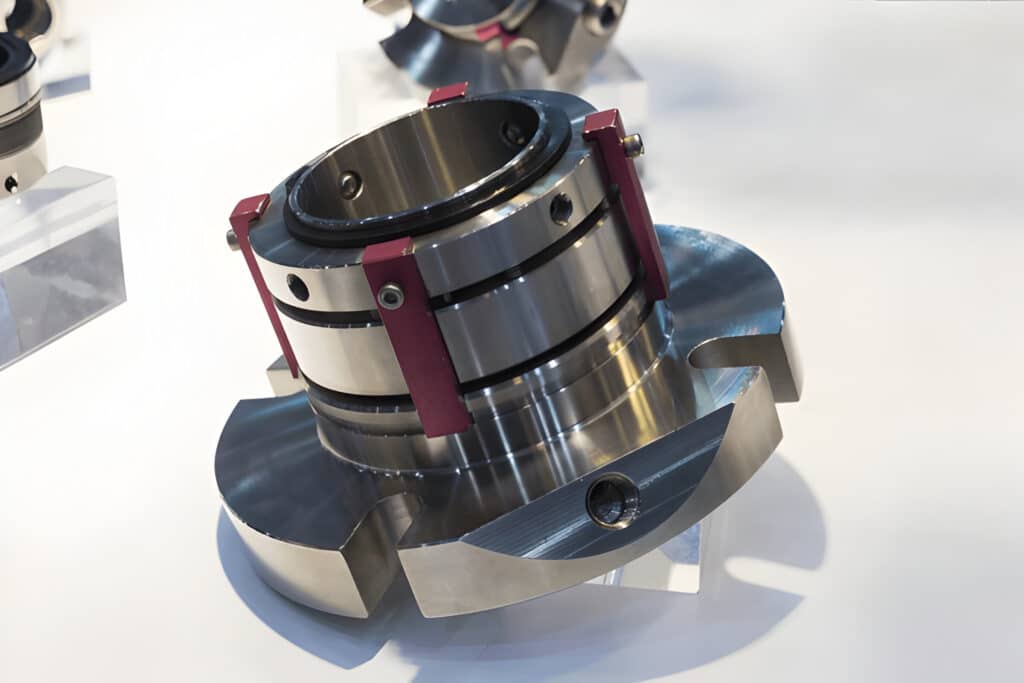
Mechanical seals and bearings are both crucial components in machinery, but they serve distinctly different purposes. While mechanical seals prevent fluid leakage between rotating and stationary parts, bearings support moving components and reduce friction.
The main difference lies in their primary functions: mechanical seals act as barriers, while bearings facilitate motion. Mechanical seals are typically found in pumps and other fluid-handling equipment, whereas bearings are ubiquitous in various mechanical systems.
This article will delve deeper into the characteristics, applications, and advantages of both mechanical seals and bearings, helping you make informed decisions in your mechanical engineering projects.
What are Mechanical Seals
Mechanical seals are critical components in rotating equipment, designed to prevent leakage of fluids or gases between a rotating shaft and a stationary housing. These precision-engineered devices play a crucial role in maintaining the integrity and efficiency of various industrial machines, such as pumps, compressors, and mixers.
A typical mechanical seal consists of two primary faces: a rotating face that moves with the shaft and a stationary face fixed to the equipment housing. These faces are held in close contact by spring force and hydraulic pressure, creating a thin fluid film between them. This film acts as a barrier, effectively sealing the process fluid inside the equipment while allowing the shaft to rotate freely.
What are Bearings
Bearings are critical mechanical components designed to reduce friction between moving parts and support rotating elements in various machines and equipment. Unlike a mechanical seal, which primarily prevents fluid leakage, bearings facilitate smooth motion and distribute loads effectively.
Bearings consist of several key components:
- Inner race: A smooth, circular path on which the rolling elements travel.
- Outer race: The stationary outer ring that houses the rolling elements.
- Rolling elements: Balls, rollers, or needles that reduce friction between the races.
- Cage: A component that separates and guides the rolling elements.
Types of Seals Used on Bearings
There are two main categories of seals used on bearings: non-contact seals and contact seals.
Non-contact seals
Non-contact seals, as the name suggests, do not physically touch the rotating shaft. These seals create a barrier using labyrinth-like structures or clearance gaps to prevent contaminants from entering the bearing assembly. Some common types of non-contact seals include:
- Labyrinth seals: These seals use a series of intricate pathways to create a tortuous route for contaminants, effectively trapping them before they can reach the bearing.
- Clearance seals: These seals maintain a small gap between the stationary and rotating components, relying on centrifugal force to deflect contaminants.
- Magnetic seals: Utilizing magnetic fields, these seals create a barrier that repels ferrous particles, preventing them from entering the bearing housing.
Non-contact seals are particularly useful in high-speed applications where friction and heat generation must be minimized.
Contact seals
Contact seals, unlike their non-contact counterparts, physically touch the rotating shaft to create a tight seal. These seals are generally more effective at preventing contamination and retaining lubricants but may introduce additional friction. Common types of contact seals include:
- Lip seals: These flexible seals use a lip that contacts the shaft, creating a barrier against contaminants and retaining lubricants.
- O-ring seals: Consisting of a rubber or elastomeric ring, these seals fit into a groove and compress against the shaft to form a tight seal.
- Mechanical seals: While not typically used directly on bearings, mechanical seals are often found in pump applications where they work in conjunction with bearings to prevent leakage and contamination.
Contact seals are generally more suitable for lower-speed applications or where contamination prevention is critical.
Key Differences between Mechanical Seals and Bearings
Primary functions
Mechanical seals are primarily designed to prevent leakage of fluids or gases between rotating and stationary components in machinery. Their main function is to create a barrier that contains the process fluid within the equipment while keeping contaminants out. This is particularly important in applications involving pumps, compressors, and mixers where fluid containment is critical. Mechanical seals achieve this by utilizing a combination of rotating and stationary faces that form a tight seal when pressed together.
In contrast, bearings are engineered to support and guide moving parts within a machine, reducing friction and wear between components. Their primary function is to facilitate smooth rotation or linear motion while minimizing energy loss due to friction. Bearings accomplish this by using rolling elements (such as balls or rollers) or a lubricating film to separate moving surfaces, allowing for efficient transfer of loads and forces.
While both mechanical seals and bearings contribute to the overall performance of machinery, their functions are complementary rather than interchangeable. Mechanical seals focus on containment and isolation, whereas bearings emphasize load support and friction reduction. In many applications, both components work together to ensure optimal equipment operation and reliability.
Location
Mechanical seals are primarily found at the interface between rotating and stationary components, particularly in pumps, compressors, and other fluid-handling equipment. They are typically installed where a rotating shaft enters or exits a pressurized housing or vessel. For example, in a centrifugal pump, the mechanical seal is positioned between the pump casing and the rotating shaft, creating a barrier to prevent fluid leakage.
Bearings, on the other hand, are usually located along the length of a rotating shaft or axle. They can be found in various positions depending on the machine’s design and load requirements. Common locations for bearings include:
- At the ends of a shaft to provide radial and axial support
- Between different sections of a multi-component shaft
- Within gearboxes to support gear shafts
- In electric motors to support the rotor
In some cases, mechanical seals and bearings may be in close proximity, especially in pump assemblies. For instance, a pump shaft might have bearings supporting it near the impeller, with a mechanical seal positioned just outboard of the bearings to prevent fluid leakage.
Lubrication
Mechanical seals typically operate with a thin film of lubricant between the sealing faces. This film, often only a few micrometers thick, is essential for reducing friction and wear while maintaining an effective seal. The lubricant in a mechanical seal can be the process fluid itself or a specially designed barrier fluid. In some cases, mechanical seals may operate in a “dry running” condition, where specialized materials like carbon or silicon carbide are used to minimize friction without traditional lubrication.
Bearings, on the other hand, require more substantial lubrication to function properly. They typically use oil or grease to reduce friction between moving parts, dissipate heat, and protect against corrosion. The lubricant in bearings forms a hydrodynamic film that separates the rolling elements from the races, significantly reducing wear and extending the bearing’s lifespan.
The lubrication methods for mechanical seals and bearings also differ:
- Mechanical seals often rely on self-lubrication from the process fluid or a controlled leakage of barrier fluid.
- Bearings may use various lubrication systems, including:
- Oil bath lubrication
- Grease packing
- Oil mist lubrication
- Circulating oil systems
Conclusion
While both components play vital roles in machinery, they serve distinct purposes. Mechanical seals primarily function as leak prevention devices, whereas bearings facilitate smooth rotation and support loads. Their locations within machinery differ, as do their lubrication requirements and sealing mechanisms. Bearings often employ their own sealing systems, such as non-contact and contact seals, to protect against contaminants and retain lubricants. By grasping these key differences, professionals can make informed decisions about component selection, maintenance, and troubleshooting, ultimately improving equipment performance and longevity.
Ready to enhance your machinery’s performance with high-quality mechanical seals? Look no further than COWSEAL, your trusted mechanical seal manufacturer. Our expert team is prepared to assist you in selecting the perfect sealing solution for your specific application.