Are you struggling to select the right mechanical seal for your application? With so many options like balanced and unbalanced designs, it can be challenging to know which is best. Using the wrong type of seal can lead to premature failure, leaks, and costly downtime.
In this article, we’ll clearly explain the key differences between balanced and unbalanced mechanical seals, including design, pressure handling, cost, seal life and more.
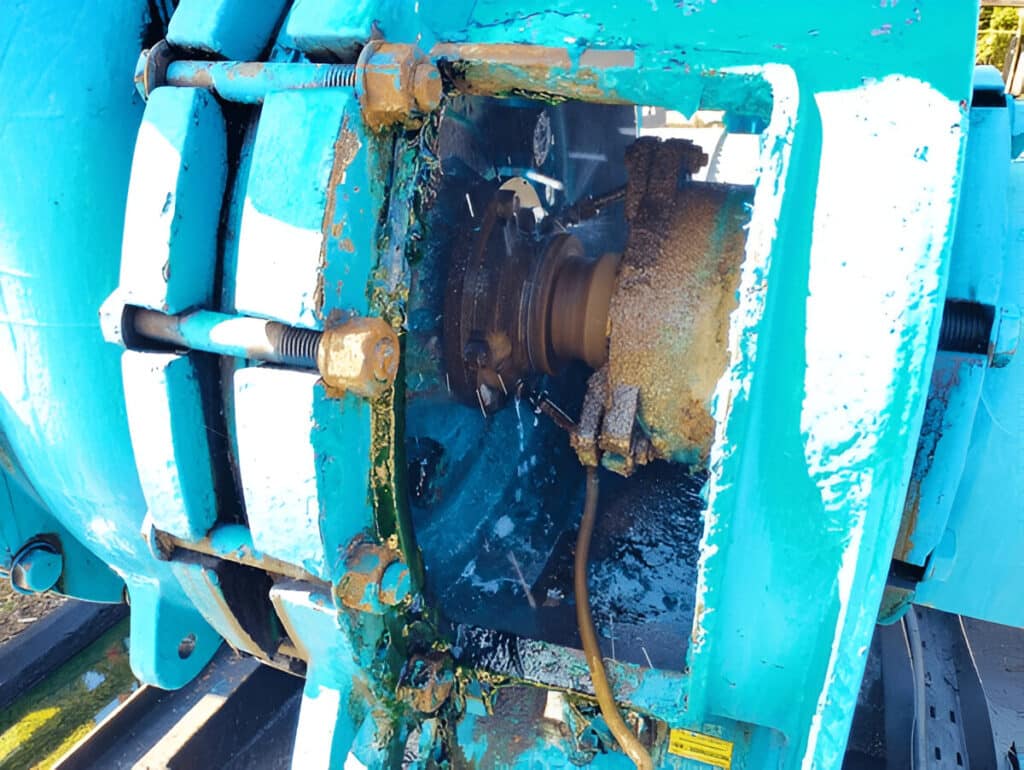
What Is Balanced Mechanical Seal
A balanced mechanical seal is a type of mechanical seal designed to handle higher pressures and speeds compared to unbalanced seals. In a balanced seal, the closing forces acting on the seal faces are reduced by modifying the seal geometry or by using hydraulic methods.
This reduction in closing forces is achieved by equalizing the pressure on both sides of the seal faces. Balanced seals often incorporate multiple springs or bellows to maintain a consistent closing force under varying conditions.
What Is Unbalanced Mechanical Seal
An unbalanced mechanical seal, also known as a conventional seal, is a simpler design compared to balanced seals. In an unbalanced seal, the closing force acting on the seal faces is directly proportional to the sealed pressure.
As the sealed pressure increases, the closing force also increases, which can lead to higher face loads and heat generation. Unbalanced seals are commonly used in applications with lower pressures and speeds.
The Difference Between Balanced and Unbalanced Mechanical Seals
Design
Balanced seals feature a more complex design that incorporates additional components, such as multiple springs or bellows, to equalize pressure on the seal faces.
Unbalanced seals have a simpler, more straightforward design with fewer components.
Pressure Handling
Balanced seals are capable of handling higher pressures due to their ability to equalize pressure on the seal faces.
Unbalanced seals are limited in their pressure handling capabilities, as the closing force increases directly with the sealed pressure.
Cost
Due to their more complex design and additional components, balanced seals are typically more expensive than unbalanced seals.
Unbalanced seals offer a more cost-effective solution for lower pressure applications.
Seal Life
Balanced seals generally have a longer service life compared to unbalanced seals.
The reduced closing forces and more consistent face loading in balanced seals contribute to extended seal life and reduced wear.
Stability
Balanced seals provide greater stability under varying operating conditions, such as pressure fluctuations or thermal changes.
Unbalanced seals are more susceptible to instability and face distortion under these conditions.
Liquid Handling
Balanced seals are better suited for handling liquids with higher viscosities or abrasive particles. The reduced face loading allows for better lubrication and reduced risk of face damage.
Unbalanced seals may struggle with these types of liquids due to higher face loads.
Seal Face Loading
In balanced seals, the face loading remains relatively constant regardless of the sealed pressure. This consistent loading promotes even wear and extended seal life.
Unbalanced seals experience increased face loading as the sealed pressure rises, leading to accelerated wear.
Heat Generation
Balanced seals generate less heat compared to unbalanced seals due to the reduced face loading and improved lubrication.
Excessive heat generation in unbalanced seals can lead to premature failure or secondary seal damage.
Applications
Balanced mechanical seals are commonly used in high-pressure applications, such as multistage pumps, boiler feed pumps, and high-pressure compressors. They are also suitable for applications with high viscosity or solids-containing liquids.
Unbalanced seals are typically used in low to medium-pressure applications, such as single-stage pumps, mixers, and low-pressure compressors.