What is API Plan 54
API Plan 54 is a piping arrangement used with mechanical seals to provide a more reliable and safer sealing system. It is designed to collect and control leakage from the seal, while also preventing the process fluid from entering the atmosphere.
How Does API Plan 54 Work
The API Plan 54 system uses an external reservoir to supply clean, cool barrier fluid to the mechanical seal. This barrier fluid is maintained at a pressure higher than the pressure in the pump, which helps prevent process fluid from entering the seal chamber and causing damage or contamination.
The barrier fluid is circulated from the reservoir, through the seal chamber, and back to the reservoir in a closed loop. This circulation is typically driven by an internal pumping ring on the mechanical seal, which uses the rotation of the shaft to pump the barrier fluid.
As the barrier fluid circulates, it helps to lubricate and cool the seal faces, reducing friction and wear. The higher pressure of the barrier fluid also provides a positive flow of clean fluid across the seal faces, helping to flush away any small amounts of process fluid that may leak past the primary seal.
The reservoir in a Plan 54 system serves several important functions. It acts as an expansion tank to accommodate changes in fluid volume due to temperature variations. It also provides a place for any process fluid leakage to accumulate, allowing it to be drained away safely without contaminating the barrier fluid.
Additionally, the reservoir allows the condition of the barrier fluid to be monitored. Pressure, temperature, and level sensors can be installed on the reservoir to alert operators to any potential issues with the sealing system.
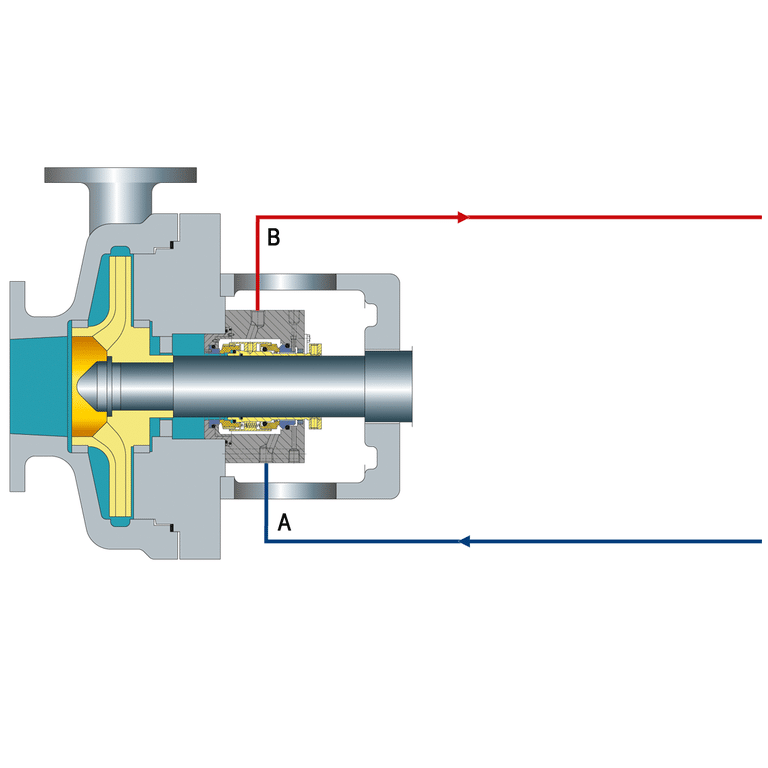
Design of API Plan 54
- External Flush Fluid Reservoir: Holds flush fluid; size depends on the seal size and required flush rate.
- Seal Flush Piping: Carries flush fluid to and from the seal chamber, ensuring correct flow rate and pressure.
- Pressure Regulating Valve: Installed to maintain constant pressure in the seal chamber, preventing process fluid intrusion.
- Flow Control Orifice: Controls flush fluid flow rate; size calculated based on required flow rate and pressure drop.
- Heat Exchanger (Optional): Cools flush fluid before it enters the seal chamber, useful when process fluid is hot.
Advantages of API Plan 54
- Enhanced seal life: By maintaining a cool and clean environment, API Plan 54 extends the life of mechanical seals.
- Improved system reliability: The closed-loop design reduces the risk of contamination and ensures a stable seal environment.
- Increased efficiency: Proper cooling and lubrication of the seal faces minimize friction and wear, improving overall system efficiency.
- Flexibility: API Plan 54 can be adapted to various pump and process conditions, making it a versatile solution for high-temperature applications.
Disadvantages of API Plan 54
- Increased complexity: The additional components and piping required for API Plan 54 increase system complexity compared to simpler seal support plans.
- Higher initial cost: The external heat exchanger, circulation pump, and additional piping and instrumentation result in higher initial installation costs.
- Maintenance requirements: Regular maintenance of the heat exchanger, circulation pump, and other components is necessary to ensure optimal system performance.
Applications
- Refineries and petrochemical plants
- Oil and gas production
- Chemical processing
- Power generation
- Pulp and paper industry
- Food and beverage processing