Seals are vital components in machinery that prevent leaks and ensure optimal performance. However, using the wrong type of seal – static or dynamic – can lead to costly failures, extended downtime, and potential safety hazards.
This post will explain the important factors that differentiate static and dynamic seals to help guide your decision-making process.
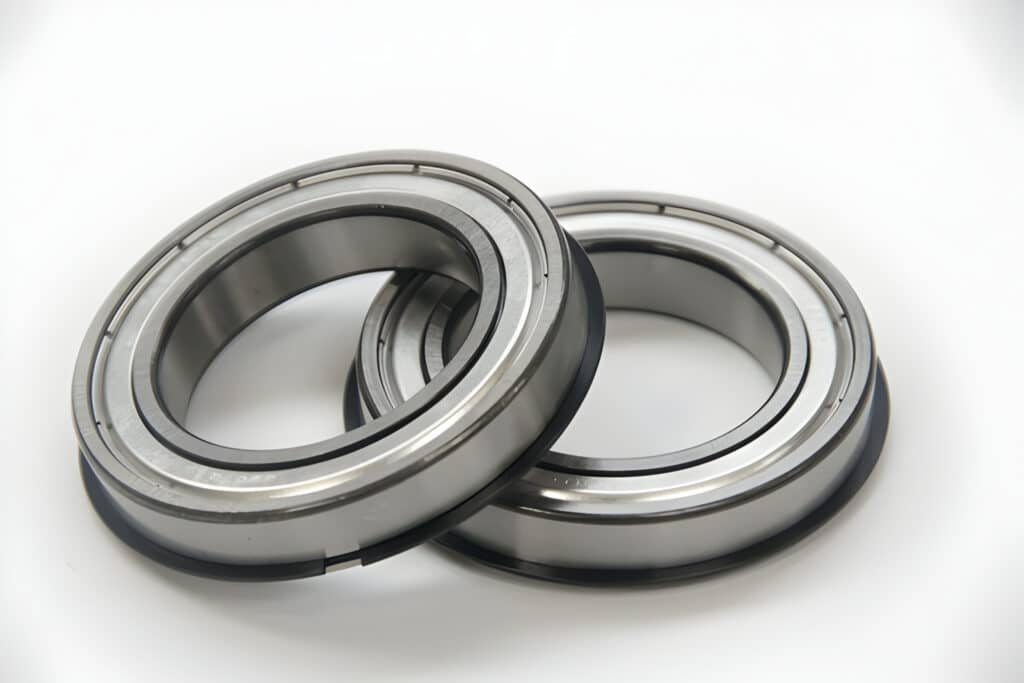
What is a Static Seal
A static seal is a type of seal that prevents leakage between two surfaces that do not move relative to each other. Static seals are designed to be compressed between two stationary mating surfaces, creating an impenetrable barrier that stops fluid from escaping the system. These seals rely on compression and deformation of the sealing material to block potential leak paths.
What is a Dynamic Seal
Dynamic seals are designed to prevent leakage between components that move relative to each other, such as rotating shafts or reciprocating rods. These seals must contain fluid while accommodating motion, making their design and application more challenging than static seals.
Key Differences Between Static and Dynamic Seals
Leak Rate
Static seals are designed to have minimal to zero leakage, as they are used in applications where any leakage is unacceptable, such as in high-vacuum or high-pressure systems.
Dynamic seals, due to the inherent challenges posed by relative motion, typically have higher leak rates compared to static seals.
Relative Motion
Static seals operate with no movement relative to their mating surface.
Dynamic seals must accommodate continuous or intermittent motion, such as reciprocating, oscillating, or rotary action, while maintaining a tight seal.
Extrusion Risk
The motion in dynamic sealing also creates a risk of seal extrusion, where the seal material is squeezed or pushed into the clearance gap between components. Extrusion can cause seal damage, leaks, and premature failure. To mitigate this risk, dynamic seals often require backup rings or special geometries.
Static seals are not subject to extrusion due to the lack of motion.
Friction
Dynamic seals inherently generate friction as they rub against their mating surface. This friction results in heat buildup, seal wear, and energy losses.
Static seals, not having any sliding motion, produce minimal friction.
Cost
The complexities of dynamic sealing generally make dynamic seals more expensive than comparable static seals. Factors like precision manufacturing, tight tolerances, anti-extrusion features, and high-performance materials contribute to the higher cost of dynamic seals.
Lifespan
The service life of dynamic seals is typically shorter than that of static seals. The wear and tear from continuous motion and friction gradually degrade dynamic seals, necessitating regular inspection and replacement to prevent leaks.
Static seals can often last the lifetime of the assembly, barring material degradation from age or environment.
Compression Tolerance
Static seals are more forgiving of compression variations or flange surface irregularities. They can tolerate a wider range of compression without leaking.
Dynamic seals require tighter control of compression to maintain sealing without causing excessive friction.
Velocity Limit
The surface speed between the seal and its mating component is a limiting factor for dynamic seals. Exceeding the velocity limit can cause rapid wear, overheating, and seal failure. Each dynamic seal design has a maximum allowable velocity based on its material and operating conditions.
Static seals have no inherent velocity limit.
Maintenance
The wear and shorter lifespan of dynamic seals necessitate more frequent maintenance compared to static seals. Regular inspection, lubrication, and replacement are needed to ensure reliable performance.
Static seals generally require less upkeep, mainly monitoring for deterioration due to age or chemical attack.
Material Selection
While both static and dynamic seals can employ elastomers and polymers, dynamic seals often demand higher-grade materials to withstand motion and friction. Properties like wear resistance, low friction, and high temperature stability are a priority. Seal materials must also be compatible with the media being sealed and the environmental conditions.
Static seal materials can be selected mainly based on chemical compatibility and durometer.
Gland Design
The gland or cavity that holds the seal is designed differently for static and dynamic applications. Dynamic seal glands must account for the motion of the shaft or bore, providing space for the seal to flex and avoid extrusion. They may incorporate special geometries like back-up rings, anti-extrusion lips, or D-shaped cavities.
Static seal glands are typically simpler, focusing on compression and retention of the seal.