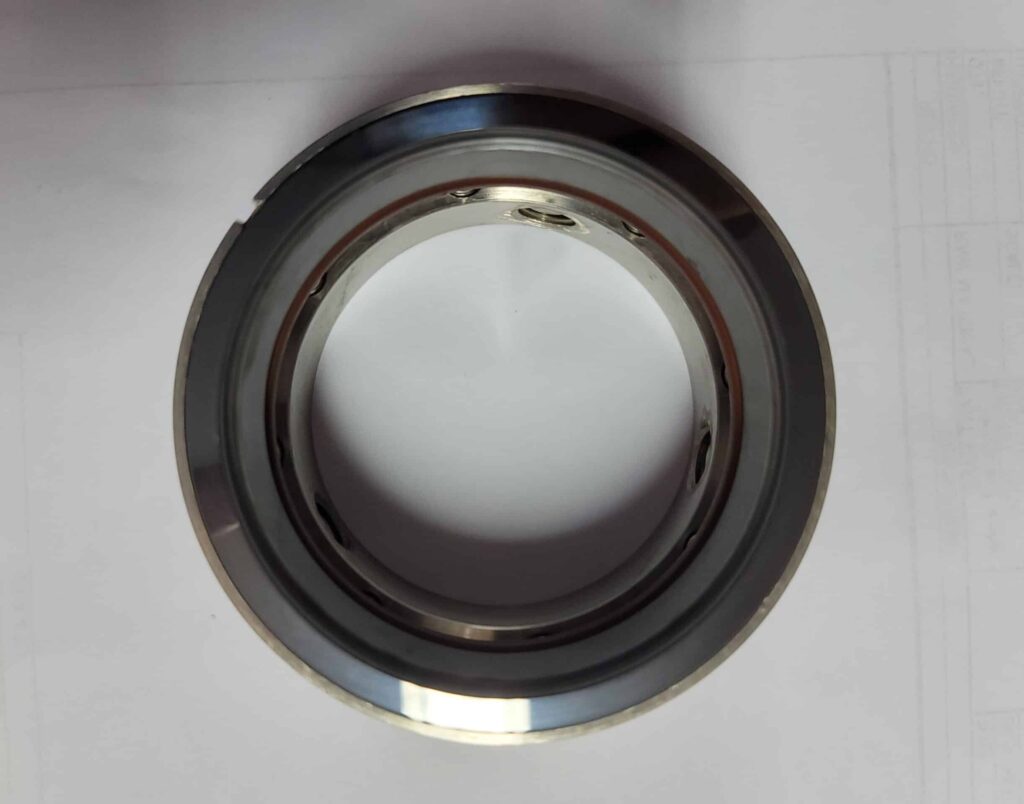
What Is Mechanical Face Seal
A mechanical face seal, also known as a heavy duty seal, is a type of seal that consists of two flat faces, one stationary and one rotating, that are pressed together by springs or fluid pressure to prevent leakage of fluids. The sealing faces are typically made from hard, wear-resistant materials such as tungsten carbide, silicon carbide, or ceramics.
Mechanical face seals are designed to operate in a thin fluid film between the sealing faces, which provides lubrication and helps to reduce heat generation and wear. The fluid film is maintained by a combination of the seal geometry, the fluid properties, and the operating conditions such as pressure, temperature, and speed.
What Is the Purpose of Mechanical Face Seal
The primary purpose of a mechanical face seal is to prevent the leakage of fluids from a rotating shaft or housing while operating in arduous environments. These seals are commonly used in applications such as centrifugal pumps, mixers, agitators, and other rotating equipment where high speeds, pressures, and temperatures are encountered.
Types of Mechanical Face Seal
There are two main types of mechanical face seals: Type DO and Type DF.
Type DO
Type DO seals, also known as duo cone seals or toric seals, consist of two sealing elements: a primary ring and a mating ring. The primary ring is typically made from a hard, wear-resistant material such as tungsten carbide or silicon carbide, while the mating ring is made from a softer material such as carbon graphite or bronze.
The primary ring has a conical sealing face that mates with a corresponding conical surface on the mating ring. This geometry allows the seal to accommodate axial movement and misalignment of the shaft while maintaining a consistent sealing force. Type DO seals are commonly used in applications with high speeds and pressures, such as boiler feed pumps and pipeline compressors.
Type DF
Type DF seals, also known as double-faced seals, consist of two primary rings that seal against each other. The rings are typically made from the same material, such as tungsten carbide or silicon carbide, and have flat sealing faces.
One of the primary rings is stationary and is held in place by the seal housing, while the other ring rotates with the shaft. A secondary sealing element, such as an O-ring or gasket, is used to seal between the stationary ring and the housing. Type DF seals are commonly used in applications with high temperatures and aggressive media, such as chemical processing and oil & gas production.
Advantages of Mechanical Face Seals
- Harsh environment resistance: The hard, wear-resistant materials used in mechanical face seals provide excellent resistance to abrasion, corrosion, and erosion.
- High-speed and high-pressure operation: Mechanical face seals can operate at high speeds and pressures without excessive wear or leakage.
- Long-lasting with minimal upkeep: The robust design and durable materials used in mechanical face seals provide long service life with minimal maintenance requirements.
- Space-efficient design: The compact, cylindrical design of mechanical face seals allows them to be easily packaged into equipment with limited space.
- Self-aligning capability: The conical geometry of Type DO seals allows them to self-center and compensate for misalignment, reducing wear and extending seal life.
Applications of Mechanical Face Seal
- Centrifugal pumps: Mechanical face seals are used to prevent leakage of the pumped fluid along the shaft.
- Mixers and agitators: Mechanical face seals are used to contain the process fluid and prevent contamination.
- Compressors: Mechanical face seals are used to prevent leakage of the compressed gas and maintain efficiency.
- Turbines: Mechanical face seals are used to prevent steam or gas leakage and maintain vacuum in condensers.
- Refineries and chemical plants: Mechanical face seals are used in pumps, valves, and other equipment to prevent leakage of hazardous or corrosive fluids.