Selecting the right pump is a critical decision in various industrial applications. Diaphragm and peristaltic pumps are common choices, each with specific advantages and disadvantages.
This article will provide a comprehensive comparison of these two pump types. You will learn their operational principles, capabilities, and differences. We will also delve into fluid handling, maintenance needs, and cost considerations. The goal is to help you make an informed decision.
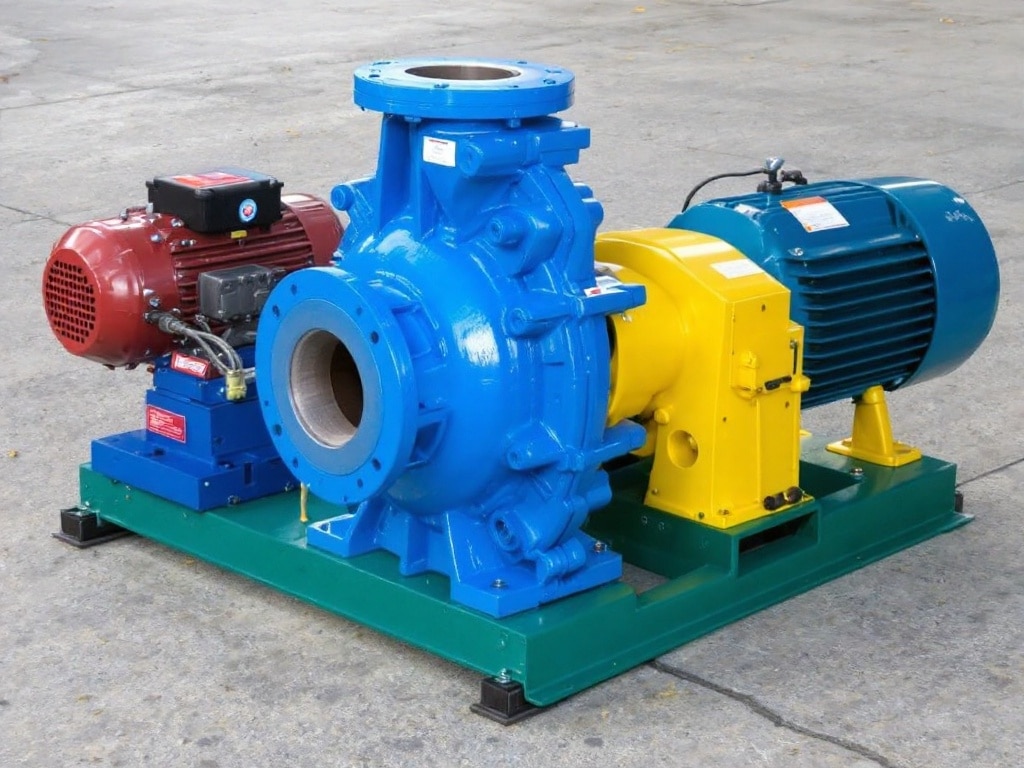
What Is a Diaphragm Pump
A diaphragm pump is a positive displacement pump that uses a flexible diaphragm to move fluids. The diaphragm, typically made of rubber, thermoplastic, or PTFE, is reciprocated by a mechanical drive. As the diaphragm retracts, it creates a vacuum, drawing fluid into the pump chamber. When the diaphragm moves forward, it displaces the fluid, forcing it out of the discharge port. This process results in the pumping action. Diaphragm pumps often include check valves to ensure unidirectional flow and prevent backflow.
These pumps are versatile and can handle a wide range of fluids, including abrasive, corrosive, and viscous materials.
Advantages of Diaphragm Pumps Over Peristaltic Pumps
- Handling of Abrasive Fluids: Diaphragm pumps are typically more robust in handling abrasive fluids and slurries compared to peristaltic pumps.
- Higher Pressure Capability: They often achieve higher discharge pressures, making them suitable for applications requiring significant head pressure.
- Wider Material Compatibility: The wetted components of diaphragm pumps are made from a wider variety of materials, allowing for better compatibility with diverse chemicals.
- Lower Cost for High Flow Rate: For applications requiring high flow rates, diaphragm pumps can be more cost-effective than peristaltic pumps.
- Better Dry Run Capability: Diaphragm pumps can often handle dry run conditions for short periods without significant damage, unlike peristaltic pumps.
- Ability to handle larger particles: Diaphragm pumps are able to handle fluids with larger suspended particles, unlike peristaltic pumps
Disadvantages of Diaphragm Pumps Over Peristaltic Pumps
- Pulsating Flow: Diaphragm pumps typically produce a more pulsating flow, which may not be suitable for applications requiring a smooth, continuous flow.
- Higher Maintenance: They have more moving parts, such as valves and diaphragms, which require regular inspection and maintenance.
- Lower Accuracy for Low Flows: Diaphragm pumps may not achieve the same level of accuracy as peristaltic pumps, especially when dealing with very low flow rates.
- Potential for Leakage: If seals or the diaphragm fail, diaphragm pumps can experience leaks.
- More Complex Design: Their design with multiple parts makes them more complicated to repair than peristaltic pumps
What Is a Peristaltic Pump
A peristaltic pump is a positive displacement pump that uses a rotating mechanism to compress a flexible tube, forcing fluid to move through it. The fluid is contained within the tube, and the pump’s rollers or shoes compress the tube sequentially, pushing the fluid forward. As the compression point moves, it creates a vacuum that draws more fluid into the tube.
This simple design ensures that the fluid never comes into contact with the pump’s moving parts, making it ideal for sterile, sensitive, or corrosive fluids. Peristaltic pumps are well-known for their gentle pumping action and accuracy, especially at low flow rates.
Advantages of Peristaltic Pumps Over Diaphragm Pumps
- Gentle Pumping Action: Peristaltic pumps offer a gentle pumping action with minimal shear, making them ideal for sensitive materials.
- Precise Flow Control: These pumps provide highly accurate and repeatable flow rates, especially at low flow rates, which is crucial for applications requiring precision.
- No Contamination Risk: Because the fluid is contained entirely within the tubing, there is no risk of contamination from the pump’s moving parts, making them suitable for sterile applications.
- Simple Maintenance: Peristaltic pumps have minimal moving parts, resulting in simple and infrequent maintenance. Tube replacement is typically the only required upkeep.
- Self-Priming: Peristaltic pumps are self-priming, meaning they can remove air from the suction line automatically.
- Handles Viscous Fluids: Peristaltic pumps can handle highly viscous fluids.
Disadvantages of Peristaltic Pumps Over Diaphragm Pumps
- Limited Pressure Capability: Peristaltic pumps are generally limited to lower discharge pressures compared to diaphragm pumps.
- Tubing Wear: The flexible tubing can wear out over time, especially with abrasive fluids, requiring periodic replacement.
- Lower Flow Rates: They are not typically suitable for high flow rate applications compared to diaphragm pumps.
- Inability to Handle Solids Peristaltic pumps are not suitable to pump fluids with suspended solids due to the risk of clogging and damage to the pump
- Not suitable for gas pumping: Peristaltic pumps are not suitable to pump gases.
Difference Between Diaphragm Pumps and Peristaltic Pumps
Fluid Handling Capabilities
- Diaphragm Pumps: Well-suited for abrasive fluids, slurries, and higher viscosity liquids, with some limitations on shear-sensitive materials. They can also handle fluids with larger particles.
- Peristaltic Pumps: Best for shear-sensitive materials, sterile fluids, and viscous liquids. Not suitable for fluids with suspended solids or gases.
Maintenance and Complexity
- Diaphragm Pumps: More complex, with multiple moving parts such as diaphragms and valves, requiring regular inspection and maintenance.
- Peristaltic Pumps: Simpler design with minimal moving parts, making maintenance mainly limited to tube replacement.
Pulsation & Flow Characteristics
- Diaphragm Pumps: Tend to produce a pulsating flow, requiring additional dampeners in some applications for smooth output.
- Peristaltic Pumps: Provide a more gentle and consistent flow, with lower pulsation, especially suitable for applications needing a stable flow.
Sealing, Contamination, and Material Compatibility
- Diaphragm Pumps: Can be more prone to leakage, with wetted components made from diverse materials, allowing better compatibility with more chemicals.
- Peristaltic Pumps: Offer superior sealing by containing fluid entirely within the tube, preventing any contamination of pump parts or the fluid itself.
Cost
- Diaphragm Pumps: Can be more cost-effective for high flow rate applications.
- Peristaltic Pumps: Generally more expensive, especially for high-volume pumping, but lower maintenance can make them more economical in the long run for some applications
Flow Rate Calculations
- Diaphragm Pumps: Flow rate is determined by the diaphragm size, the stroke length, and the pumping speed.
- Flow Rate = (Diaphragm Displacement per stroke) x (Number of strokes per minute)
- Peristaltic Pumps: Flow rate is determined by the tube diameter, the rotational speed of the rotor, and the number of rollers.
- Flow Rate = (Area of tubing) x (Linear velocity of fluid) x (Number of rotations per time)
The linear velocity of the fluid is based on the rotation speed of the rollers.
- Flow Rate = (Area of tubing) x (Linear velocity of fluid) x (Number of rotations per time)