Floating bushings are a specialized type of bearing designed to accommodate misalignment and axial movement in rotating machinery. While fixed bushings constrain shaft motion in a rigid housing, floating bushings allow a degree of freedom that proves advantageous in certain applications.
This article explores the working principles behind floating bushings, outlining their benefits and drawbacks. We will also discuss common use cases and delve into key engineering considerations for optimal bushing design and performance, including material selection, clearance calculations, and the interplay of friction and pressure forces.
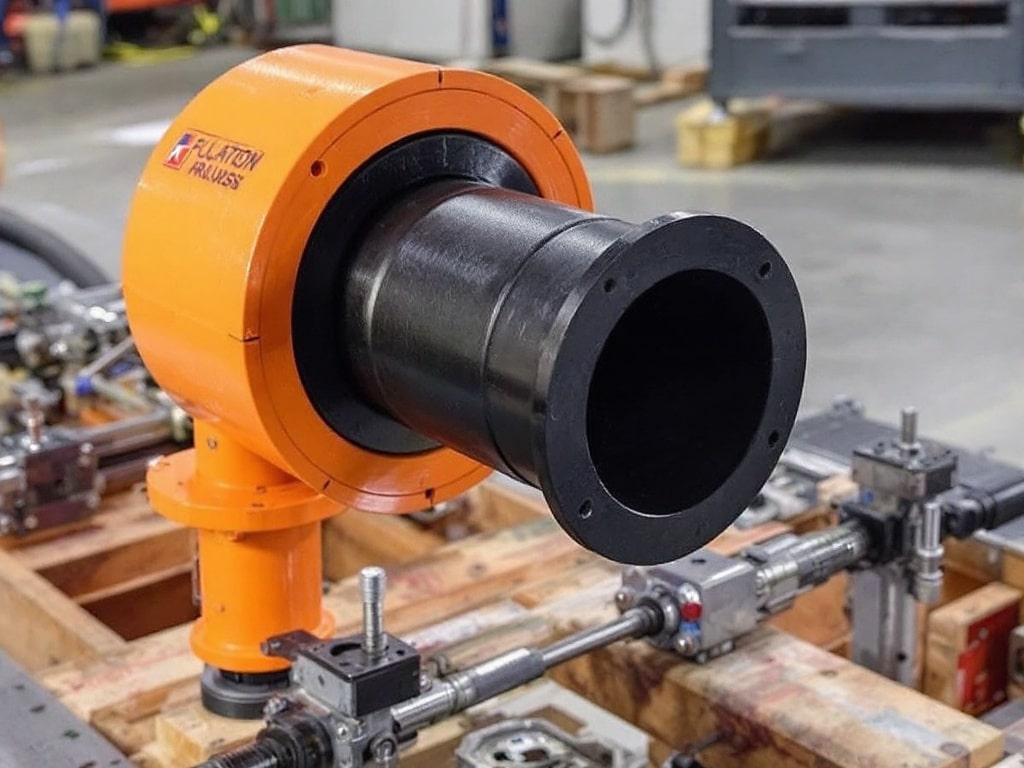
What Is Floating Bushing
A floating bushing, also known as a floating bearing, is a type of mechanical bushing designed to accommodate misalignment and provide smooth, low-friction motion between two components. Unlike fixed bushings, which are rigidly mounted, floating bushings allow for some degree of movement or “float” between the mating parts.
Floating bushings typically consist of an outer sleeve, an inner sleeve, and a layer of lubricant between the two. The outer sleeve is usually press-fit or bonded into one component, while the inner sleeve is free to move within the outer sleeve. This configuration allows the bushing to compensate for any misalignment between the two components, reducing stress and wear on the system.
How Floating Bushing Works
The key to the functionality of a floating bushing lies in its ability to allow for relative motion between the inner and outer sleeves. When the two connected components are not perfectly aligned, the floating bushing can shift slightly to accommodate the misalignment, preventing binding or excessive wear.
As the inner sleeve moves within the outer sleeve, the lubricant layer between them helps to reduce friction and prevent direct metal-to-metal contact. This lubrication can be provided by various means, such as oil-impregnated sintered bronze, PTFE (polytetrafluoroethylene), or other low-friction materials.
The clearance between the inner and outer sleeves is carefully designed to allow for the necessary range of motion while still maintaining proper alignment and load distribution. This clearance, along with the choice of bushing materials and lubricants, determines the load capacity, speed capability, and overall performance of the floating bushing.
Under load, the floating bushing allows for small angular and axial displacements, as well as slight misalignments between the connected components. This flexibility helps to distribute stress more evenly across the bushing surface, reducing wear and extending the service life of the system.
Advantages of Floating Bushings
Improved Alignment and Reduced Friction
One of the primary advantages of floating bushings is their ability to self-align within the housing bore. This self-alignment feature helps to reduce friction and wear by allowing the bushing to adjust its position slightly, compensating for any misalignment between the shaft and the housing. As a result, floating bushings can extend the service life of the components and improve overall system efficiency.
Accommodation of Thermal Expansion
Floating bushings are designed to accommodate thermal expansion and contraction of the shaft and housing materials. The clearance between the bushing and the housing allows for some movement, preventing excessive stress on the components due to temperature changes.
Vibration Dampening
The inherent design of floating bushings helps to dampen vibrations transmitted through the shaft and housing. The bushing material, typically a softer metal or polymer, absorbs and dissipates vibrational energy, reducing noise and protecting adjacent components from excessive vibration. This vibration dampening property can enhance the overall smoothness and reliability of the system.
Cost-Effective Solution
Compared to more complex bearing systems, floating bushings offer a cost-effective solution for many applications. They are relatively simple to manufacture, install, and replace, making them an economical choice for various machinery and equipment. Additionally, the self-aligning feature of floating bushings can help to reduce maintenance costs associated with misalignment and premature wear.
Disadvantages of Floating Bushings
Limited Load Capacity
One of the main disadvantages of floating bushings is their limited load capacity compared to other bearing types, such as roller or ball bearings. The load capacity of a floating bushing is dependent on factors such as the bushing material, surface area, and operating conditions. In applications with high radial or axial loads, floating bushings may not be suitable, and alternative bearing solutions may be required.
Reduced Rotational Speed
Floating bushings are generally not suitable for high-speed rotational applications due to the inherent friction between the bushing and the shaft. As the rotational speed increases, the heat generated by friction can lead to accelerated wear and reduced performance. In high-speed applications, rolling element bearings or other specialized bearing types are typically preferred.
Sensitivity to Contaminants
The clearance between the floating bushing and the housing can allow contaminants, such as dirt, dust, and debris, to enter the bushing area. These contaminants can cause accelerated wear, increased friction, and reduced performance. In environments with high levels of contaminants, additional sealing or filtration measures may be necessary to protect the floating bushings.
Regular Maintenance Requirements
Floating bushings require regular maintenance to ensure optimal performance and longevity. This maintenance may include lubrication, inspection for wear, and replacement when necessary. Neglecting proper maintenance can lead to premature failure and increased downtime.
Applications of Floating Bushings
Automotive Suspension Systems
Floating bushings are commonly used in automotive suspension systems, particularly in control arms, sway bars, and steering linkages. In these applications, floating bushings allow for some movement and alignment while providing vibration dampening and noise reduction. The self-aligning feature of floating bushings helps to maintain proper suspension geometry and improve vehicle handling.
Agricultural Equipment
In agricultural equipment, such as tractors, harvesters, and implements, floating bushings are used in various pivot points and linkages. These bushings provide the necessary flexibility and alignment to accommodate the varying loads and terrain encountered in agricultural operations. The vibration dampening properties of floating bushings also help to reduce stress on the equipment and improve operator comfort.
Construction Machinery
Floating bushings are employed in construction machinery, such as excavators, loaders, and cranes, to support pivot points and allow for relative motion between components. The ability of floating bushings to self-align and accommodate misalignment is particularly beneficial in these applications, where heavy loads and rough terrain can cause significant stress on the equipment.
Industrial Machinery
In industrial machinery, floating bushings are used in a wide range of applications, including conveyor systems, printing presses, and packaging equipment. These bushings provide support and alignment for rotating or oscillating shafts while allowing for some degree of misalignment. The cost-effective nature of floating bushings makes them an attractive choice for many industrial applications.
Engineering Considerations
Material Selection
Common materials include bronze, brass, steel-backed bronze, and polymers such as nylon or PTFE. The choice of material depends on factors such as load capacity, operating temperature, corrosion resistance, and lubrication requirements. Bronze bushings, for example, offer good load capacity and wear resistance, while polymer bushings provide excellent low-friction properties and chemical resistance.
Clearance Design
The clearance should be sufficient to allow for self-alignment and accommodate thermal expansion while preventing excessive movement or vibration. Insufficient clearance can lead to binding and increased friction, while excessive clearance can result in reduced load capacity and increased wear. Engineers must carefully consider the specific application requirements when designing the clearance for floating bushings.
Friction and Pressure Dynamics
Factors such as surface finish, lubrication, and contact pressure influence the friction between the bushing and the shaft. Engineers must consider the expected operating conditions, including load, speed, and temperature, when designing floating bushings to ensure adequate performance and durability. In some cases, specialized coatings or surface treatments may be applied to the bushing to reduce friction and improve wear resistance.