Centrifugal pumps are widely employed in various industrial applications for efficient fluid transportation. However, these machines are susceptible to several common issues that can hinder their performance and lead to unplanned downtime.
In this blog post, we will delve into the prevalent problems associated with centrifugal pumps and explore strategies to mitigate these challenges. By addressing these issues proactively, industrial facilities can enhance the reliability and longevity of their pumping systems.
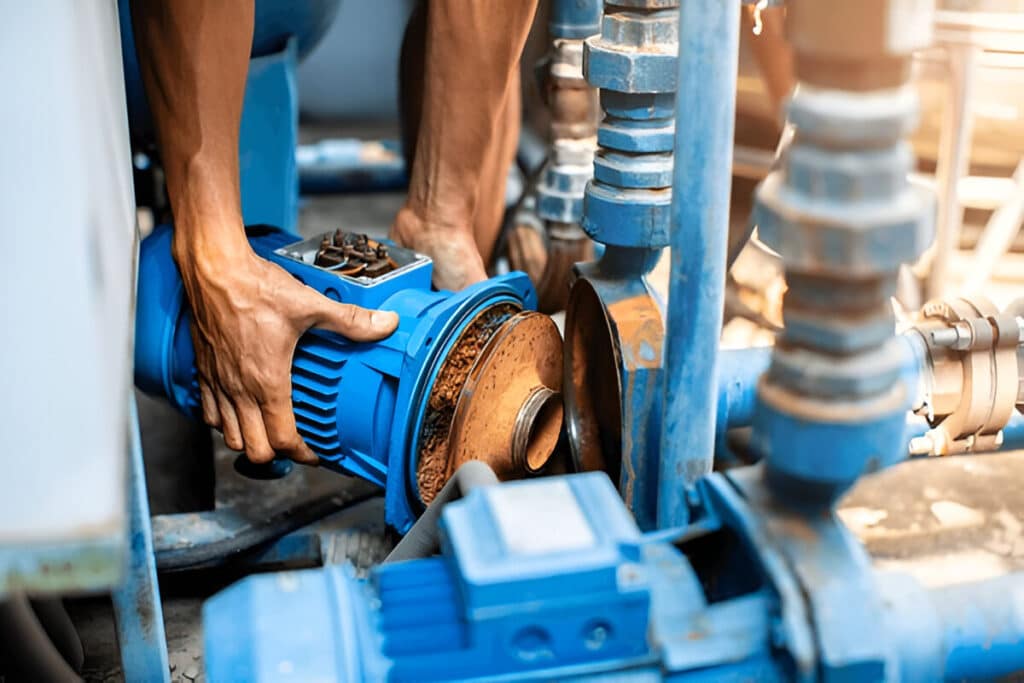
Common Centrifugal Pump Problems and Solutions
Pump Running Dry
One of the most common issues faced by centrifugal pump operators is a pump running dry. This occurs when the pump is not receiving enough liquid from the suction source, causing it to operate without proper lubrication and cooling. Running dry can lead to severe damage to pump internals, including seals, bearings, and impellers.
- To prevent this issue, ensure that the suction pipe is always submerged in the liquid and that there are no air leaks in the suction line.
- Monitor the fluid level in the suction source and maintain it above the minimum required level.
- Install a low-level switch or sensor to automatically shut off the pump if the liquid level drops below a critical point.
Reduced Flow Rate
A decrease in the pump’s flow rate can indicate several issues, such as a clogged suction filter, a partially closed suction valve, or air pockets in the suction pipeline. Reduced flow can also result from worn impellers, incorrect impeller clearances, or a damaged or defective impeller.
- To address reduced flow, start by checking the suction side of the pump.
- Clean any clogged filters and ensure that valves are fully open. Inspect the suction piping for air leaks and eliminate any air pockets.
- If the issue persists, examine the impeller for signs of wear, damage, or debris accumulation.
- Adjust impeller clearances according to the manufacturer’s specifications and replace the impeller if necessary.
Reversed Impeller Rotation
Centrifugal pumps are designed to operate with a specific rotational direction. If the impeller rotates in the wrong direction, the pump will not generate the required head and flow. This issue can occur due to incorrect electrical connections or a phase reversal in the power supply.
- To correct reversed impeller rotation, first, verify the correct rotational direction as indicated by the arrow on the pump casing.
- Then, check the electrical connections and ensure that they are properly wired.
- If the issue persists, consult with an electrician to investigate any potential issues with the power supply, such as phase reversal.
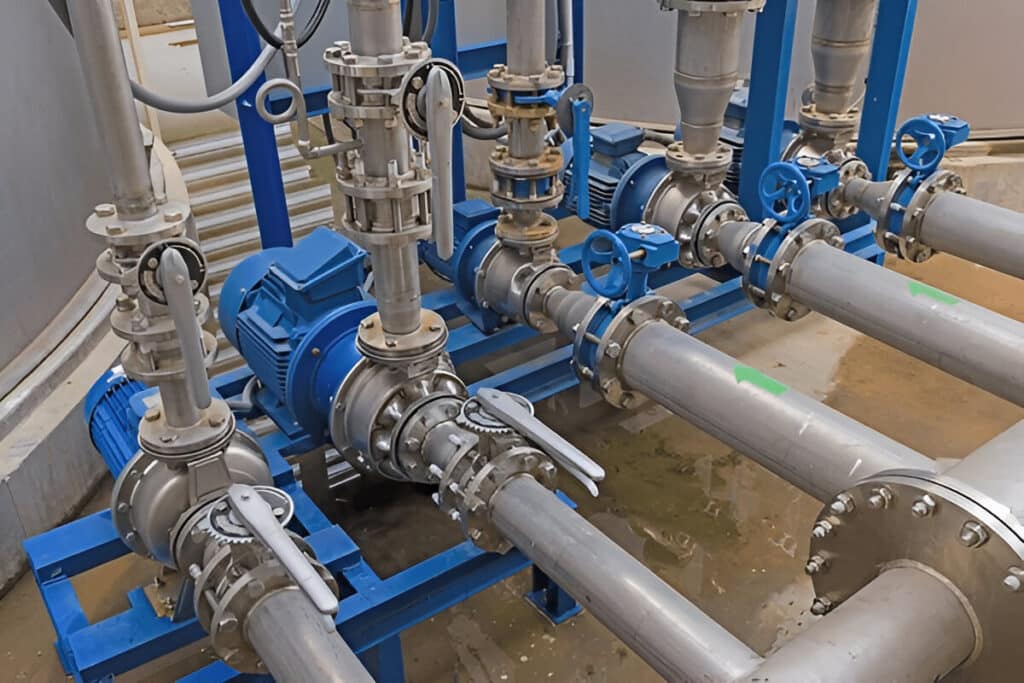
Pump Seizure
Pump seizure occurs when the rotating components of the pump, such as the impeller or shaft, become stuck and unable to turn. This can happen due to various reasons, including bearing failure, excessive wear, or the presence of foreign objects in the pump.
- If the pump has seized, immediately shut off the power supply to prevent further damage.
- Disassemble the pump and inspect the bearings, wear rings, and other critical components for signs of wear or damage.
- Replace any worn or damaged parts and ensure that the pump is properly reassembled and aligned before restarting.
Overheating
Excessive heat generation in a centrifugal pump can lead to premature failure of bearings, seals, and other components. Overheating can result from various factors, such as insufficient lubrication, improper bearing cooling, or operating the pump at low flow conditions.
- To mitigate overheating, ensure that the pump is adequately lubricated and that the bearing cooling system is functioning properly.
- Monitor bearing temperatures regularly and maintain them within the manufacturer’s recommended range.
- Avoid operating the pump at low flow conditions for extended periods, as this can cause recirculation and heat buildup within the pump.
Air Ingress
Air ingress is a common issue in centrifugal pumps that can lead to reduced flow rate, increased vibration, and cavitation. Air can enter the pump through various points, including the suction pipe, mechanical seals, and stuffing box.
- To prevent air ingress, ensure that all connections in the suction piping are airtight and properly sealed.
- Check for any visible leaks or cracks in the suction line and repair them promptly.
- Verify that the suction pipe is submerged sufficiently below the liquid level to prevent vortexing and air entrainment.
Vibration
Excessive vibration in centrifugal pumps can be caused by several factors, including improper alignment, unbalanced impellers, worn bearings, and cavitation. Vibration can lead to premature wear of pump components, seal failure, and reduced pump efficiency.
- To address vibration issues, start by checking the alignment of the pump and motor.
- Ensure that the pump is properly aligned with the motor shaft and that the coupling is in good condition.
- Inspect the impeller for signs of wear, damage, or imbalance. An unbalanced impeller can cause significant vibration and should be replaced or balanced by a professional.
- Check the bearings for excessive wear or damage and replace them if necessary.
- Ensure that the bearings are properly lubricated and cooled to prevent premature failure.
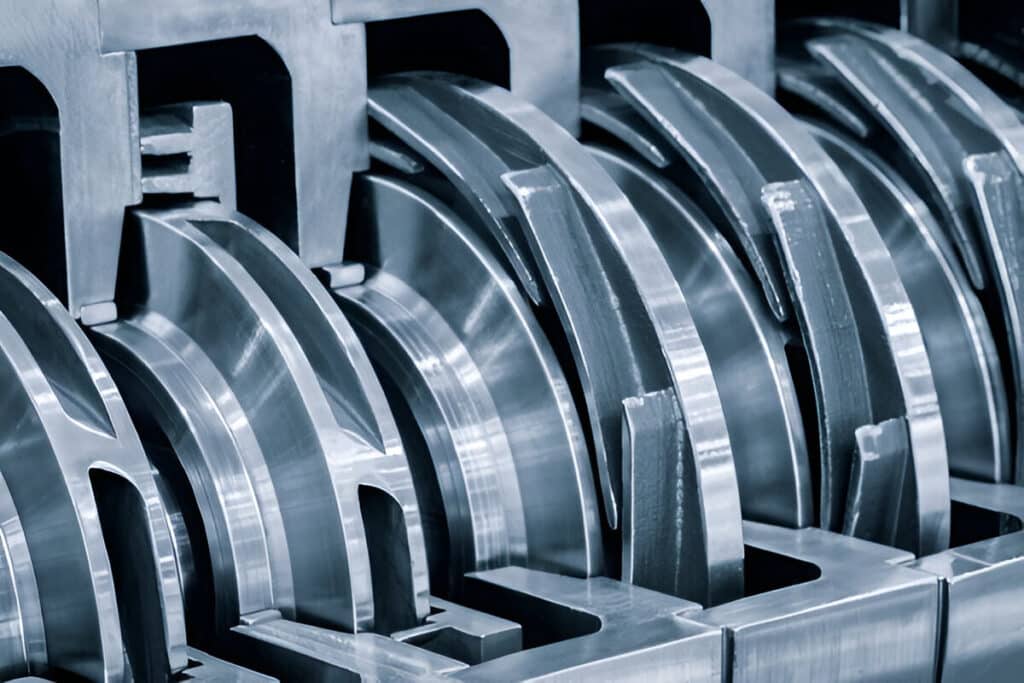
Cavitation
Cavitation occurs when the pressure in the pump falls below the vapor pressure of the liquid, causing vapor bubbles to form and collapse within the pump. This can lead to reduced flow rate, increased vibration, and damage to pump internals.
- To prevent cavitation, ensure that the pump has sufficient net positive suction head (NPSH) available. This can be achieved by increasing the suction head, reducing the suction lift, or increasing the diameter of the suction piping.
- Check the suction strainer or filter for clogging and clean it regularly to maintain adequate flow.
- Verify that the suction valve is fully open and that there are no restrictions in the suction line.
- Operate the pump within its recommended flow range and avoid running the pump at low flow rates for extended periods.
Debris in Pump
Debris entering the pump can cause clogging, reduced flow rate, and damage to pump internals.
- To prevent debris from entering the pump, install a suction strainer or filter with the appropriate mesh size for the liquid being pumped.
- Regularly inspect and clean the strainer or filter to ensure it remains unobstructed.
- If debris has already entered the pump, it may be necessary to disassemble the pump and manually remove the debris.
- Inspect the impeller, wear rings, and other internal components for signs of wear or damage and replace them if necessary.
- Consider installing a debris separator or settling tank upstream of the pump to remove larger particles before they enter the pump.
Slow Pump Re-Priming
Slow pump re-priming can occur when air pockets form in the suction line or pump casing, preventing the pump from establishing proper suction. This can be caused by air leaks in the suction piping, insufficient suction head, or a faulty foot valve.
- To improve pump re-priming, ensure that the suction piping is airtight and properly sealed. Check for leaks in the suction line and repair them promptly.
- Verify that the suction pipe is submerged sufficiently below the liquid level to prevent air entrainment.
- Install a foot valve at the end of the suction line to maintain prime and prevent backflow when the pump is not running.
- Consider installing a self-priming centrifugal pump or a priming assist device, such as a vacuum pump or ejector, to facilitate faster and more reliable priming.
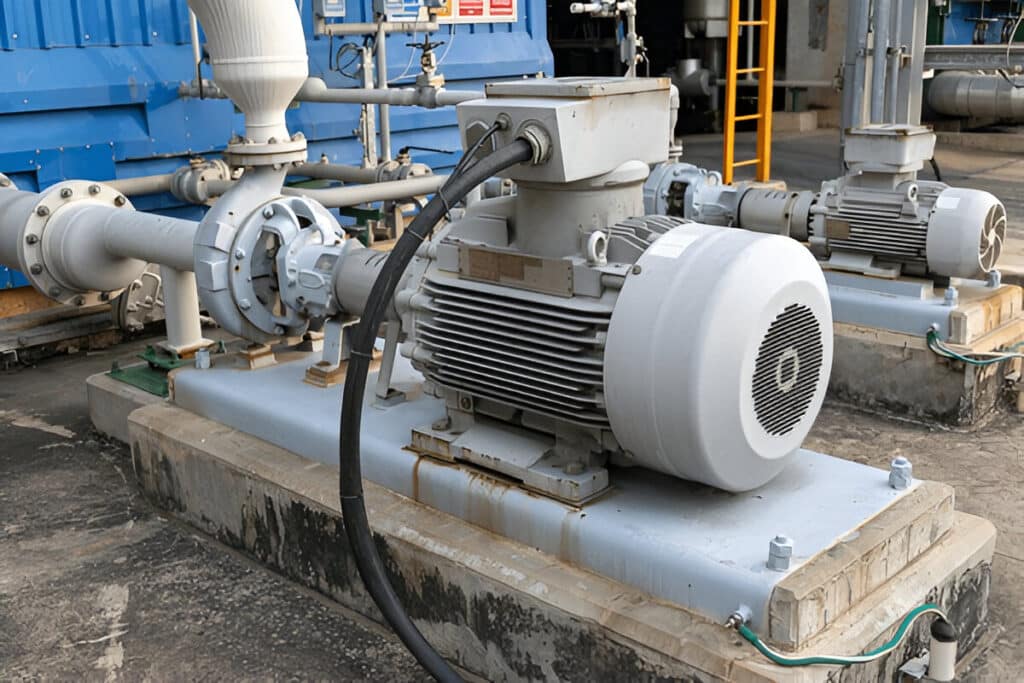
Excess Noise
Excessive noise from a centrifugal pump can indicate several issues, such as worn bearings, cavitation, or improper installation. Worn bearings can cause mechanical noise and vibration, leading to premature failure if not addressed promptly.
- Ensure bearings are properly lubricated and replace them if necessary.
- Cavitation occurs when vapor bubbles form in the pumped liquid due to low pressure, causing a characteristic rumbling noise. To mitigate cavitation, check that the suction pipe is adequately sized, the suction lift is not excessive, and the liquid level in the suction source is sufficient.
- Improper installation, such as misalignment or inadequate supports, can also lead to excess noise. Verify that the pump and motor are correctly aligned and the pump feet are securely fastened to the foundation.
Pump Driver Overloaded
An overloaded pump driver, typically an electric motor, can be caused by several factors. Excessive power draw may indicate an issue with the pump internals, such as worn wear rings or incorrect impeller clearance.
- Inspect the impeller and wear rings for signs of wear and adjust the clearance if needed. Abnormal vibration can also cause the motor to work harder, leading to overloading.
- Check for excessive vibration and address any issues with alignment, balance, or worn components.
- Fluid contamination or changes in fluid properties can increase the power requirement. Ensure the pumped fluid matches the pump specifications and install appropriate filtration if necessary.
- Lastly, verify that the motor is correctly sized for the pump and operating conditions.
Fluid Leaks
Fluid leaks in centrifugal pumps commonly occur at the mechanical seals or stuffing box. Worn or damaged seals can allow fluid to escape, leading to reduced pump performance and potential environmental hazards.
- Regularly inspect seals for signs of wear or damage and replace them as needed.
- Ensure that the seal faces are properly lubricated and cooled by the pumped fluid.
- For pumps with packing, check that the gland nuts are properly adjusted to allow a small amount of controlled leakage. Over-tightening the gland nuts can cause excessive heat and damage the packing.
- Leaks can also occur at flanged connections or due to cracks in the pump casing. Inspect gaskets and flanges for signs of damage or improper sealing, and replace or repair as necessary.
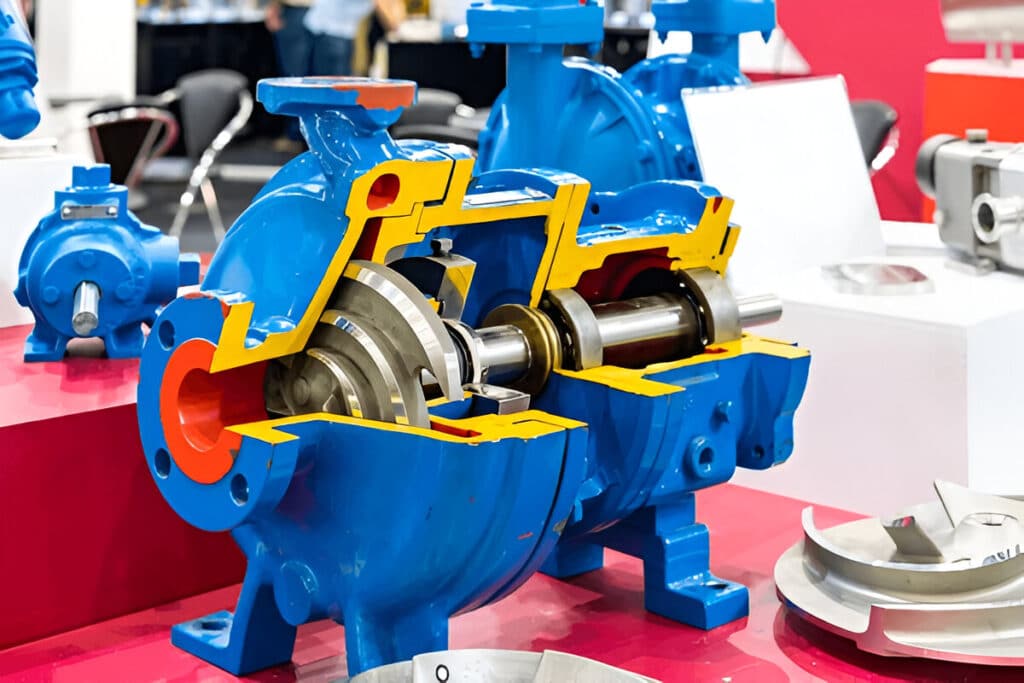
Fluid Contamination
Fluid contamination can cause a range of issues in centrifugal pumps, from reduced performance to complete failure. Abrasive particles can erode pump internals, such as the impeller and wear rings, leading to decreased efficiency and increased clearances.
- Install appropriate filtration or strainers on the suction side to capture contaminants before they enter the pump.
- Regularly clean or replace filters to maintain their effectiveness. Chemical contamination can cause corrosion or degradation of pump components, particularly in pumps handling aggressive fluids.
- Ensure that the pump materials are compatible with the pumped fluid and implement proper monitoring and maintenance practices.
- Biological growth, such as algae or bacteria, can clog the impeller or suction strainer, reducing flow and increasing power consumption. Treat the fluid with appropriate biocides or implement regular cleaning procedures to control biological growth.
- Lastly, air entrainment can lead to cavitation and reduced pump performance. Identify and eliminate sources of air leaks in the suction line or low fluid levels in the suction source.
Motor Failure
Motor failure is one of the most common problems encountered in centrifugal pump systems. The motor is the driving force behind the pump, and any issues with it can lead to reduced performance or complete pump failure. Overheating is a primary cause of motor failure, which can result from insufficient lubrication, excessive friction, or bearing wear. Electrical faults, such as short circuits or winding damage, can also cause motor failure.
- To prevent motor issues, ensure the correct motor size is selected for the pump’s power requirements and maintain proper lubrication levels.
- Regular monitoring of bearing temps and vibration can help detect potential problems early.
Energy Inefficiency
Centrifugal pumps can consume significant amounts of energy, making efficiency a key concern. Factors contributing to energy inefficiency include incorrect pump selection, improper sizing, and poor system design. Operating a pump at a flow rate far from its best efficiency point (BEP) can result in increased power consumption and reduced performance. Impeller wear, cavitation, and excessive friction losses in the suction and discharge piping can also lead to energy inefficiency.
- To optimize energy usage, select a pump that matches the system requirements, ensure proper sizing of suction and discharge piping, and perform regular maintenance to keep pump internals in good condition.
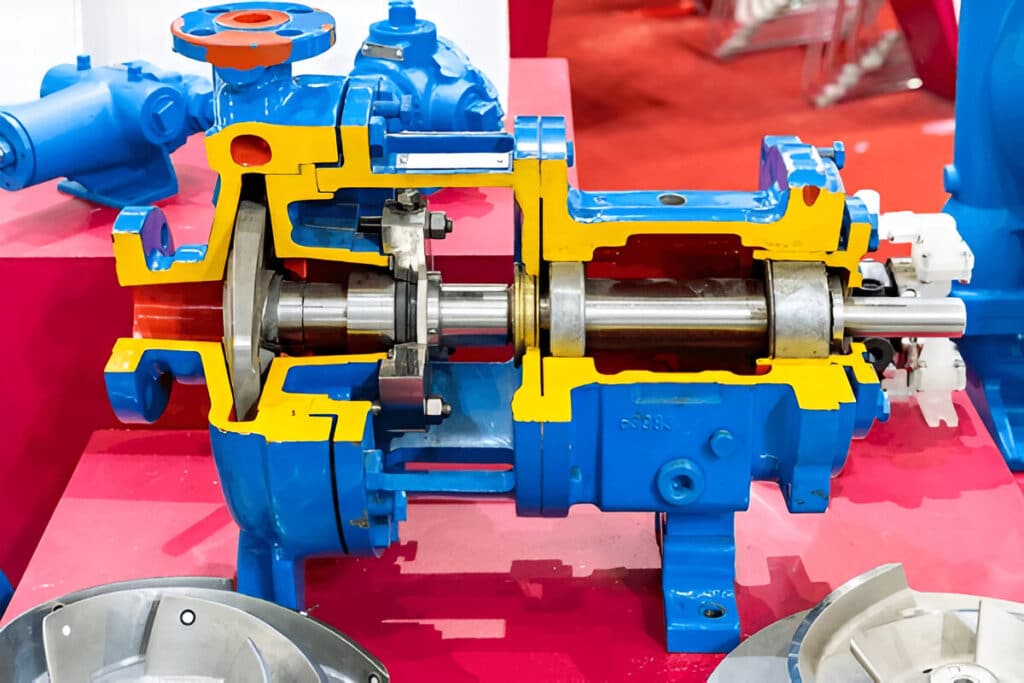
Prime Loss
Prime loss occurs when air enters the suction line, causing the pump to lose its ability to draw liquid from the suction source. This can happen due to various reasons, such as air leaks in the suction piping, insufficient suction head, or low liquid levels in the suction tank. When a pump loses prime, it may run dry, leading to damage to the mechanical seals and other internal components.
- To prevent prime loss, ensure adequate suction pressure, check for air leaks in the suction line, and maintain sufficient liquid levels in the suction source.
- Installing a foot valve or check valve in the suction piping can help maintain prime during intermittent pump runs.
Chemical Compatibility Issues
Centrifugal pumps are used in various industrial applications, often involving the transfer of chemicals and aggressive fluids. Chemical compatibility issues can arise when the pump materials are not suitable for the pumped fluid, leading to corrosion, erosion, or premature failure of pump components. Incompatible fluids can cause degradation of pump seals, gaskets, and other critical components, resulting in leaks and reduced performance.
- To avoid chemical compatibility problems, select pumps with materials that are compatible with the pumped fluid.
- Consider factors such as temperature, concentration, and pH when choosing pump materials.
- In some cases, specialized coatings or liners may be required to protect the pump internals from aggressive chemicals.
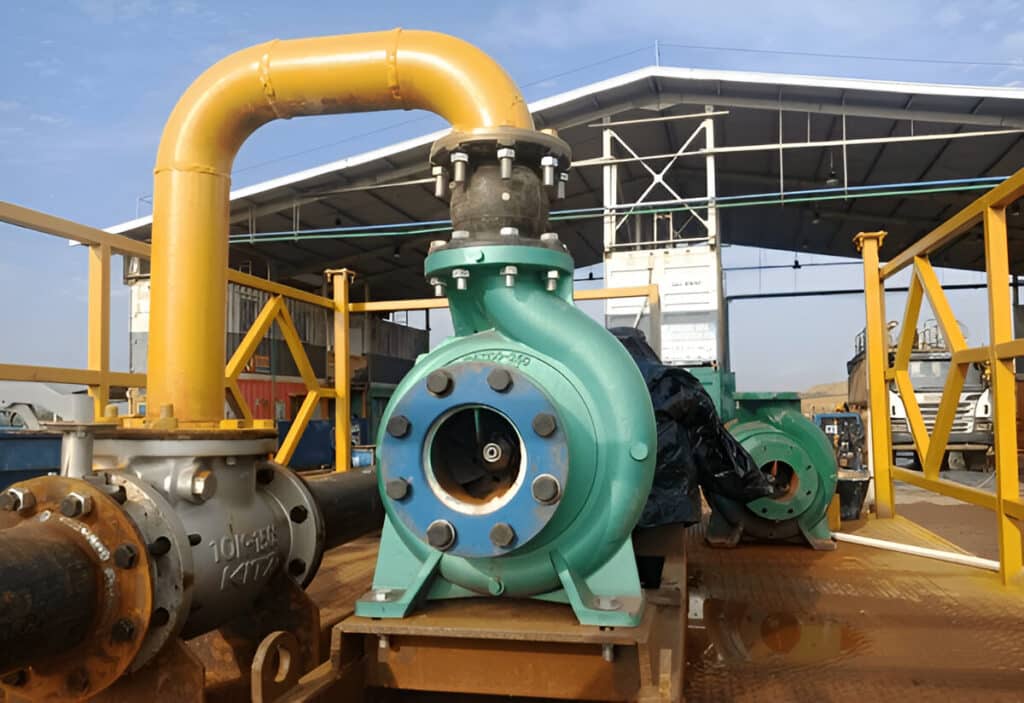
Centrifugal Pump Troubleshooting Steps
Step 1: Check Pump Rotation
One of the first steps in troubleshooting centrifugal pumps is to verify the correct rotational direction. To check the rotation, locate the arrow on the pump casing that indicates the proper rotational direction. Then, briefly start the motor and observe the direction of shaft rotation. If the impeller rotates in the wrong direction, swap any two of the three phase leads in the motor terminal box.
Step 2: Inspect Suction Piping
Inspect the suction line for any signs of leaks, as air entering the suction pipe can cause air pockets, leading to reduced flow and cavitation. Ensure that the suction piping is properly sized and installed with a minimum number of elbows and fittings to minimize friction losses. Check the depth of suction pipe submergence to ensure adequate suction pressure and prevent vortexing. Clean the suction strainer or filter to remove any accumulated debris that may restrict flow.
Step 3: Assess Impeller Condition
Visually inspect the impeller for signs of wear, damage, or clogging. Ensure that the impeller is properly balanced to minimize vibration and extend bearing life. Adjust the impeller clearance as needed to maintain optimal performance and efficiency.
Step 4: Check for Cavitation
To troubleshoot cavitation, check the suction pressure and ensure it is sufficient to prevent vaporization. Verify that the liquid level in the suction source is adequate and that the suction piping is free from restrictions. Consider increasing the suction pipe diameter or reducing the suction lift to improve suction conditions.
Step 5: Monitor Bearing and Seal Condition
Regularly lubricate bearings with the proper type and quantity of lubricant, following the manufacturer’s recommendations. Inspect mechanical seals for signs of leakage, and replace worn or damaged seals promptly to prevent fluid contamination and air ingress. Ensure that the seal flush lines are clear and functioning properly to provide adequate cooling and lubrication to the seals.
Step 6: Evaluate System Conditions
Assess the discharge piping for any restrictions, such as partially closed valves or blockages, that can increase the system head and reduce flow. Verify that the actual head and flow rate match the pump’s design specifications. Check for any changes in fluid properties, such as viscosity or specific gravity, which can affect pump performance. Ensure that the motor is sized correctly for the power requirements of the pump and that the electrical supply is stable and within the specified voltage range.