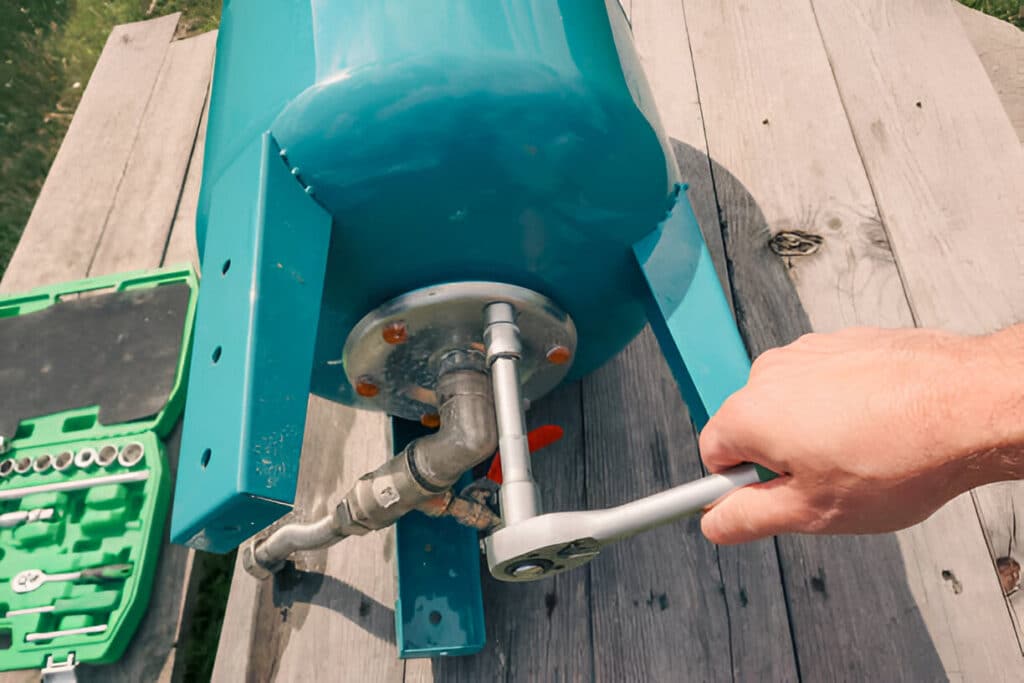
What Is Preventive Maintenance for Pumps
Preventive maintenance for pumps is a proactive approach to maintaining the optimal condition and performance of pumps. By conducting regular inspections and routine maintenance, potential issues can be identified and addressed before they lead to unexpected downtime or costly repairs.
The main goal of preventive maintenance is to identify and address potential issues before they escalate into major problems. This includes checking lubricant levels, inspecting bolts for tightness, and performing visual inspections to detect signs of wear, damage, or excessive vibration. By catching and resolving these minor issues early on, preventive maintenance can extend the lifespan of pumps, reduce repair costs, and minimize unplanned downtime.
Pump Efficiencies and Equation
Pump efficiency is a crucial factor in determining the overall performance and cost-effectiveness of pumping systems. It refers to the ratio of the useful work performed by the pump to the total energy input. In other words, it measures how effectively the pump converts mechanical energy from the motor into kinetic energy in the fluid.
To calculate pump efficiency, you can use the following equation:
Pump Efficiency (%) = (Pump Output Power / Pump Input Power) × 100
Where:
- Pump Output Power = (Flow Rate × Head × Specific Gravity) / 3960
- Pump Input Power = (Motor Power × Motor Efficiency) / 746
In this equation, the flow rate is measured in gallons per minute (GPM), head in feet, specific gravity is unitless, and motor power is measured in horsepower (HP). The constants 3960 and 746 are used to convert units and ensure consistency.
Types of Pump Maintenance
Corrective Maintenance
Corrective maintenance, also known as reactive maintenance, involves repairing or replacing components after a pump failure has occurred. This type of maintenance is often more expensive and time-consuming, as it may result in unplanned downtime and potentially more extensive damage to the equipment.
Preventive Maintenance
Preventive maintenance is a scheduled approach to maintaining pumps, aimed at preventing failures and extending equipment life. It involves regular inspections, lubrication, and replacement of wear parts based on time or usage intervals. Preventive maintenance helps minimize unplanned downtime and reduces the risk of costly breakdowns.
Predictive Maintenance
Predictive maintenance uses condition monitoring techniques to assess the health of pumps and predict potential failures. This approach involves the use of sensors and monitoring devices to collect data on vibration levels, temperature, and other parameters. By analyzing this data, maintenance teams can identify issues before they lead to pump failures and schedule repairs accordingly.
Condition-Based Monitoring
Condition-based monitoring is a type of predictive maintenance that focuses on continuously assessing the condition of pumps in real-time. It involves the use of advanced sensors and analytics to detect anomalies and trends that may indicate potential problems. This approach allows for proactive maintenance interventions, minimizing downtime and optimizing pump performance.
Centrifugal Pump Components Maintenance
- Casing Volute: Inspect the casing for signs of wear, corrosion, or damage. Check for leaks and ensure proper alignment with the impeller.
- Bearings: Lubricate bearings according to the manufacturer’s recommendations. Monitor for excessive vibration or unusual noises, which may indicate bearing wear or damage.
- Impeller: Check the impeller for signs of wear, cavitation, or damage. Ensure proper clearance between the impeller and the casing to maintain efficient operation.
- Motor: Regularly inspect the motor for signs of overheating, vibration, or unusual noises. Ensure proper lubrication of motor bearings and check for proper alignment with the pump shaft.
- Shaft Seals: Check shaft seals for leaks or signs of wear. Replace seals as needed to prevent leaks and maintain pump efficiency.
Daily Maintenance Checklist
- Check lubricant levels and ensure they are within the recommended range specified in the pump manual.
- Inspect the pump for any signs of damage, corrosion, or excessive wear.
- Examine the shaft seals for any signs of wear or leakage.
- Check the coupling alignment and ensure it is within the acceptable levels.
- Monitor the pump’s vibration levels and compare them to the baseline readings.
- Inspect the pump’s flow rate and discharge pressures to ensure they are within the normal parameters.
- Check for any unusual noises or vibrations during operation.
- Ensure the pump is clean and free from debris or contamination.
- Verify that the pump’s operating hours are within the recommended limits.
Monthly Maintenance Checklist
- Perform a thorough visual inspection of the pump, including the casing, impeller, and bearings.
- Check the pump’s motor alignment and coupling for any signs of wear or misalignment.
- Inspect the pump’s bearings for any signs of wear, damage, or excessive vibration.
- Lubricate the pump’s bearings according to the manufacturer’s recommendations, using the correct lubricant.
- Check the pump’s mechanical seals for any signs of leakage or wear.
- Inspect the pump’s shaft for any signs of damage, corrosion, or excessive wear.
- Check the pump’s impeller for any signs of damage, erosion, or cavitation.
- Verify that the pump’s operating parameters, such as head pressure and flow rate, are within the acceptable levels.
- Inspect the pump’s motor for any signs of overheating, excessive vibration, or unusual noises.
Quarterly Maintenance Checklist
- Perform a comprehensive inspection of the pump’s components, including the casing, impeller, bearings, and seals.
- Check the pump’s alignment and adjust if necessary to ensure optimal performance and prevent premature wear.
- Inspect the pump’s coupling for any signs of wear, damage, or misalignment.
- Lubricate the pump’s bearings and coupling according to the manufacturer’s recommendations.
- Check the pump’s mechanical seals and replace if necessary to prevent leakage and ensure efficient operation.
- Inspect the pump’s motor windings for any signs of damage, overheating, or insulation breakdown.
- Test the pump’s safety devices, such as temperature and vibration sensors, to ensure they are functioning correctly.
- Verify that the pump’s operating parameters, such as power consumption and discharge pressure, are within the acceptable levels.
- Inspect the pump’s foundation and mounting for any signs of damage, corrosion, or looseness.
Annual Maintenance Checklist
- Perform a comprehensive overhaul of the pump, including disassembly, cleaning, and inspection of all components.
- Replace any worn or damaged components, such as bearings, seals, or impellers, to ensure optimal performance and prevent unexpected failures.
- Inspect the pump’s casing and volute for any signs of damage, erosion, or corrosion.
- Check the pump’s shaft alignment and straightness, and correct any issues to prevent vibration and premature wear.
- Lubricate the pump’s bearings and coupling according to the manufacturer’s recommendations, using high-quality lubricants.
- Test the pump’s motor insulation resistance and winding continuity to ensure electrical integrity.
- Calibrate the pump’s monitoring devices, such as pressure gauges and flow meters, to ensure accurate readings.
- Verify that the pump’s operating parameters, such as efficiency and vibration levels, are within the acceptable ranges.
- Inspect the pump’s piping and valves for any signs of damage, leakage, or obstruction.
- Document any maintenance activities performed, noting any issues, repairs, or replacements in the pump’s maintenance history.
Tips for Preventive Maintenance
Viscosity Index
The viscosity index indicates the change in viscosity of a lubricant with temperature. Using lubricants with a high viscosity index ensures that the oil maintains its lubricating properties across a wide range of operating temperatures.
Laser Alignments
Laser alignment tools provide precise measurements, ensuring that the shaft and motor are correctly aligned within the manufacturer’s specified tolerances.
Precision Rebuilds
When pumps undergo maintenance or repairs, it’s essential to use precision rebuilding techniques to restore them to their original specifications. This process involves replacing worn or damaged components with high-quality parts that meet the manufacturer’s tolerances.
Installation & Start-Up
Follow the manufacturer’s guidelines and industry best practices when installing pumps, including correct mounting, alignment, and piping connections. During start-up, monitor key parameters such as vibration levels, discharge pressures, and flow rates to ensure that the pump is operating within its design limits.
Vibration Monitoring
By regularly measuring and analyzing vibration levels, you can identify problems such as misalignment, imbalance, bearing wear, and cavitation. Establishing baseline vibration readings and setting alert levels allows you to track changes over time and schedule maintenance activities proactively.
Training
Properly trained staff can identify potential issues, perform routine maintenance tasks correctly, and make informed decisions regarding pump operation and repairs. Training should cover topics such as pump fundamentals, maintenance best practices, troubleshooting techniques, and safety procedures.
Hire outside Help When Needed
For complex pump systems or when faced with unfamiliar issues, consider hiring professional pump maintenance services. These experts can provide valuable insights and assistance in developing and implementing effective preventive maintenance plans.
Factors to Determine the Frequency
Several factors should be considered when determining the frequency of preventive maintenance for pumps:
- Degradation Process: Understanding the degradation process of pump components helps determine the appropriate maintenance intervals. Factors such as wear, corrosion, and fatigue should be considered.
- Failure Developing Period (FDP): The FDP is the time between the onset of a potential failure and the actual failure. Knowing the FDP for critical components helps schedule maintenance tasks before failures occur.
- Inspection Tools: The availability and capability of inspection tools influence the frequency of maintenance tasks. More advanced tools may allow for longer intervals between inspections.
- Person’s Ability and Environment: The skill level of maintenance personnel and the working environment should be considered when determining maintenance frequencies. Harsh environments or less experienced staff may require more frequent maintenance.
- Component Life and Criticality: The expected life of pump components and their criticality to the overall system should be factored into maintenance frequencies. Critical components with shorter lifespans may require more frequent attention.