Dynamic seals are essential components in machinery, preventing leaks and ensuring optimal performance. However, choosing the wrong type of seal for an application can lead to premature failure, costly downtime, and even safety hazards. Dynamic seals come in a wide variety of types, materials, and designs to handle different pressures, temperatures, speeds and other challenging operating conditions.
This guide explains the key types of dynamic seals, materials, and performance factors to help you select seals that will keep your critical machinery assets running reliably.
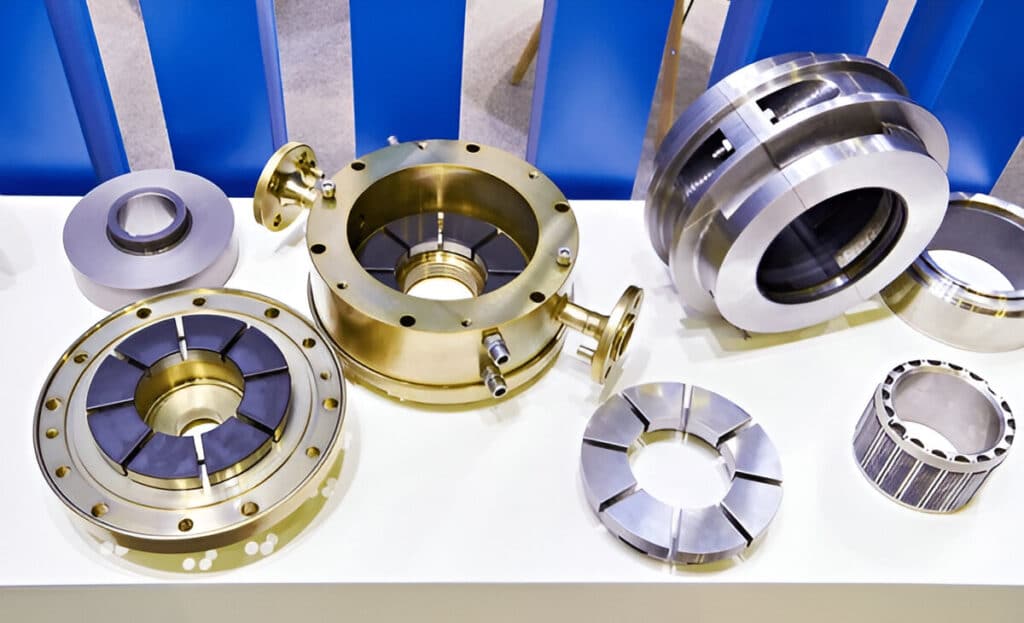
What is a Dynamic Seal
A dynamic seal is a specialized mechanical component designed to prevent leakage or contamination in systems where there is relative motion between parts. Unlike static seals that operate between stationary surfaces, dynamic seals are used in applications involving linear, rotary, or oscillating movement. The primary function of a dynamic seal is to contain fluid (liquid or gas) within a system while simultaneously protecting against external contaminants.
Types of Dynamic Seals
Dynamic seals are broadly categorized into two main types:
- Contact Seals: Contact seals operate by maintaining direct physical contact between the sealing element and the moving surface. This continuous contact helps prevent fluid leakage and ingress of contaminants.
- Clearance Seals: Clearance seals, also known as non-contact seals, maintain a small gap between the sealing element and the moving surface. This design minimizes friction and wear while still providing effective sealing.
Piston Seals
Piston seals are used to seal the interface between a piston and the cylinder wall in reciprocating applications. They prevent fluid from leaking past the piston during both compression and extension strokes.
Rod Seals
Rod seals are designed to seal the interface between a moving rod and the stationary housing or cylinder head. They prevent fluid leakage along the rod while also protecting against external contamination.
Rotary Seals
Rotary seals are used to seal the interface between rotating shafts and stationary housings. They prevent fluid leakage and ingress of contaminants in applications involving rotational motion. Rotary seals can be either contact seals (e.g., lip seals) or clearance seals (e.g., labyrinth seals).
Wiper Seals
Wiper seals are designed to remove contaminants, such as dirt, dust, and moisture, from the surface of a moving component. They are often used in conjunction with other seals to provide an additional layer of protection against external contamination.
Hydraulic and Pneumatic Seals
Hydraulic and pneumatic seals are specifically designed for use in fluid power systems. They are engineered to withstand high pressures, temperatures, and fluid velocities while maintaining optimal sealing performance.
Oil and Grease Seals
Oil and grease seals are designed to retain lubricants within a system while preventing the entry of contaminants. Oil and grease seals often feature a flexible sealing lip that maintains contact with the rotating surface, ensuring effective sealing and lubrication.
Exclusion Seals
Exclusion seals, also known as dust seals or dirt seals, are designed to prevent the ingress of external contaminants into a system. They are typically used in environments where exposure to dirt, dust, or moisture is a concern.
X-Rings
X-rings are four-lobed, X-shaped seals that provide excellent sealing performance in both static and dynamic applications. They offer low friction, high pressure resistance, and good chemical compatibility.
O-Rings
O-rings are simple, versatile seals with a circular cross-section. While primarily used as static seals, O-rings can also be employed in dynamic applications with relatively low speeds and pressures.
Isolator Seals for Bearings
Isolator seals, also known as bearing isolators, are designed to protect bearings from contamination and lubrication loss. They consist of a stationary and a rotating component that work together to create a non-contacting, labyrinth-like seal.
Lip Seals
Lip seals are one of the most common types of dynamic seals. They feature a flexible sealing lip that maintains contact with the moving surface, providing effective sealing and minimal leakage.
Materials Used in Dynamic Seals
Metals
- Stainless Steel: Known for its excellent corrosion resistance, stainless steel is often used in food processing, pharmaceutical, and chemical industries. It maintains strength at elevated temperatures and has good formability.
- Cast Iron: Valued for its high compressive strength and wear resistance, cast iron is frequently used in heavy-duty industrial applications. It is relatively inexpensive but has limited corrosion resistance.
- Bronze: Prized for its low friction coefficient and good wear resistance, bronze is often used in applications involving rotating shafts. Its superior thermal conductivity helps dissipate heat in high-speed applications.
Polymers and Rubbers
- Polytetrafluoroethylene (PTFE): PTFE, also known as Teflon, is known for its excellent chemical resistance, low friction, and wide temperature range. Its self-lubricating properties make it ideal for applications where external lubrication is not possible.
- Polyurethane (PU): PU offers high abrasion resistance, good mechanical strength, and excellent oil resistance. It is commonly used in hydraulic and pneumatic seals due to its ability to handle high pressures and fast sliding speeds.
- Nitrile Rubber (NBR): NBR, also known as Buna-N, is valued for its excellent resistance to oils, fuels, and hydraulic fluids. It performs well in moderate temperatures and has good abrasion resistance.
- Ethylene Propylene Diene Monomer (EPDM): EPDM offers exceptional heat, ozone, and weather resistance. Its good chemical resistance and wide temperature range make it suitable for outdoor and automotive applications.
Factors Influencing Dynamic Seal Performance
Pressure and Load
Higher pressures necessitate greater interference between the seal and the mating surface to prevent leakage. However, increased contact force also leads to higher friction and wear.
In addition to fluid pressure, externally applied mechanical loads can significantly impact seal performance. Radial or axial loads from misalignment, vibration, or other sources may distort the seal geometry, leading to uneven wear and potential leakage paths. Seal design must account for any anticipated load conditions to maintain proper contact and sealing force throughout the operating range.
Type of Movement
Dynamic seals are used in applications involving linear reciprocating motion, rotary action, or a combination of both. The type of movement dictates the seal geometry and material requirements. For example, rod or piston seals for linear motion must accommodate the sliding contact and relative motion between the seal and the mating surface. Rotary shaft seals, on the other hand, must contend with the continuous rotation and potential eccentricity of the shaft.
The type of movement also influences the lubrication regime and wear mechanisms the seal experiences. Reciprocating motion may result in boundary or mixed lubrication, while rotary applications often operate with full fluid film lubrication.
Movement Speed
At low speeds, the seal must maintain sufficient contact to prevent leakage, even with potentially limited lubrication. Higher speeds can improve lubrication by generating a fluid film, but also introduce concerns such as increased friction, heat generation, and wear.
Temperature
Elevated temperatures can cause thermal degradation of the seal material, leading to hardening, embrittlement, or loss of elastic properties. This degradation can result in leakage, increased wear, or complete seal failure.
Low temperatures can also pose challenges, particularly for elastomeric seal materials. Cold temperatures may cause stiffening and loss of flexibility, compromising the seal’s ability to maintain contact and sealing force. In extreme cases, low-temperature embrittlement can lead to seal cracking or fracture.
Surface Finish
Rough or irregularly finished surfaces can lead to accelerated seal wear, leakage paths, and reduced sealing effectiveness. The seal material must be able to conform to and maintain contact with the mating surface to establish a reliable seal.
For most dynamic sealing applications, a smooth, uniform surface finish is desirable. Generally, harder seal materials require smoother mating surfaces, while softer, more conformable materials can tolerate somewhat rougher finishes.
Pressure
High pressure differentials require greater sealing force and can lead to increased wear and deformation of the seal material. Rapid pressure changes or pulsations can cause fatigue and loss of sealing contact.
Seal design must account for the maximum expected pressure differential, as well as any cyclic pressure loading.