Axial bearings and thrust bearings are essential components in mechanical systems, playing a crucial role in supporting loads and enabling smooth rotation. This article provides a comprehensive comparison of these two bearing types, highlighting their differences and applications.
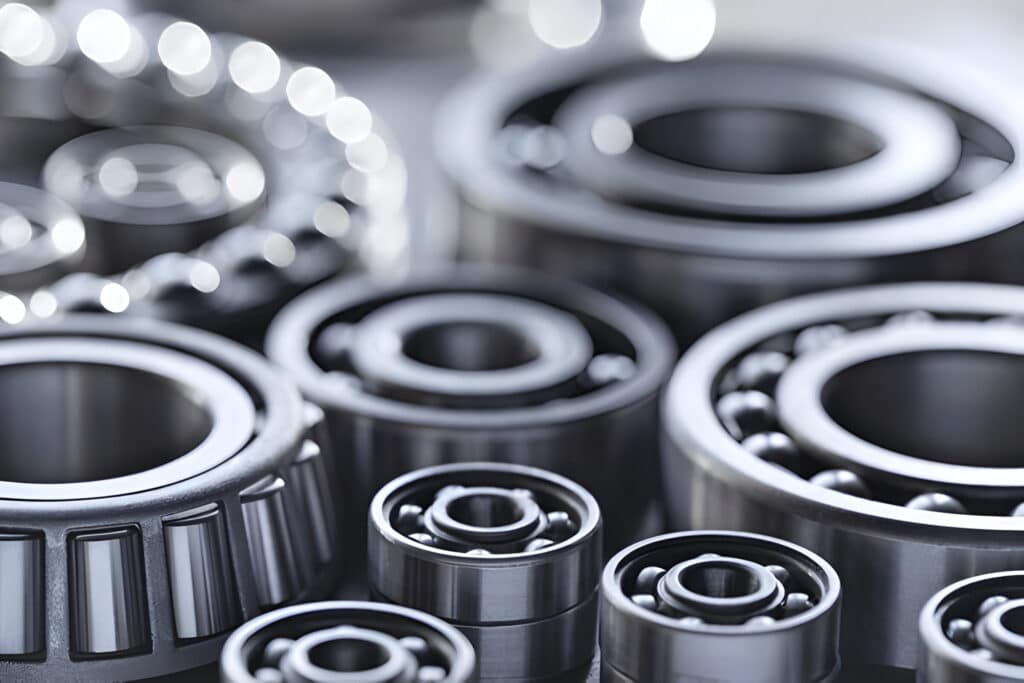
What Is Axial Bearing
An axial bearing, also known as a thrust bearing, is a type of rotary bearing designed to support axial loads, which are forces acting parallel to the shaft axis.
These bearings are commonly used in applications where the primary load is axial, such as in electric motors, automotive transmissions, and industrial machinery.
Axial bearings come in various designs, including ball thrust bearings, cylindrical roller thrust bearings, and tapered roller thrust bearings.
What Is Thrust Bearing
Thrust bearings are a specific type of axial bearing designed to handle thrust loads, which are forces acting in the axial direction of the shaft.
They are used in applications where the primary load is thrust, such as in marine propulsion systems, wind turbines, and hydroelectric generators.
Thrust bearings are available in several designs, including spherical roller thrust bearings, cylindrical roller thrust bearings, and tapered roller thrust bearings.
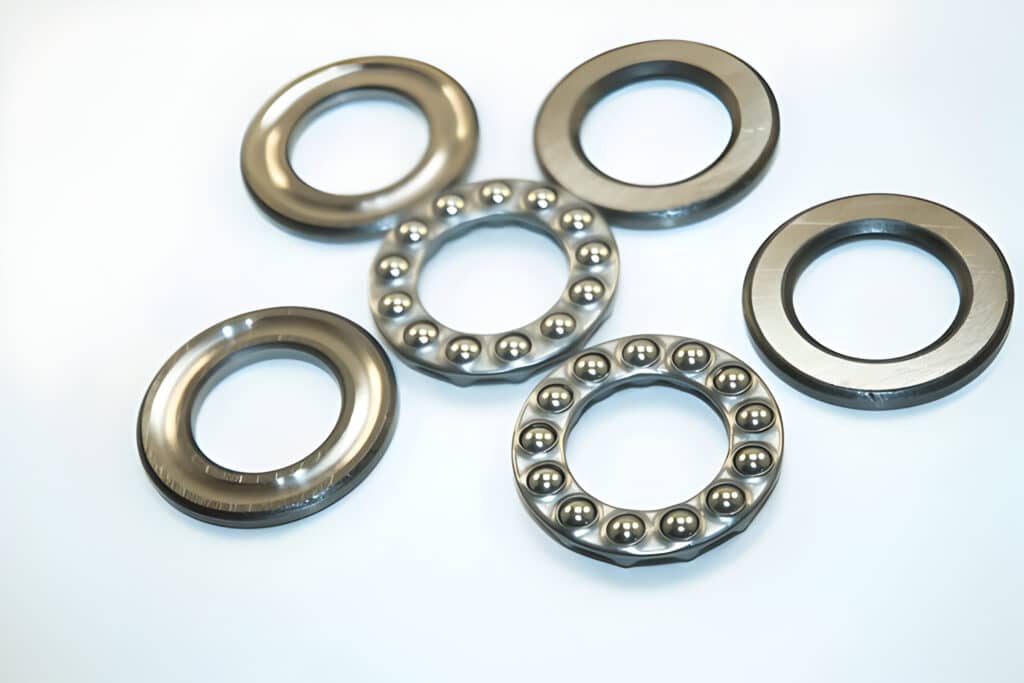
Key Differences between Radial and Thrust Bearings
Load Direction
Radial bearings: Radial bearings are designed to handle radial loads, which are forces acting perpendicular to the shaft axis.
Thrust bearings: Thrust bearings are designed to support axial loads, which are forces acting parallel to the shaft axis.
Speed Capability
Radial bearings: Radial bearings are generally capable of operating at higher speeds compared to thrust bearings. This is due to their design, which allows for better heat dissipation and lower friction.
Thrust bearings: Thrust bearings are typically used in lower-speed applications due to their larger contact area and higher friction.
Load Capacity
Radial bearings: Radial bearings, while capable of supporting significant loads, have a smaller contact area and, therefore, a lower load capacity.
Thrust bearings: Thrust bearings generally have a higher load capacity compared to radial bearings of similar size. This is because thrust bearings have a larger contact area between the rolling elements and the races, allowing them to distribute the load more effectively.
Design and Internal Geometry
Radial bearings: Radial bearings typically feature rolling elements arranged in a circular pattern around the shaft, with the load being supported by the rolling elements and the outer and inner races.
Thrust bearings: Thrust bearings have rolling elements arranged in a planar configuration, with the load being supported by the rolling elements and the thrust plates or washers.
Misalignment Tolerance
Radial bearings: Radial bearings generally have a higher tolerance for misalignment compared to thrust bearings. This is because radial bearings allow for some angular misalignment between the shaft and the housing, thanks to their circular arrangement of rolling elements.
Thrust bearings: Thrust bearings, being planar in nature, have a lower tolerance for misalignment and require more precise alignment during installation and operation.
Selecting between Radial and Thrust Bearings
Matching Bearing Type to Application Loads
If the primary load is radial, a radial bearing should be used. If the primary load is axial or thrust, a thrust bearing is the appropriate choice.
In applications with combined loads, a bearing type that can handle both radial and axial loads, such as an angular contact ball bearing or a tapered roller bearing, may be suitable.
Consider Speed, Load Magnitude and Direction, Space Constraints
Radial bearings are generally better suited for high-speed applications, while thrust bearings are more appropriate for lower-speed, high-load scenarios. The available space in the system may also dictate the bearing type, as some bearing designs are more compact than others.
Combining Radial and Thrust Bearings for Some Applications
In some cases, it may be necessary to use both radial and thrust bearings in a single application. This is common in systems where the shaft experiences significant radial and axial loads simultaneously, such as in automotive transmissions and industrial gearboxes. By using separate radial and thrust bearings, each bearing can be optimized for its specific load type, ensuring optimal performance and longevity.
Conclusion
Understanding the differences between axial and thrust bearings is essential for selecting the appropriate bearing type for a given application. By considering factors such as load direction, speed, load magnitude, and space constraints, engineers and designers can make informed decisions when specifying bearings for mechanical systems.