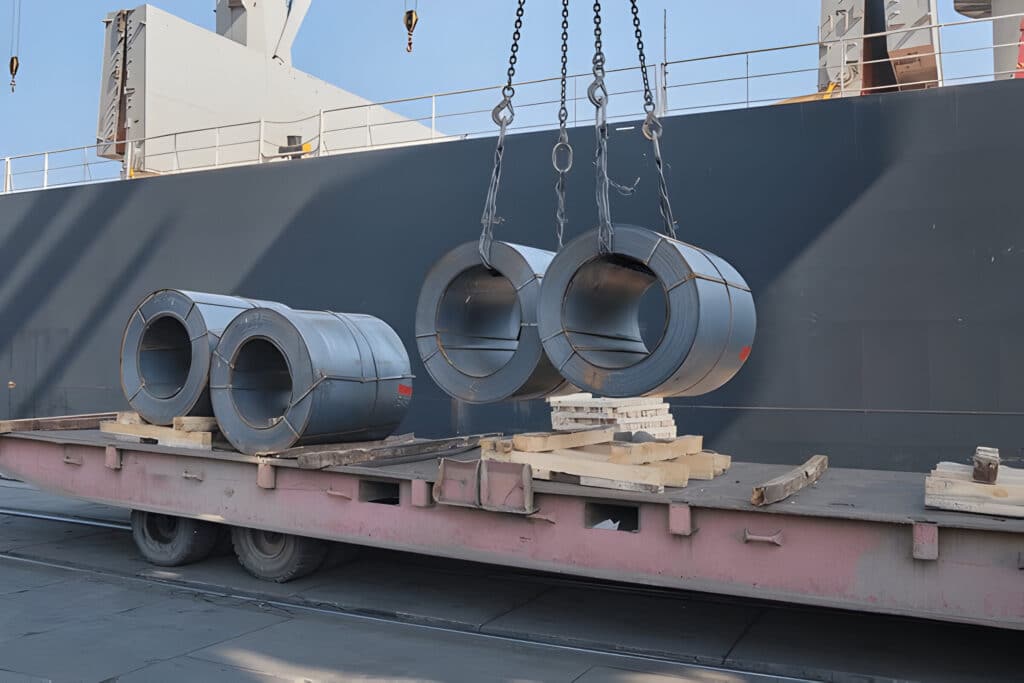
Stainless steel is known for its corrosion resistance, but the question remains: does stainless steel rust in saltwater? The answer is not a simple yes or no, as several factors influence the corrosion resistance of stainless steel in marine environments.
This article will explore the different grades of stainless steel, how they resist corrosion, and the factors that can cause stainless steel to rust in saltwater.
Corrosion Resistant Grades and Alloys
Stainless steel is an alloy of iron, chromium, and other elements. The chromium content, typically between 12-30%, is responsible for forming a protective layer of chromium oxide on the surface of the metal, which helps prevent corrosion. Some grades of stainless steel are more corrosion resistant than others, particularly in saltwater environments.
304/L Stainless Steel
304 and 304L stainless steel are the most common grades, known for their good corrosion resistance in a variety of environments. These austenitic grades contain 18-20% chromium and 8-10.5% nickel. While suitable for many applications, they may not provide sufficient corrosion resistance in harsh marine environments with high chloride content.
316/L Stainless Steel
316 and 316L stainless steel, also austenitic grades, contain 16-18% chromium, 10-14% nickel, and 2-3% molybdenum. The addition of molybdenum enhances resistance to pitting and crevice corrosion, making these grades more suitable for saltwater applications. 316 and 316L are often referred to as “marine grade” stainless steel.
Duplex Stainless Steel
Duplex stainless steels, such as 2205 and 2507, have a two-phase microstructure consisting of austenite and ferrite. They offer higher strength and better corrosion resistance than austenitic grades, particularly in environments with high chloride content and elevated temperatures. Duplex stainless steels are an excellent choice for demanding marine applications.
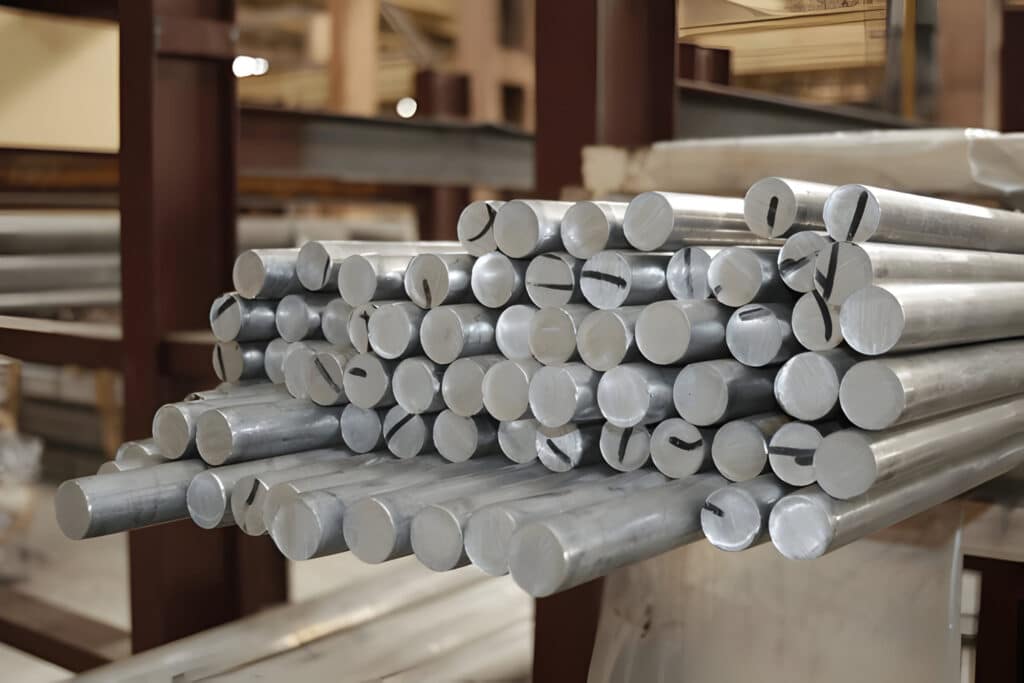
How Stainless Steel Resists Corrosion
Stainless steel resists corrosion through a passive layer of chromium oxide that forms on its surface when exposed to oxygen. This thin, invisible layer acts as a barrier, preventing further oxidation and corrosion of the underlying metal. As long as this passive layer remains intact, the stainless steel will maintain its corrosion resistance.
However, the passive layer can be compromised by various factors, such as surface damage, improper cleaning, or exposure to harsh chemicals. When the passive layer is disrupted, the stainless steel becomes vulnerable to corrosion, particularly in the presence of chloride ions found in saltwater.
Factors That Can Cause Stainless Steel to Rust in Saltwater
- Grade of Stainless Steel Used: Lower grade stainless steels, such as 304 and 304L, may not provide adequate corrosion resistance in harsh marine environments.
- Chloride Concentration: Higher levels of chlorides in the water can increase the risk of pitting and crevice corrosion.
- Service Temperature: Elevated temperatures can accelerate corrosion rates and weaken the protective passive layer.
- Water Flow Rates & Oxygen Levels of the Water: Stagnant or low-oxygen environments can promote the formation of localized corrosion cells.
- Cleaning and Maintenance Frequency: Infrequent or improper cleaning can allow salt deposits and other contaminants to accumulate on the surface, leading to corrosion.
- Amount of Time in Contact with Saltwater: Prolonged exposure to saltwater increases the likelihood of corrosion.
- Galvanic Corrosion from Contact with Dissimilar Metals: When stainless steel is in direct contact with a less noble metal, such as carbon steel, galvanic corrosion can occur.
- Surface Damage or Imperfections That Compromise the Passive Layer: Scratches, welds, or other surface irregularities can disrupt the passive layer and provide initiation sites for corrosion.
Types of Stainless Steel Suitable for Saltwater Environments
For marine applications, it is crucial to select a stainless steel grade with sufficient corrosion resistance. Some of the most suitable types include:
- 316 and 316L stainless steel
- Duplex stainless steels (2205, 2507)
- Super austenitic stainless steels (254 SMO, AL-6XN)
- Super duplex stainless steels (Zeron 100, Ferralium 255)
Preventing Corrosion of Stainless Steel in Saltwater
- Material Selection: Choose a stainless steel grade with sufficient corrosion resistance for the specific environment and application.
- Design Considerations: Avoid crevices, stagnant areas, and contact with dissimilar metals. Use proper insulation and protective coatings when necessary.
- Regular Cleaning and Maintenance: Regularly clean stainless steel surfaces to remove salt deposits and other contaminants. Use mild detergents and avoid abrasive cleaning methods that could damage the passive layer.
- Cathodic Protection: In some cases, cathodic protection systems can be used to prevent corrosion by supplying an electrical current to the stainless steel.
FAQs
What Metal Is Best for Saltwater?
Marine-grade stainless steel (316L or 316) is the most corrosion-resistant and durable metal for saltwater applications. It contains molybdenum, which enhances its ability to withstand salt corrosion.
What Metal Doesn’t Rust in Salt Water?
No metal is entirely immune to rust or corrosion in saltwater. However, certain alloys like stainless steel, copper-nickel, and titanium offer excellent corrosion resistance in marine environments.
Will Stainless Steel Rust near the Ocean?
Stainless steel can rust near the ocean if the grade selected is not suitable for marine environments or if factors like surface damage, improper cleaning, or contact with dissimilar metals compromise its corrosion resistance.
How Long Does Stainless Steel Last in Sea Water?
With proper selection and care, stainless steel can provide decades of service in marine applications.