What causes pump vibration? Excessive vibration in pumps can lead to reduced performance, increased maintenance costs, and even complete failure.
In this blog post, we’ll explore the primary factors contributing to pump vibration and provide you with practical insights to identify and address these issues effectively.
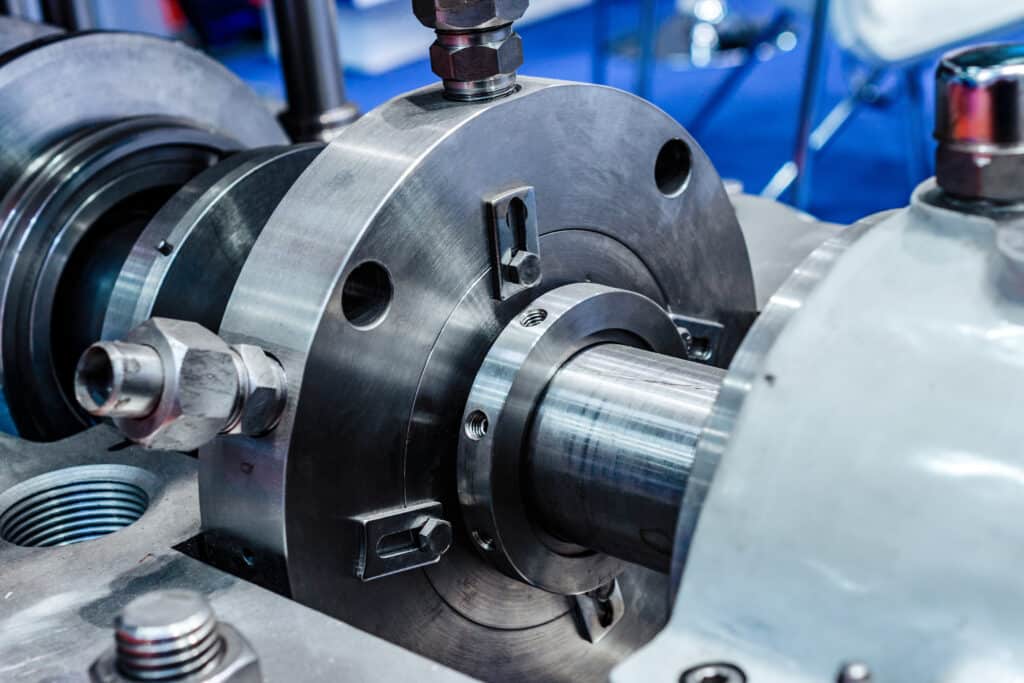
Mechanical Causes of Pump Vibration
1. Rotor Imbalance
Static and Dynamic Imbalance
Rotor imbalance, a common cause of excessive vibration in centrifugal pumps, can be classified as static or dynamic.
Static imbalance occurs when the center of mass is offset from the axis of rotation, causing the rotor to experience a net force.
Dynamic imbalance, on the other hand, arises when the principal inertia axis is not aligned with the rotational axis, resulting in a net couple.
Causes and Effects on Vibration
Factors such as material non-uniformity, manufacturing tolerances, and uneven wear contribute to rotor imbalance.
An imbalanced rotor generates undesirable vibrations, leading to increased bearing loads, reduced seal life, and potential structural damage.
The vibration frequency typically matches the pump operating speed, with amplitude proportional to the degree of imbalance.
How to Fix
To mitigate the effects of rotor imbalance, various balancing techniques are employed. Single-plane balancing is suitable for short, rigid rotors, while two-plane balancing is necessary for longer, flexible rotors.
2. Bent Shaft
How a Bent Shaft Induces Vibration
A bent shaft introduces a geometric asymmetry that causes the rotor to wobble during rotation. This wobble generates a vibration at the shaft rotational frequency, often accompanied by harmonics.
The severity of the vibration depends on the degree of shaft deflection and the rotor’s operating speed.
Methods for Detecting and Quantifying Shaft Runout
Shaft runout, a measure of the shaft’s deviation from a straight line, can be detected using dial indicators or laser alignment tools. These instruments measure the radial displacement of the shaft at various locations, allowing for the quantification of the bend’s severity.
Shaft Straightening and Replacement Considerations
If a bent shaft is identified, corrective actions must be taken. For minor bends, shaft straightening techniques, such as cold or heat straightening, may be employed.
However, if the bend is severe or the shaft has undergone multiple straightening attempts, replacement is often necessary to ensure reliable pump operation and prevent further damage to associated components.
3. Impeller Imbalance
Causes of Impeller Imbalance
Impeller imbalance can arise from various factors, including erosion, corrosion, and fouling.
Erosion occurs when abrasive particles in the pumped fluid wear away the impeller material unevenly.
Corrosion, caused by chemical reactions between the impeller and the pumped fluid, can lead to non-uniform material loss.
Fouling, the accumulation of debris on the impeller surfaces, also contributes to imbalance.
Effects on Vibration and Pump Performance
An imbalanced impeller generates vibrations at the pump operating speed and its multiples. These vibrations can cause excessive bearing wear, seal failure, and coupling damage.
Additionally, impeller imbalance can lead to reduced pump efficiency, increased power consumption, and decreased flow rate, as the impeller’s hydraulic performance is compromised.
Impeller Balancing and Trimming Techniques
To address impeller imbalance, in-situ balancing or impeller trimming may be performed.
In-situ balancing involves adding or removing material from the impeller while it is installed in the pump, using specialized tools and techniques.
Impeller trimming, on the other hand, requires removing the impeller and machining its surfaces to restore balance.
4. Bearing Issues
Types of Bearing Failures and Their Vibration Signatures
Common failure modes include inner race defects, outer race defects, ball or roller defects, and cage failures.
These defects generate vibrations at specific fault frequencies, which are related to the bearing’s geometry and rotational speed.
Analyzing the vibration spectrum can help identify the type and severity of the bearing fault.
Causes of Bearing Failures
Bearing failures can stem from multiple causes, such as improper lubrication, overloading, and misalignment.
Inadequate lubrication leads to increased friction and heat generation, accelerating wear.
Overloading, caused by excessive radial or axial forces, can result in premature fatigue failure.
Misalignment, whether angular or parallel, induces additional stresses on the bearings, reducing their lifespan.
Bearing Maintenance and Condition Monitoring Strategies
Regular lubrication, using appropriate lubricants and quantities, helps reduce friction and dissipate heat.
Condition monitoring techniques, such as vibration analysis, temperature monitoring, and oil analysis, provide insights into the bearing’s health.
5. Shaft Misalignment
Types of Misalignment
Shaft misalignment can be classified into three types: angular, parallel, and combined.
Angular misalignment occurs when the shafts are at an angle to each other, while parallel misalignment arises when the shafts are offset but remain parallel. Combined misalignment is a combination of both angular and parallel misalignment, and is the most common type encountered in the field.
Effects on Vibration and Coupling Wear
Misaligned shafts generate vibrations at the coupling, with frequencies typically being multiples of the shaft rotational speed.
These vibrations can cause accelerated wear on the coupling components, leading to premature failure.
Additionally, misalignment can induce excessive radial and axial loads on the bearings, reducing their lifespan and increasing the risk of catastrophic failure.
Alignment Techniques and Tolerances
To correct shaft misalignment, various alignment techniques are employed, including laser alignment, reverse dial indicator method, and feeler gauge method.
Laser alignment is the most accurate and efficient technique, using laser beams to measure and adjust the relative positions of the shafts.
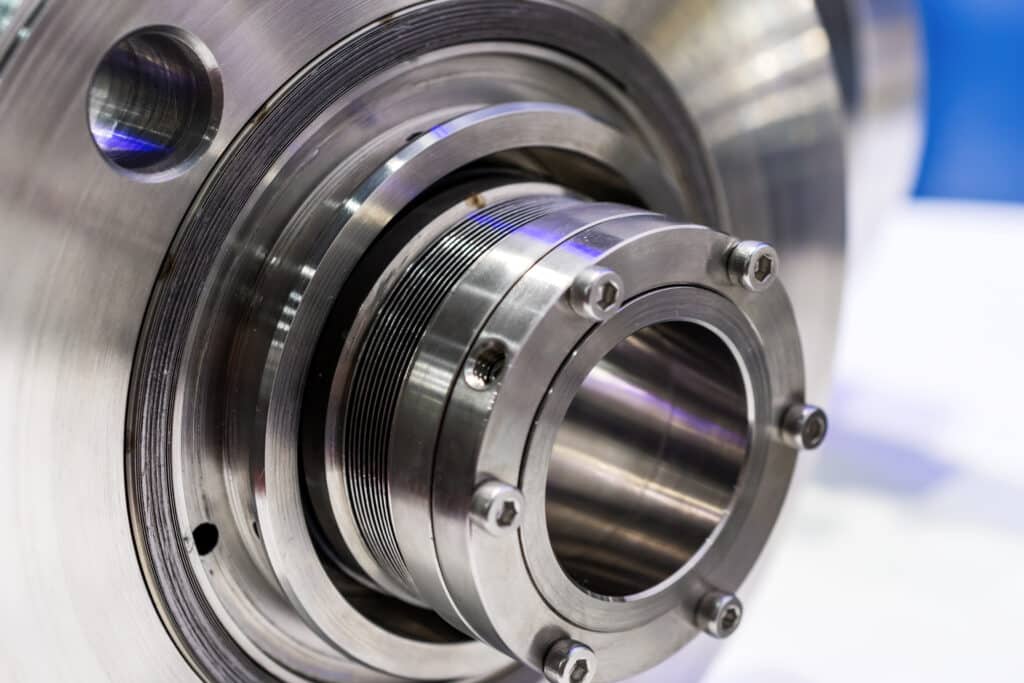
Hydraulic Causes of Pump Vibration
1. Cavitation
Explanation of Cavitation and Its Causes
Cavitation is a phenomenon that occurs when the local pressure in a liquid drops below its vapor pressure, causing the formation of vapor bubbles. In centrifugal pumps, cavitation typically occurs at the impeller inlet, where the fluid experiences a rapid pressure drop.
Factors such as insufficient Net Positive Suction Head (NPSH), high fluid temperature, and restricted suction lines contribute to the onset of cavitation.
Effects on Vibration, Noise, and Pump Damage
Cavitation can have severe consequences on pump performance and longevity. As the vapor bubbles collapse, they generate high-intensity shock waves, leading to increased vibration and noise levels. This process, known as cavitation erosion, can cause significant damage to the impeller, volute, and other pump components.
Cavitation also reduces pump efficiency and can lead to complete pump failure if left unchecked.
NPSH Requirements and Cavitation Prevention Strategies
To prevent cavitation, it is crucial to ensure that the available NPSH (NPSHA) always exceeds the required NPSH (NPSHR) specified by the pump manufacturer.
This can be achieved by proper system design, including adequate suction piping size, minimizing suction line losses, and maintaining sufficient suction pressure.
Operating the pump near its Best Efficiency Point (BEP) and selecting a pump with a suitable suction specific speed (Nss) also help reduce the risk of cavitation.
2. Flow Pulsation
Causes of Flow Pulsation
Flow pulsation in centrifugal pumps can arise from various factors, such as operating near the shut-off head or system resonance.
When a pump operates near its shut-off head, the flow becomes unstable, leading to pressure fluctuations and pulsations.
System resonance occurs when the pulsation frequency matches the natural frequency of the piping system, amplifying the vibrations and potentially causing severe damage.
Effects on Vibration and System Stability
Flow pulsation can significantly impact the vibration levels and overall stability of the pumping system.
The oscillating flow induces alternating forces on the pump and piping components, leading to increased vibration and stress.
In extreme cases, flow pulsation can cause pipe rupture, equipment damage, and unscheduled downtime.
It can also interfere with process control and product quality, particularly in sensitive applications.
Pulsation Dampening and System Design Considerations
To mitigate the effects of flow pulsation, various pulsation dampening techniques can be employed.
These include installing pulsation dampeners, such as bladder or diaphragm accumulators, in the discharge line to absorb pressure fluctuations. Proper piping design, with attention to pipe supports, anchors, and flexibility, can help reduce the risk of system resonance.
Additionally, operating the pump away from the shut-off head and ensuring adequate NPSH can minimize flow instabilities.
3. Off-BEP Operation
Best Efficiency Point (BEP) and Pump Performance Curves
The Best Efficiency Point (BEP) is the flow rate at which a centrifugal pump operates with maximum efficiency. Pump performance curves, which plot head, power, and efficiency against flow rate, provide valuable information about the pump’s operating characteristics.
Operating a pump at or near its BEP ensures optimal performance, minimizes energy consumption, and reduces the risk of mechanical issues.
Consequences of Operating Away from BEP
Operating a pump significantly away from its BEP can have detrimental effects on vibration levels and pump life.
At flow rates lower than BEP, the pump experiences increased radial loads, leading to higher shaft deflection and bearing wear.
At flow rates higher than BEP, the pump may encounter cavitation, excessive noise, and vibration.
Prolonged operation away from BEP can result in premature bearing failure, seal damage, and impeller wear.
Importance of Proper Pump Selection and System Design
The pump should be selected to operate near its BEP under normal operating conditions, taking into account factors such as flow rate, head, and fluid properties.
The system should be designed to minimize pressure losses and ensure stable flow conditions.
Regular monitoring of pump performance and vibration levels can help detect off-BEP operation and prompt corrective actions.
In conclusion
Pump vibration can be caused by various factors, including cavitation, misalignment, imbalance, and mechanical issues. Identifying and addressing the root cause is crucial for maintaining pump performance and longevity.
For expert assistance in diagnosing and resolving pump vibration problems, contact our experienced team today.