What are the different types of centrifugal pumps? Centrifugal pumps are widely used in various industries for fluid transfer applications.
In this blog post, we’ll explore the main types of centrifugal pumps and their unique characteristics.
By the end, you’ll have a clear understanding of which centrifugal pump type best suits your specific needs, helping you make an informed decision for your pumping system.
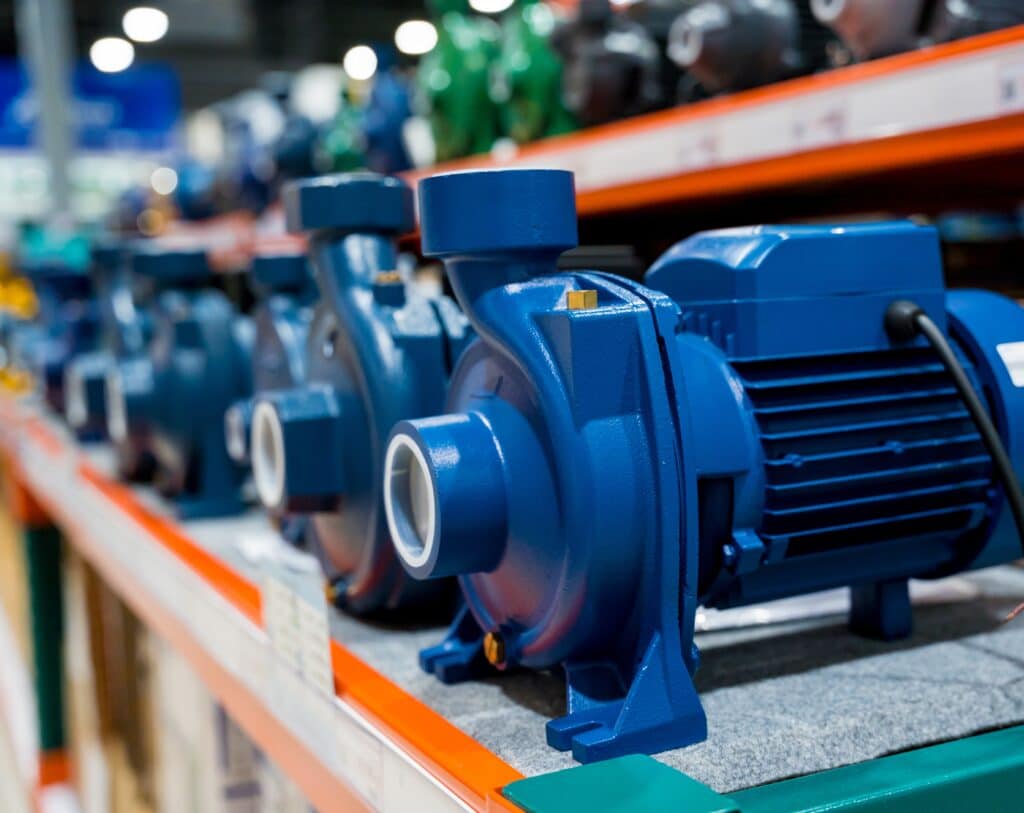
By Flow Direction
Radial Flow Pumps
Radial flow pumps, also known as centrifugal pumps, move fluid radially outward from the impeller. As the impeller rotates, it accelerates the fluid and directs it perpendicularly away from the shaft, creating a high-velocity flow.
Axial Flow Pumps
Axial flow pumps propel fluid along the same axis as the impeller shaft. The impeller blades are designed to guide the fluid in a direction parallel to the shaft, resulting in a high-volume, low-pressure flow.
Mixed Flow Pumps
Mixed flow pumps combine the characteristics of both radial and axial flow pumps. The impeller design allows for fluid movement in both radial and axial directions, providing a balance between the high-pressure output of radial flow pumps and the high-volume flow of axial flow pumps.
By Shaft Orientation
Horizontal Centrifugal Pumps
Horizontal centrifugal pumps are the most common type of centrifugal pump. They feature a shaft mounted horizontally, with the impeller and motor positioned on either end.
This design allows for easy maintenance and a wide range of applications, making them a popular choice in many industries.
Vertical Centrifugal Pumps
Vertical centrifugal pumps have their shafts oriented vertically, with the impeller located at the bottom and the motor at the top. This configuration is ideal for applications where floor space is limited or when the pump needs to be installed in a sump or pit.
Vertical pumps are often used in deep well and underwater applications, as they can be easily submerged.
Submersible Centrifugal Pumps
Submersible centrifugal pumps are designed to operate completely submerged in the liquid being pumped. The motor and impeller are housed together in a single, watertight unit.
These pumps are commonly used in applications such as sewage treatment, drainage, and underwater excavation, where the pump must be able to function reliably in harsh, submerged conditions.
By Number of Stages
Single-Stage Centrifugal Pumps
Single-stage centrifugal pumps feature a single impeller that transfers energy to the fluid, increasing its velocity and pressure. These pumps are well-suited for applications requiring moderate head and flow rates.
Single-stage pumps are known for their simplicity, compact design, and cost-effectiveness. They are commonly used in various industries, such as water supply, irrigation, and chemical processing.
Multi-Stage Centrifugal Pumps
Multi-stage centrifugal pumps consist of two or more impellers arranged in series, allowing them to generate higher head and pressure than single-stage pumps. Each stage incrementally increases the fluid’s energy, making these pumps ideal for high-pressure applications.
The multiple stages enable the pump to overcome greater resistance and achieve higher discharge pressures. Multi-stage pumps are frequently employed in deep well pumping, boiler feed systems, and high-pressure industrial processes.
The number of stages in a multi-stage pump depends on the specific head and pressure requirements of the application. By adding more stages, the pump can generate higher pressures while maintaining a relatively compact design compared to using a larger single-stage pump.
By Impeller Design
Closed Impeller
Closed impellers feature vanes that are encased between two discs, forming enclosed passages for the fluid. This design offers higher efficiency and is suitable for clean liquids without solids or abrasive particles.
Closed impellers are ideal for applications requiring high pressure and flow rates.
Semi-Open Impeller
Semi-open impellers have vanes that are open on one side and attached to a single disc on the other. This design allows for better handling of liquids with some solids or slurries compared to closed impellers.
The semi-open design also simplifies maintenance and cleaning procedures.
Open Impeller
Open impellers consist of vanes attached to a central hub without any enclosing discs. This design is best suited for pumping liquids with high solid content, slurries, or viscous fluids.
Open impellers are less efficient than closed or semi-open designs but offer excellent solids handling capabilities and ease of maintenance.
Special Types of Centrifugal Pumps
Self-Priming Pumps
Self-priming pumps are designed to automatically remove air from the suction line and create a vacuum, allowing them to prime themselves without manual intervention. This unique feature makes them ideal for applications where the pump is located above the fluid level or when the suction line may contain air pockets.
Magnetic Drive Pumps
Magnetic drive pumps use a magnetic coupling to transmit power from the motor to the impeller, eliminating the need for a mechanical seal. This sealless design prevents leaks and minimizes maintenance requirements, making them suitable for handling hazardous, toxic, or expensive fluids.
Canned Motor Pumps
Canned motor pumps feature a motor that is completely enclosed and sealed within a stainless steel “can.” The pumped fluid circulates around the motor, providing cooling and lubrication. This design is ideal for applications involving high-temperature, high-pressure, or ultra-pure fluids.
Immersed Pumps
Immersed pumps, also known as submersible pumps, are designed to be fully submerged in the pumped fluid. They are commonly used in applications such as wastewater treatment, drainage, and dewatering. Immersed pumps offer several advantages, including compact design, quiet operation, and the ability to handle solids-laden fluids.
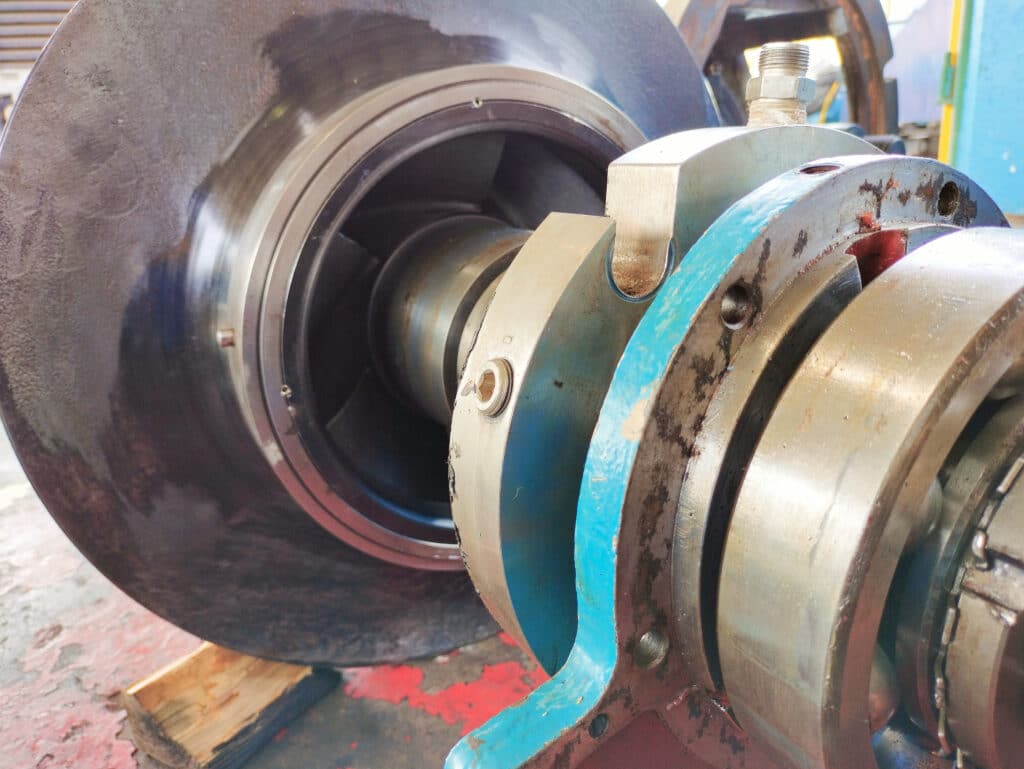
Selection Criteria for Centrifugal Pumps
Fluid properties: viscosity, temperature, corrosiveness
When selecting a centrifugal pump, consider the fluid’s viscosity, as high-viscosity liquids require more power to pump and may necessitate specialized impeller designs.
Evaluate the fluid’s temperature range, as extreme temperatures can affect pump materials and sealing components.
Assess the fluid’s corrosiveness to ensure the pump’s materials are compatible and resistant to chemical attack, preventing premature wear and failure.
System requirements: flow rate, pressure head, efficiency
Determine the required flow rate and pressure head for the system to select a pump that meets these parameters effectively. Consider the pump’s efficiency, as higher-efficiency pumps can reduce energy consumption and operating costs over time.
Analyze the system’s pipeline layout, including suction and discharge conditions, to ensure the selected pump can overcome any restrictions or losses.
Reliability and maintenance considerations
Prioritize pumps with proven reliability records and robust construction to minimize downtime and ensure consistent performance. Consider the availability of spare parts and the ease of maintenance for the selected pump.
Evaluate the pump’s design features, such as seal type, bearing arrangement, and coupling, which can impact its reliability and maintenance requirements.
Life cycle costs: initial investment and operating expenses
Assess the initial investment cost of the pump, including purchase price, installation, and commissioning expenses. Evaluate the long-term operating costs, such as energy consumption, maintenance, and repair expenses, over the pump’s expected lifespan.
Consider the potential for energy savings through the use of variable frequency drives (VFDs) or other efficiency-enhancing technologies, which can reduce overall life cycle costs.
In conclusion
Centrifugal pumps come in various types, each designed for specific applications and requirements. Understanding the differences between these types is crucial for selecting the most suitable pump for a given task.
For expert guidance on choosing the right centrifugal pump, contact our team of experienced professionals today.