Are you confused about the differences between oil seals and mechanical seals in machinery?
Using the wrong seal can lead to costly leaks, equipment damage, and unplanned downtime. It’s crucial to understand the key distinctions to make the right choice for your application.
In this post, we’ll clarify the main differences between oil seals and mechanical seals, covering aspects like design, sealing mechanism, pressure and temperature ratings, lifespan, cost, maintenance needs, and typical applications.
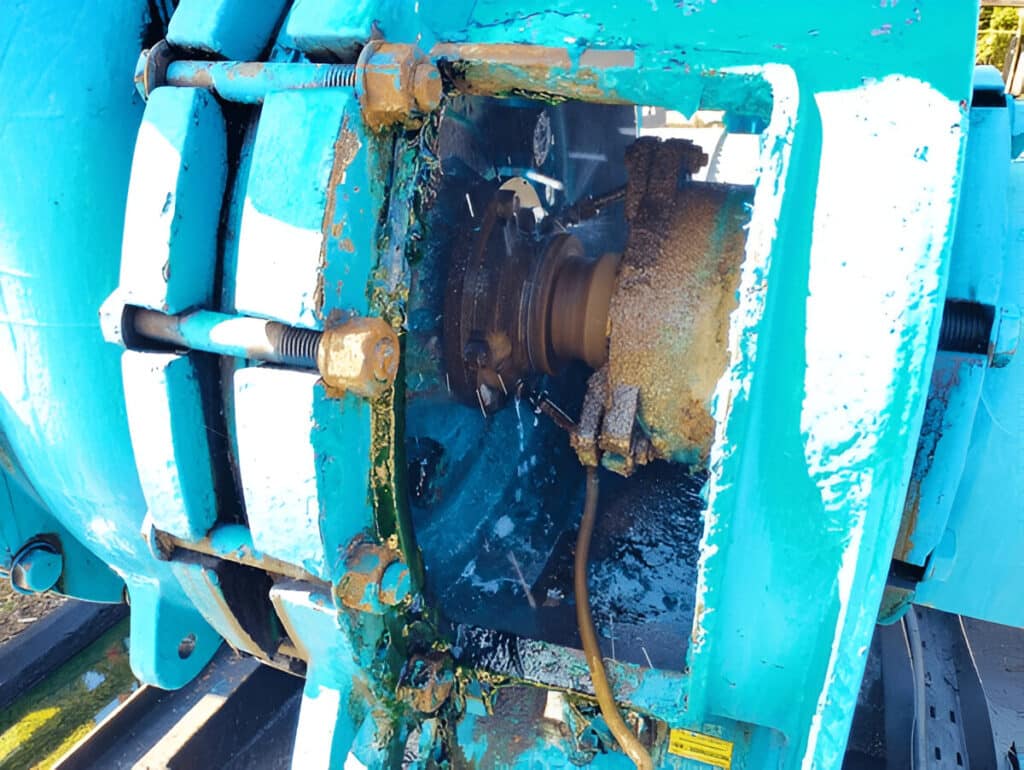
What Is Oil Seal
An oil seal is a type of mechanical device designed to prevent the leakage or ingress of fluids, such as oil or grease, between moving parts in machinery. Oil seals typically consist of a flexible elastomeric material, such as nitrile rubber or fluoroelastomer, bonded to a metal case. The elastomeric material forms a lip that rides against the shaft or housing to create a seal.
What Is Mechanical Seal
A mechanical seal is a device used to seal the rotating shaft of a pump, compressor, or other rotating equipment to prevent leakage of process fluids. It consists of two main components: a stationary part (stator) that is fixed to the equipment housing, and a rotating part (rotor) that is attached to and rotates with the shaft. The stator and rotor have precision-machined, highly-polished sealing faces that are held in contact by springs and hydraulic pressure. A thin film of fluid between the faces lubricates and cools the seal. generation, and water treatment.
Difference Between Oil Seal and Mechanical Seal
Design
Oil seals have a relatively simple design, consisting of an elastomeric sealing element bonded to a metal case.
Mechanical seals have a more complex design with multiple components, including the stator, rotor, springs, and secondary seals.
Sealing Mechanism
Oil seals rely on the contact between the flexible lip and the shaft to create a seal. The lip is energized by a garter spring to maintain contact.
Mechanical seals rely on the contact between two precision-machined, highly-polished faces to create a seal. The faces are held in contact by springs and hydraulic pressure.
Pressure Capability
Oil seals are typically used in low to moderate pressure applications, up to about 0.5 MPa (72 psi).
Mechanical seals can handle much higher pressures, with some designs capable of sealing up to 20 MPa (2900 psi) or more.
Temperature Range
The operating temperature range of oil seals is limited by the elastomeric material, with most seals rated for temperatures from -40°C to 200°C (-40°F to 392°F).
Mechanical seals can operate at higher temperatures, with some designs capable of handling temperatures up to 400°C (752°F) or more.
Service Life
Oil seals typically have a shorter service life compared to mechanical seals. The elastomeric lip is subject to wear and degradation over time, especially in abrasive or high-temperature environments.
Mechanical seals, with their hard face materials and fluid film lubrication, can provide longer service life if properly installed and maintained.
Cost
Oil seals are generally less expensive than mechanical seals due to their simpler design and lower-cost materials.
Mechanical seals require precision manufacturing and high-quality materials, which contribute to their higher cost.
Maintenance
Oil seals require minimal maintenance beyond periodic inspection and replacement when worn.
Mechanical seals require more frequent monitoring and maintenance to ensure proper operation. This may include checking for leaks, monitoring flush fluid pressure and temperature, and replacing worn components.
Applications
Oil seals are commonly used in applications such as automotive engines, transmissions, and hydraulic systems where moderate pressure and temperature conditions exist.
Mechanical seals are used in more demanding applications, such as pumps and compressors handling high-pressure, high-temperature, or hazardous fluids in industries such as chemical processing, oil and gas, and power generation.