Static seals are critical components in machinery, but they often get overlooked. Inadequate seals can lead to leaks, contamination, and equipment failure.
Ignoring the importance of static seals can result in costly repairs, unplanned downtime, and even safety hazards. Left unaddressed, seal problems can escalate and cause significant damage to your machinery.
In this blog post, we’ll explore the key considerations for selecting and maintaining static seals in the machinery industry.
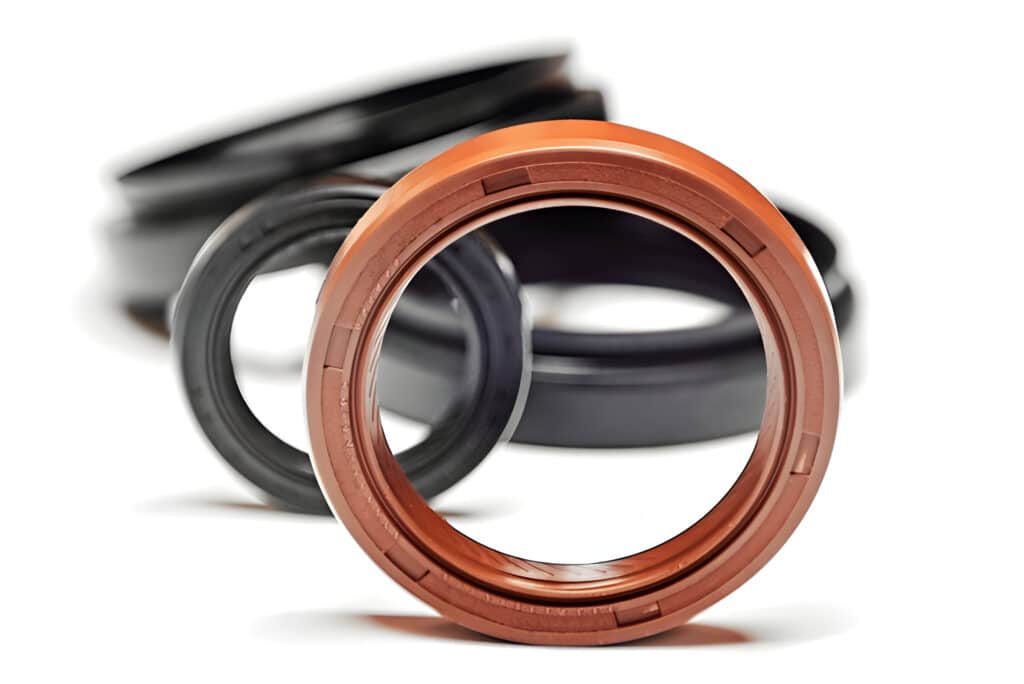
What are Static Seals
Static seals are fixed sealing elements that create a barrier between two stationary surfaces to prevent leakage of fluids or gases. Unlike dynamic seals that contain moving parts, static seals maintain a leak-proof junction between two components that do not move relative to each other. The primary purpose of a static seal is to provide a tight and reliable seal at the interface of two mating surfaces.
Forces on Static Seals
Initial Compression
Initial compression, also known as squeeze or assembly force, is the compressive force applied to the seal during installation. When a static seal is fitted between two mating surfaces, it undergoes compression that squeezes the seal material and initiates a sealing effect.
System Pressure Activation
Once a static seal is installed and the system is pressurized, the seal is subjected to system pressure activation. The fluid or gas pressure within the system acts on the seal, further increasing the contact stress between the seal and the mating surfaces. This pressure activation enhances the sealing effect and helps maintain a leak-tight joint.
Types of Static Seals
Static seals can be categorized into two main types based on their orientation and function:
Static Axial Seals
Static axial seals are used between two surfaces that are perpendicular to the axis of the seal. Some common examples of static axial seals include:
- Flange Gaskets: Flat gaskets used between two flanges to prevent leakage.
- O-Rings: Round, elastomeric seals with a circular cross-section. O-rings are compressed between two surfaces to create a leak-proof seal.
- Crush Seals: Soft, deformable metal seals that are crushed between two surfaces to create a leak-tight joint. Crush seals are often used in high-pressure, high-temperature applications where elastomeric seals are not suitable.
Static Radial Seals
Static radial seals are used between two surfaces that are parallel to the axis of the seal. Examples of static radial seals include:
- Piston Seals: Seals used on the periphery of a piston to prevent leakage between the piston and the cylinder bore.
- Rod Seals: Seals used around a rod or shaft to prevent leakage where the rod enters or exits a housing.
- Cap/Plug Seals: Seals used to seal openings or ports in a housing or component. Cap and plug seals can be threaded, press-fit, or retained by other means.
Materials in Static Seals
Elastomeric Compounds
- Nitrile Rubber (NBR): A general-purpose elastomer with good resistance to oils, fuels, and hydraulic fluids. NBR is suitable for temperatures ranging from -30°C to 100°C.
- Fluorocarbon (FKM): An elastomer with excellent resistance to high temperatures, chemicals, and aggressive fluids. FKM seals can operate in temperatures ranging from -20°C to 200°C.
- Perfluoroelastomer (FFKM): A high-performance elastomer with exceptional chemical resistance and thermal stability. FFKM seals can withstand temperatures up to 325°C and are resistant to nearly all chemicals.
Metallic and Composite Materials
- Aluminum: Soft, ductile metal seals that conform well to mating surfaces. Aluminum seals are often used in low-pressure applications or as backup rings for elastomeric seals.
- Stainless Steel: Durable, corrosion-resistant metal seals suitable for high-pressure and high-temperature applications. Stainless steel seals are available in various grades to suit specific environments.
- Graphite: A self-lubricating, high-temperature material used in seals for extreme conditions. Graphite seals can withstand temperatures up to 500°C and are resistant to most chemicals.
- PTFE: A low-friction, chemically inert material with a wide temperature range. PTFE seals are often used in dynamic applications or as backup rings for elastomeric seals.