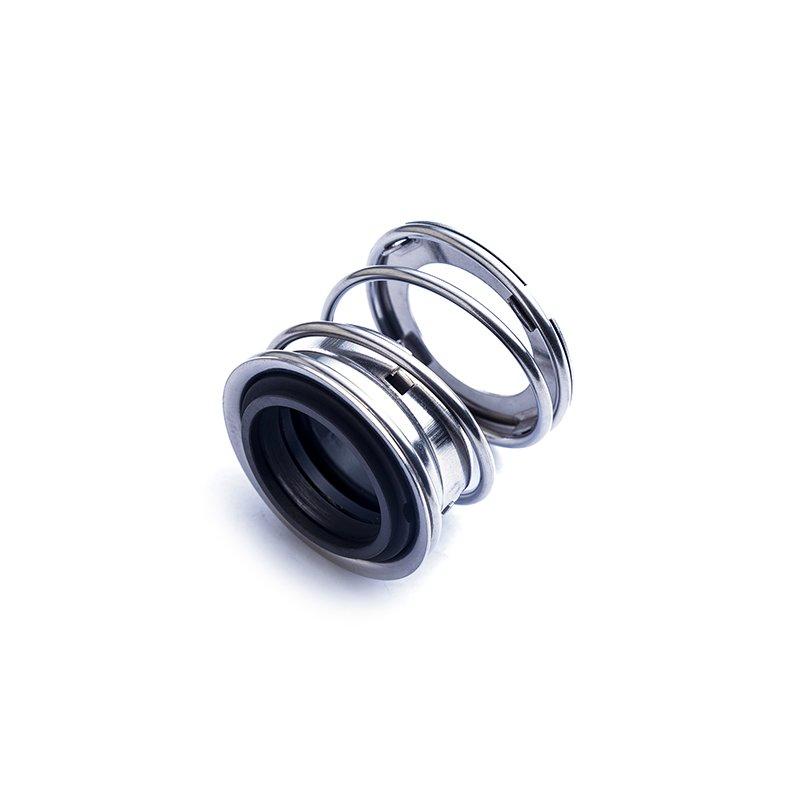
What Are Type 2 Mechanical Seals
Type 2 mechanical seals, also referred to as multi-purpose non-pusher seals, are another widely used sealing solution in industrial settings. Like Type 1 seals, they consist of a rotating primary ring and a stationary mating ring. However, the key difference lies in the design of the flexible element and the location of the springs.
In Type 2 mechanical seals, the flexible element is typically a multi-convolution bellows or a diaphragm, which is designed to provide axial movement and maintain a constant sealing force. The springs in Type 2 seals are located outside the fluid environment, usually in the atmospheric side of the seal. This design allows for a more compact seal assembly compared to Type 1 seals.
Type 2 mechanical seals offer several advantages, including a wider range of pressure handling capabilities. They are available in single, double, and balanced configurations, allowing them to handle pressures from vacuum to high-pressure applications. The balanced design of some Type 2 seals enables them to operate with minimal wear and friction, extending seal life and reducing power consumption.
These seals find applications in various industries, such as oil and gas, petrochemicals, power generation, and water treatment. They are capable of sealing a broad range of fluids, including hydrocarbons, chemicals, and water-based solutions, and can operate in temperatures ranging from sub-zero to over 200°C (392°F).
Comparing Type 1 Vs Type 2 Seals
Bellows Design
Type 1 seals: Type 1 seals feature a full convolution bellows, which consists of deep convolutions that allow for greater axial movement. This design enables Type 1 seals to accommodate misalignment and shaft movement more effectively than Type 2 seals.
Type 2 seals: Type 2 seals typically employ a multi-convolution bellows or a diaphragm as their flexible element. While these designs provide axial movement, they generally have less axial travel compared to the full convolution bellows found in Type 1 seals.
Seal Height
Type 2 seals: Type 2 seals are generally more compact than Type 1 seals due to the location of their springs. In Type 2 seals, the springs are situated outside the fluid environment, usually on the atmospheric side of the seal. This arrangement allows for a shorter seal assembly, as the springs do not add to the overall height of the seal.
Type 1 seals: Type 1 seals have their springs located within the fluid environment, often nested inside the convolutions of the bellows. While this design provides excellent axial movement, it also results in a taller seal assembly compared to Type 2 seals.
Pressure Handling
Type 2 mechanical seals: Type 2 mechanical seals offer a wider range of pressure handling capabilities. This versatility is due to the availability of different configurations, including single, double, and balanced designs.
Single Type 2 seals are suitable for low to medium pressure applications, while double Type 2 seals can handle higher pressures by utilizing a barrier fluid between the two sealing elements. The balanced design of some Type 2 seals allows for even greater pressure handling capacity, as the hydraulic forces acting on the seal faces are minimized, reducing wear and extending seal life.
Type 1 mechanical seals: Type 1 seals, while still capable of handling a wide range of pressures, may be limited in their pressure handling capabilities compared to the various configurations available for Type 2 seals. The pressure limitations of Type 1 seals are often dependent on factors such as the bellows material, the number of convolutions, and the overall seal design.
Application Breadth
Type 1 mechanical seals: Type 1 seals are often considered more versatile in terms of the range of fluids they can handle. The full convolution bellows design of Type 1 seals, coupled with the availability of various corrosion-resistant materials, allows them to seal a wide variety of fluids, from low-viscosity liquids to high-viscosity slurries. They can also operate in a wide temperature range, from cryogenic to over 400°C (752°F), making them suitable for extreme temperature applications.
Type 2 mechanical seals: While Type 2 seals are also capable of sealing a broad range of fluids and operating in various temperature ranges, they may be more limited in terms of their compatibility with certain fluid types or extreme temperature conditions compared to Type 1 seals.